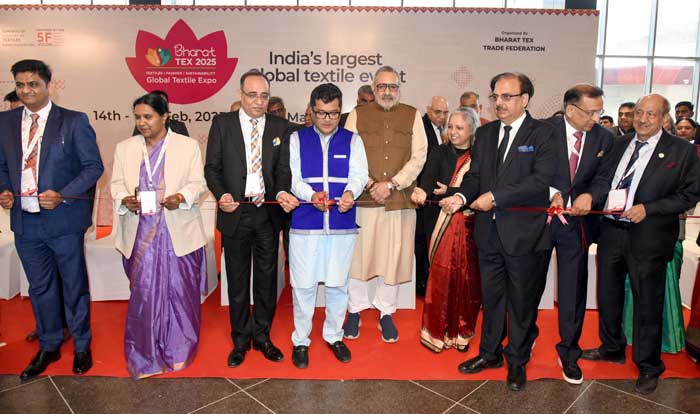
Bharat Tex 2025: Way to Go!
Following a successful second edition, Bharat Tex has firmly established itself among the leading textile industry events globally, writes ITJ’s Manish Pant.
With an exhibition area spread over 2.2 million square feet, more than 5,000 exhibitors, and over 120,000 trade visitors from 120 plus countries, Bharat Tex 2025, held at Bharat Mandapam in New Delhi from February 14-17, was a resounding success. As India aims to increase its textile exports to ₹9 trillion by 2030 from ₹3 trillion, the event showcased the country’s ‘Farm to Fibre, Fabric, Fashion, and Foreign Markets’ vision by providing a large platform for innovation, sustainability, and global collaboration.
While celebrating this year’s theme of ‘Resilient Global Value Chains and Textile Sustainability’, the event provided a comprehensive view of the country’s textile ecosystem, encompassing raw materials and fibres, finished products, technical textiles, home furnishings, and high-end fashion. Related exhibitions on accessories, garment machinery, dyes and chemicals, and handicrafts were held at the India Expo Centre and Mart in Greater Noida. Multiple conferences, seminars, CEO roundtables, and B2B and G2G meetings also took place on the sidelines. The Indian Textile Journal (ITJ) spoke to a cross-section of the Indian textile industry to get a perspective on the emerging opportunities and challenges and their potential solutions.
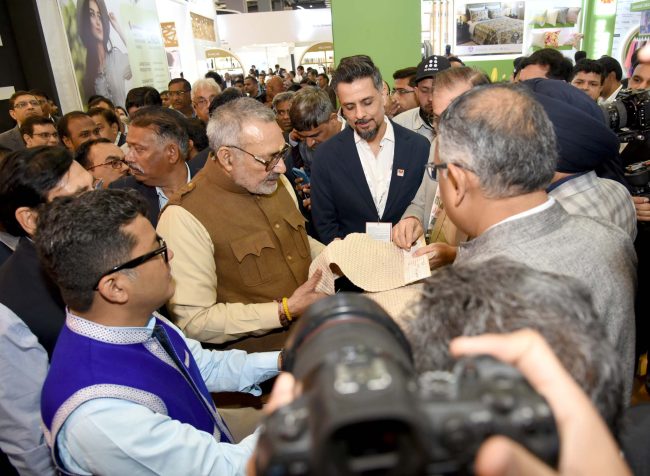
Getting future-ready
The political crisis in Bangladesh, which resulted in garment and fabric buyers shifting to India, the expectation of a return to stability in geopolitics, and the government’s support for turning the textile sector into a $3.5 trillion industry are major positives, says Rajeev Gupta, CEO, RSWM, LNJ Bhilwara Group’s flagship arm. “In the recent Union Budget, the allocation for the textile sector has increased to ₹53 billion from ₹45 billion [in FY2024-25], which is a significant increase. The introduction of import duty on Chinese goods or imported fabric will also support Indian weavers,” he said.
The company is a leading manufacturer of yarns, knits, denim, and fabrics in India. While the demand for cotton yarn remains healthy, the demand for mélange yarn has slowly revived in the last six months. However, with the decline in demand from Turkey and parts of Europe, synthetic yarn sales have struggled, noted Gupta. With the acquisition of Ginni Filaments in March of last year, RSWM has expanded its capacity. “We have worked on product development, efficiency, and quality to improve our knitting division. There has been some improvement in domestic demand for knitted fabric though.” On the sustainability side, the company manufactures nearly 130 metric tonnes of polyester fibre from 6 million PET bottles daily. LNG denim, meanwhile, continues to be a trusted name in denim-based clothing.
He said that given the highly fragmented nature of the textile business, the company was committed to improving efficiencies, controlling costs, and expanding product development. “RSWM is focusing largely on product development and sustainability-related initiatives, where you can create demand.” Gupta, who joined RSWM in December, has the twin challenge of maintaining the LNJ Bhilwara Group’s legacy while applying modern management tools to create a strong global brand with a strong Indian ethos.
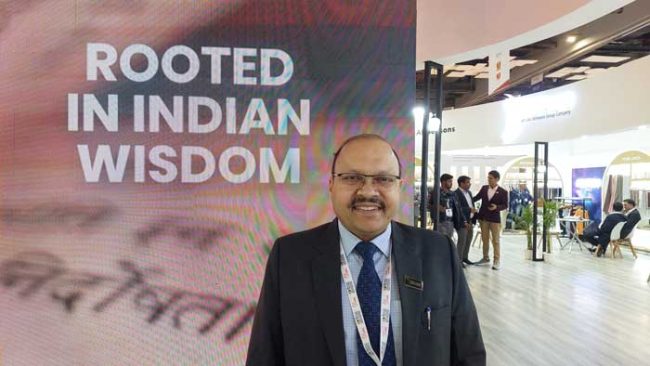
Rajeev Gupta, CEO, RSWM
The political crisis in Bangladesh, which resulted in garment and fabric buyers shifting to India, the expectation of a return to stability in geopolitics, and the government’s support for turning the textile sector into a $3.5 trillion industry are major positives, says Rajeev Gupta, CEO, RSWM, LNJ Bhilwara Group’s flagship arm. “In the recent Union Budget, the allocation for the textile sector has increased to ₹53 billion from ₹45 billion [in FY2024-25], which is a significant increase. The introduction of import duty on Chinese goods or imported fabric will also support Indian weavers,” he said.
The company is a leading manufacturer of yarns, knits, denim, and fabrics in India. While the demand for cotton yarn remains healthy, the demand for mélange yarn has slowly revived in the last six months. However, with the decline in demand from Turkey and parts of Europe, synthetic yarn sales have struggled, noted Gupta. With the acquisition of Ginni Filaments in March of last year, RSWM has expanded its capacity. “We have worked on product development, efficiency, and quality to improve our knitting division. There has been some improvement in domestic demand for knitted fabric though.” On the sustainability side, the company manufactures nearly 130 metric tonnes of polyester fibre from 6 million PET bottles daily. LNG denim, meanwhile, continues to be a trusted name in denim-based clothing.
He said that given the highly fragmented nature of the textile business, the company was committed to improving efficiencies, controlling costs, and expanding product development. “RSWM is focusing largely on product development and sustainability-related initiatives, where you can create demand.” Gupta, who joined RSWM in December, has the twin challenge of maintaining the LNJ Bhilwara Group’s legacy while applying modern management tools to create a strong global brand with a strong Indian ethos.
Technology is the disruptor
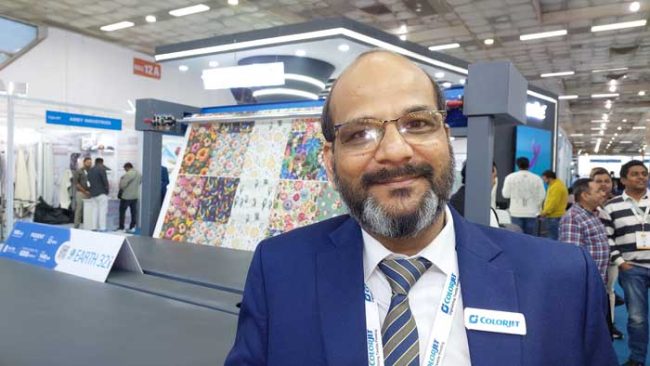
Arun Varshney, VP & Head of Textile, ColorJet India
Expanding digitalisation and the growing demand for sustainable clothing are transforming textile printing, avers Arun Varshney, VP & Head of Textile at ColorJet India. Due to the heavy discharge of effluents during dyeing and printing, the segment has traditionally been looked down upon in the textile value chain. But that’s slowly changing. “With the adoption of digital printing, there has been a drastic two-thirds reduction in water discharge compared to analogue printing,” informed Varshney. But there is more to come. “We are now talking about pigment printing, which is almost waterless, with no steaming or washing required. As a result, only around 5 per cent of water is required for the entire process.”
Be it home textiles or clothing, he felt the domestic market would be an important growth driver. At the same time, the textile sector must be open to adopting these technology-based eco-friendly solutions that are presently perceived as expensive by a large section of the industry. “Wider adoption of such solutions will help achieve economies of scale and offer competitively priced products.”
As a homegrown entity, the company is immensely proud to be the country’s largest manufacturer of digital inkjet printers for the textile sector. Its 350,000 sq ft factory in Noida near Delhi churns out high-speed machines for the Indian and international markets. “We currently have a 40 per cent share of the domestic market,” said Varshney, adding, “We also export 100 per cent Made in India products to around 25 countries.”
Enthused by the response to their digital printing products, he expects demand for pigment printing products to pick up traction. “We are seeing good adoption in the digital printing segment. As pigment printing also starts growing, we will have a major chunk of the overall market.” In the long term, he saw India, along with other textile-producing countries in the Southeast Asian region, acquiring a leadership position in sustainable textiles. “We grow a lot of cotton, have good spinning and fabric manufacturing capacity, and have a legacy going back thousands of years. This right amalgamation of everything makes one very positive about the Indian textile industry’s potential.”
Recycling waste to wealth
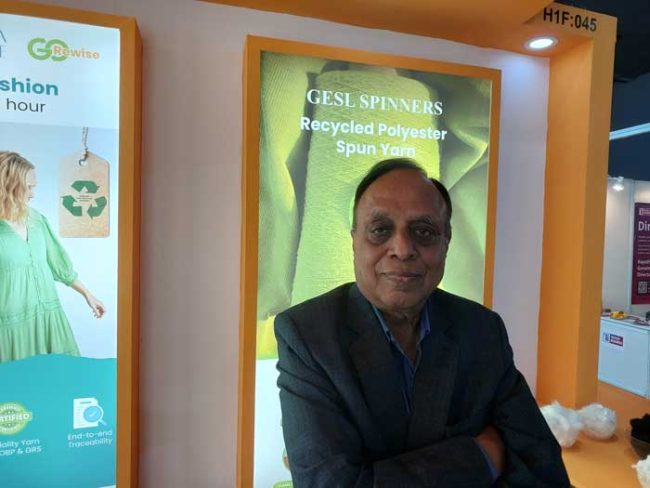
BP Sultania, Joint President, Ganesha Ecosphere
The country’s largest recycled polyethylene terephthalate (R-PET) player sees a bright future for the industry, provided certain immediate concerns are addressed on priority. “The high quality offered by Indian manufacturers makes our products readily accepted everywhere. Our recycled fibre has largely replaced virgin polyester. The same situation is now developing in filament yarns,” observed BP Sultania, Joint President, Ganesha Ecosphere. He claimed that more than 80 per cent of their overseas orders came from repeat clientele.
The company has been expanding manufacturing and sourcing to keep up with the growth. In the next five years, it projects its total PET recycling capacity to reach around 1,000 million tonnes. It currently has capacities in fibres, yarns, filament yarns, and B2B chips. With the new regulation mandating PET bottles to contain 30 per cent recycled PET chips, it is now looking to enhance focus on B2B chips. “We are close to finalising [chip manufacturing] sites in Uttar Pradesh and Assam, with more sites being considered for the future,” informed Sultania. Recognising the vast potential of filament yarn, Ganesha Ecosphere is significantly expanding its operations in this area. “Big brands are focusing on recycled yarn for manufacturing fabrics. Presently, we have a 1,500 tonne capacity in filament yarn.”
However, with PET scrap in short supply, the ready availability of raw materials has become a major issue. “Earlier, the scrap was only used in polyester fibre. But now it’s also used in making sheets, filament yarns, and PET chips.” Sultania said this warranted immediate action. “The government must allow the import of certain raw materials to overcome the shortage,” he said, adding, “Besides, a separate cell must be created to address the concerns of the recycling industry.” Meanwhile, the company has been talking to stakeholders about setting up scrap collection and washing centres to ensure uninterrupted raw material supplies.
Move up the value chain
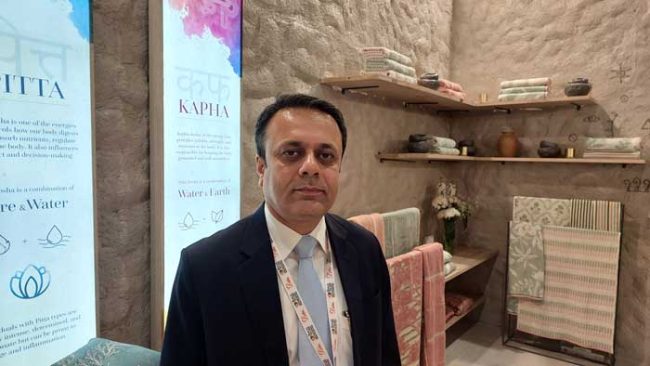
Samir Joshipura, Group CEO, Trident Group
Paper-to-apparel manufacturer Trident Group has continued its laser-sharp focus on its two-pronged strategy of servicing the domestic market and exports for sustained growth. “Our goal is a journey, not a destination, and where we keep moving up. We should be growing three times in India over the next three years,” declared Samir Joshipura, Group CEO, Trident Group. “India is moving up the lifestyle chain, driven by the trend towards urbanisation. As the opportunity cost of exports increases, we will become choosier about what we produce and export.”
Besides new launches for the domestic market, the company is creating high-value products for overseas markets. “Where exports are concerned, moving up the value chain is happening programme by programme, order by order. Again, it’s a journey.” The company has design development and product teams working on new ideas to cater to different market segments.
The company is looking at a capex of around ₹10 billion in FY2025-26, with a large share proposed to be spent on modernising production and expanding sustainable practices. Its technology unit, the manufacturing excellence team, plays an important role here. All manual work is being converted to system-driven processes through investments in automation and IoT. Simultaneously, the team is also tasked with making processes and products environmentally friendly. “It works on figuring out new solutions available in the market and how best they can be adopted in the overall process. For instance, how can we use less water and chemicals and make long-lasting products with minimal environmental impact.”
Joshipura admitted that the transformation wouldn’t succeed without a strong job training backbone. The company has trained hundreds of young people from different regions of the country through its Takshashila programme. It also runs a talent acquisition programme called Karmayogi.
Talking about government initiatives to support the textile industry, Joshipura welcomed the Mission on Cotton Productivity announced in the Union Budget 2025-26 and work being done under the National Technical Textile Mission. “The government has addressed most things through its focus on sustainability and smart technologies.” He said it was now time for the industry to make the most of the emerging opportunities.
Don’t ignore textile machine makers
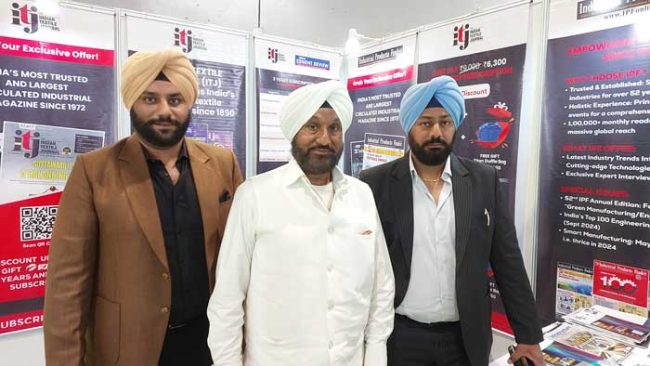
L-R: Harmeet Singh (Director – Sales & Marketing), Jagjeet Singh (CMD), and Inderpal Singh (Director – Technical), of Jogindra Industries Pvt Ltd
With growing automation and increasing demand from the domestic market, textile manufacturers are opening up to high-capacity machines. For instance, sales of a multi-pot dyeing machine launched by Jogindra Industries a few years ago have gained significantly. “Compared to conventional machines, this has variable dyeing machines on the same tabletop. We can offer up to ten machines on a platform in this product category,” said Harmeet Singh, Director of Sales & Marketing, Jogindra Industries.
The New Delhi-headquartered family-run firm manufactures yarn dyeing, conditioning, laundry, and dyeing machines for the domestic market and export. With repeat orders from the countries of the Far East, including China, and the Commonwealth of Independent States (CIS), the company has ramped up production year-over-year. It also sets aside 10 per cent of its revenue for R&D activity.
Although the company did not participate in the second edition of Bharat Tex, the management team was present in full force at the main venue for a series of meetings with existing and potential clients. When asked the reason for opting out of the exhibition, Singh said they weren’t keen on taking the stall allotted to them at the co-located Garment Technology Expo (GTE) held in Greater Noida, 39 km away. “When we visited there, we found most participants to be machine traders from China.” He felt the organisers must support the interests of domestic machine manufacturers in future events. “They must promote Indian machinery manufacturers because we are making capital goods for export.”
Additionally, with garment manufacturers located at the main venue, Indian textile machinery manufacturers should have been given space there as well. “Bharat Tex is one of the biggest textile shows in the world. However, by not having Indian textile manufacturers at the main event, they have made us feel alienated this time.”
Imbibe sustainability
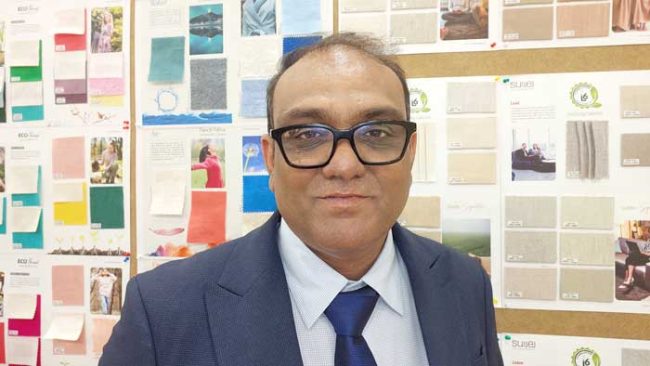
Dhiraj Banka, Sr VP, Sutlej Textiles and Industries
With stability slowly returning to the textile sector, Indian manufacturers must focus more on sustainability for future growth, according to Dhiraj Banka, Senior VP of Exports at the yarn and textile manufacturer Sutlej Textiles and Industries, a KK Birla Group subsidiary. “The demand for fashions made using recycled cotton has been growing,” he noted. “With sustainability emerging as a key demand driver, one must start working on areas like identifying the raw material sources.”
While a few categories of yarns such as raw white and mélange may continue to struggle, he sees new positives emerging for the business. For instance, the current demand is for peached fabrics. “Some segments that were earlier seen as premium are now facing challenges,” he said. However, he quickly pointed out that fashion changes rapidly. “After six months, mélange may suddenly become fashionable. Besides, yarn is the basic raw material for garments, and without the right yarn, there can be no sustainable clothing either.” Therefore, the industry would evolve to the next growth phase.
On being asked about the impact of instability in Bangladesh, Banka mentioned that the crisis has not significantly impacted business. “The only major challenge we are facing from Bangladesh is delayed payments. As a result, the interest burden on yarn manufacturers is marginally high at this point.” However, he is optimistic about things evening out over time. The South Asian country is a major importer of yarn from India for its textile industry.
Banka also saw the domestic market contributing to demand growth due to a large consumer base and rising disposable incomes. “The industry players will be focusing more on India, while also keeping a close watch on the situation in other parts of the world,” he said. He also emphasised the need to improve the country’s logistics infrastructure and markedly ramp up the production of technical textiles to compete with China.