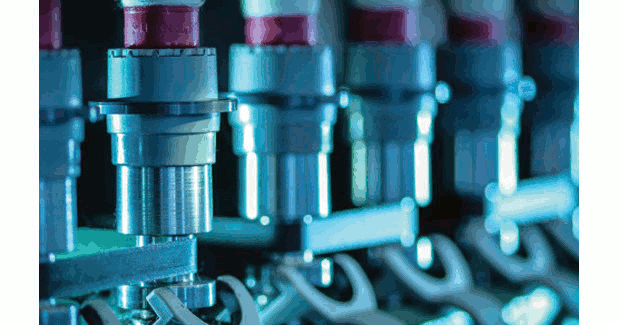
Textile machinery parts & accessories: Prospects
The Indian textile machinery industry is nearly 60-years old and has more than 1,000 machinery and component manufacturing units, says Avinash Mayekar.
The Indian textile machinery industry is nearly 60-years old and has more than 1,000 machinery and component manufacturing units, says Avinash Mayekar.
Textile industry can be broadly fragmented into two segments, one segment producing the actual textiles. From essential clothing to speciality materials i.e. technical textiles that provide technical advantages to numerous processes having application in almost every sector from sports, automobile, construction to industrial sector. The other segment is the one that take cares of producing machineries required by this sector. Naturally the ever increasing demand and need for innovations in textile is being reciprocated for tremendous demand and innovations in the manufacturing of textile machinery as well.
Globally the textile manufacturing industry is almost completely shifted to Asian countries wherein China is way ahead in the race followed by India. However the major textile machinery manufacturing sector for years is dominated by the European countries. Recently with the complete shift of the textile manufacturing sector in Asia, the machinery manufacturing market has also naturally started moving towards the Asian counterparts. The European dominated textile manufacturers are now having their manufacturing setups in Asian countries. By 2020, the Asian region will account for a market share of more than 90 per cent of the total textile machinery market.
The global textile machinery market is projected to grow at an impressive CAGR of nearly 8 per cent by 2020. The major countries manufacturing textile machinery are Germany, Italy, Switzerland, Japan, France and now China. The textile technologies are available in two versions, low cost (semi-automatic) mostly manufactured in China for low cost countries and high cost (automatic) for developed countries.
The Indian textile machinery industry is nearly 60-years old and has more than 1,000 machinery and component manufacturing units. Nearly 300 units produce complete machinery and the remaining produces various textile machinery components. We are having best quality of cotton and producing finest quality of yarns, fabrics and garments. The textile machinery exports from India to the world registered a growth of 20.03 per cent to $739.49 million in 2017-18. The export destinations for India’s textile machinery are Bangladesh, Germany, Netherlands, Pakistan, Indonesia, China, Turkey, Vietnam, Italy and the UAE.
India is being known as leaders in yarn producers for decades now and so naturally the high demand for spinning machinery have led to production of spinning machinery in India itself to further bring down the cost of imports. Fulfilling Indian market demands and comparatively low operating cost for production of machinery in India Indian textile machinery exports from 2012-13 have appraised a growth of 68.5 per cent. The major share comes from the Spinning and twisting machines segment accounting export value of $255.15 million in 2017-18 constituting 35 per cent of the total textile machinery exports. Bangladesh is the number one export destination for India’s textile machinery business. Asia being hub for textile manufacturing it is the largest export destination for Indian textile machinery market accounting for 55 per cent share.
Cotton spinning ring frames accounted a share of 59 per cent in total spinning machinery exported by India, registering a growth of 26.7 per cent registering a value of $150.16 million in 2017-18. These machines where majorly exported to the Netherlands. Cotton combing machines registered an export growth of 16.93 per cent for 2017-18. Vietnam is the top market for cotton combing machines. Cotton spinning roving frames has witnessed remarkable growth of 388.4 per cent amounting to $11.82 million. China is the topmost market for cotton spinning frame machine in 2017-18 recording a value of $7.06 million.
The exports for printing machinery including the digital printing machines had witnessed a negative trend in 2015-16 and 2016-17 of -14.6 per cent and -9.97 per cent respectively. But in the last fiscal year (2017-18) the commodity has shown a rising trend with growth of 24.3 per cent and having a 14 per cent share in the total textile machinery exports. The export for this commodity was $105.64 million in FY2017-18. Bangladesh is the topmost market for this product. Auxiliary machinery are the second highest commodity with respect to export value and growth. The commodity has seen a growth of 18.4 per cent with a 21 per cent share having export value of $156.38 million.
Weaving machine has witnessed average growth of 3.79 per cent amounting to $32.35 million with a 4 per cent share in the total textile machinery exports. This commodity has shown consistency in growing its exports value from 2012-13 showing a growth of 242.69 per cent. Exports of sewing machines and accessories are showing downward fall reaching -8.93 per cent valuing to $57.29 million in 2017-18.
Despite growth in the machinery Industry unlike China, we do not have full in house manufacturing of textile machinery. Most of the machinery are still being imported. India’s Textile machinery imports have registered a growth of 16.02 per cent compared to the previous fiscal registering imports of $4027.29 million in 2017-18. China, Japan, Germany, Italy, Switzerland, Belgium, Vietnam, the Philippines, Korea and Singapore are the top import partners. We are still importing a lot of textile machinery as there are only a handful of quality machinery manufacturers in India. There is hardly any Indian machinery manufacturer manufacturing machines for weaving, knitting that provides high level of quality standard and performance to compete with the European manufacturers. Imports of weaving looms have increased by 21.26 per cent in 2017-18 to $368.28 million. Even knitting, embroidery, trimming, braiding and other machines have shown an average upward trend with growth rate of 12.93 per cent summing to $365.94 million. In processing segment, printing machinery and digital printing machines are being imported the most by India from Asia with total of $1,098.28 million.
Conclusion
India needs to look into seriously the strategic decision of manufacturing textile/ technical textile machinery in a big way. While global renowned players in spinning like Rieter, Truetzschler have well established in India and ‘Saurer’, ‘Marzoli’ to follow soon, we have not done significant progress for weaving, knitting & fabric finishing machinery. Similarly technical textile machinery manufacturing is completely a grey area.
We need to understand the basic concept that if we are thinking of doing value addition in regular conventional textile business, we need to positively and aggressively think of innovating machinery manufacturing setup within India itself.
Various incentives given by central and state government mentions about it, but no concrete efforts are seen at ground level. We at Suvin, can help probable investors to completely roll out a plan by assessing existing situation and carrying out complete techno commercial study with location analysis for such investment plan.
The article is authored by Avinash Mayekar,MD & CEO Suvin Advisors