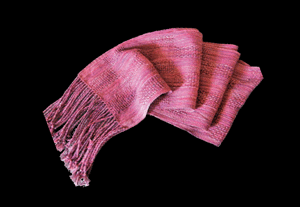
Yarn structure and its impact on softness
The process of converting fibres into yarn is complex, and requires many investigations and new technical solutions. The most common spinning systems to convert fibres to yarn are ring, compact, rotor, and air-jet spinning.
The process of converting fibres into yarn is complex, and requires many investigations and new technical solutions, feel Dr S P Borkar and Nitin T Patil.
The most common spinning systems to convert fibres to yarn are ring, compact, rotor, and air-jet spinning. Characteristics of yarns made from each of these systems and their limitations are briefly described under.
Ring spinning
In ring spinning, the fibre mass of the rove is reduced by a drafting unit. The twist inserted moves upwards and reaches the fibres leaving the drafting unit. The fibres lay around one another in concentric helical path. The normal force encountered by the fibres enhances the adhesive forces between the fibres and prevent fibres from flying or slipping past each other under the tensile strain.
It is the process of attenuating the roving strand until required final yarn count achieved and inserting twist to the fibres by means of a rotating spindle and winding the yarn on a bobbin. These three stages take place simultaneously and continuously. The ring yarn is characterised by high flexibility in the use of the raw material, the yarn count and the yarn character. It possesses a high degree of strength and yarn hairiness.
Compact spinning
All the improvements and optimisations of the ring spinning process only partially relieve the problems caused by the spinning triangle. The spinning triangle formed by the fibre bundle at delivery roll nip is the weakest point in the ring-spun yarn forming process.
Based on a thorough analysis of the spinning triangle structure, reached was the conclusion that only successful solution of the spinning triangle problem would enable the production of the ring-spun yarn with less hairiness and better physical-mechanical properties.
The ring spinning process with the minimised spinning triangle is called the compact (condensed, compressed). Compact is also distinguished by extremely high strength, even yarn structure, low hairiness and high yarn density.
Rotor spinning
In rotor spinning, fibre bundle from the sliver feed stock is separated into individual fibres with an opening roller in an air stream and fibre are re-collected in the rotor groove. The rotating, brush-like open yarn end first catches fibres in the core and then with further rotation gradually takes up fibres towards the periphery. In the interior, where the fibres cannot avoid the twist, the strand becomes more compact but also somewhat harder. On the other hand, towards the exterior, compactness and hardness fall off to an increasing degree, since here the fibres are partially less twisted-in. Shortly before leaving the rotor groove the twisting yarn catches some single fibres, which then are wound around the fibre compound like wrappers. Those "wrapper fibres" are a typical characteristic of rotor yarns.
Air-jet spinning
In air-jet spinning, a sliver is fed to the drafting system; the drafted sliver enters a spinning nozzle. The leading end of the fibres forms the parallel yarn core; the free fibre ends are wound around the yarn core by the air in the spinning nozzle. The air-jet yarn is then wound onto a package.
The air-jet-spun yarn structure consists of core fibres without significant twist and covering fibres with a genuine twist, which ultimately produces the corresponding yarn tenacity. The specific yarn structure results in yarn tenacity between that of a ring-spun yarn and that of a rotor-spun yarn.
Yarn structure and its influence on end product
The yarn structure primarily depends upon the raw material, spinning process, spinning principal, ma