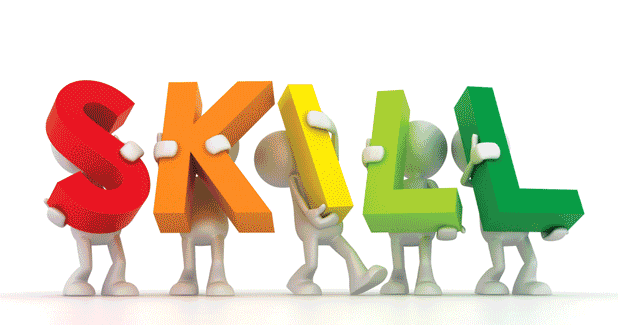
Skilling on track!
Indian textile industry cannot afford to ignore the implications of ‘skilling’ the labour force, for to sharpen the competitive edge in producing and exporting quality textile goods, skilled labour is a must. The ITJ cover story traces the ‘skilling’ moves in the textile industry.
Indian textile industry cannot afford to ignore the implications of ‘skilling’ the labour force, for to sharpen the competitive edge in producing and exporting quality textile goods, skilled labour is a must. The ITJ cover story traces the ‘skilling’ moves in the textile industry.
The Government’s ‘skilling’ target of 400 million by 2022 may look a far cry at the present context, but with the announcement of the Rs 1,300-crore Scheme for Capacity Building in Textile Sector (SCBTS), the Modi Government has reiterated its keen desire and serious intent to achieve the target, at least in the textile sector.
In the textile industry, Dr J V Rao, Chief Executive Officer of Textile Sector Skill Council (TSC), is very confident: “TSC, since its inception in August 2014, has strived to create a robust ecosystem for skilling in the textile mill and handloom sectors. TSC is governed by 14 Textile Mill Associations and four Export Promotion Councils and has three technical committees to decide various aspects for ensuring quality skilling in the sector. Till date, TSC has developed 88 Qualification Packs listing the competencies required for 80 per cent of job roles in the textile mill and handloom sectors, which are declared as National Standards by the National Skill Development Council.â€
Skilling is not just the Government’s responsibility alone. Many textile companies, which were using unskilled labour in crucial departments, have started training workforce or recruiting skilled labour. Training is a part and parcel of the working at companies like ELGi Equipment in Coimbatore, which has been spending huge amounts of money and time on skilling the labour force.
Only about 4.69 per cent of India’s workforce is formally skilled, as against 52 per cent in the US, 68 per cent in the UK, 75 per cent in Germany, 80 per cent in Japan and 96 per cent in South Korea. In China, skilled workers account for 24 per cent of the workforce.
About 64 per cent of India’s population is expected to be in the working age group of 15-59 years by 2026, according to Ernst and Young, a professional services consultancy. India is expected to have the largest workforce in the world by 2025, with an estimated two billion English-speaking people by the end of 2020. By the same year, the world is expected to face a shortage of 56.5 million skilled workers, while India is projected to have a surplus of 47 million, Indian government claims.
Speaking on the current status of skilled labour in textile industry, Dr JV Rao says, “There is a huge shortage of skilled labour in Indian textile industry. A big issue which employers are facing today, is absenteeism due to the social system of India. There isn’t an absolute shortage of labour, the problem is absenteeism and churning. India is a country with multiple festivals, hence local workers take leave without notice on and off – making production planning a challenge. The model of migrate residential labour faces the problem of they taking two to three months holiday in a year for reasons like Holi, harvesting, marriages, deaths, Diwali, Chat puja and so on. Further they get benefits under MNREGA for 100 days, which makes their stays at home comfortable.â€
Dr JV Rao thinks that the textile industry (except the spinning sector) is fragmented in nature on account of policy restrictions relating to labour laws and the fiscal advantages enjoyed by the small-scale units. He adds, “The textile units mostly engage in job work (sub-contracting) and hence a large portion of the employment is in the production activities. Also, the small units do not have explicit demarcation of functions for sourcing, sales, etc. Though all segments suffer severe shortage of skilled labour, spinning, being mostly organized sector is slightly better than the others.â€
However, in Dr Darlie Koshy’s (DG and CEO of ATDC) perspective, it seems that entry-level short-term training has been overdone in the country, during the period 2012-2017 with other schemes launched by different apex agencies/state skill missions, etc. flooding the crowded market with varying quality of delivery with often “bad coins†driving out or overwhelming the “good coins†and the subterfuge activities of some dubious players (gold-diggers so to say) vitiating the market!
“Weaving and garmenting subsectors would continue to hire at a rate of 8 per cent to 8.5 per cent year-on-year against a historical growth rate of 9 per cent to 9.5 per cent to reach 40.7 million in 2022, says Dr Koshy. A spokesperson from T.T. Limited said, “Labour wages have risen significantly over the last few years and there are seasonal shortages in labour on a regular basis. Further skill India efforts have lead to skilled labour flowing into the industry.â€
Speaking on the SCBTS, the spokesperson from T.T. Limited said, “Very positive and timely step – unfortunately the organised spinning and weaving industry have not been included which are best positioned to take advantage of such skilling schemes. The challenge is going to be see that the benefit can reach the unorganised industry effectively.†He added, “Relaxation have been made by certain States on women employment, plus under Apparel Package last year fixed term employment was allowed which are much needed steps. However the Government needs to be able to complete the proposed labour reforms by consolidating laws and making it easier for small companies to comply with various provisions.â€
According to Avinash Mayekar, MD and CEO, Suvin Advisors: “There is a great gap between the industry needs and training offered in such courses. The training courses completely lack the knowledge on advances that have taken place over the years, the courses are not just version behind the actual advances but are decades behind thereby making such courses loose its effectiveness for the industry. Focusing on textile such courses do not provide the knowledge or skills needed for the new machinery that are currently operational. If we graph the technological advancement and training provided in India, we will observe that we are currently on two different globes. Any advances in electrical, mechanical or electronics are immediately mapped into textile machinery for betterment. So, our day-by-day machinery are becoming smarter but the people operating them are remaining dumber.â€
The government has addressed this key issue of lack or gap in training the workforce and has launched subsidy and initiative like National skill development mission to envisage India as world’s human resource capital. The National Skill Development Mission with a mandate to train 300 million Indians by 2022.
Says Mayekar, “We all know that India is having a huge advantage of manpower and is also being promoted to contain skilled labours. The part of skilled labour though a questionable asset today is however true in broader sense because of the quality and talents that people possesses. The Indian labours for years are capable to easily adopt and flourish in any situation when provided the right training. So India is having labour that is capable of learning and adapting to the technologies, provided necessary training is given to them thus converting the labours into skilled labours.†The Indian textile industry needs to evolve and take huge steps as far as providing the training to their workforce is concerned. The methodology has to be changed, it must focus on providing actual training during production peek time rather than demo sessions on demo machinery. They need to train the people on technology advances and involve technology providers for better understanding. The best option will be to have trainers who are assigned the only job of getting trained on technology advances and then providing this training to the workforce as and when new workforce joins the organisation. As we are aware that every year the manpower is getting replaced around 20 to 25 per cent of them so a trainer will ensure the knowledge flow in organisation even if the entire operation staff changes.
Dr JV Rao concludes: “The sector is projected to provide employment to at least an additional 20 million people from the current 45 million to 65 million by 2023. TSC targets to establish ecosystem for over 200 job roles to address the skill gap in the textile mill and handloom sector. It also aspires to run at least one Centre of Excellence (CoE) for Training of Trainers in each of the four regions of the country. These CoEs may also work as common facility centres and provide knowledge support to the local industry and handloom Weavers and help the explore new designs and wider markets.â€