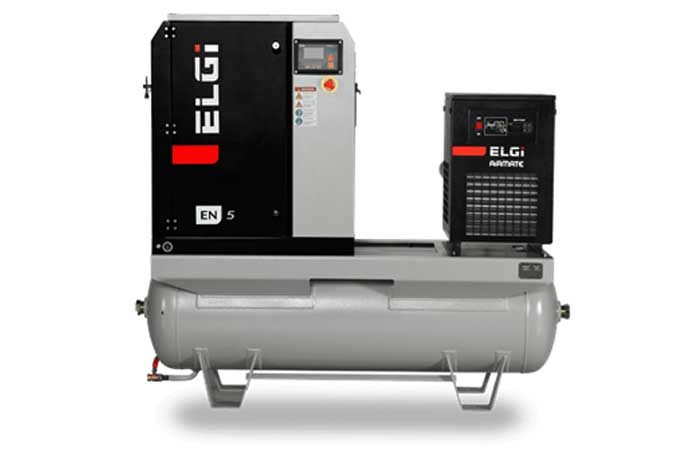
Enhancing textile production with energy-efficient modern compressors
Energy-efficient compressors enhance sustainability by reducing greenhouse gas emissions and improving the industry’s reputation with environmentally conscious consumers, explains Thomas Paulose.
The textile market has experienced significant growth in recent years, expanding from $ 638.03 billion in 2023 to a projected $ 689.54 billion in 2024, reflecting a compound annual growth rate (CAGR) of 8.1 per cent. According to IBEF, the Indian textiles and apparel market is projected to grow at a 10 per cent CAGR, reaching $ 350 billion by 2030, with exports anticipated to hit $ 100 billion. While the industry serves as a key player in global manufacturing, it is under increasing pressure to enhance energy efficiency and reduce its environmental impact. Among the various technological advancements driving these improvements, modern compressors stand out as critical components in optimising energy consumption throughout the textile production process.
Textile industry’s energy challenge
Textile production is inherently energy-intensive, involving multiple stages such as spinning, weaving, knitting, dyeing, and finishing. These processes demand significant amounts of electricity and thermal energy. Historically, the industry has relied on traditional, less efficient compressors that consume substantial energy, leading to higher operational costs and greater environmental impact.
Given the growing emphasis on sustainability and cost-efficiency, the textile industry is increasingly adopting advanced technologies to mitigate energy consumption. Modern compressors, designed with energy efficiency in mind, are playing a pivotal role in this transformation.
Role of compressors in textile production
Compressors play a vital role in textile production by supplying compressed air essential for various operations, including air-jet weaving, spinning, and pneumatic conveyance of materials. Compressors provide the air needed to propel the weft yarn through the warp shed, where their efficiency directly impacts the energy consumption of the weaving process. In spinning mills, compressed air is crucial for cleaning machinery and operating spinning equipment, making energy-efficient compressors essential for reducing overall power usage. Additionally, compressors are used in pneumatic systems to transport fibres and fabrics within the facility, with efficient compressors ensuring minimal energy wastage and contributing to the overall energy efficiency of the production process.
Innovations in modern compressors
Modern compressors incorporate several technological advancements that enhance their energy efficiency. A few of which are as follows:
- Variable Speed Drives (VSDs): VSDs allow compressors to adjust their speed and output based on real-time demand, reducing unnecessary energy consumption during periods of low demand. This adaptability ensures that the compressor only uses as much energy as needed, leading to significant savings.
- Energy recovery systems: Some advanced compressors come equipped with energy recovery systems that capture and reuse waste heat generated during compression. This recovered energy can be repurposed for heating water or spaces within the facility, further reducing the overall energy footprint.
- Smart controls and IoT Integration: Modern compressors often feature smart controls and Internet of Things (IoT) integration, enabling real-time monitoring and optimisation of performance. These systems can predict maintenance needs, prevent downtime, and ensure the compressor operates at peak efficiency.
- Improved air filtration and drying: Efficient air filtration and drying systems integrated into modern compressors ensure that the air used in production is clean and dry. This not only enhances the quality of the textile products but also reduces the energy required for subsequent processing stages.
- Less oil fumes and oil capturing: Efficient air oil separation systems with the least pressure drop ensure minimal oil carryover to the distribution lines. Collecting the contaminated oil from the pipelines is also being emphasized, which has become part of the green initiatives.
Benefits of efficient compressors
The adoption of modern, energy-efficient compressors in textile production offers numerous benefits across various facets of operations. These compressors reduce energy costs significantly by optimising consumption, thereby enhancing the profitability of manufacturing activities. Energy-efficient compressors enhance sustainability by reducing greenhouse gas emissions and improving the industry’s reputation with environmentally conscious consumers. Additionally, their advanced features, such as smart controls and predictive maintenance capabilities, minimise downtime and ensure smoother production processes. Lastly, the quality of textile products sees an improvement due to consistent and clean compressed air, minimizing impurities and moisture during critical production stages.
The textile industry’s pursuit of energy efficiency is vital for both economic and environmental reasons. Modern compressors, with their advanced technologies and energy-saving features, are key enablers in this quest. By reducing energy consumption, enhancing sustainability, and improving production reliability, these compressors not only contribute to the industry’s bottom line but also support global efforts towards a greener future.
As the textile industry continues to innovate and adopt more sustainable practices, the role of modern compressors will undoubtedly become even more significant. Investing in these advanced systems is not just a step towards energy efficiency but also a commitment to a more sustainable and responsible textile production process.
About the author:
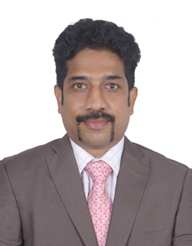
Thomas Paulose is the Vice President and Head – Oil Free Business (India, South Asia, Africa, and the Middle east) of Elgi Equipments