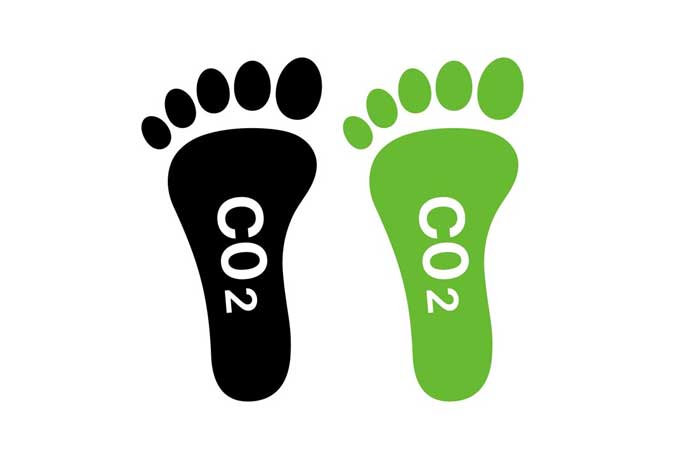
Carbon footprint assessment in textile wet processing industries
Vijay Shirole believes that through such assessments, textile industries can work toward more sustainable practices and meet global environmental standards.
The carbon footprint, which represents the total amount of greenhouse gases (GHGs) emitted by human activities, has become a key metric in the context of climate change mitigation. These emissions contribute directly to global warming and climate change, which threaten ecosystems, economies, and human health.
The carbon footprint of textile wet processing industries refers to the total amount of greenhouse gases (GHGs) emitted as a result of various activities contributing to carbon emissions during textile wet processing, including energy consumption, water heating, chemical reactions, and waste disposal.
- Energy use (electricity, steam, fuel)
- Water and chemical inputs (dyes, surfactants, etc.)
- Emissions from dyeing and finishing
- Transportation and Supply Chain Emissions
These processes are highly energy-intensive and often involve substantial water and chemical use, making it crucial to calculate the associated carbon emissions in order to identify opportunities for reductions and improve sustainability.
Process wise CO2 emissions and its contribution: The textile industry, according to the US Energy Information Administration, is the 5th largest contributor to CO2 emissions. Thus, the textile industry is huge and is one of the largest sources of greenhouse gasses on Earth. In 2008, annual global textile production was estimated at 60 billion kg of fabric. The estimated energy and water needed to produce such quantity of fabric is considered to be
- 1,074 bn kWh of electricity or 132 million MT of coal and
- About 6-9 trillion litres of water
Thus, the thermal energy required per metre of cloth is 4,500-5,500 Kcal and the electrical energy required per meter of cloth is 0.45-0.55 kwh.
Total carbon footprint of textile wet processing: The carbon footprint of the textile wet processing industry varies based on several factors, including energy consumption, the type of chemicals used, the scale of production, and the geographic location of the facility. Here’s an estimated breakdown of the overall carbon footprintin a typical textile wet processing facility:
Process | Energy consumption (kWh/unit) | CO2 emissions (kg CO2/unit) | Contribution to total carbon footprint (%) | Key factors affecting emissions |
Desizing (starch removal) | 1.5 – 3.5 kWh/kg fabric | 0.9 – 2.1 kg CO2/kg fabric | 20 – 30% | Energy used for heating water, steam, and drying fabrics |
Scouring | 1.0 – 2.5 kWh/kg fabric | 0.6 – 1.5 kg CO2/kg fabric | Energy consumption in hot water and chemical use | |
Bleaching | 1.5 – 3.0 kWh/kg fabric | 0.9 – 1.8 kg CO2/kg fabric | High energy for heat and oxygen-based bleaching agents | |
Dyeing (reactive/acid) | 3.0 – 6.0 kWh/kg fabric | 1.8 – 3.6 kg CO2/kg fabric | 35 – 45% | Energy for heat and steam, and use of energy-intensive dyes |
Printing | 2.0 – 4.0 kWh/kg fabric | 1.2 – 2.4 kg CO2/kg fabric | 10 – 15% | Energy use in printing machines, curing, and drying |
Finishing (softening, starching, anti-wrinkle treatment) | 0.8 – 2.0 kWh/kg fabric | 0.5 – 1.2 kg CO2/kg fabric | 5 – 10% | Energy for steaming, heat-setting, and chemical treatments |
Water and wastewater treatment | 0.5 – 1.0 kWh/m³ treated water | 0.3 – 0.6 kg CO2/m³ treated water | 5 – 10% | Energy for pumping, filtration, and chemical treatment |
Chemical production and transport | 0.2 – 0.5 kg CO2/kg fabric | 5 – 10% | Emissions associated with the production, transportation, and storage of chemicals used in the processes | |
Miscellaneous (maintenance, building energy, packaging) | 0.2 – 0.4 kg CO2/kg fabric | 5 – 10% | General facility operations and maintenance activities, as well as the impact of packaging materials used in shipping products |
Note: This table is meant to serve as a general guideline and may vary depending on the specific setup of a textile processing plant. For more precise data, a life cycle assessment (LCA) for a specific facility or product would be required.
Total carbon footprint of textile wet processing:
- Average range: 3.0 – 9.0 kg CO2 per kg fabric processed
The importance of carbon footprint assessment
A carbon footprint assessmentinvolves the quantification of greenhouse gas emissions directly and indirectly caused by an individual, organisation, event, or product. It enables stakeholders—governments, corporations, and consumers—to:
- Quantify environmental impact: By understanding the total GHG emissions from an activity or organisation, stakeholders can gauge the environmental consequences and focus on the largest sources of emissions.
- Support decision-making: Accurate carbon footprint data can help organisations and governments make informed decisions on resource allocation, sustainability investments, and carbon mitigation strategies.
- Identify hotspots for emission reductions: Carbon footprint assessments can highlight areas where the greatest emissions occur (e.g., energy use, transportation, waste) and guide strategies to reduce these emissions.
- Regulatory compliance: Many countries and regions are now mandating emissions reporting, including carbon footprint calculations, as part of environmental laws. Accurate assessments help organisations comply with regulations and contribute to national and international GHG reduction targets.
- Improve transparency and accountability: By measuring and reporting carbon footprints, organisations can demonstrate environmental responsibility, which can enhance their brand image and strengthen consumer trust.
- Enable carbon offsetting: Accurate assessments allow organisations to identify emissions that cannot be eliminated and offset them through carbon credits or projects aimed at reducing global emissions.
Key concepts in carbon footprint calculation
A carbon footprint is typically calculated based on the amount of greenhouse gas emissions (GHGs), expressed incarbon dioxide equivalents (CO₂e), froma specific activity or product. The major GHGs include:
- Carbon Dioxide (CO₂): The most common greenhouse gas, emitted primarily from the burning of fossil fuels.
- Methane (CH₄): A potent greenhouse gas emitted from agriculture, waste management, and energy production.
- Nitrous Oxide (N₂O): Emitted from agricultural practices, industrial processes, and the use of fertilizers.
- Fluorinated gases: A group of synthetic greenhouse gases used in industrial applications such as refrigeration and air conditioning.
These gases have different global warming potentials (GWPs). CO₂e is used to standardise the impact of all gases, making it easier to compare and aggregate emissions.
Methodology for carbon footprint calculation
To calculate the carbon footprint of textile wet processing, we can break down the process into several components and estimate emissions based on key factors such as energy consumption, water use, and chemical inputs. The most widely used methodology is Life Cycle Assessment (LCA), which quantifies the environmental impacts (including carbon footprint) of each stage in the textile production lifecycle.
The Carbon Footprint is assessed in 2 layers;
- Primary footprint monitors carbon emission directly through energy consumption – burning fossil fuels for electricity, heating and transportation, etc.
- Secondary footprint- relates to indirect carbon emissions (Life cycle of products and Sustainability). Thus, the most effective way to decrease a carbon footprint is to either decrease the amount of energy needed for production or to decrease the dependence on carbon emitting fuels
The calculation process generally involves quantifying direct emissions (e.g., from energy use) and indirect emissions (e.g., from the production of chemicals or from transportation). The following steps outline the methodology and approach for calculating the carbon footprint for textile wet processing.
Key steps in carbon footprint calculation
- Identify boundaries: Determine the scope of the study (cradle-to-gate, cradle-to-cradle, or cradle-to-grave). For wet processing, it typically covers the stages from fabric preparation (e.g., dyeing, bleaching) to the final product leaving the factory.
- Data collection: Collect data on:
- Energy consumption (electricity, steam, fuel) used in wet processing operations.
- Water use for dyeing, washing, and finishing processes.
- Chemicals and auxiliary inputs used in dyeing, bleaching, finishing, and printing.
- Wastewater and chemical waste generated during the processes.
- Transportation and logistics (for materials, chemicals, etc.).
Emission factors: Apply emission factors to convert the inputs (energy, water, chemicals) into CO₂-equivalent (CO₂e) emissions. Emission factors are available in databases such as those provided by the Intergovernmental Panel on Climate Change (IPCC), EPA, and Eco invent.
Calculate direct and indirect emissions:
- Direct emissions: These include emissions from energy consumption, fuel use, and process-related emissions (e.g., CO₂ released from burning natural gas for steam generation).
- Indirect emissions: These emissions result from the supply chain, such as those associated with the production and transportation of chemicals, dyes, or raw materials.
Summing up emissions, aggregate the emissions from all stages of textile wet processing to obtain the total carbon footprint.
Strategies for reducing carbon footprint in textile wet processing
Certain strategies are listed below;
- Cleaner production technologies: Identification of clean technologies that reduce energy consumption, chemical use, and waste generation.
- Eco-labelling and certification: Overview of environmental certifications and standards such as GOTS (Global Organic Textile Standard), OEKO-TEX, and ISO 14001, and their role in driving sustainable practices.
- Circular economy in textiles: Exploration of the potential of circular economy principles, such as recycling and reusing textile waste, in reducing the carbon footprint of textile production.
- Shift toward sustainable fabrics: Discussion on the use of sustainable materials, including organic cotton, hemp, and recycled fibres, as a means to reduce environmental impacts.
- Energy efficiency: Implementing energy-efficient technologies and practices can significantly reduce Scope 1 and 2 emissions.
- Renewable energy: Transitioning to renewable energy sources (e.g., solar, wind, hydro) can reduce Scope 2 emissions from electricity use.
- Sustainable transportation: Shifting to electric vehicles (EVs), improving logistics, and reducing travel distances can cut down emissions in Scope 3 from transportation.
- Circular economy: Reducing, reusing, and recycling materials can reduce the carbon footprint in the product lifecycle (Scope 3).
Conclusion
The carbon footprint calculation for textile wet processing involves estimating emissions from key activities like energy use, water treatment, chemical consumption, and waste management. By applying emission factors to these activities, companies can calculate the total carbon footprint of their processes. These calculations are crucial for identifying areas where energy efficiency, chemical use, and water consumption can be optimised to reduce the environmental impact of textile production. Through such assessments, textile industries can work toward more sustainable practices and meet global environmental standards. If the facility wants to assess the carbon footprint, BTRA team is ready to assist the same.
References
- Comprehensive list of scholarly articles, industry reports, and other relevant sources used in the paper.
- Allwood, J. M., et al. (2006). “The Environmental Impacts of the Textile Industry.” Cambridge University Press.
- Kering (2020). “Environmental Profit & Loss: Textile Footprint Report.”
- Global Fashion Agenda (2021). “Circular Fashion: The Apparel Industry’s New Agenda.”
- ISO 14040:2006, “Environmental Management—Life Cycle Assessment—Principles and Framework.”
- Sharma, P., et al. (2020). “Energy and Water Management in Textile Wet Processing.” Journal of Cleaner Production, 123, 142-158.
About the author:

Vijay Shirole is presently working as Senior Scientific Officer-I in Technical Services Department at BTRA, Mumbai, he has more than 20 years of experience in textile processing industry. He has worked mainly in home textile, yarn dyeing shirting divisions and has vast experience in quality as well as process control in textile processing.