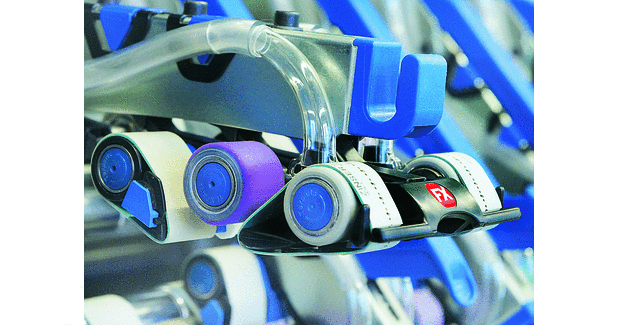
Impact FX: Optimisations for increased quality
The new Impact FX unit has an optimised compact front top roller with new roller cots and a diameter that has been modified to 27 mm.
The new Impact FX unit has an optimised compact front top roller with new roller cots and a diameter that has been modified to 27 mm.
From September 2018, all Zinser compact spinning machines will be supplied with a new Impact FX Generation. The pioneering features include: the enlarged front top rollers and compact front top rollers with new cots, the original Zinser compact apron, the built-in leaf spring and the flow-optimised suction tubes. The new generation of Impact FX reduces manufacturing costs, improves process safety and produces excellent yarn quality.
Front top roller with 30 mm dia
The diameter of the front top roller was increased to 30 mm. Thanks to the larger diameter, the roller can be ground down more frequently, which in turn increases usability. The defined offset to the front of +1 mm achieves more precise fibre clamping. Even floating fibres can thus be more effectively led into the main draft field – for optimal yarn quality.
The front top roller is fitted with the new AccoSmart sandwich cots. By combination of two tailor-made, high quality elastomer layers, AccoSmart cots feature higher deformation and provide larger contact surfaces compared to conventional one-layer soft cots. A higher degree of abrasion resistance and a lower susceptibility to tears are thus achieved.
Optimised compact front top roller
The new Impact FX unit has an optimised compact front top roller with new roller cots and a diameter that has been modified to 27 mm. The new cots and the greater roller diameter improve the technical spinning qualities, thereby significantly contributing to the quality of the yarn.
Overall, the compact element can now be adjusted even more easily and in a more user-friendly way.
Original Zinser compact aprons
The centrepiece of Impact FX is the self-cleaning compact apron. The newly developed Original Zinser compact apron has an optimised inner layer and offers improved running qualities and a longer lifetime. It can now be economically replaced during standard machine maintenance.
The new leaf spring enables secure positioning of the Impact FX unit. The optimisation leads to constant compacting and guarantees a constantly compact yarn quality from spinning position to spinning position.
Flow-optimised suction tube
Last but not least of the innovations is the flowoptimised suction tube with improved suction effect. It consists of a base body with enlarged internal diameter and a matching adaptor.
The new tube reliably avoids lap formation. It is easier to clean and replace, as there is no longer a need to differentiate between the left and the right tube. The opening of the tube is easily positioned accordingly.
Zinser compact yarns for the highest quality
The new performance features of the Impact FX unit, combined with its self-cleaning design, high level of process safety and unique variety of applications will give Saurer’s customers decisive competitive advantages in the textile markets of the future.
The Spinning Segment supports customers with solutions for staple fibre processing from bale to yarn. The portfolio includes machines, components, service, systems and automation for the processing of all staple fibres. Schlafhorst and Zinser are leading in staple fibre spinning and together with Jintan offer solutions from spinning preparation to winding. Components from Texparts ensure excellent yarn quality and maximum productivity. Saurer Group is a leading globally operating technology group focusing on machinery and components for yarn processing. As a company with a long tradition, Saurer has always been a leader in innovation. Today, Saurer comprises the two segments Saurer Spinning Solutions and Saurer Technologies. Saurer Spinning Solutions offers high quality, technologically advanced and customer-specific automation solutions for processing staple fibre from bale to yarn. Saurer Technologies specialises in twisting and embroidery as well as engineered and polymer solutions. With annual sales revenues of EUR 1.1 billion, 4 300 employees, and locations in Switzerland, Germany, Turkey, Brazil, Mexico, the USA, China, India and Singapore, the strongly growing group is well positioned to serve the world’s textile industry centres.