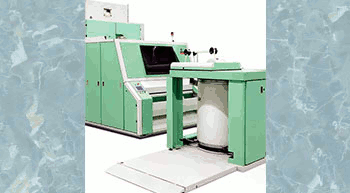
Marzoli C701 card: Key to quality & productivity
Marzoli C701 sports all the features of modern high-performance cards, and thanks to its innovative geometry represents a technological benchmark to fully satisfy the needs of a modern spinning mill. The card has always been at the heart of the spinning process. Only with an effective carding of the fibre the spinner can produce a homogeneous, regular, resistant and clean yarn and therefore ensure efficiency and quality in downstream operations.
Marzoli C701 sports all the features of modern high-performance cards, and thanks to its innovative geometry represents a technological benchmark to fully satisfy the needs of a modern spinning mill.
The card has always been at the heart of the spinning process. Only with an effective carding of the fibre the spinner can produce a homogeneous, regular, resistant and clean yarn and therefore ensure efficiency and quality in downstream operations. No machine in the spinning mill can overcome the defects that arise from non-effective carding, therefore it is necessary that the card can properly select, open, clean and parallelise the fibres without damaging or weakening them.
Carding technology has become even more important with the advent of high production requirements. The times when spinning mills had several cards running at 20-30 kg/h are over and modern competition requires to produce impressive quantities of yarn in order to minimise the average cost per kilogram. But for the card an increase in production can have serious effects on the quality of the output, therefore technological innovation has become fundamental to meet the increasingly demanding requirements of modern competition.
This article describes from a technical and technological standpoint the latest model of Marzoli?s card, the C701, thereby highlighting the advancements achieved by the Italian textile machinery leader in carding technology.
Machine description
With Marzoli C701, the raw material is supplied via pipe ducting and enters the card by falling into the feed inlet. The raw material accumulated in the pre-chute chamber is then clamped between a feed roller and a feed table and is delivered to an opening roller that delivers very fine tufts to the batt formation chamber. The batt is then delivered to a feed device comprising a feed roller and a feed table that delivers the clamped material to the licker-in. After having passed through a mote knife and two carding segments that remove the impurities, the material is delivered to the main cylinder and is processed by six carding bars and two mote knives in the pre-carding area. The main carding zone comprises 90 mobile flats, thirty two always in working position. The post-carding area comprises two mote knives and four carding bars for a further cleaning and parallelisation of the fibres.
The material is then delivered to the doffer, the web detaching device and the sliver formation area. The sliver is then coiled inside the 40? cans.
Although the carding principle is still the same as that of previous models and of competitor machines, Figures 3, 4 and 5 testify a quite substantial improvement in productivity and efficiency levels. When compared to the previous model, Marzoli C701 allows an increase in production under the same quality level of up to 50 per cent and a reduction of energy consumption of up to 30 per cent. These results have been achieved thanks to technical innovations in some critical parts of the machine, e.g. the feed chute and the carding area allowing for a better opening of the feedstock and a more effective carding of the material.
Integrated feed chute
The feed system of the card is of the utmost importance for the consequences it has on sliver regularity and on machine productivity. An even sliver can be obtained only if the feed batt presents a perfectly even distribution of the tufts and high production requires that the feedstock is perfectly open.
The feed system of Marzoli C701 is a two-piece chute with an integrated opening system: the material enters the pre-chute feed chamber (the reserve chute) and is then delivered through a feed roller that seals the upper half of the feed system to an opening roller, which plucks the clamped material and delivers very fine tufts to the batt formation chamber. The compressed air introduced directly in the batt formation chamber leaks through the perforated steel sheet.
The airflow ensures that the tufts are carried in the zone where the perforated steel sheet is currently least covered. This entails the perfect uniformity of the batt along its entire width. An electronic pressure sensor guarantees constant pressure of the feedstock. If the feedstock became too heavy, the tufts would compress and this would yield irregularities in the sliver. This pressure sensor controls the feed of material to the batt formation chamber by adjusting the speed of the feed roller.
The described technology, along with the auto-leveler that adjusts the speed of the feed roller according to the batt width, guarantees the delivery of a perfectly open and even feed batt to the licker-in.
Licker-in
One of the main objectives of a card is to open the fibre material and remove the impurities still present within the feedstock. In the card the working organ that mostly contribute to the achievement of these objectives is the licker-in, a cast iron roller with saw-tooth clothing that plucks the feed batt in very small tufts and cleans them thanks to carding segments and mote knives.
One of the peculiarities of Marzoli C701 card is the small diameter of the licker-in, which must thus rotate faster in order to keep the desired peripheral speed. This grants a greater centrifugal force that, in combination with the knife and the carding segments positioned underneath the licker-in, contributes to a very effective elimination of dust and trash.
It is argued that in order to achieve the desired degree of opening in the card several licker-ins are necessary. In reality in the card the opening of the raw material to individual fibres is carried out through a draft effect occurring between the feed roller and the main cylinder that is not affected by the number and the dimension of the licker-in. In fact draft is always and only the ratio between the delivery speed and the input speed: the intermediate rollers do not affect the final draft whatsoever.
The draft between the feed roller and the main cylinder of Marzoli C701 Card is very high (800) ensuring perfect opening of the fibre mass. This adds onto the high cleaning performance of the licker-in, which does not alter the draft effect in any way.
Carding zone
The problem of boosting productivity on the card stems from the fact that in order to increase production levels the card must process greater amounts of material and therefore open up more feedstock in the time unit. The opening effect is usually represented by the number of fibres per point, i.e., average of total fibres fed in per unit of time over the number of points available in the same time. Increase in production levels would require a proportional increase in the number of points available in the time unit and this can be only achieved in two ways: higher roller and cylinder speeds; more carding surface.
Increasing roller and cylinder speeds, however, would go to the detriment of quality: due to the already high speeds of these working organs, a further increase would provoke too much stress on the fibres and on the clothing of the carding flats. All the major textile machinery manufacturers have therefore opted for the second option and have revised the geometry of their cards.
In Marzoli C701 card, the main cylinder has been raised and the licker-in and the doffer have been located underneath. This entails a carding angle, i.e. angle between the centre of the licker-in and the center of the doffer, of 284°. The great carding angle, the diameter of the cylinder of 1 meter and the working width of 1.5 m entail a carding surface of 3.74 sq m, one of the greatest carding surfaces in the world, thereby reducing the number of fibres per point. The core of a card is the area of the revolving flats. It is in this zone where the tufts are opened into individual fibres, where the raw material is parallelised, impurities and neps are eliminated and short fibres are removed. It may appear logical that with a higher number of revolving flats, quality can be enhanced. However, this is true only partially: as elimination of waste can be done only by filling the clothing of the revolving flats, after a certain amount of processed fibres, the flat loses its functionality and needs to be cleaned. This entails that the quality of the card sliver keeps improving until a certain number of revolving flats in working position; over this number, quality does not improve because the flats closer to the licker-in are so filled with short fibres and impurities that cannot card anymore. Marzoli has identified this number in 32 carding flats and has consequently equipped its C701 model with 90 mobile flats, 32 of which always in contact with the cylinder.
Doffer
The fibres after having been carded must be transferred from the main cylinder to the doffer where they are condensed into a web. However, as the clothings of the two rollers are arranged relative to each other in the carding configuration, the transfer of the fibres is not easy and the material usually rotates several times on the cylinder before passing to the doffer. On one hand this is an advantage as it fosters fibres blend; on the other it negatively affects sliver evenness. It is therefore necessary to foster fibre transfer and to do this the cylinder and the doffer must be as close as possible to each other.
In Marzoli C701 card, the distance between the two rollers is the minimum mechanically achievable and the transfer of fibres is also fostered by their large contact zone enabled by the big diameter of the doffer.
Conclusion
Carding has always been and will continue to be one of the most important phases of the spinning process. The market demand for higher productivity with constant quality levels have made technological advancements on carding operations even more important. Marzoli C701 includes all the features of modern high-performance cards and thanks to its innovative geometry represents a technological benchmark to fully satisfy the drivers of modern competition.