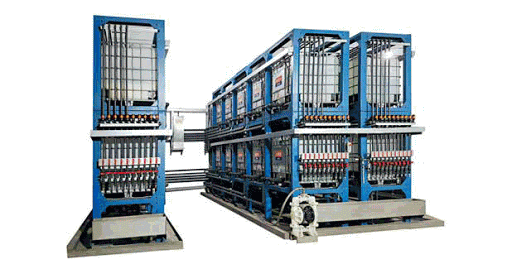
Smart dyeing & finishing, CHTC FONG’s innovations
CHTC Fong’s has been committed to the development and manufacturing of dyeing and finishing equipment for more than 50 years. In the past decades, CHTC Fong’s devoted to the development of energy-saving and emission reduction machines and now it becomes the basic conditions for dyeing factories.
CHTC Fong’s has been committed to the development and manufacturing of dyeing and finishing equipment for more than 50 years. In the past decades, CHTC Fong’s devoted to the development of energy-saving and emission reduction machines and now it becomes the basic conditions for dyeing factories. Today, we live in a digital era, though in the traditional textile industry, CHTC Fong’s has been with the times. Together with its well-known brands: Fong’s, Monforts Fong’s, Xorella, Then, Goller, FWT and Monforts, CHTC Fong’s dedicated in the development of Smart Dyeing & Finishing and join with the customers to build the intelligent dyeing factory.
The CHTC Fong’s Group presented the “one-stop†sustainable solution in dyeing and finishing range of “pre-treatment, dyeing, post-treatment and waste water treatment†at Shanghaitex 2019 in W1, A10 and yarn conditioning and heat setting in E1, A60, Shanghai New International Expo Center, Shanghai, China from November 25-28. CHTC Fong’s will exhibit a full line of the most advanced and innovative products and technology.
Fong’s TECWIN
Fong’s TECWIN is designed to satisfy the ever-changing market demands. The reliability and versatility of the machine are improved.
TECWIN is equipped with several patented designs:
Combined air and front spray nozzle
- Standard Feature: Increase the degree of dye liquor interchange before passing through the main nozzle.
- Optional Feature: Optional blower is equipped. High pressure aerodynamic flow in spray nozzle is provided to resolve the special fabrics that demand high quality.
Automatic adjustable nozzle
- Adjustment of nozzle setting is automatically done by means of motor drive system, and hence manual changing of nozzle is not required.
Liquor Dispersion Storage Chamber
- This is a uniquely design chamber for providing a better liquor dispersion effect.
Upper and Lower Overflow
- Lower Overflow: Maintaining pump operation with low water level to prevent disturbance caused by rinsing at a high water level.
- Upper Overflow: This is adopted for conventional overflow rinsing function.
FONG’s ALC
The ALC automatic liquid chemical weighing and dispensing system realises unmanned dispensing according to the instructions fed from the Enterprise Resource Planning (ERP) system using advanced computer control technology. By means of precision mass flow-meter and metering pump, the liquid chemicals are accurately and precisely delivered and weighed from storage tanks, and with the application of valves and pipe network connections, the chemicals are accurately and rapidly distributed to the designated dyeing machine in the most effective way. With the efficient cleaning function after each delivery, not only is the operation efficiency of the dyeing plant improved but also it avoids human errors. Thus, dyeing quality is guaranteed.
GOLLER DYEPADDER ECONOMICA
TheNew GOLLER DYEPADDER ECONOMICA Nip-in-Trough with Double Impregnation Mechanism provides even dyeing for knitted fabric without crease mark and distortion incurred. The newly-designed double impregnation mechanism provides further improvement on the impregnation effectiveness in combination of a lower running tension. As the ECONOMICA guarantees reproducibility and handling in the highest standard, a smooth and clear fabric surface can be expected after dyeing.
The deflection-controlled rollers of ECONOMICA are working according to the principle of the swimming rollers, irrespective of the overall pressure of the padder- the deflection of the squeezing rollers is always consistent with the set values to ensure an even dyeing over the fabric width. On top of the deflection-controlled rollers, the large diameter guide rollers ensure a smooth knitted fabric transport with minimal tension incurred, which is beneficial to the dyeing process as a whole. The double impregnation mechanism consists of a trough with a padder inside and with the minimum level of working liquor required. This mechanism provides sufficient impregnation and low-tension running condition for knitted fabric during the dyeing process. Furthermore, Thermplates keep the temperature of the dyebath as per the set value throughout the dyeing process – no matter it’s cool or hot.
Monforts QUALITEX
It’s well-known that the astonishing success of China’s economy over the past decade has sent wages soaring and made it difficult for the country’s textile manufacturers to find and retain trained machine operators, while operating in a highly competitive market where optimised production and full resource efficiency are of paramount importance.
In direct response to this situation, A. MonfortsTextilmaschinen GmbH & Co. KG has introduced a range of new Industry 4.0 technologies aimed at simplifying machine operation while providing easy access to all data and instant or remote assistance.
Monforts specialists will be at stand A10 in Hall W and look forward to discussing the company’s latest developments in this area with valued Chinese customers.
They include the latest Qualitex full touch panel control system, with its digital twinning capability and Smart Check and Smart Support apps, reinforced by the comprehensive Monforts Smart Sensor machine monitoring programme.
Monforts NEW CYD
Monforts will also be providing full details of its new CYD continuous yarn dyeing system which is based on the Econtrol technique – the most effective and established dyeing process for denim fabrics that is now being applied for yarn dyeing. Econtrol is a pad-dry process employed in Monforts continuous dyeing in which the reactive dyestuff is fixed to the cellulose fibres during drying.
The fixing medium is a controlled by a steam/air mixture within the MonfortsThermex unit. With sulphur and reactive dyes in particular, the improvement in both quality and fixation is considerable, and with significant savings in energy and time due to the combined bleaching and padder fixation.
The CYD system also integrates new functions and processes into the weaving preparation processes – spinning, direct beaming, warping and assembly beaming, followed by sizing and dyeing – in order to increase quality, flexibility, economic viability and productivity.
Monforts Fong’s
Innovative Technology Center is a new research and development center for exploring our innovation of the textile product application, which aims at improving the performance of equipment which is used for finishing processing in technical textiles. Meanwhile, we provide the platform for machine demonstration and bulk trial of coating fabric samples for our customers. In ITC, there are laboratory areas, machine showing area, office area, storage room, and meeting room. Up to now, we have a coating line which is consisted of Montex 6500 stenter and MonfortsTexcoat coating machine, and a Monfongs StrahmHiPer Shrink Astra dryer.
The coating line is mainly applied to textile finishing processes in technical textiles aspect such as mobile textiles, protective textiles and also non-woven fabrics. The infeed unit has options of either plaiter or batch unwinding. The fabric tension in the warpwise direction can be optimized by the two-loop float compensator in the cloth path. The centering device can ensure the fabric always feeding in the center position. The even pressure roller of “Matex 6000â€â€™s padder is allowed to be adjusted for optimal padding effect. There are various texture and different hardness of the roller wrappings which are available for padding of different fabric processing demands. The different capacity of the liquid trough is designed to have different length of immersion path. A double-walled execution for indirect heating or cooling with temperature control system is also available. Besides, the immersion roller in the liquid trough can be driven actively by the motor.
Monfongs STRAHMHiPer Shrink Astra
MongfongsStrahm is a Shrinkage & Relaxation Dryer for open width and tubular knit fabrics. Its unique design focuses on the highest drying capacity, low residual shrinkage and a soft hand feel by mechanical action inside the chambers. The uncompromising design also features an incorporated energy recovery system (EnRec 1&2) that saves energy consumption, particularly, when it is compared with standard common dryers in the market. The relaxation dryer mainly includes infeed section, overfeed area, tumbling zone, and delivery section. It can also have an option to add the double padder configuration in the infeed section in order to give a more even pick-up to the fabrics.
The width and the length of fabrics in the overfeed zone can be restored to its original state by the overfeeding and the stretching on the pin chain. Fabrics under low tension subsequently enter the wave maker zone of chambers.
XORELLA XO-Series
XORELLAXO-Series energy saving vacuum conditioning and heat setting machines has been well used in improving the qualityof yarn and also heat setting of garment. The Xorella XO-Steaming treatment could evenpenetrate the textile products for humidification; twist setting, preshrinking the synthetic filament, anti-static, colour fixation of digital printed fabric and heat setting of garment. The latest saturated steam generating system could reduce 30 per cent of connected power loading and save between 15 per cent to 25 per cent energy consumption.
In order to satisfy the requirement of different users, Xorella provides both round and cubical machine and also variety of loading and door opening systems for customer selection. Nowadays, XO-Series machines were used in more than 50 countries in the world.
Fong’s Water Recycling System
With global service for the dyeing and finishing industry, CHTC Fong’s Group has focused on its principal business in design, research and manufacture of innovative and energy saving dyeing and finishing machines to help a sustainable balance between the industry development and environment protection. In recent years, Fong’s has researched and developed the wastewater treatment technology, to achieve fully automatic operation water recycling system with dual-membrane processes, providing one-stop sustainable solutions of dyeing wastewater treatment especially for the dyeing and finishing industries.
Fong’s Water Recycling System which can reuse any kind of qualified discharge water by using the most advanced and reliable dual-membrane processes (ultrafiltration system combined with reverse osmosis membrane system). The recycled water can be directly used for all dyeing processes after most of the mineral salts, calcium, magnesium hardness; Chroma, turbidity and COD composition are effectively removed from the waste water. The quality indicator of recycling water is superior to the normal tap water.