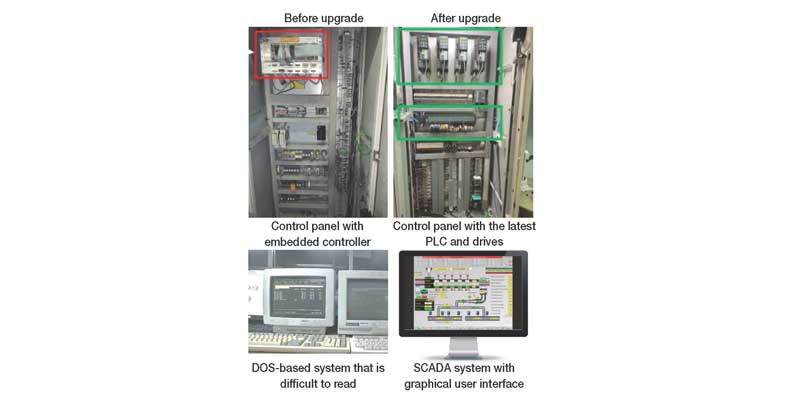
Convert old generation extruder from a liability to an asset!
With its deep domain knowledge in automation and upgradation of textile machinery, A.T.E. undertakes customised upgrade of an older extruder.
As with any older machine, synthetic textile manufacturers with aging extruders face many challenges managing these machines, such as:
- Increased downtime leading to loss of production: (a) Frequent failures due to obsolete hardware and electronics, and (b) Instances of breakdowns and tripping are higher
- High maintenance costs: (a) Expensive OEM services; special purpose drives manufactured only by OEM, which are expensive and can be hard to obtain, and (b) Unavailability of spares, and if they are available, it is often at an exorbitant cost
- Production reporting is either limited or unavailable: Out-of-date communication protocols
- Difficult to use DOS-based monitoring systems: Require skilled workers and a steep learning curve for new workers
Manufacturers therefore find themselves in a quandary: do they make a massive investment in new, expensive machinery? Or, should they continue investing time and effort into maintaining these older machines?
Solution
While the extruder itself may be mechanically sound and operational, the problems mainly originate from outmoded control systems. The solution, therefore, is the complete overhaul of the control systems.
A.T.E. with its deep domain knowledge in automation and upgradation of textile machinery can undertake a full-fledged, customised upgrade of an older extruder. The upgrade programme would consist of:
• Replace all end-of-life embedded hardware with latest PLCs, SCADA systems and HMIs
• Replacing special purpose OEM drives with standard drives which are easily available in the market, like Yaskawa and Siemens
• Production reporting and trends covering a minimum period of 1 year
• Archived alarm logging covering a minimum period of 1 year
• PROFINET communication protocol for a future-ready system
A comprehensive upgrade from A.T.E. leads to many benefits:
- Improved machine performance: (a) Increased machine uptime, (b) Improved machine efficiency and production, and (c) Diagnostic features in graphics reduces instances of breakdowns as well as start-up time after preventive maintenance
- Reduced maintenance costs: (a) Service and training support is easier and cheaper, and (b) PLC and drive hardware spares are easily available
- Production reporting now available: (a) WinCC SCADA systems installed enabling current and historical production reporting with trends, and (b) Updated latest PROFINET communication protocol allows data transfer at higher speeds without data loss resulting in accurate data logging
- Easy-to-use monitoring system: HMIs with GUI that are easier to use with a gentle learning curve for new workers
- By far the more economical option, compared to buying new machines
- The machine life is expected to be augmented by10 years!
Additionally, operators have greater control over the machine as the DOS-based systems are replaced with user-friendly GUIs of the process. The control system is IoT-ready, which provides an additional layer of future-proofing.
With the multitude of benefits that an A.T.E. upgrade brings, it is not surprising that the synthetic textile manufacturers are increasingly choosing this option for their extruders.
For details, contact A.T.E. Enterprises Private Limited on Mob: +91 22 6676 6100 or email: automation@ategroup.com