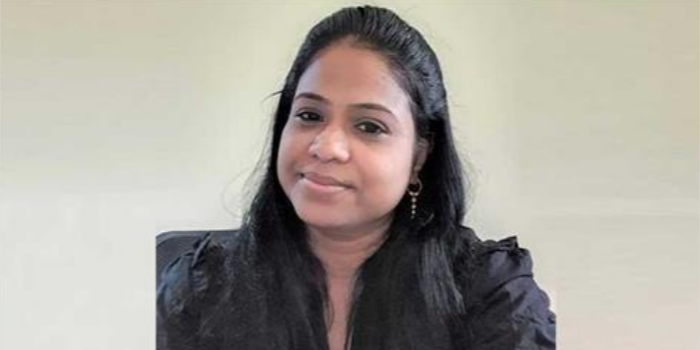
We help textile companies to mitigate risks and ensure products standout
SGS has state-of-the-art laboratories with complete capability to manage a full spectrum of services, from sample pickup through to testing, along with inspection, verification, and audits which are trusted by brands and retailers in India. The company stands for expertise and detailed understanding of the consumer goods and retail industry, and can help to build a stronger and strategic business model. SGS offers a wide range of services to support industry such as general chemical, physical and functional testing, technical support, certification, and sustainability and chemical management services, including wastewater testing, MRSL testing, root cause analysis service etc. Anitha Jeyaraj, Deputy Director – Softlines, Connectivity & Products, SGS India, explains to Divya Shetty about the company’s stage testing and inspections process and what the industry is now focusing on.
What types of solutions does SGS provide for the Indian textile industry as well as globally?
In India, SGS has state-of-the-art laboratories with complete capability to manage a full spectrum of services, from sample pickup through to testing, along with inspection, verification, and audits which are trusted by brands and retailers. We have expertise and detailed understanding of the consumer goods and retail industry, and can help you to build a stronger and strategic business model. We offer a wide range of services to support industry such as general chemical, physical and functional testing, technical support, certification, and sustainability and chemical management services, including wastewater testing, MRSL testing, root cause analysis serviceetc.
SGS also offers one stop services for testing and product certification, including CE marking. We also offer the SGS (ICM), performance mark, and the environmental claims certification scheme (ECCS) mark. An innovative way for manufacturers and retailers to generate confidence and trust among consumers, our product marks bring transparency to the complex world of product testing and regulation compliance for textile products. They offer reassurance that a product has passed independent, third-party testing and provides consumers with independently verified proof that certain criteria have been met, allowing them to make more informed purchase decisions.
Besides this, market demand for product traceability is increasing. SGS has developed a new IT tool called SGSmart, which is a one-stop platform to manage supplier chains.
Globally, SGS is the world’s leading testing, inspection, verification and certification company with more than 96,000 employees strategically located around the world. We work throughout the supply chain, providing specialised business solutions that improve quality, safety and productivity, and also reduce risk. Our network of over 2,700 offices and laboratories helps customers navigate an increasingly regulated world by offering local expertise on a global scale.
How many segments does SGS caters to?
SGS provides a full range of testing services, starting with raw materials such as fibre and yarn, through to the finished product, plus materials and/or components, which are required by various segments in multiple product ranges.
We service a wide range of product categories. These include textiles and clothing, bags and accessories, functional and performance wear, footwear and leather, home textiles, nursery textiles and Personal Protective Equipment (PPE). Evaluation parameters include quality, performance, restricted chemicals, and regulatory and safety properties.
We also support factory specific parameters like wastewater testing, chemical formulation analysis, factory assessments, training services etc.
What kind of quality and testing challenges do exporters deal with?
The textile production cycle starts with the delivery of raw materials. High quality finished products can only be made with good quality raw materials, but the biggest challenge in the textile industry is non-homogeneous incoming materials. The next challenge is the processing, where so many varieties of dyes, chemicals and auxiliaries are used. Finally, preparing the finished products involves a lot of labour and manual skill, which also poses a big threat to uniform quality across the entire bulk. Every process poses a different type of quality challenge to the industry, and needs an independent team and professional experts to continuously monitor and focus on improvement.
SGS supports exporters with multiple stage testing and inspections such as pre-production, production, final stage, accessories and auxiliaries testing, etc. Verifications are performed for the required properties so that unsuitable materials can be rejected, or appropriate adjustments made before shipment or retailing.
Apart from the regular processes, the industry is now focusing on organic cotton, recycled polyester, circularity, wellness textiles, protection (e.g.UV), special anti- microbiological finishes, etc. The biggest challenge is ensuring the material supplied meets the claim and is aligned with the complete supply chain. SGS can support the complete range of testing and process verifications.
As well as challenges of quality, exporters and buyers also still need to prevent overclaiming for their products. To support the market, SGS has developed several certification schemes e.g. the ICM, ECCS and Performance Mark, for the verification of product claims.
Has the number of companies coming to SGS for testing increased as a result of increased exports?
Post-pandemic, the industry is in revival mode, and there is good improvement in the export situation. There is much improvement in testing volumes also. This drive comes from retailers who would like to show their customers a difference in various product features, e.g. verifying them as organically produced, recycled, produced responsibly, etc.
Manufacturers and retailers are more interested in demonstrating their ability to focus on creating and supplying products that meet very good quality specifications as well as legal requirements. Also, regulatory compliance in many countries requires comprehensive restricted substance testing for products, chemical management and the discharge of wastewater. Before any product reaches the marketplace, it is necessary to test the materials, to check that the properties have been improved or meet the desired quality specification of the buyer/end user, and that they have not been degraded by faster, more intensive, production methods.
With the motto of “Trusted means Tested”, SGS is engaged with textile companies to support them in the delivery of garments that consumers trust, and which meet sustainability goals as well as supply chain requirements. In today’s fast changing and complex markets, SGS can help textile companies to mitigate the risks and ensure products stand out.
Kindly elaborate on the new developments in technology for testing textile products and for QC/QA of textile products.
SGS has developed several programmes to support the market in enhancing quality, reducing risk, improving efficiency and ensuring compliance. Some of the interesting programmes, for example, cover digitisation and traceability. A company’s environmental impact comes through its supply chain, which leads to inefficiency and waste. Digitising the supply chain will save companies significant budget as a result of waste reduction, while also reducing their carbon emissions.
SGSMART is the global online platform for managing the complete testing needs of brands and customers. This is a great tool to manage the quality levels/specifications for multiple materials, components or factories.
Our new developments include special testing like vegan verification and non-GMO (genetically modified organisms) programmes. These are very handy for the supplier who wishes to verify organic or premium price claims. It is important to ensure traceability and transparency at these critical points. We analyse the material to ensure non-GMO cotton is used for producing organic textile products. In addition, laboratory testing is used to check for the presence of pesticides and chemical residues in finished products. Detection of chemical substances over acceptable limits means that an organic claim cannot be made.
SGS’s laboratory network is now equipped with the harmonised Digi-Eye and spectrophotometer system, and is also able to provide a virtual sampling colour assessment service. These can manage the colour supply chain from virtually anywhere in the world, without the need for physical samples. Our laboratories can capture a true sample image, which can then be accessed anywhere through cloud sharing. This has several benefits over traditional methods such as cost savings, fast communication, higher productivity and a shorter development time and cycle.
SGS in India has complete capability for services for the entire supply chain, from raw materials, REACH, factory wastewater and accessories testing, through to MRSL for the chemicals used. We also offer root cause analysis to help suppliers overcome issues/failures in chemical management. These, and many more services, are available to help to address any specific concerns.
SGS also offers Chemical Screening (SGS BRS300-2020) an advanced solution for commercial chemical formulations used in textile, footwear and leather supply chains. This is used to screen chemicals commonly used in textile and leather wet processing, raw materials production, machinery maintenance, wastewater treatment, sanitation, etc.
Do you notice a recent increase in clothes or garment testing?
There is a noticeable increase in testing due to various factors like sourcing shift, order volumes etc. However, in the past couple of years, the industry has faced order fluctuations, reduced volumes, shorter lead times etc. which have also impacted the testing orders.
In these changing scenarios, SGS strongly suggests a complete testing plan from raw material, including the accessories, components, chemicals etc. which are very important to ensure a safe product, through to fabric stage testing, to identify potential defects before the finished garment is produced. The pile up of stock has also created some new problems like quality deterioration, development of banned substances and microbiological issues due to long storage in chemicals, and weather conditions which also trigger additional testing to ensure good quality products.
Leading fashion companies are aligning with the UN 2030 sustainability agenda, with regard to supply chains and product life cycles, as well as developing their action plans and milestones accordingly. These need more testing to justify their claims, or to ensure they are on the right track to reach their goals.
In addition to meeting regulatory requirements, factories should also take care of effluent processing, chemical requirements etc. To help our clients to improve their sustainability and supply chain quality, we have developed holistic chemical management solutions, e.g. root cause analysis services to help their suppliers establish best practices during production to maintain their product quality.
What are your growth plans for the textile industry?
SGS has a digital and data platform – a one-stop solution to manage client testing programmes globally. Through data analysis, buyers can make timely decisions with action plans based on facts. SGS labs are state-of-the-art facilities with the latest equipment and highly accurate analytical instruments.
Virtual sampling colour assessment is one of the latest technologies we have adopted to manage the colour supply chain virtually, from anywhere in the world, without the need for physical samples. Our laboratories can capture a true image of samples which can then be accessed anywhere through cloud sharing.
We are offering a range of services under sustainability and chemical management, covering the environmental, safety and social aspects of sustainability, to support companies strategically. The services are:
Bluesign system
Chemical management
Hazardous substances control (HSC) workshops
International standard training programme
Labelling recommendations
Regulatory compliance for emerging markets
Root cause analysis
ZDHC programme
Recycling and upcycling verification
Preferred materials testing, verification and certification
Our knowledge and expertise will help manufacturers reach new heights in addressing issues such as climate change, pollution, product safety, and quality. In the end, it’s only trusted because it’s tested.