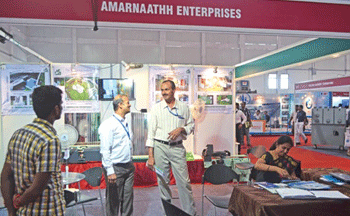
Upgrade your carding from Amarnaathh
Coimbatore-based Amanaarthh Enterprises (AE) has been one of the leading retrofit card manufactures in India for the last 25 years. More than 6,500 machines has been retrofitted in India and abroad.
Coimbatore-based Amanaarthh Enterprises (AE) has been one of the leading retrofit card manufactures in India for the last 25 years. More than 6,500 machines has been retrofitted in India and abroad.
Over the past four years, the company´s innovative AE240 carding machine has been performing well in OE, synthetic, and cotton processing industries for over 20 machines. AE240 card machine has the flexibility, depending up on the raw materials. In OE processing, AE240 machine can be able to deliver 1,250 kg per day with zero maintenance. In synthetic, dyed card can be able to deliver 150 mpm and other counts at par with latest cards.
Since card is delivering nearly 1.2 tonne per day to meet the customer requirements with improved , AE has started to manufacture the chute feeding system along with autoleveller. AE chute feeding system has been installed in the mills for the last three years with zero maintenance. AE also manufactures two different type of chutes – gravity chute and presser chute.
Autoleveller for Rieter cards for c1/2, c1/ 3 AE autoleveller consists of two feed roller at the back side. The first feed roller sensor senses the feed material thickness and AE autoleveller helps to controls over the lickerin feed roller before presenting to the lickerin in the carding machine. The delivery sensor helps to monitor the auto leveled material, and if any correction is needed, correction will carried out. The perfect combination of sensors with high sensitivity PLC with HMI and mechanical attachment helps to maintain the uniform CV% throughout the process.
For improving the quality of carding sliver, AE has introduced flat reversal with c-cleaner. It helps to open the lap feed batt in a very well manner in lickerin zone by introducing the 5 mm mode knife, waste control bar, red and green combing segment (life is 8-10 years). It helps to open the fibre better and reduce the strain in the cylinder. The advantages of our combing segment is removal of seeds as it has: no fibre rupture, avoids wires damages in cylinder zone is saved, removal of more short fibre, less fibre hanging in lickerin zone. Hence there is better opening of fibre in lckerin zone.
AE has introduced flat reversal with c-cleaner, which helps to open the fibre again and form three layer of fibre. First one is long fibre layer as it is very close layer to the cylinder, second is short fibre (no grip support from wires), third layer will be contamination, which evenly distribute the fibre throughout cylinder area. The cylinder one has divided into three triangle – fixed flats, revolving flats and undercasing. Fixed flats helps to control short thick and raw material faults, while revolving flats controls the neps and paralysing and remove more short fibres. Undercasing helps to open the fibre, which is less than 0.125 mm (unopen fibre from the cylinder zone) and representation to the stationary flats zone again. This is the main secret of the latest cards. It depends upon the raw material process. Cards are manufactured with different models. If we process short stable and more trash, raw material (OE yarn) needs more stationary. Flats with knife alongwith three lickerin has been introduced. The apron doff is also must for high production and handling of short fibres. If we process the man-made fibre like polyester, etc., it needs more stationary flats with single lickerin.
But in case of dyed material, more revolving flats is needed, no cards is available in market with more revolving flats (40 working like c1/3 cards) needed because dyed material will be getting immediately loaded in the stationary flats and become ineffective. More revolving flats help open the fibre better, comb better, paralise better, and helps remove the flat waste continuously. Less stationary flat is most suitable with more revolving flat is always advisable for synthetic, because flat reversal system is always one per cent more flat