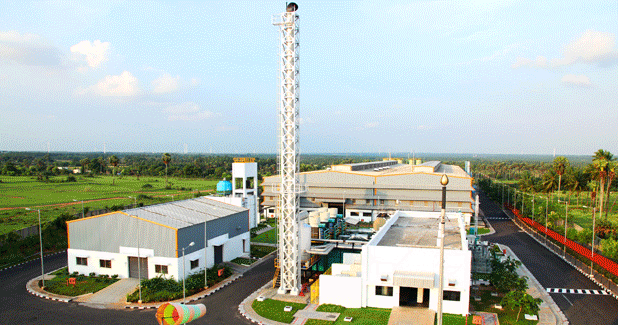
ELGi on road to become No. 2 in air compressors
ELGi Equipments is geared up to achieve its goal of emerging as No. 2 air compressor manufacturer globally within the next decade. The ITJ reports after a factory visit to ELGi’s facilities in Coimbatore. Every logo of the Coimbatore-based ELGi Equipments Ltd carries a two-word slogan – Always Better! But by the time, the ITJ Editor finished his tour of its HQ, factory and foundry, he realised that the slogan is a bit modest and should have been “Always Bestâ€! And this compressor giant is not at all modest about its ambition, which is: To be the No. 2 in global compressor making within the next decade, from a position of being No. 7 now. In the last four years, after the completion and working of its sprawling 1,00,000 m2 facility at the Kodangipalayam village in Coimbatore, ELGi can proudly claim that the foundation to reach its goal has been well laid.
ELGi Equipments is geared up to achieve its goal of emerging as No. 2 air compressor manufacturer globally within the next decade. The ITJ reports after a factory visit to ELGi’s facilities in Coimbatore.
Every logo of the Coimbatore-based ELGi Equipments Ltd carries a two-word slogan – Always Better! But by the time, the ITJ Editor finished his tour of its HQ, factory and foundry, he realised that the slogan is a bit modest and should have been “Always Bestâ€! And this compressor giant is not at all modest about its ambition, which is: To be the No. 2 in global compressor making within the next decade, from a position of being No. 7 now. In the last four years, after the completion and working of its sprawling 1,00,000 m2 facility at the Kodangipalayam village in Coimbatore, ELGi can proudly claim that the foundation to reach its goal has been well laid.
ELGi is involved in manufacturing air compressors since 1960. What does ELGi brand stand for? Reliability? ‘Yes†said Anvar Jay Varadaraj, Senior Manager – Marketing & Corp Communications, who minced no words. “Our mission is to establish the ELGi brand.
Today with many companies giving technical details and characteristics of their products, we focus on a content-driven approach. Compressor is at the background, and the challenge is to make the customer understand how important are its reliability, power saving factor, etc.â€
ELGi plans to leapfrog to No. 2 position with the markets shares in the country versus international at the present 50:50 going up to 20:80. Hence most of the growth will be coming from outside and the inorganic growth will reach 70 per cent, asserted Varadaraj.
Some of the breakthroughs in ELGi’s exports have happened in south-east Asian countries including Indonesia in the recent times. ELGi’s journey to the 10x growth in the next decade has already begun in earnest. The company has already three subsidiaries: ATS ELGi Ltd, ROTAIR Spa, Italy and Patton’s Inc, USA.
A joint venture in the name of ELGi Sauer Compressors in India is an added asset. ELGi offers a complete range of air compressors from 1HP piston to 2000HP centrifugal machines. It offers over 400 compressed air systems from the large centrifugal compressors to the world’s smallest screw compressors.
The Singanallur best-in-class conveyor assembly line with automated monitoring and testing stations has a production capacity of 15,000 screw air compressors and 25,000 piston compressors.
ELGi has a leadership position in supplying compressors to the Indian textile industry. Stressing this, Varadaraj added: “The textile segment has been historically a strength to us.
In the last few years, it has been a big challenge from this segment since orders have started coming in large numbers and the selling strategy has been elevated. The stress for this industry is now on the entire compressor system rather than individual compressors. The customers are persuaded to move up the value chain. Now most customers have shifted to oil-lubricated screw machines with filters and dryers, which deliver the same good quality. We are starting to see more technologies coming in like variable frequency drives (VFDs).â€
ELGi exports about 50 per cent of its compressors abroad, of which more than 70 per cent goes to the western markets, mainly the US and Europe. It does business in over 70 countries having over 200 distributors and is actively present in 18 countries.
This is no mean achievement. “The challenge is to enhance the brand of our compressors globally. And get more pull in the market for ELGi compressors. Globally as start selling compressors to big names like Johnson Controls, people turn their attention to our compressors. Our big competitors are in Europe or the US and hence the challenge to become No. 2 globally will be taken up without any compromise on any of our divisions.â€
Said Ramesh Ponnuswami, Director-India, South Asia, Africa and Middle East: “Our technological capability is of very high order, and as we grow globally, we are prepared to meet many challenges. Today we are a force to reckon with in compressors within the country. India has a relatively small share in the global compressor market. The country has just 5 per cent of the $15 to $16 billion global compressor market. We are in the process of strategising and getting a lion’s share in the total market. Our back-end is very strong. Now, with the global aspiration to be No. 2, we are working together towards achieving the goal collectively.â€
“Our core competency is building perfect compressors, and we have achieved this step by step over the years. Today, we stand among the best compressor manufacturers all over the world. We have learnt and applied as the journey progressed and today have reached the position among top players in the world. Besides, new markets have been explored abroad and captured,†said R Jayakanthan, Director – Product, Systems & Strategy.
In the construction industry too, ELGi plays a dominant role in the supply of compressors. Not only that, it has explored and opened up new areas of applications in various sectors. With the economy opening up and segments like infrastructure taking its due place in the developments, ELGi is positive about the demand for compressors perking up in the coming years. ELGi is always in a state of preparedness with technological changes and demand matching such transformation.
ELGi operates four factories in the world with the same quality standards using its own airends, with the capability of producing 15,000 airends and 40,000 compressors (screw and recip) per annum. ELGi has two factories in Coimbatore, the old Singanallur 20,000 m2 facility is for the final assembly line, and the four-year old Kodangipalayam plant making the airends right from the foundry production line. ELGi has installed machine tools in its main plant mostly imported to ensure highest quality standards with a production capacity ranging from 3 to 250 kg and 38,00 parts per annum at an accuracy level of less than two microns.
The airend is at the heart of compressors, said a factory manager who took this correspondent around the main factory. “We produce sets of 60 to 65 airends per day. The size range is from 53 mm to 310 mm diameter rotor. In the airends, cast iron casing and the male- and female-rotors come from the company itself and other some parts are procured from outside to end up finally as compressors,†said the factory manager.
ELGi has also started developing its own machines—for profile milling, grinding and polishing—which can do the same functions of the imported machines. At least half a dozen machines are already in use and more such machines are under preparation.
“The foundry adjacent to the airend manufacturing facility is another site of excellence in structure and facilities. “Everything about the foundry is green, and even the wastage of just 4 per cent of the sands that go for moulding is recycled as bricks,†said KV Rao, DGM – Foundry, who is passionate like all the managers while explaining the various features of the foundry.
The foundry is equipped with best-in-class foundry equipment under one roof with minimum use of exhaustible natural resources, contamination of ambiance and facilitates to produce constantly reliable quality castings. It is recipient of green foundry award by Institute of Indian Foundrymen for the year 2015-16.
The furnace, moulding line and the casting fettling and finishing lines are noteworthy spots for conducive working and show great concern for safety and productivity. Said Rao: “The foundry-grade sands are sourced from the country in processed condition and sometime high quality sands are imported from Saudi Arabia. The entire process is almost automated and is handled by a few workers with a shift of 7 am to 5 pm.â€
No compromise on HR & workers training What is the USP of this Kinathukadavu plant? Technology, said S Arun Prasad, General Manager – Air Center & Foundry, without batting an eyelid. “This is a unique plant. Just see, when you enter, you will notice the scrap yard. We keep all these accessible to the people at large, for them to see how clean and green our environment is. This demonstrates our commitment to society, on which stands the whole concept of quality. The structure of the plant and the entire lay-out emphasise the importance we give to the final quality.â€
“The second most important thing in this plant is my people and the working culture they follow. The airends we manufacture here is meant for the entire global facilities. We have high-end machines which are mostly imported, capable of producing parts at tolerance levels less than 10 microns,†said Prasad.
“We have a vocational training centre. We get young people who have finished 10th standard, but are unable to go for further studies. The training centre is a certificate-based course, with the quality standards kept at very high level. This is a much better course than any diploma course since the students get trained at the factory level. After the three-year course is completed, they are given one-year shopfloor training,†said Prasad. Another strength of the factory is that it has self-managed teams working on all the departments.
There is also another wing to training called Dexterity Training Centre, which enhances the ergonomic use of four motion principles of the operators during assembling the compressors. “The training is intense and the graded system selects workers on their various capacities to be placed suitably. There is always continuity in training and retraining and the system is aimed at achieving higher levels of accuracy, speed and quality.
One of the cornerstones on which the strength of the company is built is the HR policies and culture. Said Jayashankar Jayaraman, Director – HR, “The strength of our management policy lies in the fact that we have one policy from the lower rung of workers to the top level. This is a culture we have built over the years. Our constant endeavour is to hold our values very high. There will be no compromise on that. We have even worked out how to fill the gaps, when some of our senior managers will be retiring in the next few years. The training to bridge the gap is already on.â€
ELGi has 1500 employees worldwide out of which 800 (Note that this 800 is inclusive of sales professionals directly employed by ELGi and by its dealers worldwide) are in sales. ELGi spends about 3 to 3.5 per cent on R&D, and is equipped with an efficient design team to take care of the futuristic requirements. “The biggest challenge for us is to create awareness about energy saving through compressors and also to find new applications. We do not want to sell just a product but a system that will contribute to the growth of the company,†said Varadaraj summing up the philosophy of the company.