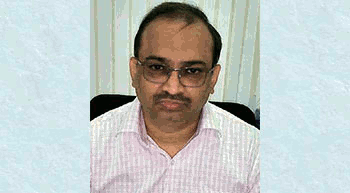
Tirupur was the first industrial cluster to implement ZLD in India
Tamilnadu Water Investment Company Limited (TWIC) is a pioneering developer of water/waste water projects in India. Promoted by Infrastructure Leasing and Financial Services Limited (54 per cent) and Government of Tamil Nadu (46 per cent). Over the last few years, TWIC has been in the forefront of a number of initiatives both in the urban water space as well management of industrial effluent.
Tamilnadu Water Investment Company Limited (TWIC) is a pioneering developer of water/waste water projects in India. Promoted by Infrastructure Leasing and Financial Services Limited (54 per cent) and Government of Tamil Nadu (46 per cent). Over the last few years, TWIC has been in the forefront of a number of initiatives both in the urban water space as well management of industrial effluent.
While speaking to the Editor of ITJ, I. Sajid Hussain, Head O&M (Water Reuse), TWIC, discusses about the various ZED projects undertaken by TWIC and its take on ZLD.
Can you give us some background details of TWIC, its inception and progress?
TWIC was promoted in the year 2000 by the Government of Tamil Nadu and IL&FS, essentially as an investment vehicle to implement 185 million litres per day (MLD), Rs 1,000 crore, New Tirupur Area Development Corporation Limited (NTADCL) water supply project in Tirupur for supply of water to the industry and the municipality. The project was the first public-private partnership (PPP) project in the water sector commissioned in 2006. Thereafter, the company ventured into textile and tannery effluent management zero liquid discharge (ZLD) projects. Today, the company is majorly into consulting and project management and operation and maintenance in the water and water reuse sector.
Give us details of the ZED/ZLD projects in textiles completed and ongoing in Tirupur.
Tirupur was the first industrial cluster to implement ZLD in the country and the first in the textile cluster in the world. Based on court directions, the industry wanted to implement ZLD. TWIC developed nine CETPs and is currently operating seven of them in Tirupur. The combined capacity of the nine CETPs is about 53 MLD.
What are the other textile projects undertaken in the other places? Both CETP and ETP.
As per directions of Chief Minister of Tamil Nadu, TWIC is now carrying out diagnostic study and detailed project reports (DPRs) for over 12 clusters in Erode, Nammakkal, Salem and Karur. This will cater to over 2,000 dyeing units in Tamil Nadu. The Government has earmarked Rs 700 crore for these projects. Two projects namely Kariyapatti CETP in Virudhunagar and Kadayampatti CETP in Bhavani have been accorded in-principal sanction for 50 per cent funding under IPDS scheme by the Government.
What is TWIC’s take on ZLD? Is this a possibility in India in the next few years or should we need more time?
ZLD technology and experience is only about 10 years old and has made rapid improvements during this decade. What was once thought as impossible has been successfully demonstrated.
Of course lack of experience and technology worldwide created several challenges in implementation of this project resulting in closure in 2011-12, however with the development of ‘treated brine reuse technology’ by TWIC and the support of Tamil Nadu Government, CETPs have now been successfully in operation for the last four years.
The Tirupur project developed by TWIC has won several international recognition including for the Highly Commended Industrial Water Project of the Year 2014 from Global Water Intelligence, UK; Industrial Water Reuse Project of the Year 2014 from WateReuse Association USA and Corporate Water Stewardship Award 2015 from GWI, UK showing the global recognition and actual success of the project. When the Tirupur dyeing cluster which was closed down in 2011-12, the exports stagnated at Rs 12,000 crore but since re-opening, the exports have strongly rebounded to Rs 24,000 crore in 2015-16, showing the overall impact of the dyeing cluster in the textile value chain and the positive impact of ZLD.
The major challenge is to reduce the operating costs. The cost of operating ZLD results in a 12 to 15 per cent increase in the cost of the dyed fabric, however, with recovery of salt and water this can be brought down to 5 per cent. This still is a significant cost for what is essentially a job work industry. We have realised that the cost of energy (power and steam) contributes to 50 per cent of the operating costs, therefore we need to develop low energy technologies.
We are also suggesting to couple all ZLD CETPs to captive power plants (CPP) with cogeneration of steam, this would reduce the operating cost by 40 to 50 per cent. This would essentially mean that the impact of ZLD on dyed fabric can be brought down to less than 1 per cent. This would mean ZLD at almost near zero cost! TWIC is also looking at several interesting technologies to further bring innovation and lower operating costs in the next few years. The major issue today is lack of strict implementation of ZLD in clusters other than Tirupur and other parts of the country, which can ensure a level-playing field.
One of the advantages of ZLD is that monitoring is easier as any discharge from the industry means non-compliance, which can be noticed even by a layman unlike in river/marine discharge system where the effluent needs to be sampled and analysed in a laboratory to confirm compliance to standards. While river discharge is not an option as meeting TDS standard of 2,100 mg/l is not possible for most textile effluents and also for other polluting industries, marine discharge is still a ‘lower opex’ option. However, many marine discharge CETPs are reportedly not doing well. Monitoring them and their impact on the marine ecology will continue be a challenge.
What are the USPs of TWIC in the effluent projects?
We work and focus on projects which recovers water for reuse. We also focus on recovery of salts and other chemicals and energy. In short we look at wastewater as a resource. We do not work in projects with conventional treatment which focuses on meeting standards and discharge into the environment. We feel there is no incentive for the industry to meet the standards under such a scenario which is reflected in poor compliance of standards in most CETPs/ETPs. Therefore recovery and reuse in all ETP projects is a must.
How can one compare the effluent management practices in India with other developing countries?
We aren’t blessed with the nature’s bounty as seen in most developed countries. Our rivers are dry during most parts of the year and many are polluted. Our ground water too is depleting alarmingly and most parts of the country will be severely water stressed by 2020 due to over exploitation of water, large population growth and pollution. Therefore there is a need to innovate and go beyond what the developed world has so achieved. Therefore ZLD is our way forward.
Implementation of ZLD will also push the boundaries for technology, which today still comes from the developed world. Countries like Bangladesh too are considering implementing of ZLD by 2021 for their textile sector and are learning from the Indian experience. Countries like China too have started implementing some ZLD projects in the coal to chemicals sector. As compared to most developing countries, we have formulated stringent laws, implemented CETPs all over the country, however we lack in their successful operation due to lack of incentives.
ZLD: Awake now or never….
– Avinash Mayekar of Suvin Advisors
Industrial growth will definitely come to an end, if environmental-related issues are not taken care immediately. Industrial pollution is the major issue faced today but still the awareness is not much in India. Many industries are implementing effluent treatment plants (ETPs) just because the Government has enforced stringent laws otherwise, in our country people are least bother about harmful effects of pollution on the environment. If we see our own industry, textile industry is one of the largest contributors in water polluters. The World Bank estimates that almost 20 per cent of global industrial water pollution comes from the treatment and dyeing of textiles. The hazardous chemicals, that are used in a dye house or a printing unit, do not all remain on the final product – the fabric – but get washed out and drained through the effluent discharged from the production factory into nearby river bodies and municipal sewers.
In textile industry there is enough scope to recover salts and brine solution which can be reused in the manufacturing process and reduce the impact of treatment cost on the overall cost of production. Lesser waste water means lesser treatment cost and thus improving water use efficiency will have significant benefits especially for industries like textile industry, which have a considerably large water footprint. For imparting desired quality to the fabric, the unit carries out series of processing steps continuously or discontinuously (such as desizing, mercerizing, bleaching, dyeing, finishing and printing). In the process, many chemicals, dyes and auxiliaries are used, out of which some are very harmful for environment.
Environmental norms
The use of hazardous chemicals in the textile and apparel wet processing has been under the scanner of MPCB, CPCB, MOEF and forest departments. The Indian Government has initiated a draft regulation on October 22, 2015, which will make zero liquid discharge (ZLD) mandatory for textile units having wastewater discharge of more than 25 KLD (Kiloliters per day), including re-use of the treated water back in process. No groundwater extraction will be allowed by industry except for make-up water and drinking purposes. CPCB has suggested the small textile players to have industrial parks and treat their water in a common effluent treatment plant (CETP) based on ZLD principle. The Government are clamping down on polluting factories and implementing stringent laws for wastewater discharge, which includes ZLD.
Overview of ZLD
ZLD means zero or no discharge of wastewater or any liquid effluent from a factory to outside surroundings.
The entire wastewater generated due to processes inside a factory has to be treated and recycled back into the factory! ZLD – it is not a single system but a combination of various treatment processes which may vary from industry to industry. This is due to the fact that the type to technology depends upon the quality of effluent and process water quality requirement.
In order to achieve ZLD, we have to recover the water and salt separately from the effluent and reuse it in the dyeing process. As a simple explanation, the effluent is treated in an ETP comprising primary, secondary and tertiary treatment steps. The treated water is recovered from the membrane processes such as ultra filtration (UF), nano filtration (NF) and reverse osmosis (RO) during tertiary treatment phase and salt is then recovered by using multiple effect evaporation (MEE) with crystallisation. Fundamentals of ZLD system design or technical route for achieving ZLD include:
- Primary treatment
- Secondary treatment
- Tertiary treatment
- Membrane processes
- Evaporation and crystallisation
Primary treatment
- Bar screen: Raw Effluent from the source is usually received into the bar screen chamber by gravity. Screen provided will remove all floating and big size matter, which may otherwise choke the pipeline and pumps. Solids separated are collected into a basket, which has to be emptied periodically.
- Homogenisation: Waste water quantity and quality discharged are not constant; it depends on type of industrial process. In order to feed a biological plant it is necessary to have a homogenizing tank, where water is homogenised quantitatively and qualitatively, this guarantees a constant feeding and stable performance of the plant.
- Neutralisation: Normally wastewater coming from a textile process has a high value of pH 9.0-12.0, and biological oxidation needs in fact a neutral pH value, or a slightly alkaline one. Hence in neutralisation station, an automatic dosing of acid is driven to settle pH-meter.
- Cooling tower: Wastewater coming from dye house has high temperature with an average value of 40-42°C. This temperature can badly influence the bacteria activity and can cause suffering to electromechanical components as pumps. The cooling tower is used to lower the temperature up to 35 °C.
Secondary treatment
- Anaerobic: This tank is designed to have high concentration of bacteria and high concentration of nutrient anaerobic conditions that means without oxygen. In these particular conditions the filamentous bacteria tend to be removed for the benefit of those bacteria with better sedimentation properties.
- Aerobic biological treatment: The aerobic biological treatment is a particular kind of process where bacteria are in contact with the waste water and continuously oxygenated in the reactor.
- Sedimentation: After the oxidation tank the water flows by gravity to the sedimentation phase. The mixture liquor of water and bacteria goes from the oxidation tank to the clarifier, a kind of tank that in calm condition it permits the gravity sedimentation of the sludge. The sludge (bacteria) is collected in the clarifier bottom, a scrapper collect it in a pit point where by means of submersible pumps is sent again to the selector, so it stays in continuous recycling.
- Sludge thickener: Exceeding sludge coming out from sedimentation is pumped in a sludge thickener, which permits the increasing of the dry substance contained into sludge up to 2-3 per cent. The sludge should be thickened in a storage tank (thickener) where a reagent cationic polyelectrolyte is dosed to improve the thickening process. The sludge from the sludge thickener is then pumped to filter press for dewatering.
- Filter press: Filter presses are highly efficient for removing water from sludge. Filter presses operate on feed pressure and can be used for high volume separation of solids from slurries, utilizing membrane plates. Disinfection: The treated effluent is then added with chlorine to kill the pathogens or E-Coli coliforms, so that it becomes fit for disposal in the lake or water ways.
Tertiary treatment
- Pressure sand filter: Biologically treated water from the treated water tank is fed to pressure sand filter. Pressure sand filter is ideal for filtration of water having very fine suspended matter like mud, rust particles and biological growth. Pressure sand filter is a pressure vessel constructed of welded mild steel and provided with manhole with cover / top and bottom flanged covers, supports, raw water distributor, under drain collection and backwash water jet system.
- Activated carbon filter: After the removal of suspended matter and turbidity in pressure sand filter, the water is passed through activated carbon guard filter for removal of the color, odor and organic contamination in the water. Activated carbon guard filter is supplied as a pressure vessel constructed of welded mild steel and provided with flanged covers four leg supports raw water distributor, under drain collection and backwash water jet system.
- Membrane process:
- Ultra Filtration: The ultra-filtration plant here proposed in order to remove suspended solids still present in water. Treatment through membrane filtration is a technology for separation taking into consideration their weight. The plant is completely automatic, pre-assembled on a stainless steel skid and it is controlled by a PLC unit equipped with operator interface. The ultra-filtered water is collected in a tank and from here through horizontal centrifugal pumps is lifted to Softener.
- Softner: Filtered water passes through a softener (Ca & Mg ions are removed by the resin & equal numbers of sodium ions are imparted to the water). Ca & Mg salts present in water are called hardness. This hardness of water is removed by using Softener. The softeners contain strong acidic Cation exchange resin in sodium form. Resin has finite capacity for removal of Ca & Mg ions and after this capacity is exhausted, the resin will have to be regenerated to bring it back in sodium form.
- RO: The aim of reverse osmosis treatment is the 97-99 per cent reduction of dissolved salts and the removal of bacteria and organic substances, etc. from clean water which has already been treated through filtration or ultra-filtration. A multi-stage reverse osmosis treatment maximizes the reduction of those undesirable substances. RO utilises special semi-permeable membranes which enable water to flow through but not molecules, ions or other dissolved substances.
- Nano filtration: Nano filtration is a relatively recent membrane filtration process used most often with the purpose of softening (polyvalent Cation removal) and removal of disinfection by-product precursors such as natural organic matter and synthetic organic matter. Nano filtration (NF) is a cross-flow filtration technology which ranges somewhere between ultrafiltration (UF) and reverse osmosis (RO). Nano filtration refers to a specialty membrane process used for the removal of two valued ions and the larger mono valued ions such as heavy metals which rejects particles in the approximate size range of 1 nanometer (10 Angstroms), hence the term “Nano filtration.†Multi Evaporator: The feed to evaporation will be concentrated in three effect evaporator plant. Feed will flow in forward feed manner in evaporators. All three effects shall be of Forced circulation type. Concentrated product from evaporation shall be fed to agitated thin film dryer (ATFD) for separation of salt from salt slurry to meet ZLD. Whole evaporation system operates under vacuum. Common closed loop sealing water system shall be provided for flushing of mechanical seals of centrifugal pumps for proposed system. This sealing water system shall be included one plate heat exchanger (PHE), one balance tank and one dedicated centrifugal pump.
Merits of ZLD
- No impact on surrounding soil salinity
- No groundwater pollution
- Compliance with stringent legislative and environmental regulations.
- Conservation of water resource through recovery and re-use of treated effluent
- Reducing dependence and use of municipal water sources
- Recovery and re-use of salt used in the textile dyeing process
- Optimizing the industrial water cycle
- Consistency of water supply and quality
Challenges
- High capital and operating costs of ZLD
- Achieving ZLD in all the given industries as it depends on quality and contaminants in the waste stream
- Factories shift to the other areas (and pollute freely there) to stay competitive in market rather than installing a ZLD
- A ZLD plant will incur between Rs 1-1.5 crore/KLD in capex. Thus, the treated and recycled water costs approximately Rs 120-150/KLD, while the cost of water extraction from the ground or from the municipality would be between Rs 30-60/KLD
Conclusion
Although ZLD is an ‘end-of-pipe’ concept to mitigate the impact of wastewater pollution on the environment and human health. The cost of this recovered water recycled into the process is always higher than the cost of input water used from other sources but keeping the stringent norms of the pollution board and water scarcity in mind, it seems right decision to establish a ZLD. As far as operating cost is concerned, there are new technologies coming up which will reduce the cost of operation in ZLD. There are recent technologies in developed countries, which will soon be realised in India following the FDI. The technology will emphasise on oxygen transfer, which will be four times higher and reduce the energy usage in biological treatment. Similarly, new technology is coming up in RO, which will reduce the consumption of energy by 30 to 40 per cent.
India gaining momentum in CETP/ETP: Lanxess GM
LANXESS offers a whole range of innovative products that are used in the textile industry, the applications of which extend from textile auxiliaries, fibres, softener, lamination, and dyestuff. LANXESS offers a whole range of innovative products that helps to tap, safeguard, and inexpensively purify water – and to effectively reduce the waste of water. For example Ion Exchange Resins from LANXESS remove impurities from drinking water. In industrial waste water treatment, Lanxess offers a host of products under the brand name Lewatit® and Bayhibit®. Lanxess has been involved in setting up of CETPs and ETPs in Tirupur, and has always been associated with the Chennai-based TWIC.
Prakash Shanmugam, GM, Head of BU-Liquid Purification Technologies at LANXESS India Pvt Ltd, Thane, spoke with Samuel Joseph, Editor of The Indian Textile Journal in an exclusive interview.
Can you share with us about Lanxess’ textile business since its inception?
Lanxess already had a textile business unit but was sold off in 2003. Now, we have a division called Liquid Purification Technologies in which we have two kinds of products. First is the ion exchange resins, which are required to soften the water. The second is the reverse osmosis (RO) process, which is vital for the effluent treatment and such processes. So, basically, Lanxess is not an OEM building up any plants, but one who supplies the vital components for companies building ZED plants. We are working very closely with TWIC in the Tirupur area and for the CETPs there we are supplying the ion exchange and RO processes and equipment. First is the recycling process and then the removal of colours since after dyeing a lot of colours are a part of the effluents. This makes it a total of three applications in textiles that Laxess offers.
Lanxess India entered this market seriously only two years back. Because we found a lot of potential in this segment and also that the industry needs it badly and we have the technologies already. Last year, we even had a big seminar in Tirupur to make awareness about effluents and treatment and received a very good response. We showcased our applications in ETPs and such areas and many MDs from Tirupur companies showed keen interest.
Our company is in the growing stage, but we see immense potential in India.
Lanxess is an offshoot of Bayer, the German giant, which had four major divisions. One is the Agrochemicals Division, then the Pharma Division, the Material Science Division and the fourth, which is the smallest of all is the Chemicals Division. They hived off this last division and Lanxess was formed, which came into existence on July 1, 2004. Lanxess has most of the people from Bayer itself and the headquarters is Germany. There were 17 business units at Lanxess, which then went into a phase of restructuring, and now after 12 years, all businesses have been contained in 10 business units.
What is the strength of Lanxess in terms of tech supplier to the textile industry?
Our main focus is on two kinds of products as I mentioned earlier: One is the ion exchange product line and the other is the RO line. On December 2, 2010, we inaugurated the third resin manufacturing plant in India, 20 km away from Bharuch in a place named Jagadia in Gujarat. So, as of now, we have three major plants globally. First is the plant in West Germany, the second one near Berlin and Gujarat plant is the third. The Gujarat plant is the “Made in India†of the German plant – same technology, same high class products and processes. From the technical perspective, we have a full-fledged laboratory there. The strongest point is that the best international technology for effluent treatment is today available in India, produced in our own country with the best technical talents possible.
What sort of a network you have in India to take this technology across the country?
We have regional offices in Delhi, Chennai and other places depending on the verticals we are dealing with regard to the industry in and around such places. These two cities are very important to us and through them we can penetrate into all the markets of India.
What is your opinions on effluents & treatment in India in comparison to global experiences?
India is young in environmental issues. We are yet to catch up with the developed countries. The awareness is growing. In developed countries the movement towards environmental protection is at a peak. They are fully aware of the dangers of ignoring the signs of ecological degradation. If you take even China, they have moved up a lot in terms of green technology and environmental protection. India has started it late, but the momentum towards green movement and effluent treatment is gaining rapidly. Today, we can read about factories being closed if they are not following effluent norms.
What are your suggestions to the industry & the government?
The customers are well aware of the country’s situation. One thing is awareness but the next things is to get educated on what one should do. Our main mission is to educate the industry, and that is why last year we organised the big seminar which received a good response. Industry people from areas like Erode attended the seminar and since we have the technologies and solution, they were keen to put them into action. Of course, it is going to be costly, but somehow we have to do it. Because environment protection is of primary importance today in a world, which is getting polluted day by day. The Government on its part should also be stringent and use all conditions and orders to curb pollution. At the end of the day, effluents are being discharged into the rivers; cattle die, drinking water is polluted posing health hazards. We need a big push. There are CETPs coming up – in Tirupur, Erode and other parts of Tamil Nadu. This should be widened to cover more areas. Rajasthan and north Gujarat, where a textile belt is coming up, also should take up efforts to build world-class CETPs and ETPs.
What is the present and future strategies of Lanxess to propagate effluent treatment in India?
I myself have been in Tirupur many a time and is monitoring the progress of a few plants we have set up on experimental basis and showed the industry how the effluent treatment plants work. Industry is responding, and in the course of the next few years, we are planning to take up this on a bigger scale all over India. Today, effluent treatment is not a choice but a necessity because our very life depends on unpolluted water for everything.
ZLD will soon become a reality in India
For almost two decades in the industry, Enviro Analysts & Engineers Pvt Ltd offers services in turnkey projects, consultancy services and laboratory services. In addition to this, the company also supplies industrial chemicals and laboratory equipment to supplement these projects and services. Enviro has a well equipped laboratory recognised by MoEF. Further, the company has branch offices at Nagpur, Pune, Nashik and Tarapur.
Rohan Desai, Director of Enviro Analysts & Engineers Pvt Ltd, speaks with ITJ Senior Sub Editor, Karthik Muthuveeran in an exclusive interview.
Take us through the journey of Enviro Analysts & Engineers over the years. We are a 25-year old company. My dad started this company in 1991. Before this, he was working for environmental consultancy firm, which were dealing with wastewater turnkey projects. For more than seven years, he has worked there. During his tenure, he worked on his first big project for the Bisleri factory, Mumbai in 1992. He did the entire zero liquid discharge (ZLD) for the Bisleri factory. By the time, we had established ourselves in Tarapur, Maharashtra, which were dealing with a lot of chemicals. And then slowly we started growing in Tarapur, and now we have almost 120-150 wastewater units in Tarapur. This includes textiles, steel, pharmaceuticals, electro plating, etc.
What are the various services offered by the company?
If you have any industry coming up, then we provide environmental engineering solutions – it can be wastewater or it can be even environmental clearance, etc. We have been accredited by MoEF. We do layer studies, we represent them in front of the Ministry. Otherwise, we also provide system solutions to high-rise buildings. It can be rainwater harvesting, solar, etc. Industry-wise, we provide turnkey projects for wastewater treatment. We have a monitoring system and we have a laboratory which do all the analysis related to water and soil.
For textile industry, what have you done?
We have done many projects for the textile industry. We have worked for Welspun, Detco Textiles, and have provided consultancy to SK Garments and many more. There are at least 7-8 projects in Tarapur itself. We have done their turnkey projects, we have found solutions for their issues with the solutions control board and made sure that solutions control board has no issues with this.
What are the USPs of the technologies offered?
Specially in a place like Mumbai and around space is always a constraint. Companies that were there long time back did not have space for ETPs and wastewater. We had to find the solution and find the best in that space. One of the textile companies, Detco Textiles, they had to shift the ETP to some other place. But the space they provided was less than before. We made sure that everything suffices in the same area. If you look at the plant, you cannot figure out it is 300 to 400 kwH plant. The place they provided was only 150 kwH. Cost is always the issue especially in a textile industry.
Kindly let us know your ongoing or completed projects.
In textiles, we have just finished the Detco project. For Welspun, we did the whole consultancy service for them. For ETP, we only did the designing part and not the erection.
Tell us more about ZLD.
Definition of ZLD in terms of pollution control and in terms of a layman is: In every process, water is been used in a maximum. ZLD is a water treatment process in which all wastewater is purified and recycled. Why is ZLD become so famous? It is because, there is CETP all over Maharashtra which does not cater to all the plants. Imagine the CETPs were made in 1990s with the capacity of 25 MLD. Currently the minimum requirement is almost 100 MLD. Tirupur became the first textile cluster in India to achieve ZLD in their units. It has not reached that level yet. It will take time. ETP is based on four different processes: physical process, biological process, chemical process and tertiary process.
Is complete ZED a reality in India?
Of course it is. The biggest issue that comes is the trust factor. A lot of suppliers have become consultants now. We are design consultants who provide turnkey solutions. There are only consultants who does only supply but also provide designs and put the plant there with low cost. That is the biggest issue right now. Cost is also the biggest issue right now.
Small companies have still not adopted these technologies. Why?
I would rather say, textile indust