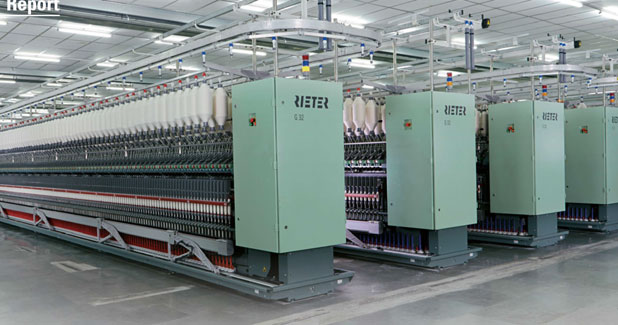
The profitable Rieter ring system
Despite historically low prime interest rates in the industrial nations, in many regions of the earth very high capital costs still prevail. For the affected customers, the question of the optimal design of their spinning mill in relation to the degree of automation and flexibility therefore still continues to be raised. Both factors have a significant influence on the investment sum and the associated capital costs over the depreciation period.
In order to lower the investment costs in ring spinning mills, Rieter has been offering the proven model G 32 for several years.
Despite historically low prime interest rates in the industrial nations, in many regions of the earth very high capital costs still prevail. For the affected customers, the question of the optimal design of their spinning mill in relation to the degree of automation and flexibility therefore still continues to be raised. Both factors have a significant influence on the investment sum and the associated capital costs over the depreciation period.
Comparison of capital costs
In order to keep the investment costs as low as possible, an automatic winder transport system was dispensed with and in its place the economic SERVOtrolley system selected. The automatic lap changing and piecing system ROBOlap, which is only available for the Rieter combers, is also an option in combination with the SERVOtrolley and is included in the calculation for this example.
More than 60 per cent of the capital costs, however, are incurred in the area of the actual yarn manufacturing. In order to lower the investment costs in the ring spinning mill, Rieter has therefore for several years been offering the proven model G 32. This machine was conceived as an economic solution, without the customer having to sacrifice the well-known Rieter yarn quality and highest productivity. To reduce the personnel costs in the end spinning sector, the automatic roving package transport system SERVOÂtrail is used. However, a version has been selected with reduced investment requirements.
The example
The spinning mill used in the comparison produces Ne 30 ring yarns from combed cotton for the knitting unit. The yarn production of the Rieter plant amounts to 489 kg/h. The practical data of existing mixed plant from three suppliers is compared to the Rieter values.
Lower yarn manufacturing costs
The economic advantages of the Rieter plant begin in the preparation. The clearly more selective cleaning of the cotton in the VARIOline blowroom is achieved, amongst other factors, by the B 12 UNIclean. By the way, this efficient preparatory cleaner can also be excellently integrated in existing plants from other suppliers.
In the carding section, the Q-package on the C 70 card provides further raw material savings. Thanks to the new Rieter combing technology of the E 80 comber, noil savings of up to 3 per cent compared to other machines are also possible at the same quality. In the end spinning unit, the higher productivity of the G 32 ring spinning machine with simultaneously reduced energy consumption due to the suction tube ECOrized leads to a significantly better economic effectiveness.
All these advantages result in 5 per cent lower yarn manufacturing costs, which amount to CHF 1,00,000 annually. Added to this is the additional contribution margin due to the higher yarn production of the Rieter plant. The slightly higher investment costs of around CHF 0.3 million for the complete Rieter solution are thus compensated in approximately two years. If we consider the total service life of 14 years, an additional contribution margin of CHF 1.91 million thereby results.
Attractive financing solutions
A further advantage of a partnership with Rieter is the possibility of a tailor-made financing solution for the complete package from bale to yarn. Our experts for export financing will be pleased to work out a corresponding offer.
Alexander Stampfer,
Head Product Management
Email: alexander.stampfer@rieter.com