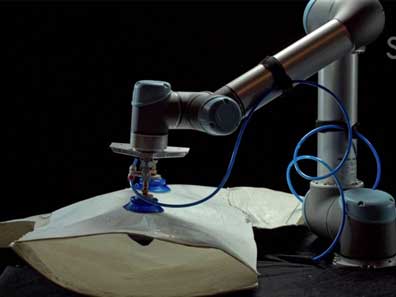
Application of robotics in textile industry: A review of recent advances
Prof N Gokarneshan suggests, the sooner we can introduce robotics and automation in any textile and apparel industry, we can seek thousands of benefits.
In the world market, survival in the competition of apparel industry depends on the advanced technology, automation and robotics, which are used from the designing to production process and product transportation of the industry. There is no doubt that automation can increase the production efficiency, reduce the number of faults and reduce the overall cost of production. The global demand for quality clothing, low production costs and competitive advantage can be achieved through automation adoption. In many developing countries, budget constraints prevent garment manufacturers from adopting advanced technology. But in order for the apparel industry to survive in the market, it needs to be able to produce more flawless products in less time and at a lower cost.
Application of robotics and automation in the textile industry had begun over two centuries ago when John Kay’s invented the flying shuttle. The flying shuttle machine was not only enabled an increase in production but also brought down the number of people required to operate the weaving loom, from two to one. The geographical distribution in the textile industry has seen a dramatic shift in the past 50 years. Textile manufacturers have moved a proportion of their textile production facilities from manual to automation. In the recent years, the application of robotics has increased, coupled with the rapidly rising wages in Asia, has seen some manufacturers made interested in the robotics production-based business model. Its clear that textile manufacturers are shifting priorities to automation to increase productivity and boost efficiency.
To achieve this, textile industry needs to adopt robotics automation, manipulation systems need to some artificial intelligence (AI). Automation and robotics are two closely similar technologies. Basically, robotics is a form of industrial automation. This article will describe a wide range of automation in textile process by using robots which is ultimately increasing the both basic requirement of textile industry both: productivity and efficiency.
Areas of robotics and automation in textile industry
There are several areas of automation in the production of textile materials including the yarn and fabric manufacturing process. In this article I will try to focus on the application of robotic and automation in the textile fabric manufacturing process and garments production. These include Robotics in handling of bales in blow room, Robotics in carding, Robotics in the splicing in auto-coners, Robotics in cleaning of textile industry, Robotics in fabric handling, Fabric Inspection, CAD & CAM, Fabric Spreading & Cutting, Sewing, Pressing, Material Handling & Radio Frequency Identification (RFID) in automation.
Robotics in handling of bales in blow room: Samples of the bales are sent to a grading laboratory for observation. After it has been received, verify the quality of the shipment immediately. Then passing, each bale is moved by the conveyor to a loading station. Where it will be picked by a robot and brought to storage. All the bales in blow room will be stored randomly in racks and position of bale with relevance bale number, weight and fibre characteristics. When bale is being selected for processing, it will be removed from the warehouse by a robot on a “first in, first out” basis.
Robotics in carding: Robot could be programmed to pick up cams from each card place them on to a truck and transport them to a production area for drawing frame for conventional operation. This can provide excellent cross blending and it will be an easy matter for an operator to clear the cans from the touch into a drawing frame.
Robotics in the splicing in Auto-Coners and other winders: Each time there will be an end break or bobbin change. This joins the yarn ends with a splice that’s virtually similar to the yarn. The strength and elongation values of the spliced joint are nearly always comparable, which is quite 90 per cent, with those of the yarn itself. Latest automatic splicer arm is act sort of a robot. It offers even Robotics in Cleaning of Textile Industry: Recently, application of robotics in cleaning of textile industry has been started with a mobile robot. A robot named MRP Nomad 200 can clean and polish of floor surfaces in textile industry.
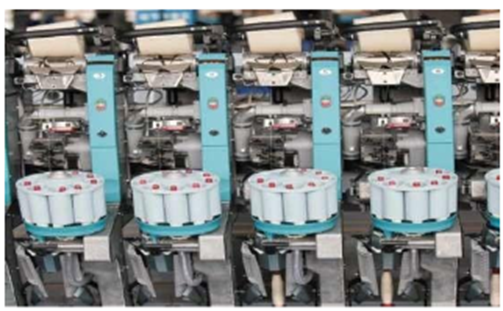
Robotic autoconer
Robotics in fabric handling: Fabric handling tasks require various tools and sensors in textile industry. To accommodate these tasks, ATI Industrial Automation Gamma 30/1 00 FIT sensor is mounted at the robot arm. A tool changer is also mounted on the FT sensor. The custom-built tool rack provides space for a standard pneumatic gripper and other special end effectors for fabric manipulation in the textile industry.
Robotics simulator in fabric handling: The robot simulator allows to running the robot control programs in simulation mode, without accessing hardware. This is very effective for debugging robot programs without the risk of damaging the robot during fabric handling. The operator can easily navigate by using the mouse, selecting and defining custom viewpoints.
Robotics in airbag manufacturing: In automotive industry, realistic manipulation processes involve interaction of fabric parts with other objects such as work surfaces, robot manipulators, and other fabrics. That’s why; the ability to model contact had been implemented.
Robotics in laser cutting: Laser cutting is really helpful to fabric cutting. Among the various types cutting technologies computer-controlled lasers cutting system are suitable for multi-ply cutting of heavy textile materials. It has been most widely adopted to increase the mass production in textile industry.
Robotics in folding and packing: The products folding and packing can carry out by the robots. They can take the garment, fold it and then pack it properly. It can be automatic or semi-automatic system.
Robotics in nonwovens:
The production of nonwoven and 3D structures for protective apparels by using
Robotics is under development by the researchers. Particularly, the combination of robotics and a small- scale melt blowing unit is additionally possible.
Garment automation in fabric inspection: Previously fabric inspections were performed in a manual process, so many times defects couldn’t be accurately identified. The use of automated equipment helps to enhance the efficiency of the fabric inspection process. Fabric inspection has proven to be one of the most difficult of all textile processes to automate. Various technique like Statistical approach, Spectral Approach and Model- based Approach can be adopted for automatic fabric inspection. In all of these methods, the fabric image is manipulated by a software or modelling tool to extract information about the severity of the fabric defect. The identified defects are automatically identified on the fabric, if the amounts of defects in a fabric lot exceed a certain limit, they are rejected.
Auto CAD and CAM: In the past, the design of fabric was done manually. So that a lot of time would be spent and the design would be recorded on paper. But now garment manufacturers use Computer Aided Design (CAD) and Computer Aided Manufacturing (CAM) to make garments. CAD is used to create 3D designs of clothing using computers, then CAD sends that information to CAM. CAM controls and manages the production process according to that information.
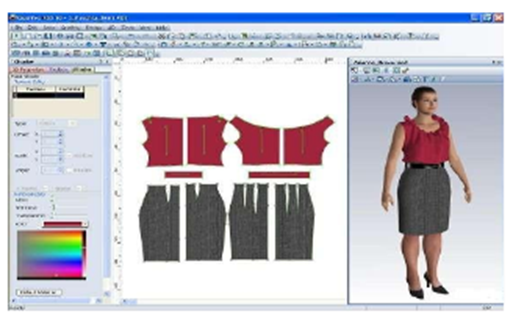
Application of CAD/CAM
Automation in fabric spreading: Many years ago, fabric spreading was done manually; workers spread the fabric by hand. It also required more than one worker to complete the work. Then came the semi- automatic machine, where one could operate the machine and get the job done. At present fabric spreading can be done with the help of fully automatic machines. In automatic fabric spreading, the work is done quickly by keeping the length- width as per the instructions given by the operator. Automatically spliced and starts new fabric spreading where the last fabric roll has finished. Effective & high-quality sensor is used to identify the defects and the defective fabric is cut by itself. Counting the ply number and the machine shuts down automatically when the specified ply number is exhausted. Any type of fabric can be spread by this machine. Less time required and less labour cost. However, it is very expensive and skilled operator is needed to operate this machine.
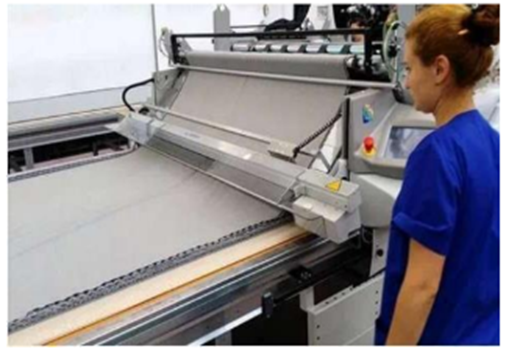
Automated fabric spreading
Automation in fabric cutting: This process was also done manually earlier but now automatic fabric cutting machine is being used. As a result, it is possible to cut the fabric more accurately and smoothly than before. According to the design of the garment now the design of that pattern is saved directly in the computer memory without making marker paper and according to that instruction the cutting machine automatically cuts multiple layers of fabric together, in a short time and accurately. This cutting process is also done somewhere using laser. The use of automatic cutting machines has reduced both the number of workers and the time compared to manually or operator operated machines.
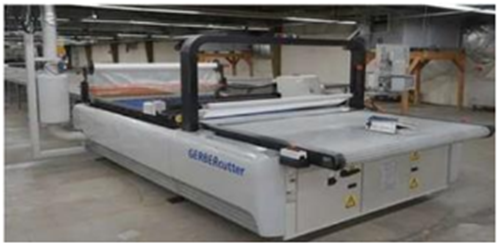
Automated fabric cutting
Automation in sewing : In countries like Vietnam, Vietnam, Cambodia and Laos most of the garment manufacturing process especially the sewing process is still done by skilled workers.
Manufacturers have not made significant progress in purchasing automatic sewing machines or Sewing Robot, this has helped keep their investment low. But manufacturers who have not invested in modern equipment are facing extreme competition to keep labour costs low. Recently for the automation of the sewing process, industrial robots are being built that can handle fabric during sewing activities, where no labour will be required. The process of forming seam in these automatic machines is similar to that of traditional sewing machines. Different types of sewing stitches such as overlock stitch, double chain stitch, double lock stitch etc. can be formed by robotic sewing machine.
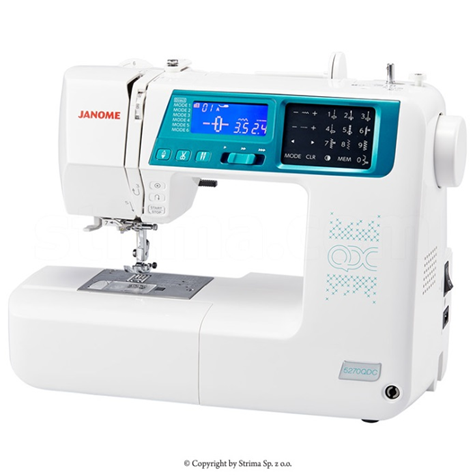
Computerised sewing
Sewing robot (Sewbo): The Sewbo is an industrial robot used in apparel industry for fabric gripping and handling. There have been some experimental trials to sew the whole garment using robots. One such example is Zornow‟s robot “Sewbo” which can automatically handle fabric elements during sewing. The robot “Sewbo” invented by Zornow in 2015 can sew a T-shirt from start to finish. This success was a milestone in achieving 100 per cent automation to create a complete outfit.
The robot can be programmed for a specific size and style. If the size or style of clothing changes, the robot needs to be re-programmed LOWRY SewBot: LOWRY SewBot is invented by Atlanta based company of USA “Softwear Automation”, it’s a special type of robot that is designed for the apparel industry. These SewBots are built using the advanced industrial 4.0 revolution technology such as computer vision or advanced robotics, which can analyse and manipulate the fabric like human. SewBots can perform multiple garments manufacturing tasks such as, Fabric Cutting, sewing, Awaking, labelling, Inspection etc. all of these works is controlled with just one touch panel. Dimensions in sewing as it can create high quality garments. Philipp Moll GmbH & Co. invented a 3D Sewing Technology, which could automatically create 3D Seam. Also, a 3D sewing robotic arm developed in China, the robotic arm can quickly scan the fabric pieces with a laser scanner and sew them together supported programmed patterns and cut the threads, the whole process takes just a few minutes to complete. The 3D robotic arms are currently applied to the stitching of automotive interiors. 3D sewing technology can make clothing (trousers, jackets, shirts) and car seat covers, airbag fabrics. This 3D technology can help achieve better quality of high-efficiency sewing products. 3D sewing technology also helps reduce labour costs and increase productivity.
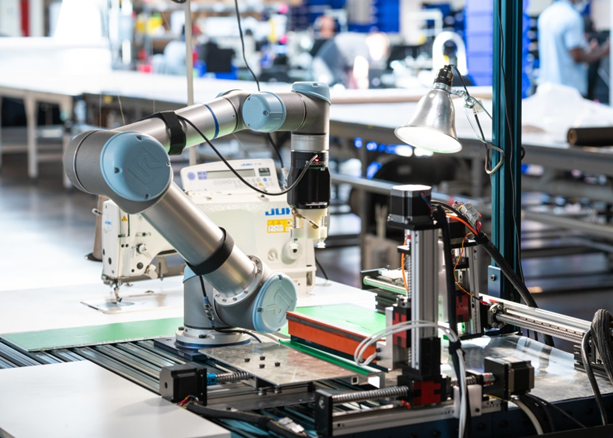
Sewbo
Automation in pressing: Pressing is one of the important steps to enhance the aesthetics of the product before going to the customers. Pressing operation is done to remove any crease in the garment so that it looks attractive when the customer buys it. Finding and retaining skilled workers for pressing operations is always a challenging affair. Operators migrate to other sectors for higher salaries when they gain sufficient skills. As a result, there is a shortage of skilled workers in this sector. These problems can be solved by adopting automation strategies in the pressing sector. Several advanced technologies such as pressing robots, jacket finishers, shirt finishers and shirt pressers are being commercially available now.
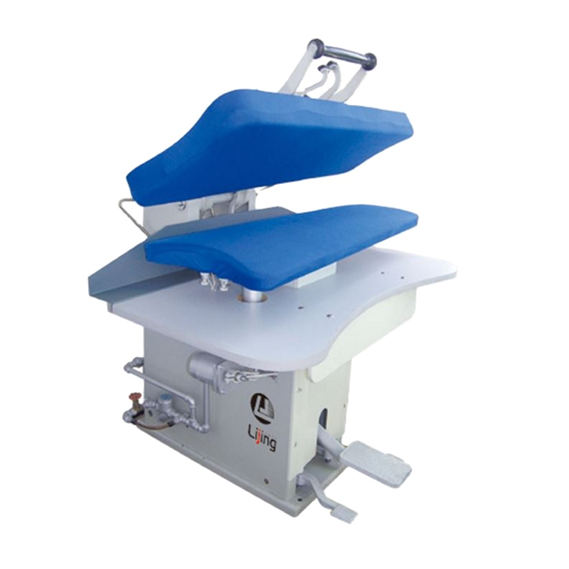
Full automatic ironing machine
Conclusion
Today, robotics and automation are widely being used in textile industry. Substantial robotics developments are already being made in textile sector. But mass production is not operated in textile manufacturing industries. Studies on robotics and automation for textile manufacturing applications tend to be less. As a result, applications of robots in textile industry have not varied much from conventional handling, assembly, welding, cutting, and so on the process. Therefore, our textile industrialist has to invest and take some necessary step to more and more research in the application of robotics in the textile industry.
As discussed above, we now realise that robotics and automation in the textile and apparel industry is indispensable for increasing productivity and prosperity. The sooner we can introduce robotics and automation in any textile and apparel industry, we can seek thousands of benefits. So, there is no comparison to robotics and automation in the textile and apparel industry to survive in this current competitive market
References
1. Application of Robotics in Textiles By: Prof. Tanveer Malik & Prof. Shivendra Parmar, Faculty, Dept. of Textile Technology, Shri Vaishnav Institute of Science and Technology
2. M. Acar, 1995: “Intelligent textile machines and systems”, M.Acar, ed. Mechatronics Design in Textile Engineering‟,Kluver Acad. Press, pp. 61- 66.
3. N. A. Hunter, R. E. King, H. L. W. Nuttle, J. R Wilson, 1993: “North Carolina apparel pipeline modelling project”, Intl. J. of Clothing Science and Technology, 5, pp. 19- 24.
4. D.H. Kincade, 1995: “Quick response management system for the apparel industry:
definition through technologies”, Clothing and Textiles Research J., 13 (4), pp. 245-251, UK.
5. U. Meyer, 1994:” Automation and control in textile production”, Globalisation: Technological Economic and Environmental Imperatives – 75th World conference of Tex
6. A. Seyam, F. Sun, 1994: “Manufacturing technology for apparel automation: lay-up
module, part II”, Intl. J. of Clothing Science and Technology, 6 (1), pp. 5-3, MCB University Press.
7. R.C. Michelini, G.M. Acaccia, M. Callegari, R.M.Molfino, R.P.Razzoli, 1997: “Shop controller-and- manager for intelligent manufacturing”, S. Tzafestas, Editor: Management and Control of Manufacturing Systems, Springer Verlag, London, pp. 219- 254.
8. C. Antonelli, 2008: “The economics of innovation critical concepts in economics”, Rutledge, New York.
9. G.L. Kovàcs, P. Bertòk, G. Heidegger, Eds., 2002 “Digital enterprise challenge lifecycle approach to management and production”, Kluwer Acad. Pub., Boston.
10. J.X. Liu., Ed., 2005: “New developments in robotics research”, Nova Sci. Pub., New York.
About the author: Dr N Gokarneshan is a Professor and Head Department of Textile Chemistry, SSM College of Engineering, Komarapalayam, Namakkal District, Tamil Nadu.