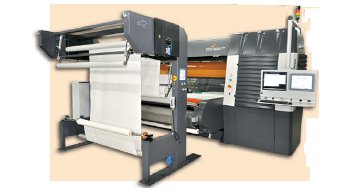
DIGITAL PRINTING
Set to soar
Digital printing has made rapid strides since its entry early 2000, and in the last few years
Digital printing has made rapid strides since its entry early 2000, and in the last few years, most of the providers of this rapidly-evolving technology are eyeing India, which has shown double-digit growth, recount S Joseph and Karthik M.
From millions to billions, digital printing of textiles is set to sweep the markets worldwide, of which India will have a pivotal role to play. Presently, globally digital printing has not even scratched the surface, with just 3 per cent of the total volume, in which rotary printing takes a lion’s share of 65 per cent. But digital’s growth rate is already a whopping 25 per cent, and the markets are already showing the tangible results of its global leap.
A look at the figures: In 2014, digital printing reached a printed volume of over 600 million sq m, which is expected to exceed 3.2 billion sq m in 2019. India’s figures are still more impressive. The geographic split in overall textile printing clearly shows China with 29.3 per cent at the top followed by EMEA (23.1 per cent) and India (17.6 per cent). The remaining amount is divided between the rest of Asia (17.4 per cent) and the American continent (12.6 per cent). Dr John Provost, founder of Provost Ink Jet Consulting Ltd, expects an annual growth of up to 25 per cent between 2012 and 2017 for digital printing – a stark contrast to the 2.5 per cent growth expected for conventional printing methods.
“Digital textile printing is proving a particular favourite within high-quality, short-run projects as pre-treated fabrics, vibrant inks and finishing techniques provide an excellent end product. Italy is well known as an epicentre for textile printing in Europe, in particular the Lake Como region, where many manufacturers base themselves,†says Roz McGuinness, Divisional Director, Federation of European Screen Printers Associations (FESPA), whose event, FESPA Digital 2016 celebrated only last month the 10th year anniversary of the show.
New technologies on the horizon
Innovation in digital printing is what is making it a hot topic! Single-pass system, one-ink-all-fabrics and such process claims are forcing buyers to make a scramble for new technologies. Digital prints clarity is another brownie point for this new revolution in printing, which made its tentative foray sometime in 2000. Short runs, reduced process steps and elimination of a lot of polluting wastes are other reasons for the digital preference. Ultimately, digital is also ushering in a new era for sustainability in printing!
Driven by the digital transformation of the printing processes, the textile industry has experienced a true renaissance in the past 15 years. Whilst developed in the early 90’s, digitally printed fabrics are rapidly evolving and for a while now have been providing the ability to print in high quality, on synthetic as well as natural fibres, at production speeds whilst at the same time using fewer resources such as water and energy.
From production to end use, digital printing – having made notable progress on the quality front too – has ended up influencing market tastes. The particular features of fabric printed digitally are now accepted as the new standard of quality, both by stylists and designers and by final consumers.
Epson’s solutions for digital printing: Epson, a global innovation leader dedicated to exceeding expectations with solutions for markets as diverse as the office, home, commerce and industry, launched Monna Lisa at the ITMA Milan in 2015. Monna Lisa created ripples of interest at the ITMA Milan in 2015. Said Paolo Crespi, Commercial Director at For.Tex: “Since the first unit in 2003, today there are more than 300 Monna Lisa located in Europe, Turkey, India, Brazil, South Korea, Thailand, Vietnam, Taiwan and Japan, all still operating. Growing in all these countries and penetrating those market where the digital textile printing technique is at the beginning is a top priority. The Indian market, where the three companies plan to increase their market share, has proved a huge potential: over the last two/three years, India has shown the highest growth rate and in fact, the three companies have a direct presence for technical service and customer support. For the future, the three companies will concentrate in the developments of inks, with a wider colour extension and more effort in meeting the performance need required by the textile market, but also in Monna Lisa printing technology, increasing the productivity while maintaining the high quality and the effort to further reduce the environmental impact.†(Read full interview with Paolo Crespi later in the issue)
Epson’s major breakthrough in digital printing include Epson Stylus Pro 4900 SpectroProofing Edition and Epson SureColor SC-S70600. With its 98 per cent PANTONE colours coverage, the Epson Stylus Pro 4900 SpectroProofing Edition printer offers excellent colour accuracy and exceptional functionality for remote proofing making it a valuable tool for digital designers. This production printer sets new standards in colour precision. It is targeted at the pre-printing, packaging, design, professional photography and fine art reproduction industry.
Epson SureColor SC-S70600 inkjet printer has an innovative application for the high fashion segment, particularly in the field of accessories and plastic-coated fabric printing for producing bags, shoes, and accessories in artificial leather with customised with the designer’s logo or graphics and drawings embellishments. Designed especially for posters, banners, backlit panels and POS materials production, Epson SureColor SC-S70600 is a printer for rolled material up to 64 inches wide.
It is available in eight or ten colours. One Ink, All Fabrics!: Bordeaux is one of the inkjet ink pioneers in digital inkjet ink manufacturing. The company, formed in 1999, offers solvent, water and other types of inkjet ink for all wide format printing. The company recently established Velvet Jet, a textile division dedicated for developing, manufacturing and marketing of inkjet inks for textile. Its latest development is a pigment ink, that can print on all types of fabrics, which enables to digitally print short runs of fashion of a mixed or multi-fibre fabric in one process.
Guy Evron, Marketing Director at Velvet Jet, the textile ink division of Bordeaux Digital Printink, said, “With the use of the Velvet Jet pigment ink, print houses are able to simplify the print procedure with a single pretreatment for all fabric and no post treatment required in order to fixate the ink to the fabric. This simple print process enables printing for a large range of applications in one print shop with one printing line, without the need to change inks.
This bold concept completely redefines digital textile printing, which until today, was characterised by multiple inks for different fabrics and complex print procedures.†(Read full interview with Guy Evron later in the issue)
ColorJet’s high speed printer, Metro: After receiving good reviews and orders at ITMA 2015, ColorJet Group, one of the largest manufacturers of digital printing machines in India, has now introduced METRO at GARFAB 2016. The METRO is a truly advanced high speed industrial grade digital textile printer, which fantastically incorporates the latest technology and efficient engineering to meet ever growing demands. It operates at a maximum speed of 362 sq m per hour.
The high speed is achieved through specially-designed jetting controls to optimise print heads performance, to match the high jetting frequency and the mechanical structure is designed to handle high speeds and precise dot placements Compatible to work with all types of inks like reactive acid disperse and pigment, this printer weaves magic on a variety of fabrics. Be it any kind of fabric, ranging from 0.1 mm to 30 mm including cotton, polyester, silk, viscose, wool, nylon, acetate and various blended fabrics can be printed on the METRO. With awesome scalable properties, this printer can suit all the needs of the textile printing business and delivers in the least payback period. It is equipped with a heater and feeder is capable of meeting the ever changing requirements of the fabric printing industry.
“Apart from the price being very competitive, since our digital textile printers are manufactured at a state-of-the-art manufacturing facility in India itself, buyers of our machines are eligible for various subsidies and benefits offered by the Government of India under EPCG & TUF schemes,†says Smarth Bansal, Brand Manager at ColorJet. (Read full interview with Smarth Bansal later in the issue)
Digital printing innovation by DyStar® & Zimmer: In response to the new industry standards, DyStar launched Jettex 4.0, the highest performing digital textile printing inks. The Jettex 4.0 ink ranges are available for all state-of-the-art and newly introduced printheads. Reactive, acid, disperse and sublimation inks are DyStar’s latest range. They also meet the most stringent ecological and fastness requirements. All newly launched Jettex Black inks exceed current limits and are setting new industry benchmarks towards deepest blacks.
The new Vat Inks are thus far none of the digital printing systems could fulfill the very high fastness requirements on inks in the home textile segment e.g. the very high fastness to light (especially in pale shades), high fastness to multiple washing and fastness to rubbing.
Based on their Indanthren Vat dyes, DyStar developed Jettex Vat inks, the first industrialised vat inks on the market. Their high performance characteristics include: high fastness to light, even in pale shades; high fastness to multiple washing; no crease markings like pigment prints; good fastness to rubbing; real, dark blacks compared to pigment prints; Vivid, brilliant shades; Excellent handle and drape of fabrics. The new Jettex Vat inks are the fit for the home textile market. The CMYK colour set is already available and DyStar will launch more shades in 2016 to offer a complete range to industries with high performance requirements.
Zimmer Austria and DyStar have been partnering for many years in developing inkjet technology. This cooperation is also the base of the VAT inkjet printing technology used in Colaris³. VAT inks are highly pigmented inks and to allow a reliable inkjet operation it has turned out that only circulating printheads can be used. Zimmer’s Colaris³ is based on the Fuji Dimatix Starfire technology which is one of the most robust and reliable printheads on the market using a circulation system.
Zimmer’s next gen printer: Recently, Zimmer Austria announced the next generation of their digital textile high performance printer. Next generation of COLARIS print lines with higher density print heads to cover even a wider range of application possibilities. The new COLARIS A-DX printer is based on a re-engineered structure of the well-known, solid built predecessor COLARIS printer. The modular layout is been continued and makes the printer ideal for customised solutions, no matter whether the application engine is to be used for printing of fashion fabrics, home textile, decorative fabrics, flags and banners, terry towel, fur blankets, carpet substrates, or as a digital coating unit. The printer can not only be complimented with the proven Magnoroll inline pre-treatment system, but now also with the COLARIS-DPT digital inline pre-treatment system, which is originating from the famous ChromoJET printer, that was initially developed as a digital carpet print system and has more recently also entered the blanket printing and the digital coating segment.
The scalability of the COLARIS A-DX will allow to configure the capacity in the range of 670 through 1.670 m²/h at 400/400 dpi with an ink limit of 7,5 ml/m² when using the SG-124/SA print head. Colaris Infiniti SK is the out-of-the-box solution at a very attractive price.
The printer is built in Shanghai, China and engineered by Zimmer, Austria. The high quality printer at lower price comes with 32 Seiko 1024 printheads.It attains high productivity with a two pass speed of 350m2/hour at 360x720dpi.Colaris Infiniti is the result of Zimmer’s textile and Colaris expertise with manufacturing and inkjet know how of Union International, China.
Aleph’s LaForte®Paper & LaForte®Textile printers: Aleph Srl, Italy presented to the international market the two new industrial large format digital printers LaForte®Paper and LaForte®Textile, delivering high performance and allowing the quickly creation of high quality finished product with precision. The arguments that convinced visitors and customers during the presentation were the technical and mechanical aspects of the two models as a result of an outstanding work masterfully executed by Aleph engineers and of course the typically Italian design and aesthetics. The printing demonstrations further emphasised the worth of the two models.
The two LaForte® machines are on top of their category and are becoming a reference point for the digital printing market for fabric and transfer paper, thanks to their high production capacity reaching a printing speed of 640sqm / h. The greatest benefit comes for all production companies, in Italy and in the world, which normally use digital printing exclusively for small batch, continuing to use the traditional printing with a considerable increase in costs; from now on, with the two industrial printers LaForte®Paper and LaForte®Textile they can take advantage of the benefits and innovation in digital printing for the entire production.
Both printers are equipped with the latest technology noticeable in the ease of use, the convenient operation of large and heavy reels (up to 10,000 m in length and 180 cm in width) and the use of inks that deliver maximum resolution up to 1200 dpi.
EFI acquires Rialco, presents new printers: EFI™ has very recently announced that it has acquired Rialco® Limited, one of Europe’s leading suppliers of dye powders and color products for digital print and industrial manufacturing industries. Rialco will now operate as part of EFI’s industrial inkjet business, and will continue to work closely with and support its existing clients as well as expand and grow its capabilities with new products and new customers. EFI plans to improve its inkjet portfolio with Rialco’s advanced ink component capabilities.
EFI featured six new EFI™ VUTEk® printers, including one of the world’s fastest production-class hybrid LED printers, a new, flagship high-volume inkjet press, and a VUTEk textile printer making its worldwide debut, at Fespa Digital 2016.
The 3-m-wide EFI VUTEk LX3 Pro hybrid roll/flatbed LED inkjet printer making its European debut at the show is a leader in production-class LED inkjet graphics print engine speeds with fast throughput of up to 318 sq m per hour. The printer also offers high-resolution greyscale imaging and its cool cure LED technology is a greener solution that reduces energy usage and costs while giving users the ability to print on a wider range of media, including media that cannot withstand the heat of other curing or drying methods.
EFI also premiered a new VUTEk printer to help customers capture new opportunities based on surging demand for high-quality, lightweight reusable fabric graphic soft signage used in retail visual merchandising, trade show graphics and other applications.
Indian Dyes Sales to distribute DTG Printers: The DTG Viper2 is among the most productive direct to garment printers in the industry. The DTG exclusive 4-2-1 platen system offers the versatility of printing four smaller images, two standard or one oversize image without the need for purchasing multiple size platens. The printers have high printing speed and are designed for industrial use.
The 4-2-1 garment pallet system is truly unique to the DTG Viper2 and prints multiple garments at a time as standard with our specialty pallet assembly with auto registration built in. Simply bring your designs from most major graphics software into our DTG RIP templates and your artwork is easily positioned with pinpoint registration (achieved via a unique conveyor garment loading system). The micro servo motor driven conveyor system produces perfect dot registration accurate to 0.017mm.
The M-Series is 100 per cent flexible with a multitude of Tex Loc™ platen options for kid’s sizes through to super wide prints. The M-Series bed in standard configuration supports two standard shirts with a unique bridge to allow extra wide prints to a maximum of 610 x 450mm (24 inch x 17.7 inch).
The following are some models available in DTG M-Series:
* DTG M2 Industrial Direct-to-Garment Printer: The M2 series machine is designed with a bespoke firmware specifically created for optimal print quality at higher production speeds by adoption of greater ink droplet control and accurate placement on the garment.
* DTG M4 Direct-to-Garment Printer: The DTG M4 printer is the ideal production centre for high volume print requirements. It boasts the same features as the industry leading M2 but with a far larger and scalable printable field area. The standard configuration of 4 x adult platens allows an operator to adopt aâ€set and forget†production workflow, effectively maximising output and minimising manpower.
* DTG M6 Direct-to-Garment Printer: The DTG Digital M6 model is designed for multiple garment prints and fashion panel decoration. A dual 4 color ink system supports a wider variety of ink styles for increased textile direct applications with 3 ink solutions developed specifically for flatbed inkjet printing to textiles.
SPGPrints’ new Nebula sublimation ink range: SPGPrints recently launched its new range of Nebula sublimation inks at FESPA Digital 2016, at Amsterdam, RAI.
Among other highlights, SPGPrints also presented information on the PIKE® digital printer and its full range of inks for the textile industry. The addition of Nebula Sublimation inks extends the realm of high quality digital textile printing with a wider colour gamut, reduced manufacturing costs and high print quality.
In the last two years, sublimation printing has established a strong position in digital textile printing for fashion applications driven by the improved quality of polyester fabrics, making them suitable for fashion garments and acceptable to the major brands.
Formulated for use with Kyocera print heads, SPGPrints’ Nebula range enables printers using any equipment with those heads to benefit from the gamut, vibrance, image quality, runnability and productivity made possible by the latest ink technologies. SPGPrints develops and manufactures its own inks at its ink plant Boxmeer, the Netherlands. The plant has recently completed the latest of three expansion programmes adding new equipment and doubling its production space.
Using specially formulated PIKE Reactive inks that eliminate mist, and Archer® technology, the PIKE printer can jet up to 4 mm between substrate and print head, making it possible to print a wide range of substrates in a single pass. This distance also means that print head damage from contact with substrates is virtually eliminated. An array of 43 Fujifilm Samba print heads fire at 32 KHz across the 1850 mm print width delivering variable dot sizes (from 2-10 pl) at a resolution of 1200 x 1200dpi. This powerful printer combines high volume output – up to 13 million sq m per year with high-quality print in a time-saving workflow, and opens a new era in the textile printing.
SPGPrints also plans to launch its JAVELIN® printer at ITM in Turkey in June. This versatile new printer, designed for production up to two million metres per year, offers a way for textile printers to take the first step into digital or for existing digital printers to step up their digital operations.
Archroma’s inkpresso® system: Archroma, a global leader in colour and specialty chemicals, officially introduced its new Inkpresso® system for digital printing at ITMA in Milan. Developed together with Ink-Situ, a Swiss technology provider, Inkpresso will change the way inks are supplied to digital printers. The system brings together benefits that were unattainable so far in inkjet printing: Production flexibility, no shelf-life problems, a larger color spectrum and the possibility of an individual coloristic fingerprint. More than 20 billion linear meters of printed textiles are produced every year. Currently, only around two percent of these are made using digital printing techniques.
The central component of the system is the Inkpresso Ink Formulation Unit (IFU), where eight color modules are available. The colors can be mixed to meet manufacturers’ specific needs – at any time. Depending on the size and complexity of the printing company, inks can be sent directly from the Inkpresso IFU to the printer through a piping system, or several printers can be supplied simultaneously using a special distribution unit. In addition, colors can be stored for several weeks in a storage unit.
The digital textile valley is Italian
Italy has played a major role in the technological transformation of the textile printing industry. A key figure in the change has been the textile district in the Como area, which has historically been at the leading edge of silk-screen production. Spurred by the need to stem the flight of production towards the Far East, and aware of having to focus on the sector’s creativity and know how, the textile firms in the Como area have been able to react, restructure and restart. They have counted on their well-established international vocation—70 per cent of production is for export—and on technological evolution: digital textile printing has gone from 2 per cent of total production in 2003 to 58 per cent in 2013, and, based on estimates, it will reach 81 per cent in 2017. What this means is that 8 sq m out of 10 of textiles will be printed digitally. These figures prove that in the Italian Digital Textile Valley, the evolution towards digital printing has already happened.
From the world of high fashion to fast fashion clothing to sportswear, from accessories to furnishings, the boom in digital printing on textiles has contributed to transforming the dynamics underlying the individual sectors, in creative, productive and application terms. Digital inkjet technology opens the doors to creativity by encouraging photographic reproduction and the creation of more complex designs, as well as to experimentation with brand-new applications. It has also modified production process logic, reducing the time to market and enabling on demand production, in small and medium-sized volumes and in large numbers of variations, without any economic impact.
Digital technology is behind the phenomenon of fast fashion, which we have seen explode and quickly establish itself over the last decade. Taking advantage of the new creative and productive opportunities provided by inkjet printing, the so-called fast fashion retailers—with Zara and H&M as trailblazers—have profoundly transformed the dynamics of the offering, introducing a rotation of the collections that is no longer seasonal but fortnightly and, in certain cases, weekly. This formula—an offering of assorted items, continually renewed and at competitive prices—has had enormous success at a mass-market level. Digital printing has enabled—on the production level—the drastic reduction of the time to market, in other words the production schedules from the creation of the design to the delivery of the finished product, and the fashion brand owners immediately identified and seized this opportunity.
The digitally printed textiles for interior furnishings are a relatively small segment – around 10 per cent of the digital textile printing market. However, there is considerable development potential given the breadth of the sector—which includes household linen, curtains, sofas, napkins and wallpaper—and the growing interest from brand owners.
The use of inkjet in textile printing began in the graphics sector with many print service providers producing signs, banners and flags on wide and super-wide format roll-to-roll devices, predominantly using polyester and sublimation technology. At the same time, some fabric producers took notice of digital wide format printing as a way to produce short run samples of fabrics or strike-off samples. This early usage turned few innovators rooted in fabric manufacturing to integrate the power of inkjet printing with traditional fabric manufacturing technologies such as fabric pre-and post- treatment, and belt transportation both critical for ultimate output quality.
As with other digital technology, inkjet continues to push the boundaries in terms of speed, quality and capability year on year. There is now a new generation of roll-to-roll inkjet printer devices ranging from entry level to full production which between them support the full range of inks required for different fabric types and applications from low-volume machines for sublimation printing to systems capable of over 8,000 m2/h standard quality in single pass printing – according to information from the technical specifications announced by some vendors. These single pass printing systems are mainly used in the apparel and decor markets.
Digital direct to garment printing
In the early 2000s, direct to garment (DTG) printing on t-shirts had emerged using modified desktop inkjet printers, pigment inks and fabric pre-treatment. Today this market has evolved to drive over 200 million garments annually as the initial modified systems developed into a multi-vendor industry encompassing dedicated DTG machines from desktop devices printing around 20 t-shirts per hour up to production systems that in some cases can print more than 400 t-shirts per hour.
Acid inks, water-based dispersion inks and pigment inks are currently the most used ink types in the digital textile industry. Reactive inks are the ones most used for natural textiles intended for fashion and furnishing applications while pigment colourants are also starting to be used, especially for large volume productions. Animal textiles, such as silk and wool, require the use of reactive and acid inks for items of clothing and home decor. There are differences between the different synthetic fibres: for polyester—mostly used in applications for soft signage, advertising printing and furnishings—dispersion inks are used while for polyamide—much used in sports clothing made in nylon and lycra—the right choice is acid inks. Finally, viscose, the artificial textile par excellence, requires reactive inks.
Technology and the environment
In a period when attention is growing in environmental sustainability, digital printing has caused a decisive shift in the textile industry towards a much greener and more efficient management of the entire supply chain. The difference compared to traditional processes has been clear since the early years when textile print houses and textile firms engaged in the digital transformation have started to see the ecological benefits, as well as the economic ones, tied to the new technology. If the environmental advantages brought by digital printing are universally recognised and tracked and measured within many companies, there is a new paradigm to face up to: sustainability as a new lever of competitiveness for companies in the sector.
Less water, less energy: these are the two factors that from the start have attracted the sector’s attention. Going forward, the reduction has been put into effect also in other parts of the process. Digital technology allows a significant containment of the consumption of inks in the printing stage thanks to the lower quantity of colour required by the systems’ set-up time and to the use, of almost the totality of the colour put into the machine – a factor which reduces waste. The road of environmental and economic sustainability is the one that, thanks to the support of digital printing, the companies in the textile sector intend to take in the present and the near future. Not only for the competitive advantages met in these years of transformation but also in the face of the new sensitivity that is being confirmed in the market: the demand for goods produced sustainably and not harmfully is also, becoming a priority for the brand owners and end consumers.
Future for digital textile printing
The textile digital printing technology has made giant strides since it was first introduced in the textile industry. Given the broad range of inkjet printing solutions currently available—ranging from entry level to full production—many textile manufacturers are moving towards the digital technology. As a result, production digital textile printing machines tend to be placed in textile mills that are replacing some traditional rotary or screen printing volume with digital ready for cut and sew applications. The adoption of digital has been so far driven by a number of factors, namely the need to improve the environmental impact and the output design creativity, as well as to satisfy the demand for shorter print volumes and faster turnarounds more effectively.
Looking at the near future, digital printing will continue to penetrate the traditional textile printing industry at strong double digit growth rates per year. This trend will be driven through continued technological developments across the range of inks and substrates with the aim of bringing the cost to print digitally down per meter squared or per garment and the flexibility of ink and substrate usage up, all within the context of environmental conservation. Whilst in the longer term as digital volumes increase and economies of scale start to kick in with production of digital printhead and ink technologies there will be a drive to bring the cost down further enabling, for example, widespread take up of digital pigment ink printing on natural fibres for the home textiles sector. When it comes to the digital production printing systems, the technology providers will keep their focus on enhancing speed and productivity and they will also be engaged in addressing the demand rising from the market for a broader capacity in finishing and print enrichment.
AT.E. has further strengthened its portfolio of high quality products. Zimmer Austria has partnered with A.T.E. since 2013 for the marketing of Zimmer’s textile and carpet digital printing solutions in India. A.T.E. has a team of well trained and experienced engineers, who have been extensively trained in Zimmer machines and can handle the erection, commissioning and trouble-shooting of these machines independently. Customers can now avail of quick and cost effective services from A.T.E.
Recently, Zimmer Austria announced the next generation of their digital textile high performance printer. Next generation of COLARIS print lines with higher density print heads to cover even a wider range of application possibilities. The new COLARIS A-DX printer is ba