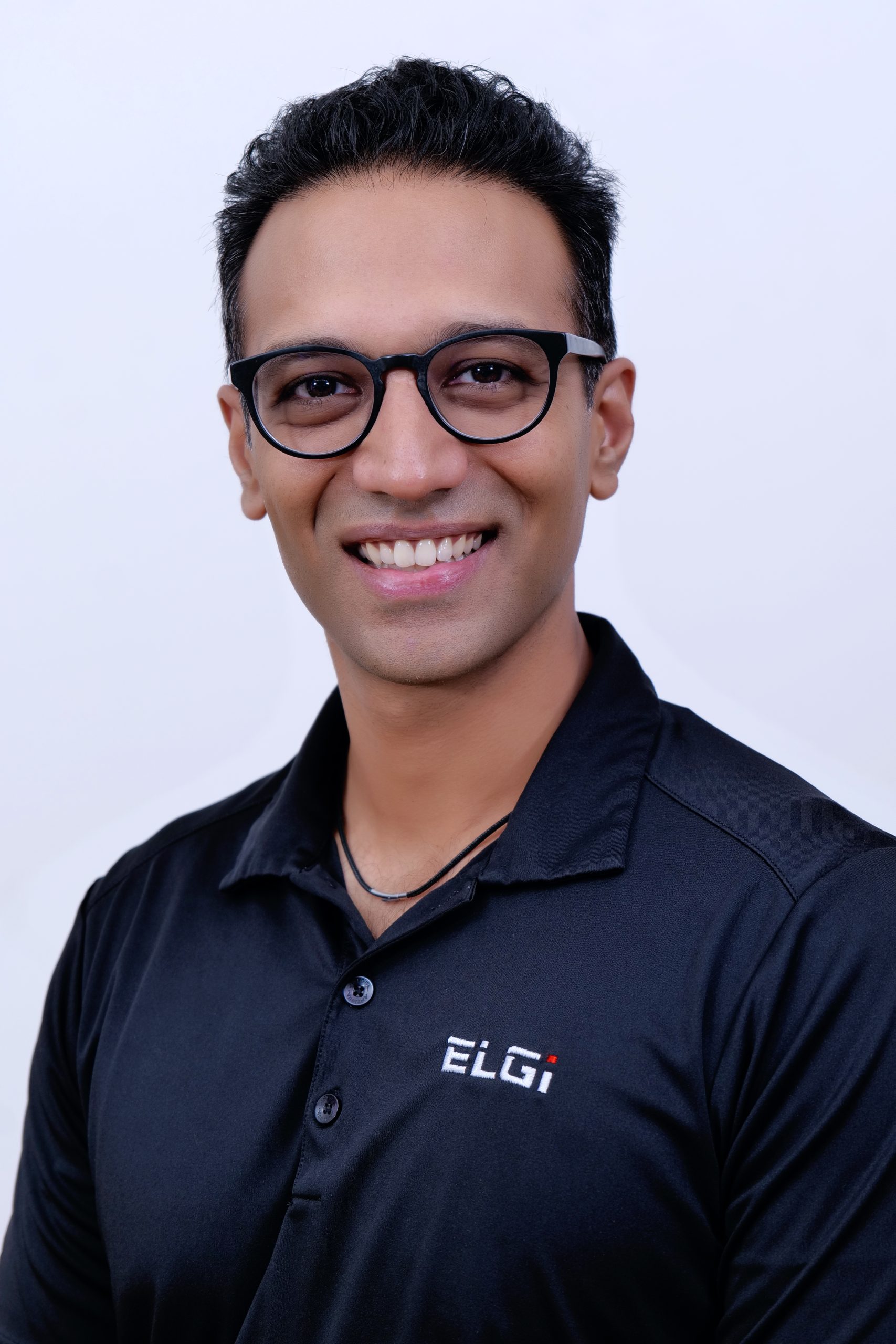
Anvar Jay Varadaraj: We’ve heavily invested in R&D to boost energy performance.
With 65 years of experience in manufacturing air compressors, ELGi is a global leader in providing sustainable compressed air solutions. ELGi designs and manufactures an extensive range of innovative and technologically advanced compressed air solutions for a variety of industry applications. Anvar Jay Varadaraj, COO of Elgi Equipments, discusses key factors to consider when purchasing a compressor, highlights the importance of air audits, and shares the company’s future plans in this interview with Divya Shetty.
What key factors should a textile factory consider when selecting a compressor, and how can it ensure the chosen model aligns with its specific operational requirements?
Textile factories must approach compressor selection with a deep understanding of their operational requirements to ensure efficiency and cost-effectiveness. The first step is to evaluate the actual air demand across various processes such as spinning, weaving, dyeing, and equipment cleaning. Overestimating needs, often due to unseen losses from leaks, rust, or poorly designed piping, can lead to the selection of oversized compressors that waste energy and increase costs. By accurately assessing consumption and minimizing inefficiencies, manufacturers can determine the appropriate capacity needed. Equally important is the design of the piping system; following best practices recommended by compressor manufacturers helps maintain stable pressure and volume delivery throughout the plant.
Understanding how compressed air is used is also critical. In many cases, textile mills rely heavily on air for cleaning, an energy-intensive activity that could be managed more efficiently with alternative methods or smaller, dedicated compressors. Additionally, factories should avoid setting unnecessarily high-pressure levels, as most downstream equipment includes built-in safety buffers. Even a small reduction in pressure, by just one bar, can yield energy savings of 10 to 15 percent. Ultimately, before investing in a new or upgraded compressor, textile manufacturers should holistically review their air system design, usage patterns, and maintenance practices. Doing so often reveals that a smaller, more efficient compressor can meet their needs while significantly reducing energy consumption and operational costs.
How do you evaluate the current landscape of the air engineering industry in India, and what growth opportunities do you foresee, particularly in textiles?
Textile customers prioritize energy efficiency, reliability, air quality, and, naturally, price, especially amid rising competition and lower-cost imports that feature technologies such as permanent magnet motors and variable frequency drives (VFDs). To stay ahead, we’ve heavily invested in R&D to boost energy performance. Our new ELGi EG Super Premium compressors feature newly configured two-stage airends that deliver up to 15 per cent savings in specific power consumption. Combined with low-speed operation and reduced load at each stage, this configuration significantly enhances the longevity of components and the overall reliability of the system.
We’ve also introduced Stabilisor technology – a cost-effective alternative to VFDs. While VFDs adjust motor speed based on demand, reducing energy waste, many customers find them too expensive. Stabilisor offers similar benefits mechanically, reducing unloading cycles and cutting energy use without the complexity or high cost. This not only improves efficiency but also lowers mechanical wear, extending component life and enabling us to offer longer warranties. It enhances operational reliability—crucial, since downtime can erase any upfront savings from a cheaper, less reliable machine. Ultimately, our goal is to reduce total cost of ownership by optimising energy use, lowering maintenance needs, and ensuring long-term performance.
Why are air audit programmes essential in manufacturing operations?
Air audit programmes play a critical role in maintaining the efficiency, reliability, and cost-effectiveness of compressed air systems in manufacturing operations—especially for large factories or those without deep in-house expertise in air management. These audits, typically conducted every 18 to 24 months depending on operational complexity, are essential because compressed air systems are not static; they evolve with use. Over time, the continuous flow of air causes vibrations, shifts components, and leads to the development of leaks or pressure drops. Simultaneously, usage patterns often change as production needs shift, making routine evaluations imperative.
A comprehensive air audit identifies and addresses these performance drifts. It assesses whether the compressor is functioning within design specifications, verifies if maintenance schedules are being followed, and checks for operational issues like elevated temperatures or inconsistent output. More importantly, it evaluates the entire air network—tracing leaks, detecting corrosion, and flagging inefficient practices such as overuse of air for cleaning. It also inspects air quality to ensure there are no harmful levels of oil or moisture that could damage downstream equipment or affect product quality.
Beyond diagnostics, a well-executed audit often reveals actionable insights that can lead to measurable savings, some of which may require no investment at all. In other cases, minor upgrades recommended post-audit can deliver significant long-term gains. Moreover, audit partners often work closely with internal maintenance teams to establish ongoing best practices, ensuring that the compressed air system continues to operate efficiently and sustainably. In short, air audit programmes are not just a technical check-up; they are a strategic tool for enhancing operational performance and reducing energy waste.
What are the latest innovations in compressors and ELGi’s contributions?
ELGi continues to lead innovation in compressed air technology with a focus on enhancing efficiency, reliability, and adaptability—especially for sectors like textiles where energy consumption directly impacts profitability.
One of our key advancements is the launch of the EG Super Premium compressors, a new addition to the renowned EG Series portfolio of oil-lubricated screw air compressors. These machines mark a significant step forward in compressed air technology, delivering energy efficiency improvements of up to 15 per cent*, along with best-in-class warranty, performance, and low life cycle costs in the 75–160 kW range. The EG Super Premium compressors are now commercially available, enabling customers to achieve enhanced performance while reducing energy consumption.
To drive further energy savings, ELGi has adopted permanent magnet motors as a standard feature. When combined with Variable Frequency Drives (VFDs), these motors significantly lower unload power consumption. Recognising that not all operations can accommodate the complexity of VFDs, we’ve also introduced Stabilisor technology—a cost-effective, simplified alternative that delivers comparable energy efficiency benefits. Stabilisor is currently undergoing field trials, and select textile manufacturers are being onboarded as early adopters.
Another often overlooked but critical system component is the air dryer. Poor moisture management can degrade system performance, so we’re engineering modular dryers that can be either integrated within the compressor or used as standalone units. These dryers are competitively priced, deliver high performance, and are a testament to our vertically integrated approach—ensuring consistent quality across all system elements.
In line with the shift towards smart manufacturing, ELGi has launched Air~Alert, a real-time monitoring system that tracks key operating parameters such as air consumption, pressure levels, and output efficiency. This platform provides maintenance teams with actionable insights to optimize energy use and improve system uptime.
Together, these innovations reflect ELGi’s commitment to addressing the evolving demands of textile manufacturing, delivering solutions that not only improve performance but also drive long-term operational savings.
What are ELGi’s future plans regarding product innovation and market expansion?
In the AB Series, that we launched 5 years ago, water serves as the primary medium for cooling, sealing, and lubrication within the compression chamber. ELGi’s design circulates water in a closed loop, eliminating the need for external water treatment systems. By maintaining water within a sealed circuit, the system ensures compliance with IS:10500-2012 standards. The absence of oil and the use of a closed water circuit minimize the risk of contamination, making the AB Series ideal for industries requiring high air purity, such as textiles. Though not yet as efficient as oil-lubricated machines, it’s improving steadily, and many customers are already benefiting from this technology. With continued R&D, we expect wider adoption in textiles.
Technology accounts for just 50–60 per cent of an effective compressed air solution. The rest depends on exceptional aftermarket support—and that’s where we differentiate ourselves. At ELGi, our service philosophy is built on 100 per cent trust. We don’t let warranties become a point of friction; instead, we prioritize fast, reliable, and dispute-free support. When we commit to restoring compressed air within hours, we deliver. Our engineers are trained not just to respond quickly, but to resolve issues right the first time.
Choosing a compressor may take a few days, but interacting with the brand is a decade-long journey. That’s why we’re constantly looking ahead anticipating our customers’ evolving needs and adapting our service model accordingly. As the industry shifts more maintenance responsibility from customers to OEMs, we’re proactively preparing by asking two key questions: What do customers need today? And what will they need five years from now? Our goal is to align with those answers, delivering not just compressors, but peace of mind throughout the lifecycle.
* When compared with single stage compressors