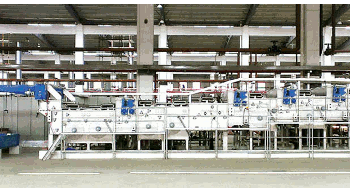
GOLLER Open-width Spun Oil Washing Range
GOLLER Open-width Spun Oil Washing Range can do continuous processing towards knitted fabric, solve the staining problem of silicone oil and keep excellent washing effect, writes Qiu Jianpeng of GOLLER Textile Machinery (Shenzhen) Co. Ltd. Warp knitted nylon/spandex fabric enjoys snug wearing, broad market demand and wide application. In order to enhance the twist of fibre, maintain the intensity of fibre and reduce break-up rate of fibre, generally, during the production of warp-knit nylon/ spandex fabric, it needs to add some specialised spinning agent.
GOLLER Open-width Spun Oil Washing Range can do continuous processing towards knitted fabric, solve the staining problem of silicone oil and keep excellent washing effect, writes Qiu Jianpeng of GOLLER Textile Machinery (Shenzhen) Co. Ltd.
Warp knitted nylon/spandex fabric enjoys snug wearing, broad market demand and wide application. In order to enhance the twist of fibre, maintain the intensity of fibre and reduce break-up rate of fibre, generally, during the production of warp-knit nylon/ spandex fabric, it needs to add some specialised spinning agent. However, the addition of the agent not only can lower the whiteness of fabric, but also can tarnish fabric and even lead to silicone oil spot. In the pretreatment process of spun oil washing, it is likely that the agent will be gathered and then stained on the fabric, which may result in ‘white spot’, this part of the fabric is not being dyed and it affects fabric dyeing and other processing. Therefore, during the pretreatment of warp knitted nylon/spandex fabric, the spun oil should be washed off evenly.
The removal of spun oil is the reaction of the agent emulsified and removed, in which we use the physical and chemical reactions to weaken the adhesive force between the agent and the fibre. After that, under the mechanical force of the washing range, the agent and the fibre will be separated and the agent will be dispersed in water, under the effect of the isolated agent, the blots are rinsed strongly and removed by the power sprays of perforated drum on the washing range.
Traditional spun oil processing is conducted on the overflow dyeing range, in which, the operation is simple but it wastes time and consumes a lot of water. Mostly likely, it causes silicone ‘oil spot’, which could be gathered and stained on the fabric, as a result, the fabric would not be dyed properly. GOLLER Open-width Washing Range can justly solve the mentioned problem of ‘spot’ and silicone oil. Its unique rotors enable the turbulent washing effect. Besides, it has an advanced automatically-controlled dosing system and circulatory and automatic filter to guarantee better washing range. Factory operation has been proved that GOLLER Open-width Washing Range can improve the production efficiency effectively, save water consumption and dyestuff, reduce production cost and ensure even spun oil effect. Last but not least, it makes the spun oil washing of pretreatment more environmental friendly and the performance of the pretreatment become more visualised and prompt.
GOLLER Open-Width Washing Range
- Automatically-controlled dosing system: Parameters and recipes controlled by PLC guarantees precise dosing.
- Automatic filter: The filter is connected with the washing compartment. After the liquor/lints/impurities in the washing compartment are filtrated by the filter and utilised repeatedly to remove the silicone oil ‘spot’, keeping the auto-cleaning of washing and consistent washing effect from beginning to the end.
- Reversely and optionally overflow way of water drainage: Optional overflow water drainage makes the gathered silicone oil ‘spot’ in washing compartment drain with the overflow after the washing compartment is supplemented with fresh water at fixed amount automatically, which maintains the cleaning effect of the washing process and consistent washing effect from the beginning to the end.
- SINTENSA high efficiency washing compartment: There is a rotor with many angles inside the perforated drum of every Sintensa unit. This rotor rotates at very high speed and makes the liquor penetrating the fabric repeatedly, which can separate the silicone oil and the blot from the fabric and the fibre. In addition, the water through the perforated drums sprays strongly on the fabric at high temperature, which can further boost the washing effect. At the same time, the washing compartments adopt overflow or optional overflow water drainage and supplement fresh water at fixed quantity. Besides, the silicone oil in the liquor is filtered and removed by the automatic cleaning filter, so as to retain the cleaning effect of washing process and maintain consistent washing effect from the beginning to the end.
- Vacuum suction device: The slot width of vacuum suction device can be adjusted to different widths according to the fabric width, and its suctional force can be continuously adjusted. With the help of vacuum suction device, the silicone oil and blot on both the fabric and the fibre can be removed effectively and the washing pressure will be reduced. Spun oil auxiliaries: Guangzhou auxiliaries company A; Hangzhou auxiliaries company B; Hangzhou auxiliaries company C.
Technology application process
- Technology application process: Fabric Preparation-GOLLER Open-width Spun Oil Washing-Monforts Stenter Range-Dyeing range-Monforts Stenter Range-Quality Control-Winder
- Technology application of GOLLER Open-width Spun Oil Washing Range: Dry Fabric Inlet-Centering Device-first Sintensa Plus Tandem 60°C countercurrent-second Sintensa Plus Tandem 80°C countercurrent-first Vacuum Suction Device-first Sintensa Plus Single 90°C countercurrent-second Sintensa Plus Single 70°C-third Sintensa Plus Single 60°C-third Sintensa Plus Tandem 35°C countercurrent-second Vacuum Suction Device-Fabric Outlet.
- Automatic dosing system: Precise Dosing by PLC automatically according to the recipe input beforehand. Spun oil washing mainly carries out in the first and second Sintensa washing compartment by adding spun oil agent and in the third, fourth, fifth and sixth Sintensa washing compartment without adding any auxiliary but rinsing with fresh water.
Remark Spun oil washing mainly carries out in the first and second Sintensa washing compartment by adding spun oil agent and in the third, fourth, fifth and sixth Sintensa washing compartment, without adding any auxiliary but rinsing with fresh water.
This experiment was conducted to test after the warp knitted nylon/spandex (74/26) with high spandex fabric that used spun oil on the surface. The spandex silicone oil could be gathered in lumps and were stick resistance or not by four groups of experiments of three auxiliaries companies. From the result of this experiment, we can conclude:
- From the two experiments of Guangzhou auxiliaries company A, we can find there was spandex silicone oil gathering in lumps, the speed of the gathering was low and few foam was found. In the pre heat setting of first group of experiment, ‘oil spot’ was found on the fabric and we need to make the second spun oil processing. After the second experiment, there was no oil spot found on the fabric after dyeing and the fabric was fine. In the pre heat setting of second group of experiment, no ‘oil spot’ was found on the fabric and the production output could be improved from the view of the speed of silicone oil gathering. After dyeing and heat setting, no ‘oil spot’ was found and the fabric was fine.
- From the experiment of Guangzhou auxiliaries company B, during production, spandex silicone oil gathered in lumps severely in filters of the first & second washing compartments and little foam was found. After pre heat setting, the ‘oil spot’ stained reversely and severely and the fabric had to be spun oil washing for the second time. After dyeing and pre heat setting, there was slight ‘oil spot’ on the fabric and the fabric was not up to standard.
- As for the experiment of Hangzhou auxiliaries company C, during production, spandex silicone oil gathered rapidly and severely in lumps in filters of the first & second washing compartments and more foam was found. In addition, the power sprays were broken up and we could only adjust them to smaller spraying. After pre heat setting, there was few ‘oil spot’ on fabric and the fabric was alright on whole. After dyeing, there was no oil spot on the fabric and the fabric was qualified the quality control. The substantive silicone oil in the washing compartment gathered and converted to be ‘oil spot’, which makes the fabric have great risk of staining reversely, resulting in limited production output and regular water exchange. Therefore, on the premise of no oil spot on the fabric after dyeing, in consideration of the production efficiency, the frequency of water exchange and the cost of auxiliaries, we can obtain a result that the spun oil agent of Guangzhou auxiliaries company A was superior to that of other companies tested.
From the above production parameters, we found out that the reason for spun oil agent staining reversely to the fabric was that after spun oil washing processing, the spun oil agent/silicone oil had not been dispersed into water but gathered and stained reversely on the fabric gradually. Thus, from the emulsification and dispersing effect of the oiling agent, we concluded that Guangzhou auxiliaries company A> Guangzhou auxiliaries company B> Hangzhou auxiliaries company C.
Conclusion
- Actual production proves that after the warp knitted nylon/ spandex fabric with high spandex are spun oil by unsatisfactory spun oil agent, the silicone oil will be gathered and stained reversely, which may cause “white spot†and make great influence. Excellent spun oil agent can make the removed silicone oil emulsified and dispersed into the water other than gathering in lumps and staining reversely on fabric and causing “white spotâ€. Hence, it is critical to choose superior spun oil agent to solve the problem of silicone oil staining reversely on the fabric, avoiding causing “white spot†and the fabric dyed poorly. Therefore, it is necessary to choose suitable spun oil agent to conduct spun oil washing processing for warp knitted nylon/ spandex fabric with high spandex to ensure the washing outcome of the fabric. From the above production parameter, we can find out that the reason for spun oil agent staining reversely to the fabric is that after spun oil washing processing, the spun oil agent/silicone oil had not been dispersed into water but gathered and stained reversely on the fabric gradually. Auxiliaries dosage is one important portion of the production cost. Choosing right auxiliary can help to decrease the dosage of auxiliary appropriately, reduce the loading of washing range and improve the comprehensive efficiency of the range. GOLLER Open-width Washing Range can meet the spun oil washing need of warp knitted nylon/spandex fabric with high spandex content. After spun oil washing, the dyeing effect is preeminent since there is no silicone oil “white spot†found on the dyed finished fabric. GOLLER Open-width Washing Range not only can make continuous processing towards knitted fabric, effectively solving the staining problem of silicone oil and keeping excellent washing effect, and it also guarantees high production efficiency. Meanwhile, GOLLER Open-width Spun Oil Washing Range can make full use of its high-efficiency spun oil washing units, such as effective vacuum suction device, perforated drum, power sprays and countercurrent water supply. We conclude that GOLLER Open-width Spun Oil Washing Range is a high-efficiency open-width spun oil washing range.