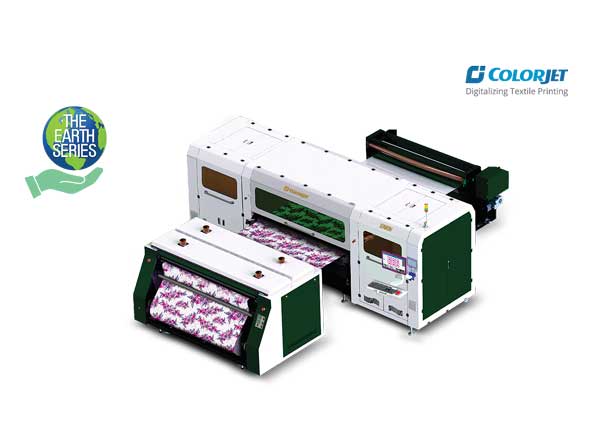
The revolution in textile printing
The textile sector has seen tremendous increase in digitalisation recently, and this trend is anticipated to continue in the future as well.
Nowadays, people want everything customised, including their meals, vacations, purchases, and services. Nothing makes individuals happier than having their chosen good or service may be customised. The ability to customise and alter things has made it feasible to modify things to suit one’s needs, and textile design is one of them. When digital textile printing first appeared on the market, it immediately became widely used.
The textile sector has seen tremendous increase in digitalisation recently, and this trend is anticipated to continue in the future as well. After years of relying on analogue printing methods, the textile industry witnessed a revolutionary change in the late 1980s when it became possible to digitally print text and images on cloth.
The creative process is being accelerated by advances in colour harmony and design, which are cutting the development time from months to weeks or even just a few days. Textile printing has been significantly improved, making it possible to make any length of fabrics or garments as needed.
With the development of advanced workflow automation solutions, satisfying the needs of designers and brands striving to meet the quick changeover is now possible without the need to prepare a cylinder or screen.
Benefits of digital textile printing
Wide coverage areas, limitless colour combinations, excellent design sharpness, quick turnaround times, real-time, instantaneous transfer from screen to fabric, printing on any textile material, and taking up less space are the main advantages of digital textile printing over traditional analogue printing.
- Low-cost establishment
- There will be less waste and no need to dispose of surplus dye and chemicals that are harmful to the environment
- Printing on demand with high printing accuracy and sharpness
- Less operational area is required, as is the use of resources and inventory
- When compared to traditional printing, it requires less education
- Rapid sampling and quick dispatch
- Affordable for both small and large orders
- No nickel deposition of screens into fabric (stricter norms and regulations in the future
Latest innovations
Companies are adopting the newest technologies at a breakneck pace in order to survive in this competitive market and meet consumers’ growing demands. Here are few companies who have made a breakthrough innovation in the last one year.
Colorjet
Earth Series Digital Printer- Pigment printing solution: This water based pigment ink is used with a binder for fixation to fabric. In this printer, pre and post treatment is not required which results in water and energy saving. It offers polymerization at 160 degrees temperature after printing provides excellent colour fastness and print quality.
Metro NXT – Industrial production digital printer: This printer hasHigh production capacity of up to 9000 sq m/day. It has an eefficient ink supply system with 32 printing heads of Kyocera delivering sharp prints.
Embee
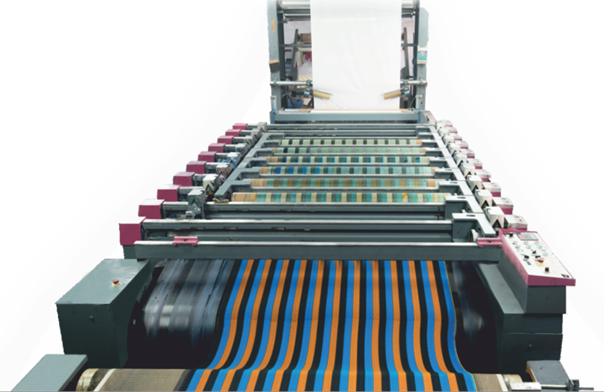
Acumen & Signature – Rotary printing machines: The machine has a high production output up to 90 m/min with high quality printing with automatic repeat setting and unique head lifting system and Multi repeat printing head. It offers options of closed bearing multi repeat (Acumen) and open bearing (Signature).
SPGPrints
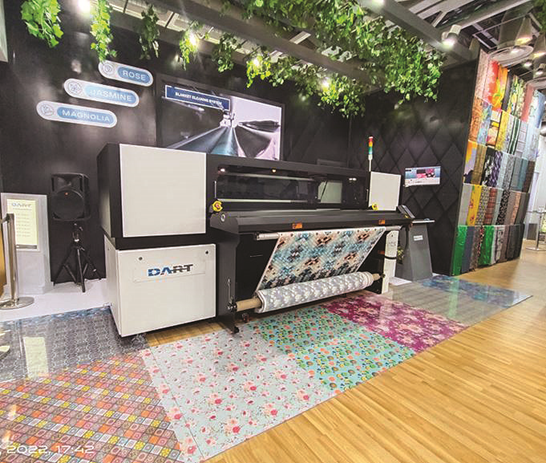
DART: SPGPrints launched the new robust entry level digital printer – DART for its Indian customers who want to kick start their journey in digital textile printing. We also introduced the addition of 3 new digital printers in the portfolio – Rose, Jasmine, and Magnolia, that focused on maximum productivity at optimal print resolution. Rose is a roll-to-roll paper sublimation system with a maximum resolution of 1200dpi, the print quality offered is excellent. Jasmine and Magnolia are direct to fabric systems that will enable our customers to extend their offering in digital printing. Jasmine focuses on maximum productivity at the most optimal print resolution where Magnolia with its true 1200 dpi and Archer+ technology raises the bar to new levels of print quality.
Konica Minolta
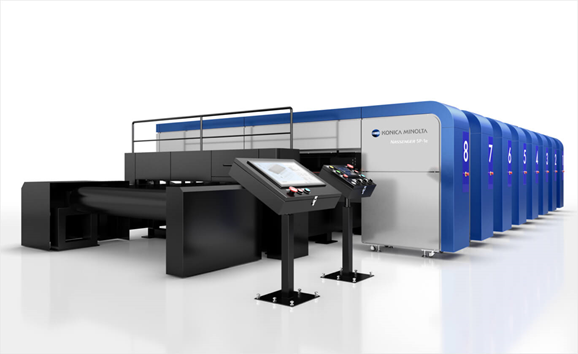
Nassenger SP-1e: This is a Ultra-high speed single pass printer realizes over 10,000m job and promote to exchange traditional rotary and auto screen machine. NASSENGER SP-1 uses single-pass technology that prints on cloth (media) fed on a belt under the fixed printing units. The result is an inkjet printer that achieves comparable production quality to screen printers. It is is equipped with a newly developed printhead module for single-pass printing. In addition, our proprietary ink injection control technology has reached a new level that allows flexible ink adjustments for small, medium, or large drop sizes. Ultra-high speed, yet fine detail and excellent gradation results as well.
Kornit Digital
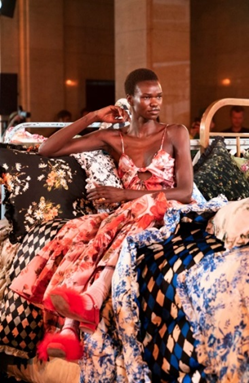
MAX technology: These solutions allow fulfillers and brands to enjoy unmatched retail-quality applications, including 3D, vinyl, screen, dye sublimation, and embroidery effects – all in one solution. Kornit is setting the pace across industries- spanning apparel, sportswear, home décor, accessories, custom fabrics, and other diverse, high- fashion textile – with its end-to-end digitized production workflow and lean, agile and profitable just- in-time fulfilment. Kornit enables its customers to establish fast and integrated production workflows for superior quality and durability with a smaller physical footprint.
Way forward
The introduction of digital textile printing would fundamentally alter how businesses chose to produce anything from bedding to home furnishings in India. Digital printing technology excels at creating small print runs rapidly and affordably. Personalisation works best on platforms intended for digital printing. Digital printing is the sole option if the industry wishes to easily alter pictures and intricate details utilising variable data printing (VDP) with improvements in print speed and quality.