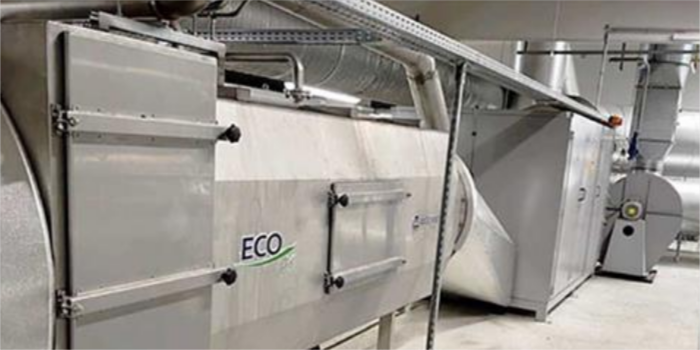
BRÜCKNER prepares FEINJERSEY for sustainable production
FEINJERSEY, the Austrian textile producer, and BRÜCKNER, the German textile machinery manufacturer, have a long-standing partnership. They both develop and produce in Austria and Germany.
Leonberg
FEINJERSEY, the Austrian textile producer,
and BRÜCKNER, the German textile machinery manufacturer, have a long-standing
partnership. They both develop and produce in Austria and Germany.
The Feinjersey
Group is a textile company that operates internationally. The value chain of
the company ranges from yarn processing to the finished product. The company
follows high-quality standards and has annual sales of 45 million Euros. The
company knits, dyes, and finishes top-quality knitted fabrics. The end products
include functional underwear for fashion and sports, light and luxurious day
and nightwear, professional work wear, shape wear, and children’s clothing. It
also produces fabrics for the automotive industry, coating substrate for artificial
leather or foils, laminating backings, and construction textiles or fabrics for
medical technology. The company is certified with the Bluesign textile seal. As
a matter of fact, Feinjersey uses its own photovoltaic system and heat-recovery
and exhaust air purification systems on all its stenters. All 6 stenters here
are made by BRÜCKNER.
The BRÜCKNER
line has a working width of 4.20 m which is used for the finishing of elastic
and extremely sensitive knitted fabric. The stenter is equipped with an indirect
gas heating system to avoid yellowing on the fabric. The heat-setting process
is extracted from the dryer and cleaned in a BRÜCK-NER ECO-AIR exhaust air so
that when they are released into the atmosphere, they are purified. There are
two stages of this air treatment on the stenter.
?
The first
stage is an ECO-HEAT heat-recovery system air. Under this, using the 12 plate
heat exchangers, the exhaust air heat is pushed into the fresh incoming air
which is first pre-heated and then released into the stenter for the drying
process. This not only increases the drying capacity but also reduces energy
consumption.
?
The second
stage is an ECO-AIR exhaust air scrubber. It performs two tasks; firstly, it
cools down the exhaust air and then binds oily pollutants in water. Due to the
design of the exhaust air scrubber, only 1 cbm of wastewater is produced every
week. The oil skimmer is used to separate the oil-containing substances
extracted from the exhaust.
BRÜCKNER exhaust air treatment system is proven
and hence, Feinjersey can safely comply with the prescribed emission limits.
Source – Press release of “Bruckner”
Image Source: Press release of “Bruckner
Also Read: