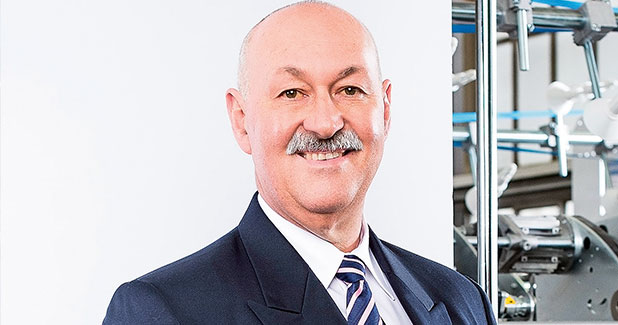
75 years of glorious history
The Swiss textile machinery industry is strongly export-oriented and has a presence with its own companies, sales and service organisations in all the world’s key markets. Consistent customer focus, innovative overall solutions and state-of-the-art technologies are the guiding lines, what makes these companies global leaders in their sector.
The Swiss textile machinery industry is strongly export-oriented and has a presence with its own companies, sales and service organisations in all the world’s key markets. Consistent customer focus, innovative overall solutions and state-of-the-art technologies are the guiding lines, what makes these companies global leaders in their sector. The division is a member of the European industry committee CEMATEX, the owner of ITMA, the world’s largest international textile machinery exhibition.
The year 2015 was a special year for Swiss textile machinery – it celebrated 75 years of glorious achievements. That year also coincided with the ITMA Milano in November, in which 62 Swiss companies—the fifth largest country representation—exhibited showcasing their latest innovations – machines and solutions along the entire textile value chain from spinning to weaving, embroidery, printing to quality control systems for the textile industry.
Said Ernesto Maurer, President of Textile Machinery Division, Swissmem: “And yet our 75th jubilee is also a proof of the positive aspects of evolution. The Swiss textile machinery industry has evolved and in the process has become stronger, constituting a robust pillar in the framework of European textile machine manufacturing today. In line with its centuries-old tradition, Switzerland has continuously developed its export business. Through their numerous international subsidiaries, Swiss textile machine manufacturers control far more than is revealed by national customs statistics. The international network of the member companies is, and will remain, impressive.”
“Over the coming decades, the secret of our success will continue to lie in the key factors of innovation, flexibility and perseverance. These are the typical entrepreneurial traits of our founding enterprises. There is no nobler thing than to foster these values and to take on the next 75 years with our heads held high.”
In December 1940, representatives from 22 companies met in Zurich to form the first textile machinery group within the Verein Schweizerischer Maschinen-Industrieller (VSM). The wartime demand for raw materials made it difficult for the machine-builders to obtain supplies in these early years of the association. An added problem was the question of cooperation with the German producers, who were the biggest competitors for Swiss manufacturers.
The 1940s was a decade of challenges for textiles, with clothing officially rationed in many countries. Fashion designers tried to stimulate demand, despite the shortages. Nylon stockings appeared in the US, and five million pairs were snapped up in a single ‘National Sales Day’ by eager customers. But their instant popularity was cut short when America’s production facilities were diverted to wartime materials such as parachutes. Switzerland’s wartime neutrality meant the country suffered minimal economic damage compared with other European countries. After the war, the Swiss industry was able to mount a rapid recovery, ready for the new growth of the 1950s.
Natural fibres such as wool, cotton and silk were the only viable textile raw materials throughout history. Rayon, based on cellulosic raw material, was introduced as ‘artificial silk’ in the 1920s. DuPont’s development of nylon in 1938 brought the world’s first true synthetic fibre. But it was not until the 1950s that the real boom took off. New polymer-based fibres such as acrylic, olefins and polyester made a massive impact, providing more than 20 per cent of America’s mill consumption during the decade. At the same time, demand for Swiss textile machinery was soaring, as textile mills tried to modernise their processes after the investment slowdown of the war years. This was despite competition from German machine producers, who benefited from the effects of US recovery funds under the Marshall Plan.
This was also the decade of innovation in textile technology. Almost every process was revolutionised, with ground-breaking inventions in the key spinning and weaving sectors which are still in the forefront of textile manufacturing today. Sulzer’s projectile loom, for example, paved the way for a new generation of shuttleless weaving methods, taking the Swiss company to global market leadership. Spinners, meanwhile, benefited from new, high-performance carding machines and the ringframe was now clearly the dominant yarn-making machine. Saurer’s 2S-55 shuttle embroidery machine set a benchmark in this technique, which was to last 20 years. Textile finishing developments included the first high-temperature dyeing machines for synthetics, and a trend to reduced liquor ratios for water savings.
The 1960s was a decade of great change in the world. New attitudes to cultural, social and political issues pervaded every aspect of Western life, from the ‘Swinging Sixties’ to the era of mass protests and demonstrations. The Space Race was won by the US, when astronauts Neil Armstrong and Buzz Aldrin touched down on the surface of the moon in the year 1969.
The growth in electronics technology spawned by the moon shots was also responsible for some important advances in textiles, notably including the launch by Swiss company Zellweger Uster of the first yarn clearers, able to control yarn quality automatically during winding. Automation of many textile processes accelerated, with improved efficiencies in both ring spinning and package winding making the industry less labour-intensive. Rieter’s chute feed system for carding machines was another significant novelty.
In 1967, Switzerland hosted ITMA for the only time in the history of the world’s biggest textile machinery exhibition. And the Basel event provided many landmark innovations, not least being an explosion in shuttleless weaving, with an estimated 40 different machines displayed, including prototypes of both air- and water-jet weft insertion methods. Swiss weaving machine builders were on top of the world at this stage, in the form of Sulzer, Saurer and later Ruti, who were soon exporting thousands of machines worldwide between them. A sideshow to the main Basel event also unveiled the earliest commercial open-end rotor spinning machines, soon to rival ringframes in specific yarn applications.
Globalisation of all the main market segments was a major trend at the beginning of the new millennium. The internet facilitated easy and cheap communication and collaboration for companies around the globe. Subsidiaries in India, China and other Asian countries became very important for Swiss textile machine manufacturers, taking them inside the world’s leading textile-producing regions. Quality was increasingly a priority in many fields of consumer and industrial products. As a result, demand was growing for textile quality testing instruments for laboratories and yarn clearers for in-process control. In the wider textile industry, this effect was evident with the heightened interest in ‘Swiss Quality’. Airjet spinning technology achieved greater commercial penetration of the yarn manufacturing sector, competing with rotor, ring and compact methods for a share of the market.
More and more applications for technical textiles were developed, with processing machines adapted accordingly. At the beginning of the new millennium the production of synthetic fibres surpassed the production of natural fibres for the first time. China and India represented nearly 50 per cent of worldwide cotton production.
Since ancient times, textiles has mainly been about the production of garments. But there are some other very old applications, which we today would call technical textiles. For example, felted wool has been used for the construction of yurts for at least 3,000 years…
Today, technical textiles are becoming increasingly important and there is a growing field of application. The range is very broad: vehicle manufacturing, aerospace, medical applications, construction, agriculture and many others. Base materials include natural or synthetic fibres—as in conventional textiles—but also glass, metal and ceramics. Technical textiles can have various advantages compared with other materials. They are lightweight, their surface is extensive compared with their volume, and they can be flexible and tear-resistant at the same time. Properties can be designed according to the requirements of the application.
Machines for technical textiles are often similar to those already used in other fields. However, in many cases they have to be modified, for example to cope with different types of materials. In future, technical textiles will be used in more and more application areas. Today the global market for technical textiles has an estimated volume of $150 billion and it is growing rapidly – an excellent opportunity for the textile machinery industry in Switzerland.