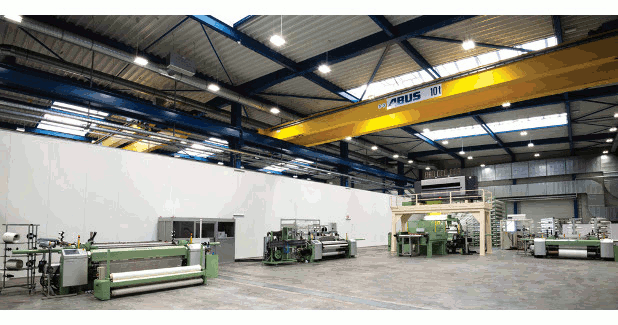
Dornier’s app-specific systems for semi-finished products
With an innovative fabric guidance system, fabrics can be manufactured with thickness of up to 100 mm.
With an innovative fabric guidance system, fabrics can be manufactured with thickness of up to 100 mm.
Tapes, tape fabrics and 3D structured textiles: DORNIER presented machines and system solutions from its Composite Systems business unit for efficiently manufacturing the latest in semi-finished fibre composite products at the JEC World, which downed its shutters recently.
“At the JEC we presented the full range of our machine and system solutions for the composites industryâ€, says Dr Josef Klingele, Head of Composite Systems. For tapes, tape fabrics and complex 3D fabrics, in the machines and production lines of the Composite Systems range, set up in 2014, the machine builder combines the unrivaled expertise collected in its globally respected Weaving Machines and Speciality Machines business units. Particularly with the extremely versatile Roving weaving machine for processing high-performance materials like carbon, glass and aramid fibres, the family company on the shores of Lake Constance has been the preferred partner for technical weavers worldwide for over 40 years. With core skills in textile and plastic processing collected in its Composite Systems business unit, DORNIER is building its reputation as a reliable equipment provider partner for the burgeoning composite industry.
Complex 3D fabrics & multilayer structures
Very high dynamic loads, good impact resistance and outstanding damage tolerance – it is often the case that the requirements placed on modern composite components simply cannot be met with layered textile reinforcements. The solution: multilayer, integrally reinforced 3D fabrics. These can be produced economically on 3D weaving machines from DORNIER.
With an innovative fabric guidance system, fabrics can be manufactured with thickness of up to 100 mm. For this, the textile weave pattern is first developed in a virtual environment and then transferred digitally to the weaving machine controller.
Machine for reinforcement fabrics
“Manufacturing technologies are in a permanent state of evolution and optimisationâ€, says Klingele. These days, both dry and fully impregnated tapes can be produced in widths up to 600 mm on the DORNIER tape production line at manufacturing speeds as high as 30 meters per minute. Then, the finished tapes are processed further on the tape weaving machine to create textiles which are ideal for structural reinforcement and design applications.
“The latest machine generation is now available for fabric widths up to 285 cmâ€, adds Klingele. This represents a significant increase in productivity and less waste particularly for applications involving thermoplastic composite materials.
High-quality composites
The challenges facing the composite industry are enormously diverse; no two machines for manufacturing semi-finished goods are the same. In order to meet specific customer requirements, DORNIER has established its own technology centre where it develops and tests complex machine and system concepts for optimal production of semi-finished products jointly with the customer.
For example, trials are conducted in a tape laboratory facility here on the manufacture of thermoplastically fully impregnated tapes, and of tape-based fabrics on a tape weaving machine. A 3D weaving machine for complex multilayer fabrics and a high-performance weaving machine for flat weaves are also available for running tests.
“It is just not possible to make the high-quality textile reinforcements needed for cars, aircraft and machine building on standard machinesâ€, says Klingele.
Lindauer DORNIER GmbH and its Weaving Machine, Speciality Machine and Composite Systems divisions has earned its place as a global technology leader. In 2017, the German family enterprise employing more than 1,000 staff (including 63 trainees) and recorded an order intake of approximately Euro 280 million. The company set up the Composite Systems division with the Roving Weaving Machine, 3D Weaving Machine, Tape Production Line and Tape Weaving Machine as a collecting point for its decades of experience in the engineering weaving machines and building production plants for plastic films.
The systems are configured according to customer specifications; consequently, the equipment of each machine varies – sometimes considerably – depending on the needs of the customer.
All machines are manufactured in the production workshops at Lindau and Esseratsweiler in Germany. Over 90 per cent of the machines produced are exported.