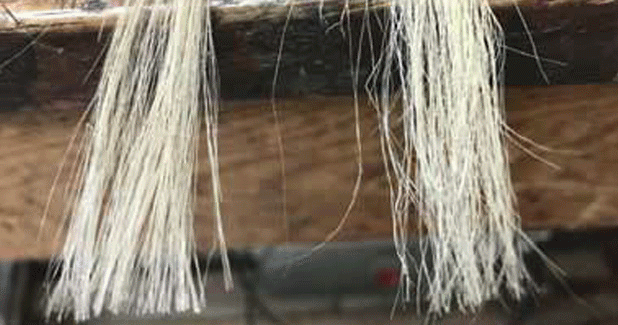
Jute reinforced PLA bio-composite for production of ceiling fan blades
In this project work, jute fabric is used as reinforcement and PLA (poly lactic acid) film is the matrix by which composites are made by stacking of number of fabric layers in between the PLA films.
In this project work, jute fabric is used as reinforcement and PLA (poly lactic acid) film is the matrix by which composites are made by stacking of number of fabric layers in between the PLA films. For surface modification of the jute fabrics, different chemical treatments are carried out such as alkali, acetylation, silane treatment and treatment with maleic anhydride. The differently treated fabrics have been tested by universal tensile tester machine and mechanical characterisation is done.
Among the plant fibers, jute is the second most important bast fibre after cotton because of its easy availability at low cost. It is produced from plants in the genus Corchorus, family Tiliaceae. Jute fibers are composed primarily of the plant materials cellulose and lignin. Jute fibre stiffness comes because of the cellulose. It also gives strength and stability. But due to the hydrophilic properties of cellulose, compatibility with that polymer matrix is difficult because they have hydrophobic nature. For this basic reason different surface modification methods has to be there for the jute fibre so that the interfacial adhesion can be improved. [2] While reinforcing the fibre with the matrix material, the cellulosic hydroxyl groups on the fibre surfaces make both the physical and chemical bonds. To say that bond between fibre and the matrix is good, number and strength of bonds between the two materials has to be better. [4] Compared to the traditional polymers (Polypropylene, polystyrene & polyethylene), PLA has better mechanical properties like: tensile strength, tensile young’s modulus, flexural strength, etc. besides the stated better mechanical properties, it has also its own Drawbacks like poor toughness property and for those applications which needs
Plastic deformation this poor property limits its use. [7] The influence of chemical modifications on jute fibres has been studied and reported in different works. Amongst them are: latex coating, alkali treatment, monomer grafting, silane treatment, isocyanate treatment, permanganate treatment, acetylation, and so on. With the stated modification methods, improvements have been seen on the fibre matrix adhesion of the composites. Usually the need for modifications is for improvements on wettability and making compatible the reinforced fibre with the resin material so that the produced composite is going to be strong and durable. [1] The ceiling fan blades are usually made up of aluminum, steel, wood, etc. The ceiling fans have become a common appliance both in domestic and industrial applications. Though the power consumed by these fans is less, it is to be considered that these fans run on a continuous duty and this makes the power consumption significant. Energy crisis and less availability of natural resources being the major challenge, selection of better material and effective manufacturing processes, can reduce both the power consumption and the manufacturing cost. Composite materials have found a wide range of application in replacing the conventional materials with enhanced strength and mould ability. Energy crisis is the major problem faced widely. Though wide range of researches is being laid in the areas of alternate energy sources, proper management of the available energy sources will contribute in controlling this energy crisis, particularly in high populous countries such as India. Ceiling fan being one of the vital electric appliance, consumes considerable electric power in most domestic and Industrial application. Imparting fibre reinforced composite blade in ceiling fans reduces the weight of the blade, thereby considerably reducing the power consumption. [16]
II. MATERIALS AND METHODS
Materials & Chemicals
Woven Jute fabric (1/1 plain fabric) and PLA (poly lactic acid) film were used. The following chemicals were used for chemical treatments and preparation of composites: NaOH,HCl,Aceticacid,Ethyl acetate,H2SO4,Amino propyl trimethoxysilane,Maleicanhydride,Acetone solvent, and Araldite epoxy.
Compression moulding machine,LCD Wind Speed Gauge Meter Anemometer & Thermometer,4 In1Digital Meter AC (80-260V/20A) Ammeter/Voltmeter/Power Meter/energy Meter are the equipment used for making of the composite blades and for testing the performance parameters.
III. METHODOLOGY
A. Jute fabric surface treatments:
Alkali treatment
5% w/w NaOH solution is prepared using sodium hydroxide pellets and distilled water. Then the fabric is dipped in NaOH solution for 1hour separately. After 1 hour, fabric is washed with 1% HCl solution for neutralization. Finally, it is washed with distilled water. Fabric is then kept in hot air oven for 3 hours at 70°c to hinder the water content.
Alkali treatment + Acetylation
The alkali treated jute fabric is then treated with acetic acid for 1hour at room temperature and then thoroughly washed with distilled water and dried.
Alkali treatment + Silane treatment
A solution of 0.5 wt% silane coupling agent [3-(2-aminoethyl amino) propyl trimethoxysilane] was prepared in acetone. Acetone was used in preference to water to promote hydrolysis to take place with the moisture on the surface of the fibres rather than within the carrier. It also promotes swelling of the fibre and so increases the fibre surface area exposed to treatment and the Alkali treated jute fabric is then immersed in the solution for 45 min. After treatment, fabric is removed from the solution and dried in oven at 650c for 1h. Finally, the fabric is thoroughly washed with water to remove chemical residues until a pH of 7 is obtained and then dried at room temperature.
Alkali treatment + Maleic anhydride treatment
In maleic anhydride treatment, the alkali treated jute fabrics were surface treated for 5 min with 1% solution of maleic anhydride dissolved in toluene solvent at 55ºC. After treatment, fabrics were washed in toluene to remove extra MA. The fabrics were then dried for 6 h followed by oven drying at 60°C.
B. Characterization Techniques
Evaluation of tensile properties of fabrics
Breaking strength and elongation of fabrics were tested on Universal testing machine following ASTM D 5035:1995 using load cell of 1000N. Five specimens were tested for each sample. The testing conditions are:
Width: 5cm; Thickness: 2mm; Length: 20cm; Gauge length: 7.5cm; Loading rate: 300mm/min.
Evaluation of tensile properties of composites
Tensile stress (MPa) and breaking extension of composites were tested on a Zwick tensile testing machineby following ASTM D 3039. A load cell of 50 KN was used. The testing conditions are:
Width: 25mm, 20mm; Thickness: 2mm, 3mm, 4mm & 5mm; Length: 175mm; Gauge length: 100mm; Cross head speed: 2mm/min
Testing of Inter-laminar shear strength of composite
By using Zwick/Z010 shear strength tester, inter-laminar shear strength of composite specimens was tested following ASTM D2344/D2344M – 16 using load cell of 5KN. The testing details are:
Thickness: 2mm; Width: thickness*2= 4mm; Length: thickness*10= 20mm; Span length: thickness*4= 8mm; Cross head speed: 2mm/min
Measurement of air velocity of fans
An LCD wind speed gauge Anemometer was used for measuring the air velocity (ft/min) of fans (both Usha and the composite blade) running at different speeds starting from the minimum to the maximum. Readings were taken at the tip (edge) part of the blades, where maximum air velocity is there and to get the actual readings data has been recorded just after completion of 3 minutes.
Measurement of power consumption of fans
Power consumptions of fans were measured using 4 in 1 Digital meter Ac (80-260V/20A). By using the wiring diagram at the back of the meter, 1st and 4th terminals of the meter are loaded to the power conductors of the fan’s regulator switch and through 20 A load current, 2nd and 3rd terminals of the meter are connected to the voltage supply of the regulator switch. Finally, the fan regulator has been switched on and readings are taken at different speeds.
IV.RESULTS AND DISCUSSION
Tensile properties of jute fabrics
The tensile strength and young’s modulus of un-treated and chemically treated fabrics are given and compared in Fig 1. The breaking extension (%) at maximum breaking load has been compared for the differently treated and untreated jute fabrics and the result shows jute fabrics treated with Maleic anhydride and Acetic acid exhibits highest breaking extension (%) and this is due to the fact that many constituent fibres in the fabric slips rather than catastrophic failure when breaking load is applied on the fabric and do not contribute for the load sharing, and hence, the fabrics show a lower breaking strength and tensile strength values. On the contrast, Alkali+Silane treated jute fabrics show the lowest breaking extension (%) value because of the catastrophic failure of the constituent fibres which in turn contributes for the load sharing and hence a highest breaking strength and tensile strength values.
Fig. 1 Tensile properties of untreated and treated fabrics
Alkali+Silane treated jute fabrics exhibits a higher tensile strength and Young’s modulus followed by alkali only treated jute fabrics (Fig.1). So for making of composite specimens with different fibre volume fractions and weights, jute fabrics treated with Alkali+Silane were only considered. Mechanical Characterization of Composite Samples
Three composite specimens made from Alkali + Silane treated jute fabrics as reinforcement by 60:40 fibre volume fraction to matrix volume fraction and with five layers of jute fabrics have been tested and results are compared with that of aluminum alloy 1050 H14, which is a potential candidate for making ceiling fan blades.
Fig. 2 Load-extension graphs of composites with five fabric layers (fibre volume fraction: 60%) Another four samples of the composite having the same volume fractions but only increasing the number of fabric layers to ten have been tested and compared and below the data is shown in figure 3 and table 3.
Fig. 3 Load-extension graphs of composites with ten fabric layers (fibre volume fraction: 60%)
Tensile Test of Composite Blades (70% Fibre Volume Fraction & sixteen fabric layers)
150 g weighing composite blade made from Alkali + Silane treated jute fabrics as reinforcement by 70:30 fibre volume fraction to matrix volume fraction and with sixteen layers of jute fabrics have been tested and results are compared with that of aluminium alloy 1050 H14, which is a potential candidate for making ceiling fan blades.
Fig. 4 Load-extension Graphs of composites with sixteen fabric layers (fibre volume fraction: 70%)
Tensile Test of Composites (50% Fibre volume fraction & twelve fabric layers)
150 g weighing composite blade made from Alkali + Silane treated jute fabrics as reinforcement by 50:50 fibre volume fraction to matrix volume fraction and with twelve layers of jute fabrics have been tested and results are compared with that of aluminum alloy 1050 H14, which is a potential candidate for making ceiling fan blades.
Fig. 5 Load-extension graphs of composites with twelve fabric layers (fibre volume fraction: 50%)
Tensile Test of Composites (50% Fibre Volume Fraction and Six Fabric layers)
75g weighing composite blade made from Alkali + Silane treated jute fabrics as reinforcement by 50:50 fibre volume fraction to matrix volume fraction and with six layers of jute fabrics have been tested and results are compared with that of aluminum alloy 1050 H14, which is a potential candidate for making ceiling fan blades.
Fig. 6 Load-extension graphs of composites with six fabric layers (fibre volume fraction: 50%)
Referring from table 3, tensile strength achieved for composite blades made with 50:50 fibre volume fraction weighing 150g is most comparable with the Aluminum alloy 1050 H14 but it is still heavier blade so composite blades made with 50:50 fibre volume fraction weighing 75g has been chosen as the composite blades because it is lightest one although it has a tensile strength value which is half of that of the aluminum alloy.
Short Beam Shear Strength Tests for Composite Blades Made with 50:50 Fibre Volume Fraction Weighing 75g
Short beam shear tests are often used to assess inter-laminar shear strength (ILSS) and to compare the effects of fiber surface treatment on the fiber matrix adhesion. A total of 9 composite specimens made from both treated (Alkali+Silane) and untreated jute fabrics having the same dimensions have been tested and results are also compared (referred to tables 4 & 5). Table 4 Summary of short beam shear strength tests for Alkali+Silane treated jute fabric composites with six fabric layers (fibre volume fraction: 50%)
So from the test results given in the tables (4&5) the composite specimens made with Alkali+Silane treated jute fabrics shows higher ILSS (inter-laminar shear strength) of 8.88 MPa and composite specimens made with untreated jute fabrics shows a lower value of 6.84MPa. A 23 % improvement on the shear strength is observed, because of the treatments.
So, based on the above stated mechanical characterizations of the different composite blades the one that shows the comparatively better properties and lightest one has been chosen and below in table 6 the weight and dimensions has been compared with the existing Usha fan blades. Table 6 Comparison of weights and dimensions of existing (Usha) fan and the composite blades made with 50:50 volume fractions
C. Performance of the Composite Fan Blades
The following technical parameters have been assessed and compared:
- Air velocity in ft/min,
- Air delivery in cfm,
- Power in watt and
- Service value in cfm/watt
As it is stated above (referring table 8), by using the composite blades there is a 15.65W power savings which is 0.01565Kw. Let in Delhi we use ceiling fans for 8 months per year for 12 hours a day. That is the fan will be on 12 hours a day for 240 days. So the energy savings will be calculated as:
- 0.01565Kw *12hr * 240 days
- =45.072 KWh/fan/year
For domestic use the electricity tariff in Delhi is about 4Rs/KWh. So, 180.3 Rs/fan/yearwill be saved.
Population of Delhi is around 20,000,000. Assuming that one family has four members, we have about 5,000,000 families. But from these families, those that can afford to buy ceiling fans be around 70 %. Then, the number of families who can afford to buy a ceiling fan is 3.5 million. Let, to the minimum 1 family has only 1 fan in home, so we are going to have a minimum of 3.5 million ceiling fans in Delhi.
So the monetary savings will be calculated as;
- 180.3Rs*3,500,000= 630 million Rupees or 63 crore Rupees savings per annum will be there.
So from the table (Table 9), service values for the composite blades are a little bit lower than the Usha fan blades due to the lower air delivery values of the composite blades that are because of the lower surface area of the blades.
E. Cost Analysis:
The composite blades are made with 50:50 fibre volume fractions, so the Wfibre = 53 &Wmatrix = 47. To produce composite blades weighing 75 g the following amounts of fabrics and matrix will be needed:
- 0.53*75g=40 g of fabric and 0.47*75g=35 g of matrix
- 1 layer of jute fabric having dimensions of 10*25 cm2 or 250 cm2 weighs about 6.6 g so 40 g of fabric will come about 6 layers. So to produce a blade with the stated dimensions and weight we need to have about 6 jute fabric layers.
Raw material cost
Jute fabric
- 1m2 jute fabric costs about 150Rs and the composite blades have dimensions of 10*25 cm2 or 250 cm2. So,
- 10,000cm2 = 150Rs
- 250cm2 = 3.75Rs (1 layer) so for 6 layers it will be 22.5Rs.
PLA matrix
- 1 kg of the matrix costs about 400Rs, but to produce a blade we need to have 35 g of it so the cost will be 14Rs.
- Chemicals cost
- NaOH
- 5 % of 40 g =2 g of it is needed,
- 5kg NaOH= 1405Rs
- 2 g= 0.562Rs
HCl
- 1 % of 40 g = 0.4 ml of it is needed,
- 500 ml= 100Rs
- 0.4 ml=0.08Rs.
Aminopropyltrimethoxysilane
- 0.5 % of 40 g= 0.2 g of it is needed,
- 500 g= 12,150Rs
- 0.2 g= 4.86Rs
Acetone
- 1 % of 40 g= 0.4 ml of it is needed,
- 2.5 L = 846Rs
- 0.4 ml= 0.14Rs
Araldite epoxy
- About 6 g of it is needed to bond one composite blade with the metal plate,
- 180 g= 250Rs
- 6 g = 8.33Rs
Manufacturing cost
- Motor power of moulding machine: 3000 W.
- Let’s convert this number to kilowatts by dividing by 1000, to get 3 kW.
- To produce one blade 8 minutes is needed,
- Let’s convert 8 minutes, into hours by dividing by 60, so 8 minutes is 0.133333 hrs.
- The moulding machine that has been on for 0.133333 hours, have consumed
- 3 kW*0.133333 hours = 0.4 KWh of energy.
- For non-domestic use the electricity tariff in Delhi is 5Rs / KWh,
- Finally, since energy costs 5.00Rs/kW-hr, the device will cost: 0.4 KWh*5Rs/KWh = Rs. 2
- So, total cost = raw material cost + chemicals cost + manufacturing costs = (22.5+14+0.562+0.08+4.86+0.14+8.33+2) Rs
- Total cost = Rs. 52.5 per blade
- So one composite blade costs about 52.5 rupees which is lower as compared with the price of one aluminum blade which costs about 100 to 150Rs.
V.CONCLUSION
For the production of jute fabric reinforced PLA composite, chemical modifications of the fabrics were carried out as, alkalization, acetylation, silane and maleic anhydride treatments. The differently treated fabrics have been characterized. Jute fabrics treated with 5 % alkali followed by 0.5 % Silane treatment shows the highest tensile strength, young’s modulus, specific tensile strength and specific young’s modulus followed by fabrics treated with 5 % alkali only. The untreated jute fabrics show lesser tensile strength and young’s modulus. 5 % Alkali treated+ Acetic acid treated with an MLR of 1:20 shows the poorest tensile strength and 5 % Alkali treated+1 % Maleic anhydride treated fabrics shows the poorest young’s modulus. From the breaking strength-elongation graph it is observed that the elongation at break percentage is found to be much highest in 5 % Alkali+1% Maleic anhydride and 5 % Alkali + Acetic acid treated with an MLR of 1:20 treated fabrics. This is because these two differently treated fabrics exhibits lower tensile strength values and when the fabric is breaking the constituent fibres slips rather than catastrophic failure which of course contribute for the load sharing. Besides the changes in the mechanical properties, Colour changes have also been observed after chemical treatments. The Alkali treated fabric gets darkened, Acetylated and maleic anhydride treated jute fabrics gets brightened/faded because of further purification on the removal of hemicelluloses, lignin and cellulosic components from the fibre after alkali treatment and that of Silane treated jute fabric colour gets into dark golden.
So, composite blades were prepared from jute fabrics treated with Alkali+Silane on a compression molding machine at a temperature of 1900c, with a pressure of 15 bars for 8 minutes followed by air cooling at room temperature. The composite blades were prepared at three different fibre volume fractions; 50:50, 60:40 and 70:30. The samples were tested for tensile-and shear-strength as per ASTM standards and also compared with the existing aluminum blade, Aluminum Alloy 1050 H14.The composites which showed better and comparable mechanical properties have been chosen as the blades. Composite blades with 50:50 fibre volume fractions and having a weight of 75g and a thickness of 2mm was found to be the lightest and showed a tensile strength of 47.1 MPa (referring to Table 3 and fig. 6), which is half of the value of the aluminum alloy and having an ILSS (Inter-laminar shear strength) value of 8.88MPa (referred in Table 4) has been chosen as the composite blades. By performing surface modifications of the jute fabric, the ILSS value has been increased from 6.84MPa to 8.88MPa which is 23% increment on the shear strength.
The composite blades are made with average pitch angles of 10.130 and 120. The performance parameters have been tested and compared with Usha ceiling fans. An air velocity of 836 and 846 ft/min and an air delivery of 251 and 254 CFM were achieved for the composite blades with the pitch angles of 10.130 and 120 respectively (referring to Table 7). From the results it can be seen that the air velocity of composite blades is higher than Usha ceiling fans which has 713 ft/min but due to the reduced surface area of the composite blades i.e .0.3ft2, the air delivery is lower than Usha fans which is 357 CFM having a higher blade surface area of 0.5ft2.
An average power savings of 15.65Watt has been achieved with the use of the composite blades while operating at the maximum speed of 5 (referred in Table 8), which is about 20% power reduction and due to this a minimum of 630 million Rupees or 63 crore rupees per annum can be saved if we use the blades in Delhi only.
The total cost to produce one composite blade is calculated to be 52.5Rs, which is lower as compared with the price of one aluminum blade which costs about 100 to 150 Rs.
Acknowledgement
I avail this opportunity to extend my hearty indebtedness to my guide Prof. R.S Rengasamy, for his valuable guidance, constant encouragement and kind help at different stages for the execution of this dissertation work.
I also express my sincere gratitude to, Dr. Sunder Balakrishnan, General Manager of Natur- tec India pvt. Ltd company for providing me the sample PLA films free of any charges. I am also thankful to Mr. B. Biswal, Mr. VikasKhatkar and Mr. Vijay, Textile protective lab, Textile testing lab and Ph.D. Student respectively, for their help in conducting the experiments.
Special thanks to my friends and other members of the department for being so supportive and helpful in every possible way.
REFERENCES
- DebiprasadGon, Kousik Das, PalashPaul,SubhankarMaity, ‘Jute Composites as Wood Substitute’, International Journal of Textile Science, Volume 1, No.6(2012), pp. 84-93.
- G.M. Arifuzzaman Khan, Hamid Shaikh, M.ShamsulAlam, M.A. Gafur and Saeed M. Al-Zahrani, ‘Effect of chemical treatments on the physical properties of non-woven jute/PLA bio composites’, ‘’Jute/PLA composite, ‘’Bio Resources Volume 10, No. 4 (2015), pp. 7386-7404.
- PriyaSinghal and S.K. Tiwari, ‘Effect of various chemical treatments on the damping property of jute fibre reinforced composite’, International Journal of Advanced Mechanical Engineering, Volume 4, No. 4 (2014), pp. 413-424.
- Mohammad Tahir Zafar, SaurindraNathMaiti, and Anup Kumar Ghosh, ‘Effect of surface treatment of jute fibers on the interfacial adhesion in poly (lactic acid)/jute fiber bio composites’, Fibers and Polymers, Volume 17, No.2, (2016), pp. 266-274.
- B. Ashok S. Naresh, K. Obi Reddy K. Madhukar, J. Cai, L Zhang & A. VaradaRajulu, ‘Tensile and Thermal Properties of Poly (lactic acid)/ Eggshell Powder Composite Films’, International Journal of Polymer Analysis and Characterization, Volume 19, No. 3, (2014),pp.245-255.
- Department of Consumer affairs, Ceiling Fans: Revolving Faster (January 2012), [online], http://consumeraffairs.nic.in/consumer/writereaddata/Ceilingfans.
- K. Hamad1, M. Kaseem1, H.W. Yang1, F. Deri, Y. G. Ko, ‘Properties and medical applications of polylactic acid’, EXPRESS Polymer Letters, Volume 9, No.5, (2015), pp. 435–455.
- TemesgenBerhanu, Pradeep Kumar, Inderdeep Singh, ‘Mechanical Behaviour of Jute Fibre Reinforced Polypropylene Composites’, Science direct.com, (2014), pp. 402-411.
- Tran HuuNam, Shinji Ogihara,HayatoNakatani , Satoshi Kobayashi & Jung Il Song, ‘Mechanical and thermal properties and water absorption of jute fiber reinforced poly(butylene succinate) biodegradable composites’, Advanced Composite Materials Volume 21, No. 3, (2012), pp. 241–258.
- B. C. Mitra, R. K. Basak, M. Sarkar, ‘Studies on jute-reinforced composites, its limitations, and some solutions through chemical modifications of fibers’, JournalofAppliedPolymerScience,Volume67 (1998), pp.1093–1100.
- Leonard Y. Mwaikambo, ‘Tensile properties of alkalised jute fibres’, Bio-resources.com, Volume 4, No. 2, (2009), pp. 566-588.
- Sunil Kumar Ramamoorthy, Mikael Skrifvars, MarjaRissanen, ‘Effect of alkali and silane surface treatments on regenerated cellulose fibre type (Lyocell) intended for composites’, Springer Science & Business Media, Volume 22, (2015), pp. 637-654.
- X. Y. Liu, G. C. Dai, ‘Surface modification and micromechanical properties of jute fiber mat reinforced polypropylene composites’, EXPRESS Polymer Letters Volume 1, No.5, (2007), pp. 299–307.
- A.K. Bledzki1, A. A. Mamun1, M. Lucka-Gabor1, V. S. Gutowski, ‘The effects of acetylation on properties of flax fibre and its polypropylene composites’, EXPRESS Polymer Letters Volume 2, No.6, (2008),pp.413–422.
- Giuseppe Cristaldi, Alberta Latteri, Giuseppe Recca and GianlucaCicala, ‘Composites Based on Natural Fibre Fabrics’, University of Catania – Department of Physical and Chemical Methodologies for Engineering, Catania Italy.
- Amazing Comfortson S, AhamedFaiyaz R, Mohamed Yousuf Afzal M R, MohapilashaNishath M, ‘Glass Fibre Reinforced Polymer Composite Ceiling Fan Blade’, International Journal of Emerging Technology and Advanced Engineering, Volume 4, Issue 11, (2014) pp. 174-179.
The article is authored by NewaySeboka, who is from the Ethiopian Textile Industry Development Institute, Addis Ababa, Ethiopia, and Rengasamy RS, who is from the Department of Textile Technology, Indian Institute of Technology, New Delhi 110016, India.
Mentored by Texcoms Textile Solutions.