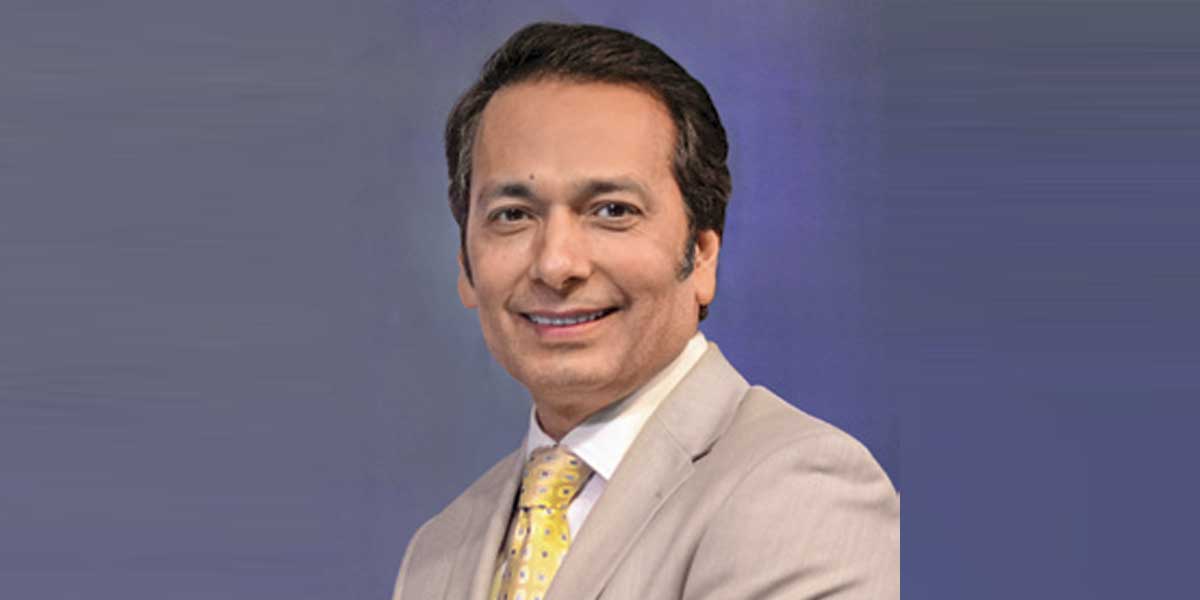
Fashionably responsible
Textile manufacturing is the oldest and leading generator of employment, especially among the developing economies. On the flip side, the industry is responsible for an estimated 2-8 per cent of the world’s greenhouse gas emissions and accounts for 9 per cent of annual microplastic losses to the oceans. According to an estimates, around 215 trillion litres of water per year is consumed by the textile industry world over, out of which 6-9 trillion litres is consumed only for fabric dyeing.
Indian textile industry, which prides itself on being the second largest employer in the country after agriculture, is also facing the brunt of climate change. Adding to the woes is the energy and water-intensive nature of the textile manufacturing industry. Textile processing units need large quantity of water for washing raw fabric before dyeing and then to remove unfixed colours after printing. And dyeing requires soft water, putting a big load on freshwater reserves. For using hard water, textile firms have to use chemical agents to soften it.
According to data from the Confederation of Indian Textile Industry (CITI), textile dyeing and processing units are among the largest consumers of water and energy in the industry. Textile dyeing and processing units consume approximately 200 litres of water per kg of fabric produced, highlighting the need for water conservation measures. Environment-friendly technologies are available, but they come at a cost; hence, the transition to sustainable development is slow.
International brands are putting pressure on their suppliers from across the world to mitigate emissions and follow the best environmental compliance standards. On their part, textile makers – mostly comprising micro, small and medium enterprises (MSMEs) – are responding by modifying manufacturing processes with the efficient use of coal, electricity and water and by adopting renewable energy.
There are some successful stories in India where companies have collaborated to find solutions for environment issues. Surat, which has over six lakh power looms and 450 processing-dyeing and printing units, became the first city in India to set up a tertiary water treatment plant to recycle sewage water and supply it to textile industries. Small changes such as installing a Y-valve (which reduces water wastage) and reusing the wash water (that has less impurities) have led to a lot of water saving in textile clusters.
Some MSMEs in India have installed a Programmable Logic Controller (PLC) for dyeing machines, an automation technology approved by Energy Efficiency Services Limited (EESL), to reduce usages of energy, steam, chemicals, and water while giving higher production. Digital printing is another solution for achieving sustainability goals. While digital printing is far more flexible and precise in terms of colours and designs (as compared to the traditional screen printers), there is no acidic effluent discharge from washing to get rid of unfixed colours.
India’s fashion industry revenue is projected to grow from $ 18.51 billion in 2022 to $ 39.42 billion by 2027 at an annual growth rate of 16.32 per cent. By implementing water and energy conservation measures, the industry can reach the goal more responsibly.