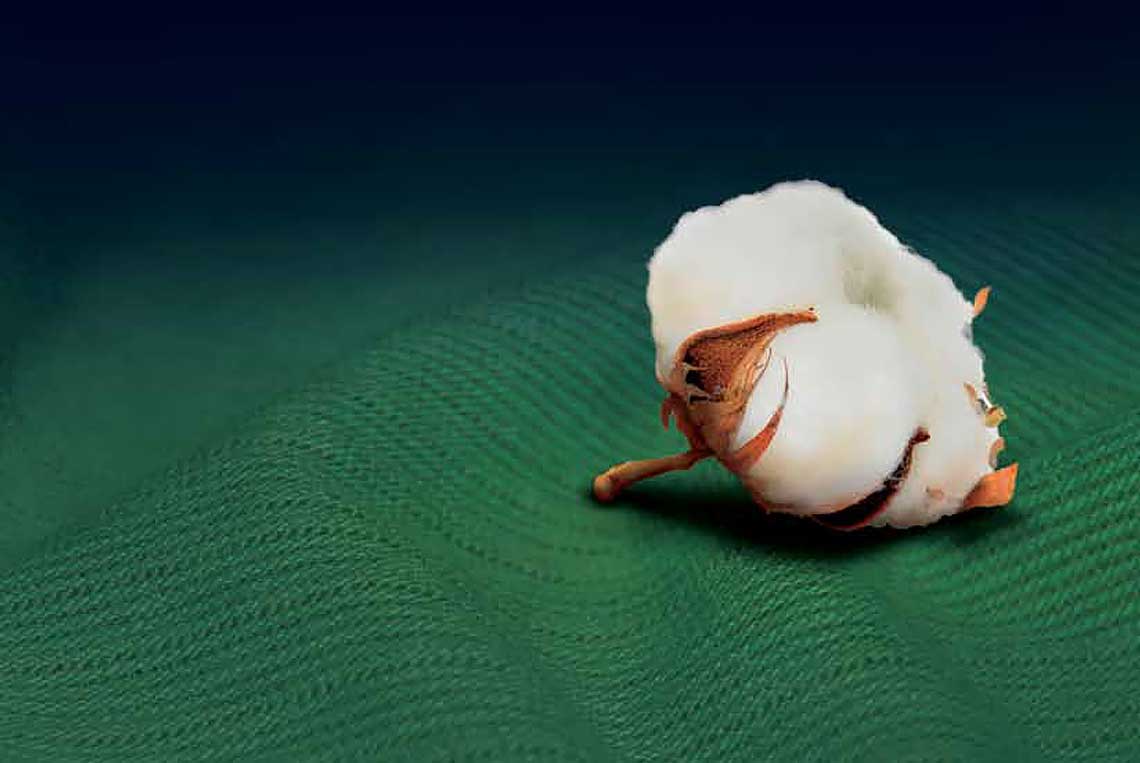
Significance of colour grade in cotton fibre mixing
Raw cotton contributes a major share of the textile production; thus, the spinners not only scrutinise the price but also their properties. In addition to other fibre properties, colour also assumes practical significance among the spinners while purchasing cotton. In this article, Dr Nagarajan Ganapathy deals with the colour assessment methods and selection of cotton for mixing.
Among the various natural cellulosic fibres available, cotton fibre still rules the textile sector due to its inherent properties and ease of blending with other regenerated and synthetic fibres. While mixing, spinners pay more attention on fibre micronaire, length, strength etc, colour of cotton assumes significant position during mixing to avoid shade variation complaints on fabrics. This article deals with the colour assessment methods and selection of cotton for mixing.
1.0: Introduction
Cotton is the basic raw material used across the world despite more competition from manmade fibres (MMF). In the present global trade, cotton plays an important role and hence the quality characteristics of cotton as well. Fibre characteristics of cotton affect both the intermediate and end products. Therefore, mills have preferences for specific fibre characteristics. Raw cotton contributes a major share of the textile production, thus the spinners not only scrutinize the price but also their properties. For the yarn manufacturers, the goal is to get a better premium for the above average fibre quality, or at a minimum, to avoid any discounts due to second quality.
Amongst the various cotton fibre properties, cotton colour is also assuming practical significance among the spinners while purchasing cotton. Traditionally cotton colour is generally assessed by visual (subjective) method by experience fibre length classers. However, this subjective assessment would often lead to human errors and misguide the cotton buyers to produce a “barre” free fabric.
2.0: Cotton colour
Cotton colour is one of the most important properties of cotton. It is affected by many factors such as rainfall, cultivation, freezes, insect attack, fungi, stains and storage conditions and temperature. Thus, colour deficiency in cotton is an indicator for lower process efficiency and lower product value. Colour deterioration also affects the efficiency of the fibres to absorb and hold the dyes and finishes. According to the USDA (United States Department of Agriculture), colour grade is defined as the colour of the cotton lint. There are standards of 25 colour grades of upland cotton and five categories of “below grade” colour. Fifteen of these grades are mentioned in a physical form in the form of boxes of cotton representing the full range of each standard, while the remaining 10 grades and five below grade categories are descriptions based on physical colour standards. The Universal Cotton standards are globally accepted and regularly used by the consumers for both US and non-US cotton.
In subjective assessment by an expert, the cotton colour is classified under a standard illumination with a set of physical standards. The visual assessment is generally done in a room with grey walls in which the samples are placed on a black background desk illuminated by a light of 1200 lux illumination.
Instrumental evaluation of Colour grade was established during the year 1930 by USDA on two parameters for cotton grade classification – Reflectance (Rd) and Yellowness (+b). The degree of reflectance (Rd) indicates how bright or dull the sample and the degree of yellowness (+b) indicates the colour pigmentation. In general, colour has three dimensions, hue, lightness and chroma. Many research investigations have found that hue of cotton is nearly constant and hence the lightness and chroma is sufficient to indicate the cotton colour grade measurement.
3.0: Principle of colour measurement
Cotton colour is determined using cotton colourimeter which uses a two filter colourimeter. This method was developed by Nickerson – Hunter in the early 1940s to check US cotton standards. The Hunter scales used in the Nickerson – hunter cotton colourimeter indicates the reflectance (Rd) and yellowness (+b) in vertical and horizontal directions. The percentage of reflectance (Rd) denotes the brightness and yellowness (+b) in the horizontal direction. The colour grade (CG) is indicated by locating the point of intersection of both Rd and +b of the sample on the Nickerson – Hunter colour diagram.
During the colour determination of cotton, photo diodes absorb filtered light from the illuminated sample and a microprocessor expresses the results in terms of the percentage reflectance (Rd) and yellowness (+b) corresponding to the value in Nickerson –Hunter colour diagram.
The same principle was incorporated in HVI which utilizes a flash light source to illuminate a sample window measuring 3.5sq. Inches colour sample area. The two light sources are arranged in such a way that they are inclined at an angle of 45 degree with respect to the viewing angle as prescribed in the ASTM method. In the colour measurement process, a small amount of predetermined pressure is applied on the sample. This is necessary to avoid any manual errors in the sample preparation. Light is reflected from the surface of the sample through two interference filters which are wide band interference filters – one located in the blue region of the spectrum and the other in the green region. The light is measured by two separate detectors and the signals from the detectors are used to calculate the brightness (Rd) and Yellowness from the yellow filter (+b) of the sample which denotes the cotton colour pigmentation. Calibration tiles are provided in the instrument to cross – check for any deviations during colour measurement.
3.1: Colour grade notation
Cotton colour notation consists of a double – digit number, the right digit indicates the five major categories (white, Light spotted, Spotted, tinged & yellow stained) and the left one indicates seven sub categories (Good Middling (1), Strict Middling (2), Middling (3), Strict Low Middling (4), Low middling (5). Strict Good Ordinary (6) and Good Ordinary (7) as shown in the Nickerson – Hunter colour diagram 1. In the current cotton classing system, colour grade of cotton is evaluated both instrumentally and visually. The HVI colourimeter measures both the reflectance (Rd) and Yellowness (+b) and provides a colour grade based on the colour diagram.
The colour grade (CG) of the cotton is determined by locating the quadrant of the colour chart diagram in which both Rd & +b intersect. For example, a cotton with Rd value of 72 and +b value of 9 will have a colour grade of 41 -3. The lower the number, the better is the cotton colour. For example, a 31-3 is superior to the base grade of 41-4. Elevated numbers (e.g., 42 or 52) indicate a dullness of colour and typically result from late-season weathering. Dullness in colour diminishes the dyeing properties of fibers and negatively affects spinning efficiencies. Colour grade of a cotton sample is represented by a three digit code xx –y.
Figure 1: Nickerson – Hunter Colour diagram
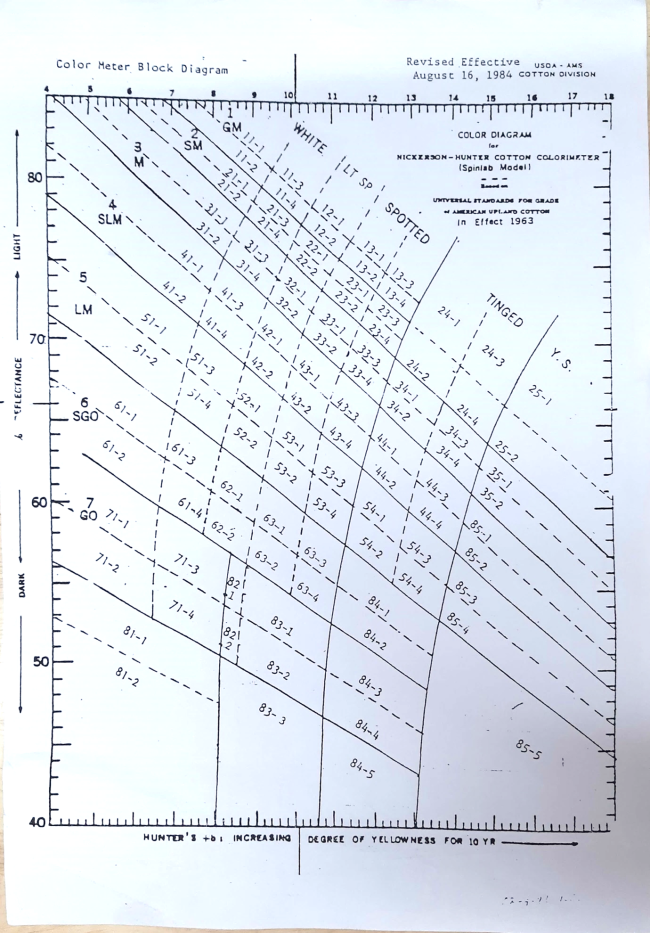
From the left, the first digit represents the brightness (Rd) of the sample. Lower the number, higher will be the brightness value of cotton. Second digit represents the yellowness. Lower the number, lower will be the yellowness. In the colour grade determination, there are 25 colour grades and five categories of colour grades. Indian cotton varieties mostly lie in white & light spotted categories with Middling to Good middling colour grade. In order to avoid barre effect on fabrics, it is advisable to select only four adjacent colour grades for mixing plan. i.e. 11, 12, 21 & 22 may be mixed. Mixing of cotton with colour grade of 11, 13, 21 & 31 should be avoided.
3.2: Significance of colour grade
Colour grade is the visual impression made on the raw cotton and it can be categorized into three components. The colour, the sample preparation and the foreign matter (trash) – each of them has a decisive influence on spinning performance and yarn quality. The colour of the cotton measured by the colourimeter directly affects the colour of the yarn. The variation in colour (brightness) in the daily or weekly blends may lead to product dichroism which is detrimental to the spinning mills. Hence by strictly colour range of individual cottons in a blend as well as in the daily blends, the shade variation problem can be avoided. A difference of +1.0 degree in brightness and +0.5 degree change in the yellowness in the daily blends may be tolerated while higher variation must be strictly avoided to avoid shade variation before the dyeing process. Variation in colour grade is one of the factors responsible for the occurrence of shade variation in fabrics. While many properties are important from different perspectives, critical factors are selected for maintaining homogeneity in mixing. Monitoring of colour grade is, therefore, important to avoid the shade defect on the yarn and in the fabrics as well.
In general, the reflectance (Rd) value of Indian cottons lies in between 72 to 82. In order to have a better control in mixing plan, it is advisable to maintain the range below 5 in daily mixing plan. Yellowness (+b) value differ both region wise and variety wise. In Indian cottons, the +b value usually lies in between 6.0 to 11.0. It is advisable to maintain the range below 2.5 or the maximum acceptable limit is 2.6 in one variety cotton mixing. The relationship between Reflectance (Rd) and Yellowness (+b) is given in Table 1.
Table 1: Classer’s designation for Rd and +b
Designation for Reflectance (Rd) | Designation for Yellowness (+b) | ||||
White | Light Spotted | Spotted | Yellow stained | Tinged | |
Good Middling | 11 | 12 | 13 | – | – |
Strict Middling | 21 | 22 | 23 | 24 | 25 |
Middling | 31 | 32 | 33 | 34 | 35 |
Strict Low Middling | 41 | 42 | 43 | 44 | – |
Low Middling | 51 | 52 | 53 | 54 | – |
Strict Good Ordinary | 61 | 62 | 63 | – | – |
Good Ordinary | 71 | – | – | – | – |
Below Grade | 81 | 82 | 83 | 84 | 85 |
For example, if the Reflectance (Rd) of cotton is 65 and Yellowness (+b) is 11.0, in the colour diagram, both the Rd & +b intersect in the quadrant 43 -4, is strict low middling and spotted.
3.3: Leaf or Trash Grade (Tr G)
Leaf or Trash grade denotes the presence of leaf, seed coats, grass etc. present in the cotton. The grade is generally a visual estimate of the amount of trash particles present in the given cotton sample. They are all represented by official standards of USDA. Further, there is a below grade category which is designated for American Upland cotton which means that the Leaf grade is below 7. The Classer;s Leaf grade and Trash measurement (% area) is given in Table 2.
Table 2: Leaf grade
Classer’s leaf grade | Trash area measurement in % |
1 | <= 0.13 |
2 | <=0.20 |
3 | <=0.34 |
4 | <= 0.51 |
5 | <= 0.72 |
6 | <= 1.00 |
7 | <=1.20 |
8 | >1.57 |
In the colour grade determination indicated by three digit XY – Z, the first two digit represents the Reflectance & Yellowness respectively. The third digit Z represents the leaf grade. For example, a cotton with a colour grade of 23 – 2 means Strict Middling, Spotted and leaf grade of 2 (<=0.20).
4.0: Conclusion
The development of advanced fibre testing instruments, at par with the modern advancements in the spinning machineries, provides a better estimation of the cotton fibre properties. With the HVI, mills have been utilizing the bale management program by giving appropriate weightage to Micronaire, Length & Strength. Although length & strength influences more on spinning process efficiency, micronaire in the mixing reflects more on the dyeability of the cotton material. Spinners give more importance in the micronaire range during the lot change to avoid shade variation in the fabrics. However, in addition to the micronaire, reflectance and yellowness also assume greater importance while mixing cotton with different growth areas. With the instrumental evaluation and careful selection of cotton for mixing, the problems of dye complaints from the consumers could be significantly reduced.
About the author:
Dr Nagarajan Ganapathy is associated with Texcoms Textile Solutions, Singapore. He has over 30 years of experience in textiles, working in the industry, academia and research. He has published more than 15 research papers in national and international journals and 3 textile books. Dr Nagarajan has presented his research studies in various technological conferences held in India during his time in SITRA.