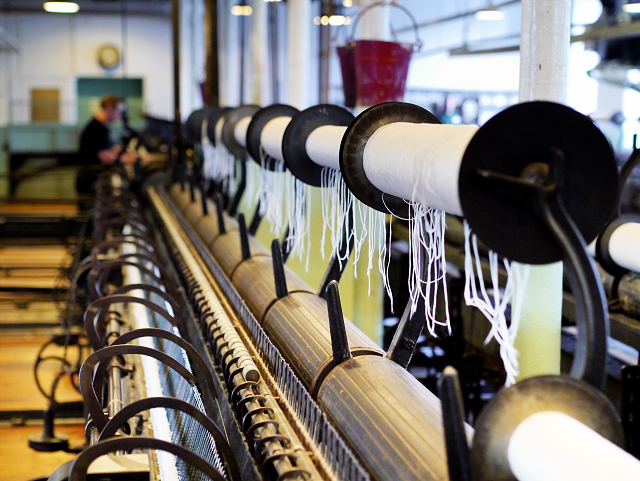
Mechanical engineering: Not just machine suppliers but technology partners
With sustainability and automation emerging as the key trends in the textile industry, German textile machinery manufacturers are gearing up towards a functioning circular economy and resource efficient textile production, writes Dr Janpeter Horn.
Sustainability and automation are two key trends in the textile manufacturing industry. Up to now, the increasing textile consumption around the world, due to growing population and purchasing power has been accompanied by a rising use of resources. The whole chain includes textile producers, brands, retailers and consumers. The textile machinery companies organised in the VDMA are geared towards a functioning circular economy and resource efficient textile production. With our highly efficient technologies we are an indispensable partner in this transition process. Real progress has already been made in energy efficiency. The same is true for raw materials like cotton or for water. The optimisation of machines, components and technologies provides a key to energy and resource-efficient manufacturing processes.
Energy efficiency – more topical than ever before
An expert team of member companies of the VDMA Textile Machinery Association has studied the energy-saving effects across the entire production chain of five textile products: a cotton T-shirt, a functional T-shirt, a textile billboard, an architectural fabric and a hygienic nonwoven. The result of this analysis: in the manufacture of these products, today’s technologies of the VDMA member companies can save up to 30% of energy compared to what was available 10 to 15 years ago. In view of the uncertainties in the international oil and gas markets, energy efficiency is more topical than ever before.
An increasing level of automation and remote services characterises the textile industry. Serving these markets, VDMA member companies see themselves not only as machine suppliers but also as competent partners on the technological aspects of digitalisation and the processes of their customers. An intensive relationship between spinners, weavers, knitters or finishers, machine suppliers, chemistry suppliers and other technology providers is the key to future success.
Remote services to avoid machine stops
Assistance via remote services/teleservice and predictive maintenance software to avoid machine stops are also now provided by numerous VDMA textile technology suppliers. Digitalisation and Industry 4.0 also help to counter the increasing shortage of skilled workers, and the machines of many VDMA companies offer many useful features to assure reproducible quality results. They include process simulation on a PC to optimise the process parameters before production even starts.
In general, there are two elements to saving resources and energy – modern plant technology and process optimisation. Modern machine concepts with intelligent control systems are significantly reducing the energy consumption, the consumption of water,
chemicals and as well the waste of expensive raw materials. The use of digitally advanced machines leads to a massive reduction in environmental footprint compared to older models.
Spinning: less production waste and lower energy consumption
In spinning, lack of efficiency, downtimes in mill production and fluctuations in quality are some of the major worries in modern mill management. To face these challenges, a digital all-in-one solution of a member company offers a transparent view of the entire spinning mill at one glance. The platform enables the users to discover optimization potential and to plan resources sensibly. Quality diagrams provide information on relevant progress parameters, such as thick spots, CV values, draft variations as well as energy consumption. The users can quickly identify negative deviations and outliers – thus, are able to prevent the production of non-usable material by intervening the process if required. This results in less production waste and a lower energy consumption.
AI to detect fabric faults
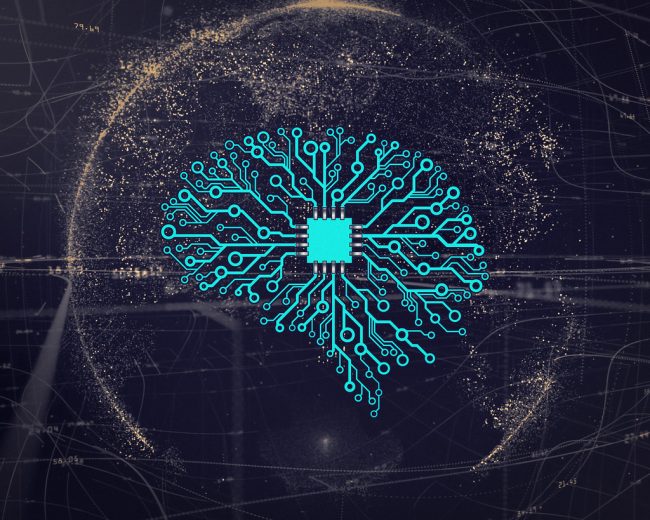
In fabric production, artificial intelligence (AI) is going to play a major role in future. A VDMA member company is working on a solution that aims to intelligently detect fabric faults by automatically monitoring quality during the production of knitted fabrics and stopping the machine in a matter of seconds. The monitoring system is more accurate through the use of AI and detects faults very fast. The extremely short response times save waste and require fewer resources. In the flat knitting sector, a software, in combination with external software for 3D prototyping, allows the design process to be digitised and the number of prototypes to be reduced. In a case study by the company, a halving was achieved under defined conditions. The ecological benefits of this are around 65% less material consumption and thus correspondingly less use of resources and energy.
Braiding – Savings in and quality of braided products are in the machines
Life cycle costs and life cycle sustainability are optimised by developments in machine technology. Braiding equipment guaranteeing consistent tension and defined strands by back twists enable to use less fibres to obtain a higher strength. Due to this with each product and the reduction the fibres actually needed the carbon footprint is reduced.
Control technology reduces water consumption in dyeing
Sophisticated recipe administration systems and process monitoring with special sensors for temperature, humidity etc. are addressing the needs in textile finishing.
For example, the development of dyeing machines in terms of design and control technology has led to an enormous reduction in water consumption over the past few decades.
Digital measurements and analysis of dyeing processes are crucial to process optimisation and several which optimise recipes and dye curves are available. Visual representations of the process curves, for example, enable both a control of the turbidity and a determination of the dye extract from the liquor.
The need for automation is growing from year to year and the benefits include both stable and increased productivity rates through the reduction of unproductive waiting times and an increase in occupational safety. Automated storage, weighing and dispensing systems also provide many advantages as workers no longer (or less frequently) come into contact with chemicals and dyes and there is less danger of accidents in the plant. Digital storage systems meanwhile manage stock levels and generate orders precisely when they are required.
Next stops Noida and Milan
Numerous member companies of VDMA will exhibit at India ITME in December in Noida. After almost three years without bigger trade shows in India, the companies are very much looking forward to deepen existing business relationships and build new ones.
Latest developments in automation and digitalisation can be expected at the next ITMA in June 2023 in Milan. We hope to welcome many visitors from India at the stands of the VDMA members.
About the author: Dr Janpeter Horn is the Chairman of VDMA Textile Machinery Association and Managing Director of August Herzog Maschinenfabrik, Germany.