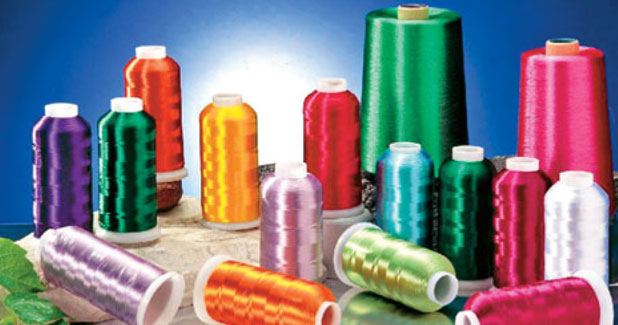
Weaving quality filament yarn fabrics
The weaving of filament yarns calls for a greater amount of skill and dexterity on the part of the operatives and supervisors. Many drastic changes in operating conditions and procedures and even modifications of equipment are sometimes necessary to weave these yarns. A high level of regularity along their length, the lustre and lie of filaments give the fabrics made from these yarns a sheer surface, which shows up the defects radially.
By using today´s state-of-the-art machinery and taking precautions in weaving preparatory steps, quality filament yarn fabrics can be woven, aver MY Gudiyawar and Rahul R Gadkari.
The weaving of filament yarns calls for a greater amount of skill and dexterity on the part of the operatives and supervisors. Many drastic changes in operating conditions and procedures and even modifications of equipment are sometimes necessary to weave these yarns. A high level of regularity along their length, the lustre and lie of filaments give the fabrics made from these yarns a sheer surface, which shows up the defects radially. Similar faults may not be noticed with spun yarns. Since filament yarns are generally low twisted, rough surfaces in its paths lead to sticking and breakage of filaments. Static build-up also presents difficulties in the weaving of filament yarn. Precision settings and high standard of skills are required for weaving of continuous filament yarn. Filament yarns are stronger than spun yarns.
The elongation at brake in filament yarns is also more than that in the spun yarns. Both these properties are favourable to weaving, yet it is not easy to weave filament yarn because the individual constituent filaments are much weaker compared to the spun yarns. Therefore it is very essential that these component filaments are not allowed to fray; avoiding filamentation, which is the key to successful weaving. Even small amount of twist in the filament yarns helps to reduce the fraying tendency. For similar reasons the tangled yarns are also easy to weave compared to the zero twist filament yarns. The very high twist filament yarns, as expected have lower strength but higher elongation. Their excessive snarling tendency becomes a problem and requires special care during weaving. The zero twist yarns require special sizing process as dealt with later in this discussion.
As to weave the filament yarns special care should be taken while warping, sizing and weaving. Even when yarn is ready to be woven then there are precautions to be taken while weaving so that fabric defects may not occur. The defects in filament yarn woven fabrics are quite different from the regular spun yarn fabrics.
The precautions have to take depending upon the type of filament being woven.
Warping
During warping, the following requirements should be met:
- The axis of package holder should be exactly in the line with the first guide element and the of yarn tensioner. The base of each holder should be covered with a ship-skin belt or foam rubber to prevent trapping of yarn behind the package.
- Guide distance should be adjusted for optimum balloon characteristics and minimum contact between the running yarn and the body of package. The distance will vary depending upon the warping speeds, maximum diametre of package, traverse length, etc.
- During creeling it must be ensured that the direction of withdrawal relative to the yarn wound on the package should be same for all packages.
- Warping tension should be maintained at 0.1-0.15 g/dtex. Spot checks (about 20 ends on each side) for every new batch by means of a hand tension-meter it will give good results.
- Thread tension unit e.g. Benninger GZB type, which comprises two pairs of discs first pair has a damping effect and the second one imparts tension to the ends as per requirement. Cantering pin is avoided to obviate of yarn path and accumulation of dirt. For high twisted yarns, pre-tensioners and double rod tensioners should be used along with disc tensioner. Parallel creel should be used. The thread of each section should have the same angle of entry.
- Half cones should not be used along with full cones and vice versa, because they will