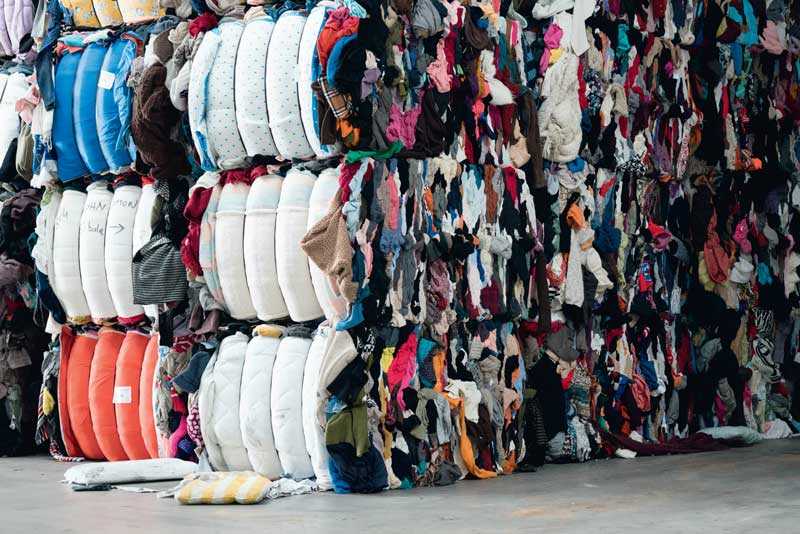
Textile recycling: Immediate challenges for the industry
There are many brands and retailers who claim that their merchandise are made of or contains recycled fibres. In this article, Dr Prabir Jana explains in detail the recycling solutions and decodes the core challenges of textile recycling.
Sustainability, circularity, carbon footprint, water footprint, micro-plastic, ocean-plastic, reduce, reuse, recycle and many more jargons has engulfed our mind in recent times. Every brand, every designer, every retailer are swearing that their merchandise are either made of or contains (certain % of) recycled fibre or ocean-plastic. In this article, we are going to decode the core challenges of textile recycling and how much we know about what we should know.Without getting into statistics, which is galore in internet (though mostly European or US centric and missing the global picture), this article will discuss about the process and technology challenges of textile recycling.
Recycling is defined in Oxford Dictionary as “to put used objects and materials through a process so that they can be used again”. The Wikipedia puts a little twist to the definition as “the process of converting waste materials into new materials and objects” and also include “the recovery of energy from waste materials”. One of the key considerations of recycling is “its ability to reacquire the properties it had in its original state”.
There are two types of textile wastes that can be recycled; industrial (waste generated in spinning, weaving, wet processing and garmenting) and post-consumer (waste generated at various levels after usage of the finished product by the end consumer). Some estimate shows post-industrial waste is around 67% (spinning accounts for 12-16.5%, weaving around 6.52%, processing 19% and garmenting around 25%). Post-consumer textile waste (PCTW) could be any textile article which has been discarded for any reason like being worn out, damaged or outgrown. Recycling of PCTW involves collection of waste, segregation of waste (fibre content wise and/or colour wise), removal of foreign articles (button, zipper, soil, dirt, etc.) and conversion of waste to either pulp/pellets or fibre. Recycling of industrial waste is comparatively simpler, as removal of foreign articles and segregation of waste are not required. The actual conversion process can be mechanical or chemical.
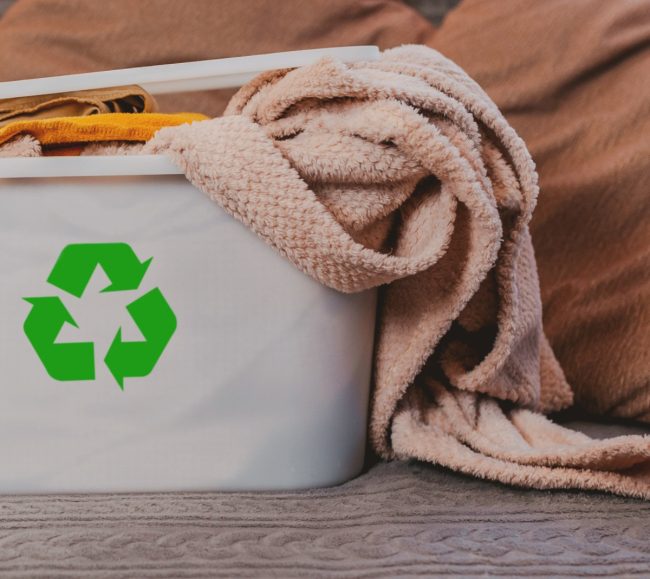
Mechanical recycling: Technology & process challenges
The main processes in a mechanical recycling plant are as follows:
- Cutting and preparation: Textile wastes usually have very different shapes and sizes. In order to work and transport them, those are cut in an adequate and homogeneous size. Some materials like cotton or polyester need an addition of a mixture of water with special oils and antistatic chemical products in order to get a better efficiency of the fibres and the machinery.
- Transport, storage and feeding: Cut textile wastes are then transported by the action of pneumatic fans up to storage silos where materials can rest until tearing machine feeder request to be filled. This is because cutting machines production rate is much higher than tearing line and also because the humidity of the emulsion of water plus antistatic and oils must penetrate inside the textile wastes.
- Tearing: This is the most important step of the installation. The rags, clips, etc. are converted to fibre again by the successive action of big pinned cylinders working against feeding units composed by feeding dish and feeding cylinders. An internal recycling system helps us to eliminate the possibility that small pieces can go out of the machine with the fibre.
- Packing: Opened fibres are packed in bale form with the help of high pressure bale presses in order to make easy their transport.
- Filtering: Technological air of the installation must be filtered before delivering to the atmosphere in order to avoid contaminating the air.
Mechanical recycling machines are generally designed to open all kinds of textile waste irrespective of colour and fibre content; due to mechanical tearing action the resultant fibre length becomes shorter than waste fibre feedstock. The recycled fibres come with mixed (melange) colour and mixed (unspecified) fibre blends and are suitable for blending with virgin fibre and open-end spinning system. Every successive recycling will reduce the fibre length leading to use in to certain non-woven products, such as under lay and insulation and finally dust form.
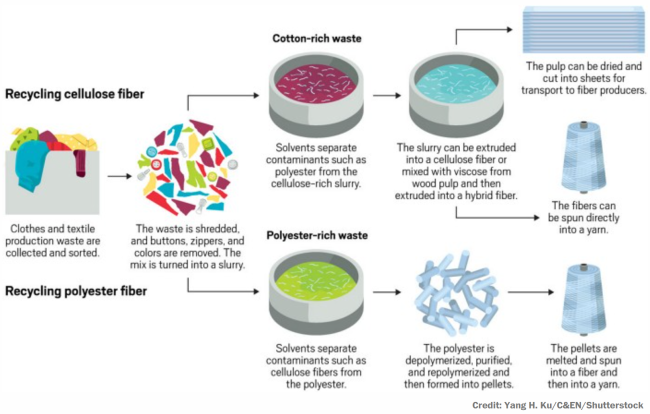
Chemical recycling infographic
Chemical recycling: Technology & process challenges
It is all about chemically breaking the fibres down into their chemical building blocks and then rebuild them into new fibres with indistinguishable (or better) performance characteristics than virgin fibres. Chemical fibre-to-fibre recycling is challenging both technically and economically. Technically because different fibres require different chemicals to break them down, and economically because the resulting fibre can’t be more expensive than the market will accept. Polyester consists 52% of the global textile industry, followed by cotton (24%) and regenerated cellulose (6%). Therefore, most of the researches and technology start-ups are targeting these two fibre types.
About 7.6% of polyester fibres produced today is actually derived from recycled beverage bottles and almost none from fibre-to-fibre recycling. Typically, they feature a solvent step to remove cellulosic and other waste before polyester is depolymerised into ethylene glycol and terephthalic acid. This is followed by a purification step before re-polymerization. Another novel polyester recycling technology uses a fermentation process in which waste cellulose fibres are converted into a sugar solution by an enzyme generated by a species of mould found on grapes. This enables the efficient separation of cellulosic fibres from polyester. Polyethylene (use to make single-use plastic bags) could also be recycled into fibres for clothes and other textiles. Polyethylene fibres take less energy to make than polyester fibres, and their chemistry makes them stain resistant and quick to dry.
Chemically recycling cotton follows the same basic steps: mechanical removal of items such as zips and buttons, washing to remove dyes and the like, dissolving the cotton cellulose in a solvent and then spinning new fibres from the resulting pulp. In a slightly different viscose-like cellulose recycling process an acid pre-treatment followed by an alkaline hydrolysis step separates most non-cellulosic materials. The remaining cellulose is then reacted with urea to form a cellulose carbamate powder. The powder is dissolved in dilute sodium hydroxide to form a so-called dope solution with a consistency of syrup that can be spun into a fibre ready for yarn making.
For recycling blends like poly-cotton, first the polyester fibres are swelled to leach out any small molecule contaminants like dyes and so on. Other polymers, polyurethane and cellulose acetate, are also washed out during this stage. All that is left behind is pure poly-cotton saturated with solvent. Now, this is heated up. At a higher temperature, the polyester dissolves and goes into solution, leaving the cotton behind as a solid, the cotton and polyester are then separated by filtration. Next, the solvent from the polymer is separated, restoring the polymer to the correct molecular weight distribution for reuse in the textiles market to be spun back into polyester fibre using existing infrastructure. The solid cotton fibres are then dissolved using a novel ionic liquid. The resultant viscous dope can be made into a pulp, which is equivalent to a wood pulp, and that can be used as a raw material for existing cellulosic fibre spinning processes.
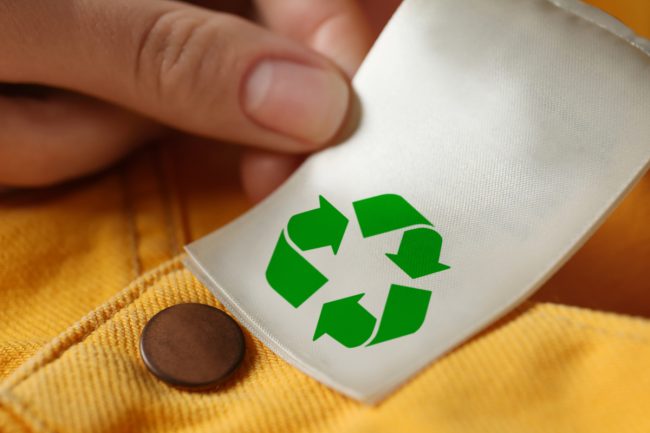
Supply side challenges
Unlike virgin textile, there are degrees of complexity and challenges related to the recycled textiles. The first challenge is issues with raw material supply, as the volume of textile waste cannot be guaranteed and retailers cannot ensure they will receive the same and/or similar items, this unpredictability of supply of post-consumer textile waste (PCTW) is a great barrier regarding supply chain of 100% recycled fibre. The second challenge is that the volume of clothing recovered for recycling is extremely low compared to the volume of clothing sold each year. This is in spite of the interest shown by consumers to recycle.
The third challenge is the purity of the waste; most technologies currently tolerate contamination up to a limit, difficult to get from the supply chain. Although the take-back schemes by different retailers, where consumers are incentivised to return their end of lifecycle garments in exchange for vouchers for future purchases, is becoming increasingly popular recovery option, is under scanner now. Some experts are arguing that these “take-back” schemes further increase the disposal mind-set of consumers (due to the incentives provided), encouraging consumption; defeating the whole purpose.
Recovery, segregation and redistribution
The recovered items are first manually sorted in terms of quality. Those considered of high quality are sold in second-hand stores or sold as second-hand products by the brand’s themselves. Most of what is leftover is sold in secondary markets, in nations across Africa, Asia, and Eastern Europe. Other low-quality textile waste are used in other industries, such as insulation for automotive or construction industries, industrial cleaning cloths, or converted to energy for heating or electricity in municipalities or going to landfill. This low quality textile waste is the primary target for recycling.
First, there are problems in the separation process of collected PCTW, as textiles are often mixed/soiled with non-textile waste (food, dirt, oil, body fluids, etc). Second, there is a current lack of technology in the separation of the blended fibres, such as PC (polyester-cotton) and PV (polyester-viscose), this brings about a challenge as some fibres cannot be recycled. Third, recovery and redistribution encompasses the efforts made by retailers to recover clothing from consumers, such as providing return boxes/areas within retail stores, street and container collection, delivery to superstores, and the take-back scheme. The fourth challenge is associated with Life Cycle Assessment (LCA) of the whole process. Any textile recycling techniques should pass the LCA to be sustainable. Specifically, the amount of manual labour currently requires to segregate, the amount of energy that is consumed during transport of waste to the recycling plant.
Conclusion
Most interesting fact is the number of intermediary organisations (think tanks, groups, associations) those are mainly creating hype and awareness about circularity and recycling today far outweighs the actual number of organisations engaged in converting the textile waste to fibre. One analysis of the research data reveals that Europe dominates the garment end of lifecycle literature with just under half of the research (49%) originating from the region. Europe is followed by North America, occupying 10%, Asia contributing to 7%, and South America with 2%.
At the core there are a handful number of organisations (mostly start-ups from European Universities) trying to solve the chemical recycling puzzle, but no single company yet has the complete process to recycle all fibres. And while most of the technology is patented and currently operated under complex licensing agreement, none of them are producing commercially viable amounts of recycled fibres yet. In comparison mechanical recycling is commercially simpler, with 10-15 machinery manufacturers offer complete solutions that anyone can install and operate.
About the author:
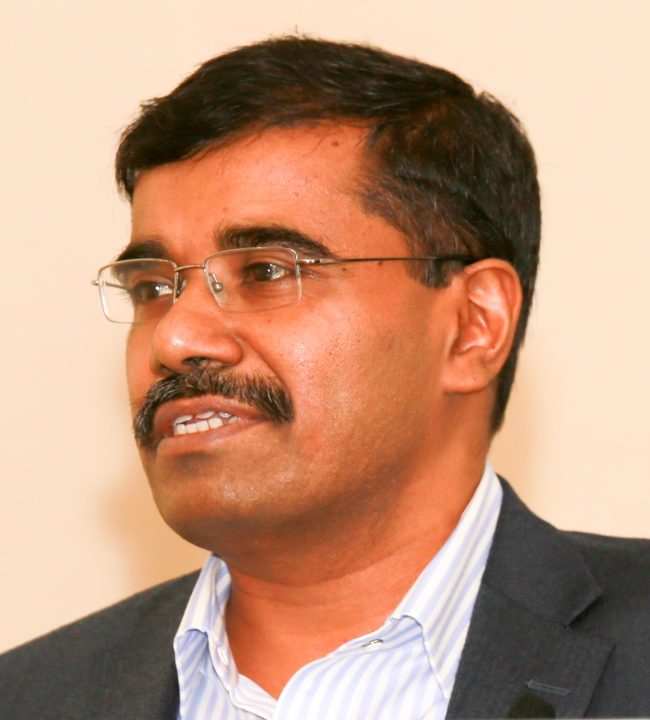