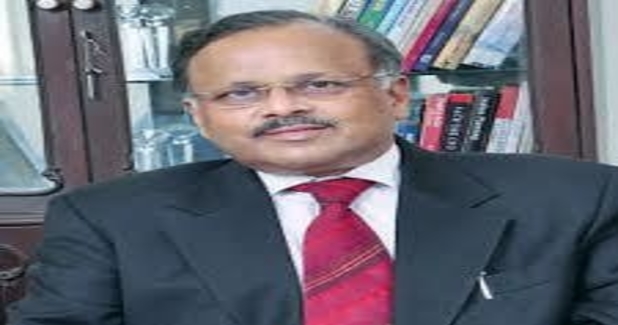
Staubli’s innovations for advanced tech fabrics
Stäubli has been one of the world’s leading manufacturers of high-speed textile machinery for more than 125 years. After decades of experience as a supplier of shedding solutions for weaving machines, weaving preparation systems, and complete carpet weaving systems in the traditional textile industry, Stäubli continued its efforts in research and development to extend its product range.
Stäubli has been one of the world’s leading manufacturers of high-speed textile machinery for more than 125 years. After decades of experience as a supplier of shedding solutions for weaving machines, weaving preparation systems, and complete carpet weaving systems in the traditional textile industry, Stäubli continued its efforts in research and development to extend its product range. For several years Stäubli has offered textile machinery dedicated to the production of technical textiles, such as:
Magma T12 warp tying machine
The MAGMA T12 ties monofilaments, coarse multi-filaments, PP ribbons, bast fibres, coarse staple fibres, and many other fibre types. It has been developed for universal application ranging from coarse technical yarns to the medium yarn-count range. Its rigid design includes an optical double-end detection system TF weaving system
R&D project managers in the automotive, medical, aeronautic or any other industry sector, searching for light weight component solutions will be amazed. the Stäubli TF system offers virtually unlimited weaving possibilities, whether for flat, spacer, or complex multi-layer fabrics and 3D fabrics. Specific requirements in terms of stiffness, impregnation capacity, drapability, or fail-safe-behaviour, etc, can be fulfilled. Featuring the latest shedding machines in combination with the double-rapier weft insertion system and a special slaying motion the TF weaving system allows high-volume production of up to very thick and/or dense fabrics and efficient processing of a wide variety of technical and highly sensitive yarns, such as glass fibre, carbon, Kevlar, or similar.
For the automotive industry, Stäubli is today’s leading supplier in shedding solutions for airbag weaving, traditional airbags woven on frame weaving machines, and OPW (one-piece-woven) airbags produced on modern Jacquard weaving machines. Airbag fabrics demand important stroke forces during weaving. The solid construction of the latest generation S3000/S3200 electronic rotary dobbies provides the basis in frame weaving for supporting these forces while running reliably at high speeds day in and day out, offering important longevity.
Frame weaving pre-requisites such as perfectly prepared warps gain in importance when it comes to deliver the automotive industry with its zero-error specifications. The weaver has to produce more 1st class fabric, while staying competitive. Using the SAFIR automatic drawing-in installations, equipped with active warp control features such as optical recognition of double ends and color/yarn type repeat management, allows the weavers to meet these strict requirements. These very efficient machines allow the distribution of each warp end according to the repeat in the drop wires, healds and reed in one cycle. Many weavers worldwide already rely on SAFIR drawing-in machines for continued quality weaving process. The machines handle as well on glass applications and are showing their efficiency in filament mills.
For the production of afore-mentioned OPW airbags, Stäubli provides the LX Jacquard machine Series. This world renowned machines feature perfectly balanced cinematics, a coaxial drive shaft, and an optimized internal airflow as well as optimum sized chassis. These features ensure clean interiors, controlled temperature in the machinery housing, the support of beams and bearings and make the Series handle great payloads and precise operating at highest production speeds. For a perfect link between machine and harness the MX module, centrepiece of the Jacquard machine plays its major role.
MX modules are built of latest optimum combined composite materials for long-lasting efficiency during thousands of up-and down movements while ensuring the reliable yarn selection. All these factors are very decisive in terms of economic production. Weaver and airbag supplier have to be certain about the high quality of the product they deliver, as the automotive industry enforces complicated, cost intensive and strict verification and validation processes for its components, and especially for components that protect human lives, such as airbags.
The latest models in the LX Series, the LXL and LXXL are specifically developed for large-sized designs and can be equipped in a format range of 6,144 to 25,600 hooks. By combining two LXXL machines, formats up to 51,200 can be achieved.
Whatever the weaving width or format size in airbag production, Stäubli weaving preparation and shedding solutions bring the advantages of an experienced solution provider to the weaver and airbag producer.
Binding technology
With its ALPHA 500 Series carpet weaving systems, Stäubli provides a product range for any kind of rug or wall-to-wall carpet. Weavers can count on the ALPHA 500 LEANTEC model for weaving superior high-quality synthetic grass, with a weaving width of up to 5.3 meters. The Stäubli binding technology allows the optimum orientation of the piles for a wide public, ranging from major league sports facilities suppliers, to public services and garden centres.
Industrials that rely on Stäubli technical textile solutions can create future applications with passion, and can rely on efficient machinery and solutions to take the lead in the technical textile business.