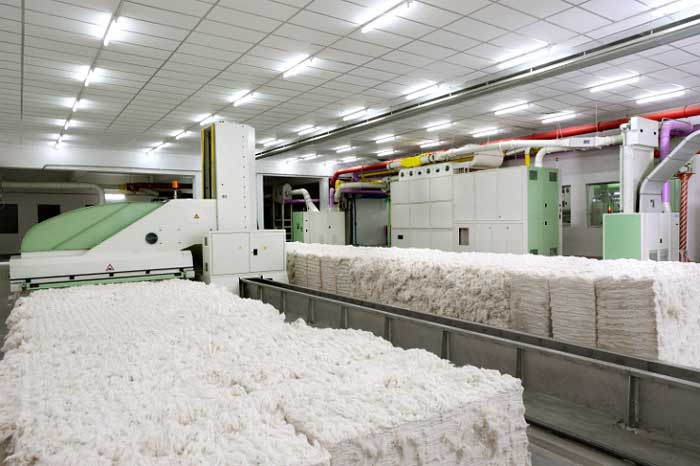
LMW’s state-of-the-art smart solutions for benchmark productivity and quality
LMW has become the preferred partner for customers who are gearing up to meet the dynamic needs of the ever – evolving spinning industry.
LMW stands among a select few global companies that undertake the complete cycle of designing, manufacturing, installing, and offering lifelong service for the entire range of machineries in the spinning line. Supported by an extensive sales and service network and a highly innovative and qualified R&D team, LMW has become the preferred partner for customers who are gearing up to meet the dynamic needs of the ever – evolving spinning industry.
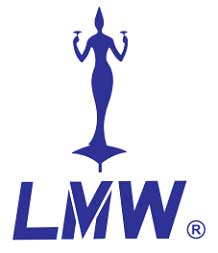
Gentle Blowroom Line
The Blowroom line is designed to enhance productivity, maintain consistent quality, and accommodate diverse fibre characteristics. The gentle Blowroom line ensures optimum opening, cleaning and homogeneous blending of raw materials. The highly flexible Blowroom line ensures highest level of cleaning efficiency and raw material realisation, with effective handling of fibres through different options of opening elements.
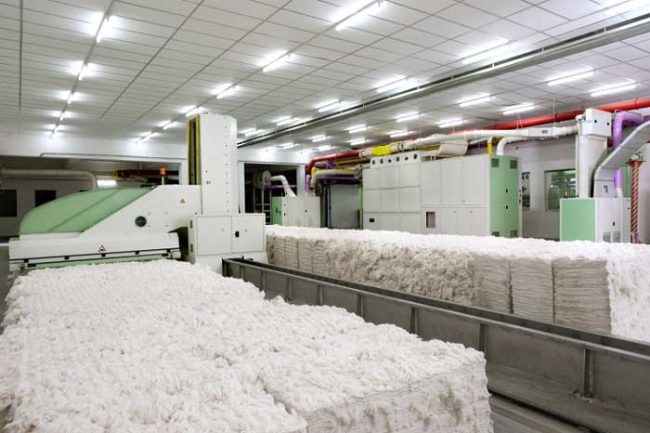
Gentle Blowroom Line Solutions for the Blowroom line from LMW include,
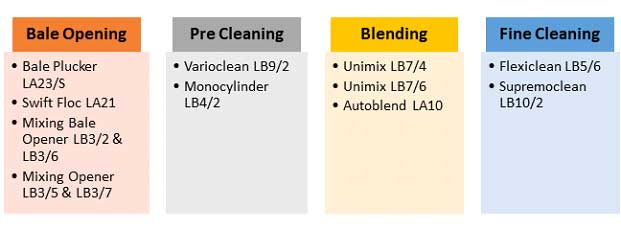
Auto Blend LA10
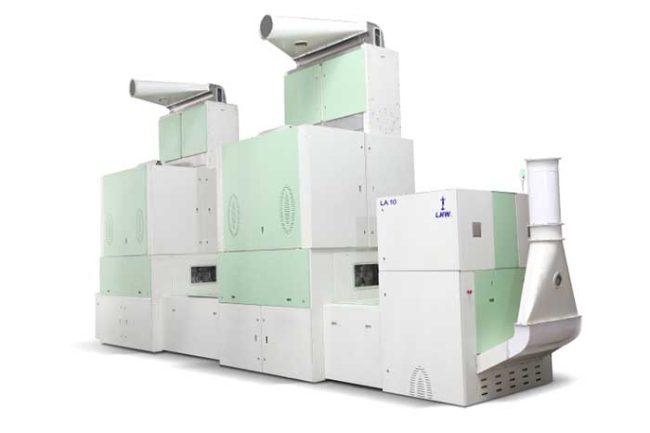
Auto Blend LA10
Auto Blend LA10 machinery from LMW is a versatile cutting edge solution which can blend a wide range of materials seamlessly. The solution can effectively blend at ratios up to 99:1, maintaining an impressive blending accuracy level of +/- 1 per cent.
The Auto Blend LA10 has been meticulously designed to accommodate up to 4 feeders, each capable of handling 500 kg/hr, and a Two-line output which facilitates achieving two different blend percentages. For precision, load cells are employed to directly measure material drops, ranging from a minimum of 100 gms to a maximum of 3000 gms.
LMW’s commitment to delivering quality material is aided by an online weight variation monitor. This feature continuously assesses weight and promptly halts the machine in the presence of any variations, ensuring consistency and excellence.
The principle of sandwich blending through conveyor is adopted where the weighed material is dropped on to the conveyor located below and the material is moved to the next feeder. Boasting a stripper roller and a pair of Feed Rollers with pin-type opening rollers, harmonizing to yield a thoroughly mixed final product. Precise blending of diverse materials is guaranteed with this innovative automation solution. It also drives reductions in labour and operational costs while ensuring unparalleled material quality at the same time.
Card LC636 SX
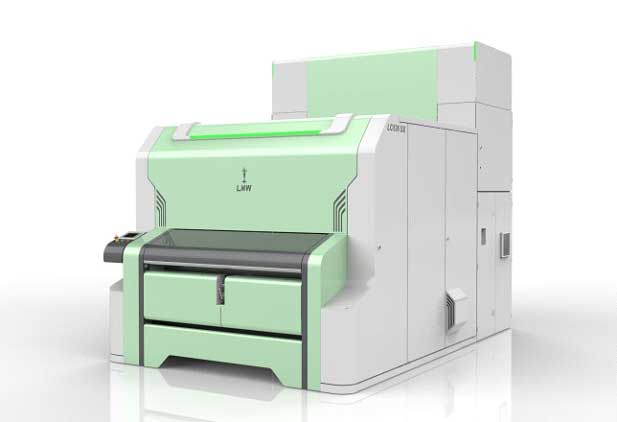
Card LC636 SX
The versatile Card LC636 SX from LMW is adept at processing various applications with equal ease. With the impressive active carding area of 1.95 sq. m. and a cylinder area of 3.95 sq. m., the LC636 SX rates high in delivering enduring value to customers.
Featuring a working width of 1.5 meters, the LC636 SX delivers an impressive increase in realization by up to 1% while saving up to 15% on power consumption thereby ensuring optimal utilization of valuable resources.
Non-Auto Leveller Draw Frame LDB3 S
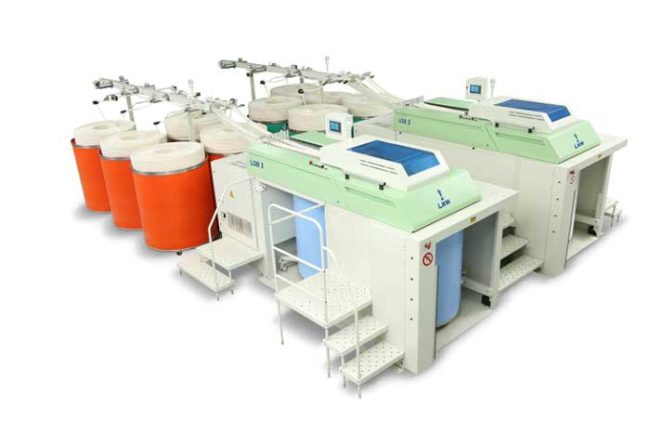
Non-Auto Leveller Draw Frame LDB3 S
The Breaker Draw Frame LDB3 S from LMW, operates at peak efficiency without compromising on sliver quality. Its unique drafting system, characterized by a shorter travelling length of sliver to coiler, enables higher delivery speed. The machine incorporates a top roller end bush with lifetime lubrication thereby minimising machine downtime. The programmable oscillating TR strip, coupled with an inverter-controlled fan motor, ensures a clean working environment.
Lap Former LH20 S
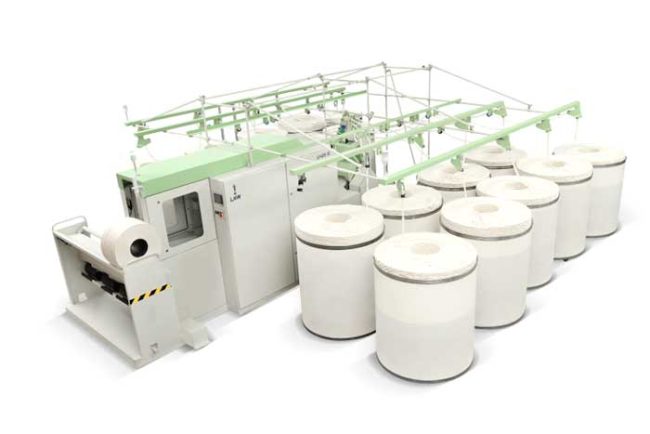
Lap Former LH20 S
LMW’s Lap Former LH20 S is equipped with a range of features designed to minimize doff time and boost productivity. The Lap Weight Monitoring System ensures consistent Lap CV%, and the unique single-head Servo Drafting improves lap appearance. The machine offers the quickest doff-time, contributing to increased overall productivity, and its compact footprint allows for efficient space utilization.
Comber LK69 S
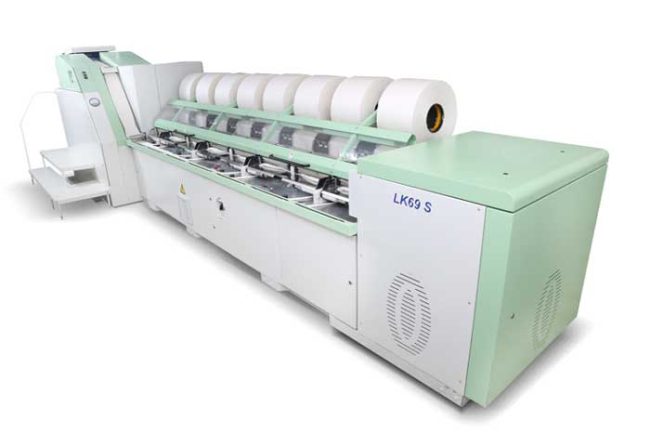
Comber LK69 S
LMW’s Comber LK69 S with Precisely Accelerated Combing Technology (PACT) sets the pace for combing technology with a production of up to 2.1 tons/day @ 600 npm. PACT technology enables LK69 S to run at higher speeds without straining the fibre and ensures efficient removal of short fibre and neps with minimal wastage. It is equipped with servo drive drafting for hank levelling and 100mm can dia for increased efficiency (100mm can is an optional feature). Flexible noil extraction between 8-25% can also be configured based on requirement.
Auto Leveller Draw Frame LDF3 2S
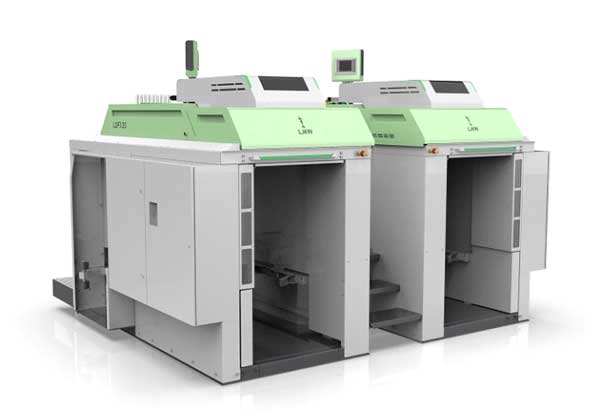
Twin Delivery Auto Leveller Draw Frame LDF3 2S
Twin Delivery Auto Leveller Draw Frame LDF3 2S is designed to enhance productivity and ensure consistent quality with the most compact footprint.
Equipped with independent drive arrangement, LDF3 2S is tailored to meet unique customer requirements, allowing for the simultaneous processing of two different materials with varying parameters effortlessly. This precise servo-driven operation with the mechanically synchronized drive system, enables impressive speeds of up to 1100 m/min and the Duo Digital Levelling Principle sets benchmark standards for sliver quality. The accurate measurement of input sliver and transmitting to drives upon the measurement of deviation results in consistently perfect sliver quality at the delivery end.
The TR Strip arrangement, featuring a programmable oscillating stripper for cleaning top rollers, guarantees the cleanliness of the top rollers and contributes to improved sliver quality. Pneumatically assisted SP – Smart Auto Piecing System eliminates the need for manual piecing of materials after breakage and saves considerable amount of time. Furthermore, the centralized roller setting arrangement with a single tool enhances user-friendliness and maintenance convenience.
Auto doffer Speed frame LF 4280/SX
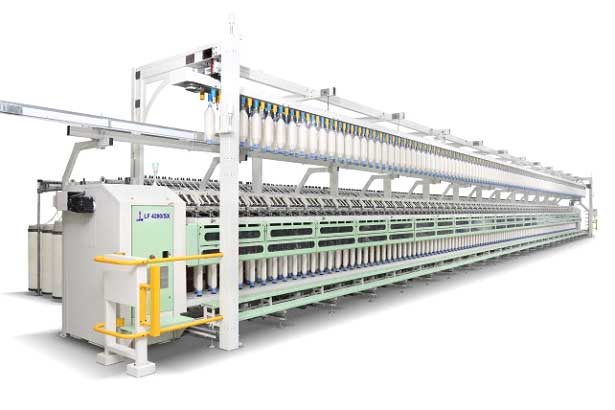
Speed frame LF 4280/SX
LMW’s Speed Frame LF 4280/SX model with Auto doffer and 280 spindles offers the highest value to the customer. Benchmark productivity is achieved through robust design and modular belt drive arrangement that supports higher delivery speeds up to 54 m/min. ATC (Automatic Tension Control), the dynamic tension sensing & control arrangement, Bottom cleaning device and Dual drive arrangement ensures consistent high-quality roving.
Energy efficiency is achieved through 4 segment drive arrangement, Unique CQ duct and 40 spindles modular drive for flyers and bobbins. Features like change of draft & twist from touch screen, wider platform and bobbin lifting safety enhance user friendliness. Additionally, the machine offers lesser footprint & lesser doff time. The optional Roving Transportation System (RTS), reduces personnel requirements, increases machine efficiency and ensures excellent roving quality.
Ring Frame LRJ 9/SX
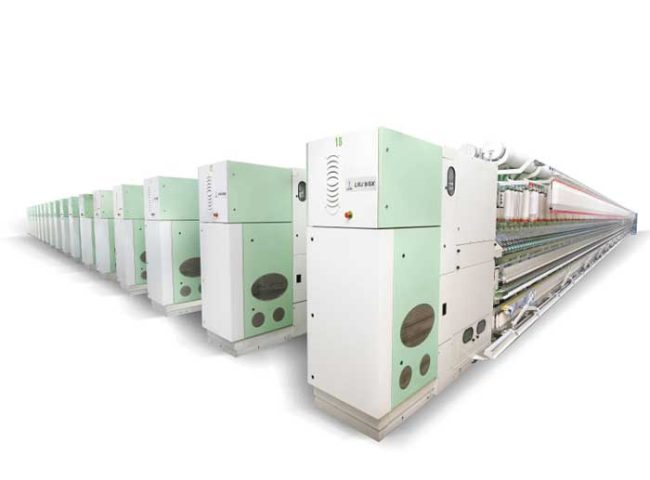
Ring frame LRJ 9/SX
LMW’s Ring Frame LRJ 9/SX is the smartest yarn spinning solution that guarantees unparalleled spinning success with consistent and superior quality. The inbuilt state-of-the-art Suction Compact System (Spinpact), facilitates unmatched yarn quality and energy savings. The machine’s versatility allows for the processing of special yarns like Siro, Slub, Multi-twist, Multi-count, Injection slub, and more. With its Flexi drive for drafting, the LRJ 9/SX ensures uniform yarn quality, and the High-Performance Module (HPM) facilitates ease of operation.
Spinpact
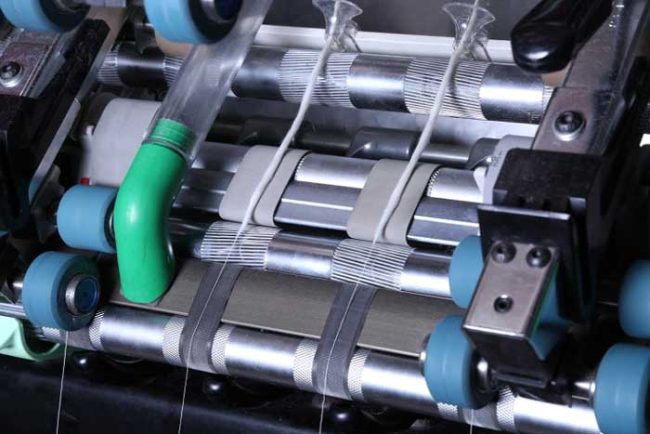
Spinpact
Spinpact, the proven suction compact system offered with LMW Ring Frame LRJ9 series and as retrofit to earlier model renders higher productivity and superior quality with utmost ease of handling. The Uni-Compact nozzle crafted from specially alloyed aluminium, the Direct Loading System (DLS), and a unique top suction arrangement facilitates the consistent and superior quality output. LMW Spinpact helps achieve up to 15% increase in yarn tenacity, an improvement of up to 30% in Uster Hairiness Index (H), and notable improvements in yarn imperfections and Classimat faults. The application of Spinpact also contributes to a better fabric appearance.
Automation focused on reducing dependence on skilled manpower
LMW is constantly working to reduce dependence on skilled manpower by introducing innovative solutions with the right balance of automation and ergonomics. The widely accepted offerings include
Card with drafting system (CDS)
LMW’s CDS boasts a 2 over 2 pneumatically loaded drafting system with servo control. The Intelligent auto levelling system ensures the consistent quality of the sliver. CDS is equipped with easy adjustment of load for drafting rollers and a maximum delivery speed of 700 MPM can be achieved. The unique design of CDS ensures quicker and effective auto piecing of the sliver which increases the machine efficiency. The simplified yarn preparation process makes it ideal for both Airjet and Open-end spinning applications.
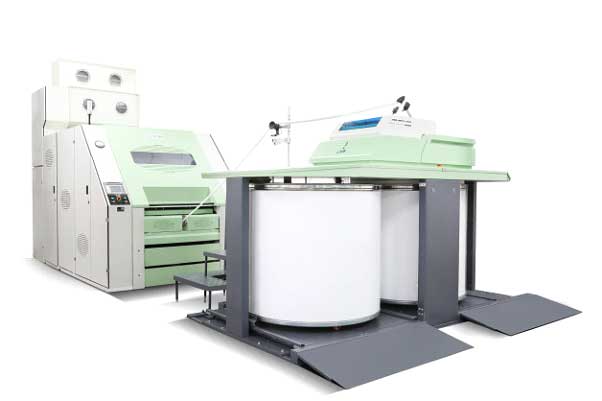
Card with drafting system (CDS)
Lap Transportation System (LTS)
Our Fully Automated Lap Transportation System (LTS) guarantees seamless transport of laps and spools between Lap Former and Comber, ensuring precise positioning and gentle handling for consistent combing quality. This system boosts Comber machine efficiency and also features a user-friendly HMI display for easy operation. The Lap Turntable option allows for layout flexibility. LTS eliminates manual errors, reduces operator fatigue, and leads to significant manpower savings. A single system can efficiently supply to 3 Lap Formers and 18 Combers, connected in a straight line with a maximum travelling length of 90 meters.
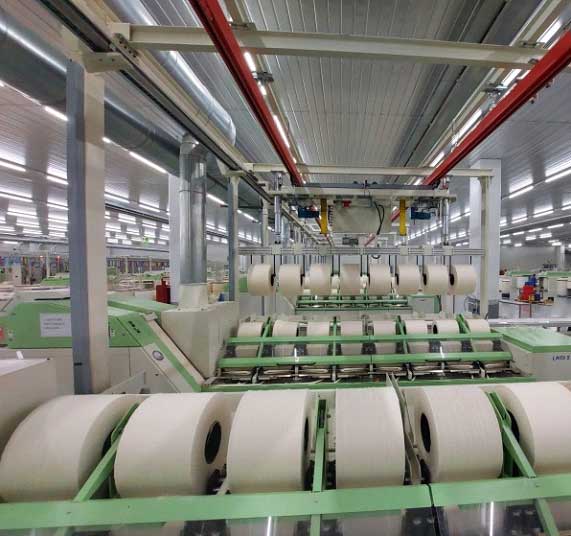
Lap Transportation System (LTS)
Roving Transportation System (RTS)
The Roving Transportation System (RTS) features a highly reliable, specially designed track made of extruded Aluminium and Anodized rail for smooth transportation of roving bobbins from Speed Frame to Ring Frame. The motorized drive system for train movement featuring a track motor with brake and Inverter drive for variable train speeds facilitates seamless transfer and positioning of bobbins in Bobbin Stripper / Exchanger. RTS incorporates an automatic roller clearer arrangement and a stripper arrangement for automatic cleaning of empty bobbins. With exchanger available for Automatic & Fully Automatic RTS, this system can be seamlessly installed in existing layout / machines with flexible design.
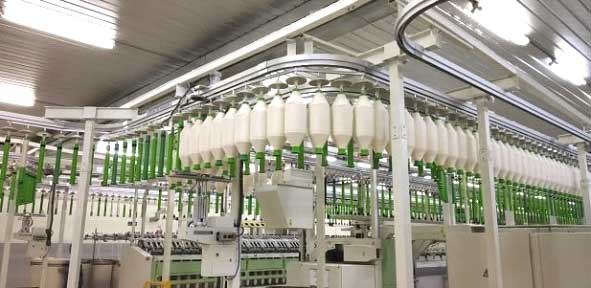
Roving Transportation System (RTS)
Yarn Breakage Sensor (YBS)
The Yarn Breakage Sensor (YBS) efficiently monitors each spindle on the Ring frame machine by tracking Traveller rotation and instantly detects individual spindle breaks, idle, slip, rouge, and abnormal slips at specific positions. Each spindle is clearly indicated with unique identifications, reducing patrolling time and allowing for the real-time monitoring of breakage rates, ultimately enhancing piecing efficiency.
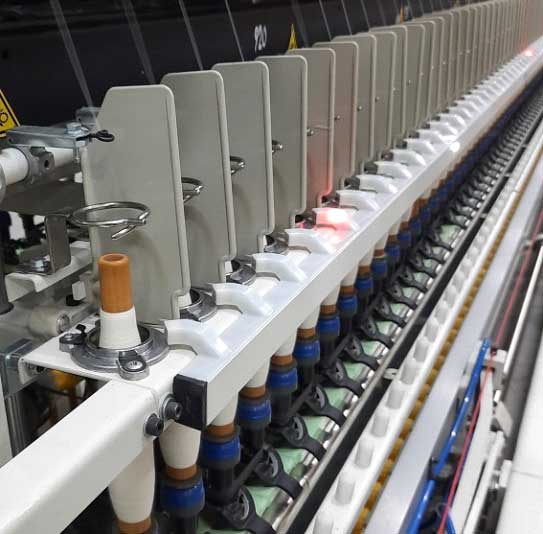
Yarn Breakage Sensor (YBS)
Roving Stop Motion (RSM)
The Roving Stop Motion (RSM) for Ring Frame machines efficiently halts the roving flow in the event of yarn breaks. It stops individual spindle roving, aiding in the reduction of pneumafil waste. Moreover, RSM prevents damage to cots and aprons while also aiding in the reduction of hard waste.
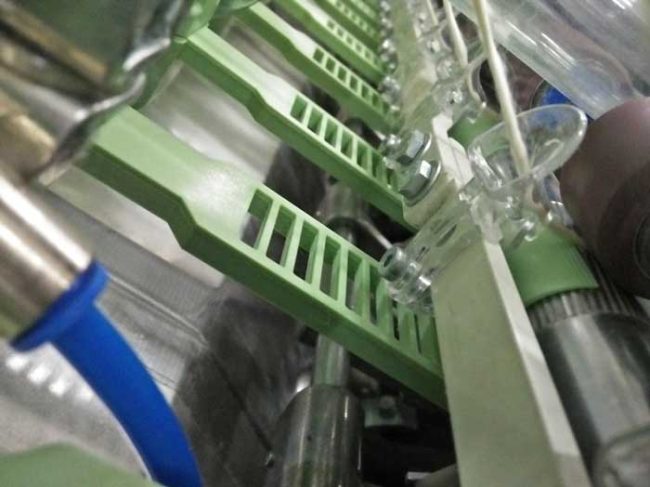
Roving Stop Motion (RSM)
Ring Frame Auto Piecing (RAP) – “As Human Piecing – AHP”
Ring Frame Auto Piecing (RAP), the fully automated yarn piecing system for Ring spinning machine, receives information on yarn break through YBS (Yarn Breakage Sensor) and travels to the particular spindle and automatically pieces the yarn instantly as a human does. By automating the piecing process, Rap reduces the dependency on skilled labour, streamlines operations and reduces the necessity for extensive training of the piecer. The immediate attention to the broken end ensures shorter auto piecing cycle time of around 35s. RAP also ensures consistent piecing length and also enhances overall quality by eliminating contamination on the cop outer surface resulting from manual handling. The unique design of RAP makes it compatible for both Normal Ring Spinning and Compact Spinning.
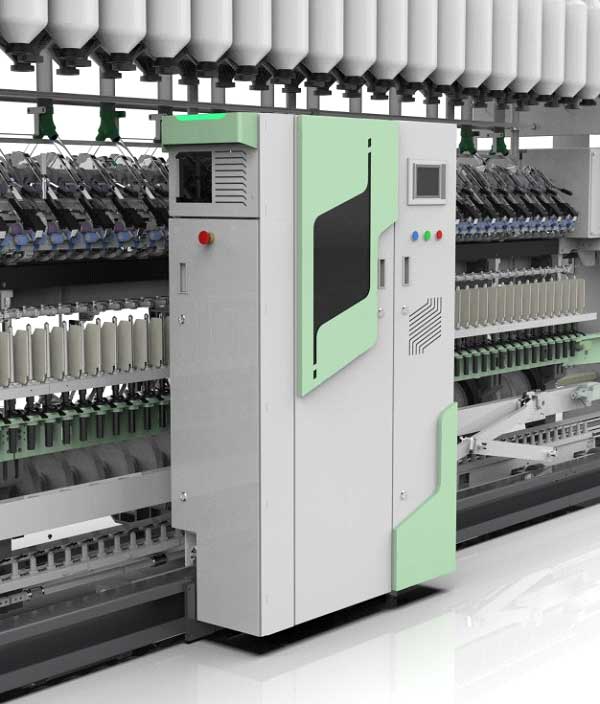
Ring Frame Auto Piecing (RAP)
Spinconnect
LMW Spinconnect, the web-based monitoring and control application interconnects the various machinery within the spinning mill. The system captures and displays critical parameters like Speeds, Production Stoppages, Quality, Power etc. By facilitating close monitoring of plant utilization and productivity levels, Spinconnect delivers comprehensive information on production, quality and maintenance to the management, technical team, and operators. This enables the optimization of processes and efficient resource utilization which leads to cost savings and increased profits.
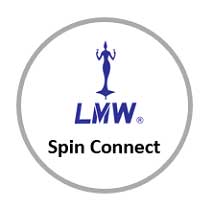
Conclusion
Since 1962, LMW has grown from strength to strength, and established itself as a pioneer in the global textile machinery manufacturing industry.
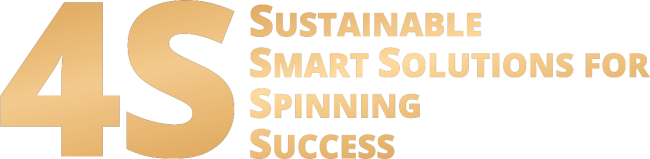
The Sustainable Smart Solutions for Spinning Success (4S) from LMW, supported by a culture of innovation, empower mills with a technological and competitive advantage. This is achieved through mission-critical automation, real-time data, analytics from connected machines, compatibility with all applications, and reliable performance under diverse operating conditions.
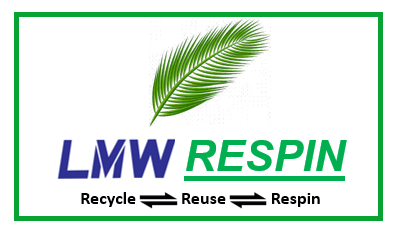
With an exhaustive range of offerings, the ability to scale and a culture of innovation LMW is committed to offering superior value today and in future.