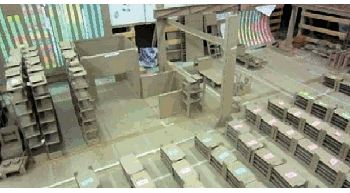
The Naroda 3P story
3P (Production Preparation Process) is designed to support and build on the foundation of lean principles. Without a solid base, lean implementation cannot succeed. When finished, 3P ensures processes have a one-piece flow; standard work and standard work in process pull systems.
A look at a rare lean jewel in the Toyota tool chest. Ingersoll Rand tells a tale of success.
3P (Production Preparation Process) is designed to support and build on the foundation of lean principles. Without a solid base, lean implementation cannot succeed. When finished, 3P ensures processes have a one-piece flow; standard work and standard work in process pull systems.
Toyota has no fear in sharing its success stories, mainly because it takes such a culture change to implement and sustain the Toyota House of lean. This Japanese culture is hard to mimic as it was derived out of necessity, and the invention sprang from a need: After the World War II. Japan was devastated, when faced with rebuilding; they had a lot of people and a huge lack of resources. They discovered how to rebuild and improve by people working together without resources, and without money, which is at the heart of 3P. When you visit Japan, try to find a garbage can, they are few and far between because, they have learned how to do much with less. They recycle their resources and minimise waste.
3P is about identifying the eight wastes of LEAN and training people on how to eliminate those wastes; the process teaches people how to be waste killers. At Ingersoll Rand, a world leader in creating comfortable, sustainable and efficient environments, we are using the process at an existing manufacturing site (brownfield) in Naroda, India to renovate and rebuild a facility that was built in 1965.
This project is a three-year plan, with three phases. This article will address phase one. Brownfield sites are challenging as we need to keep producing products to meet customer demands, while rebuilding the new facility at the same time.
Getting started
Plant transformation 3P?s start with goal setting. Below was our target for phase one.
1. One-piece, mixed model production flow lines
2. Change from post-assembly paint job to pre-assembly painted parts
3. Remove contractors from plant, build core competency in our people
4. Increase employee engagement survey score by two points
5. Remove as many monuments as possible to allow for future Kaizen
Our phase one goal was to begin building core competencies within our own workforce for certain high-skill jobs to eliminate our reliance on costly contract labour to build and improve the capabilities of our top asset: our people. Our efforts were greatly aided by the powerful close-knit culture in India. It is not uncommon to see grown men walking hand and hand, arm over shoulder as they stroll down the street; I found the people a joy to work with as I traveled at least once a month at the height of our 3P transformation effort.
The process begins
After we set our 3P phase one goals, we assembled a cross-functional 3P design team to work in the 3P Obeya room. (An Obeya room is a war room where people involved with planning a new product or process can come together in a location where the key information is available.) The team represented functions whose components comprised the entire value stream: procurement, materials, engineering, manufacturing, EHS, human resources, quality, marketing, advanced manufacturing engineering, new product development, maintenance, strategic initiatives and most important of all, the operations represented by operators from the manufacturing floor. At this point lean training began on the eight wastes and quality-at the-source. We benchmarked our 3P based on the standards of world-class facilities and world-class supply chains.
For example, in world-class facilities you do not see forklifts but rather lean flow lines without common monuments such as cranes, pits, ovens, services and walls. A perfect manufacturing floor for 3P is a clean unobstructed cement slab because we know as demand fluctuates we need to change and adapt our playbooks.
3P concepts demand this
Transportation, motion and walking waste are eliminated when we remove these monuments and improve safety. We created a swim lane value stream map that showed the process horizontally from order to delivery to the customer. After the map?s input and outputs were created, we simulated orders through the map and inserted Kaizen bursts at inputs and outputs of the system to illustrate who needs to work with whom to work ideas for eliminating defects from the value stream. This divided up the work very quickly and provided early ownership and empowerment to those personnel who know the most about these problems — they have the best chance of solving the problems and increasing cycle time to the customer.
The supply chain in India is rudimentary in some areas; it is not uncommon to see camels pulling steel deliveries, unpackaged parts being delivered in powered rickshaws and delivery promises unmet on a normal basis. One huge change was to assemble with pre-painted parts. The old facility painted our assembled products at the end of the assembly lines. Finding suppliers who can paint and protect the parts during shipment is challenging for the procurement team members.
After charging our suppliers to begin working on our new requirements, we turned our attention to the production process. We identified the flow of current state and drew a spaghetti diagram of the production flow, which identified the flow of parts, people and information. We started by identifying all the products we needed to merge by identifying the current cycle time of each and confirming that the product mix was close enough for success (utilising the 80?20 rule).
From the product families that emerged, the takt time, or pace of customer demand was calculated.
We first selected the longest cycle-time product within each group, knowing this will identify the largest space footprint and highest labour needed within each line. We then built the fishbone assembly chart of the machine and identified current sub-assemblies within each. After the charts were built, we took current defects, environmental, health and safety issues and placed these Kaizen starbursts within the fishbone diagram.
This showed us where we needed to improve and where we needed quality-at-the-source touch points to protect the process and ensure a quality end product.
By this time the team was starting to gain momentum and work very closely together ? the culture was starting to transform. 3P is all about using visuals to create universal understanding. We have a global workforce with varying levels of education and native languages. A visual management system like 3P equalises and empowers the workforce. Once the value stream map and the fishbone chart were developed, we held some seven ways sessions (a process to generate seven alternatives to encourage creative thinking) to gather best ideas, and utilised trystorm, a powerful tool of 3P. During the development of the light bulb, Thomas Edison?s Menlo Park labs try stormed over 10,000 ideas until they discovered the right material for the filament for the light bulb ? we did the same. A successful try-storming session is done in group setting and requires only brains, focus and your imagination?no computers?the digital age has segregated workers into cubicles by themselves whereas the 3P Obeya and trystorm events bring people together to collaboratively solve problems. For our events we confiscated electronic devices that distracted us from working together.
The next step is to create the takt time/cycle time chart, also known as the Yamazumi chart (used to make sure work is evenly distributed, meaning each operator has a full day?s work). This chart is also used to plan (schedule) shared resources or monuments if they cannot be removed. For example if five workers are in a crane bay and have to share a crane, if the five workers need the crane at the same time then the other four are waiting. Utilising a Yamazumi chart will enhance the success of any 3P project. The Yamazumi is built in concert with the process-at-a-glance sheet that shows material presentation needs, method of assembly, machines used, fixtures used and any mistake-proofing ideas that arise at each step. We also identify quality-at-the-source checks and total productive maintenance checks that ensure a robust manufacturing system.
While all of this is taking place there were a couple of small-scale modellers who started building the small scale simulation model. The model was designed on the new plant layout, proposed walls, columns, roof heights, doors, machinery, carts, and parts, and even included people on the plant floor, as if the observer were a giant standing inside the plant. Shrinking the scale enhances the team?s ability to communicate and collaborate as we simulated ideas in a target-state environment, something impossible to do in a real factory setting.
The takt time calculations gave us general station numbers to begin our simulations. We conducted another seven-way session to determine which future layout was most optimal for simulation trials. This was just a starting point the ongoing simulations change the layout as the team works through the process.
We were now ready to simulate. We had the stage (small-scale model), we had the script (Yamazumi and processat-a-glance data), now we started at the beginning and simulated each station using spaghetti charts for operator movements (we call them ant paths). As we simulated, if we reached for a scalpel and it is not there, we stopped the simulation and asked the team what we needed to do. Step by step we improved the process; we debated, and tried alternative solutions. Our thinking was all about LEAN thinking?s number one principle: defining value from the customer?s viewpoint.
Conclusion
This is where people really learn LEAN with their own processes, their own parts, and their own demand. We can talk about takt time, cycle time, but when you simulate the process you are not listening to a LEAN professional lecturing in front of a white board. This is the power of 3P: simulation. There will be many ah-ha moments as people learn and grow together over the power of the cardboard!
3P is all about people. When we simulate, we practice for the big game. We practice to win; we practice to be ready; we practice to win without fighting, pushback or finger-pointing, when we have launch issues, because there will be issues. Best of all, the customer is the one for whom we simulate and practice. The employees win because the practicing identifies the issues early so we can mitigate them, leaving start-ups free of stress and high cost fixes. Everyone knows what to do; simple cardboard aligns the entire team around a specific mission ? to develop the most optimal production line design to best serve the customer?s needs.
Results
Plant transformation Phase 1 goals delivered in 11 months, start to finish:
? One-piece, mixed model production flow lines
? Pre-painted parts
? Contractors removed from plant
? Employee engagement increase of 11 points
? Many monuments eliminated flexibility enabler
Phase one has been a huge success. The Naroda team is just getting started and their small-scale simulation model is their 5S model, the final S stands for sustain, the model helps sustain the plant layout standard work. They will use the model for any improvements moving forward and as a powerful tool to sustain their LEAN journey. They will also use it to train new employees and engineers coming into the plant. They are now actively building visual systems, shadow boards and MDI (Managing for Daily Improvement) boards into their daily standard work. There are no forklifts on the floor and everything is mobile to accommodate improvements and growth.
Phase two is now underway and I look forward to seeing my colleagues? progress as they embrace this next step in their plant?s transformation 3P process. They know LEAN principles and have mastered the concepts, the best process to solidify LEAN thinking and a LEAN culture.