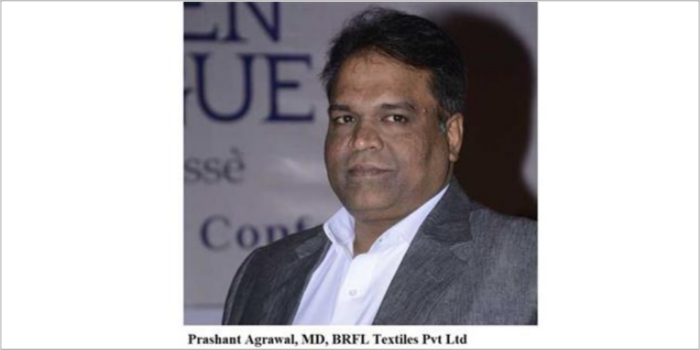
BRFL Textiles develops sustainable dyeing process
The new sulphur dyeing process does not require water. BRFL Textiles will shortly increase efficiency of reverse osmosis unit from 50% to 90% resulting in recycling capability of 7.2 million litres of water per day
Mumbai, April 16, 2021
BRFL Textiles Pvt Ltd (BTPL), home to India’s largest single-roof state-of-the-art fabric processing facility, has set a new benchmark in sustainability by introducing a new sulphur dyeing process by continuous dyeing method that does not require water. BTPL is the first company in the textile sector to implement this new process of dyeing, making them the pioneers of this innovative sustainable process.
As a sustainable manufacturing unit, BTPL, since inception, has taken efforts to limit carbon emission and increase water recycling through multiple ways. The current efficiency of the reverse osmosis unit at BRFL Textiles’ Tarapur plant facilitates the unit to reuse 50% of the effluent water, enabling the plant to recycle upto 4 million litres of water per day. The company is looking to further strengthen this efficiency and aims to increase the water recycling level to 90% in the next 3 months, enabling the plant to recycle upto 7.2 million litres of water per day. Additionally, most of the reactive dyeing processed in the plant is undertaken with e-control process, thereby avoiding salt which in turn avoids increasing the TDS content of water.
BTPL also uses its energy co-generation design at its Tarapur plant, which enables it to reuse 48 tonnes of steam per hour, and save 250 tonnes of coal per day, leading to a significant reduction in carbon emissions that exceed even the sustainability benchmarks of global textile companies.
BTPL implements its sustainability measures across its products as well. A majority of the fabrics produced by BTPL, such as linen and cotton, are sold in its natural form, making it a part of the sustainability chain. Likewise, a large part of the linen and linen blended collection is produced by maintaining a natural fibre colour without adding any dye or colour to the fabric. In addition to this, the polyester blended fabric produced by the plant is made using recycled polyester.
Speaking on the sustainability measures of the plant, Prashant Agrawal, Managing Director at BRFL Textiles Pvt Ltd (BTPL), said, “At BTPL, we are committed to adopt a sustainable approach across our company, and we will continue to accelerate the sustainability drive as we expand our output and market presence. Today, greenhouse gas emission and scarcity of potable water represent a substantial sustainability challenge across the world. We are proud to combat both these areas through our state-of-the-art processes that set new sustainability benchmarks across the global textile industry and enable a more sustainable future for our vast global customer base. We are also hopeful that the Indian textile industry strengthens its focus on the need for sustainability in the sector and encourages and supports companies in the sector to innovate and adopt sustainable practices across operations.â€
BTPL was recently formed as a separate entity in August 2020 as part of a restructuring process undertaken by Bombay Rayon Fashions Limited, in which it hived-off its yarn dyeing & fabric processing units located in Tarapur, into BRFL Textiles Pvt Ltd (BTPL) by way of a slump sale on a going concern basis and attracted private equity funding for growth. The Company’s brands, including Bombay Rayon, BRFL, Linen Vogue, Giza Classe, Dickens & Browne and others, were also a part of the transaction.
BTPL has a strong presence in the B2B and B2C space along with long-standing relations with leading brands across the globe, and sells through large garmenters in India who also sell to domestic brands. On the domestic branded sales front, the distribution network of BTPL is spread across its own EBOs, over 100 distributors and over 8000 retailers.
BRFL Textiles is engaged in processing a wide range of fabrics at its plant located at Tarapur in Maharastra, India. With its annual processing capacity of 144 million meters (400,000 meters per day), the Tarapur plant is the largest single roof fabric processing unit in India adequately supported by its captive power, effluent treatment, RO water and other utilities enabling cost competitiveness. It also has a captive yarn dyeing unit with annual capacity of 10.6 million kg (29 tonnes per day).