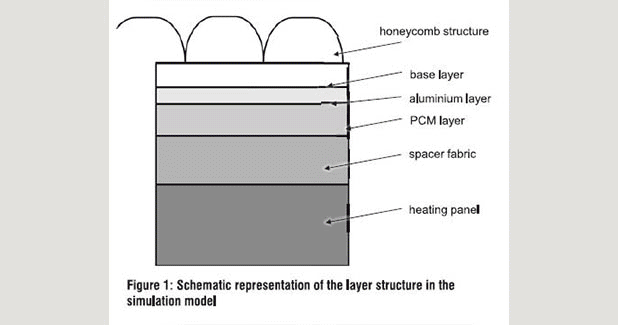
Simulation of heat transfer of heat protection textiles
In a heat-exposed working environment there is a risk of scalding and heat stroke for the employee. The heat protection textile developed as part of the HEATex research project is used here as underwear.
In a heat-exposed working environment there is a risk of scalding and heat stroke for the employee. The heat protection textile developed as part of the HEATex research project is used here as underwear. In addition to experimental tests, the heat transport properties of the multi-layer heat protection textile are simulated under the influence of contact heat. The simulation allows a qualitative pre-estimation of the heat protection effect of different layer structures. Thus, costs and effort of future comparisons can be reduced. The results of the simulation model show similarities to the experimental test results, say Kevin Krause, Paul Grünefeld, Lena Barth, Lukas Lechthaler, Christoph Peiner and Thomas Gries from the Institut für Textiltechnik of RWTH Aachen University.
The aim of the ZIM project HEATex (promotion number: ZF4018754CJ6) is the development of a heat protection textile with 3D spacer fabric and phase changing material. The textile is used as underwear for workers in heat-exposed environments. In Germany, around 10 per cent of the workers are exposed to high temperatures at their workplaces (metal, glass, ceramics and steel production as well as forges, foundries, fire brigades, …)[1]. The heat protection textile prevents direct contact between external protective clothing and skin and improves the absorption and transport of the body’s own moisture. The solid phase changing material in the heat protection textile absorbs large amounts of energy during the phase change. An additional aluminium layer serves as a radiation reflector. In order to investigate the heat protection effect of textiles in an abstract representation of reality, a simulation model is being developed in addition to experimental experiments. Thus, the suitability of different layer structures and textile configurations can be tested virtually in a minimum of time. The simulation model was created with the simulation software Abaqus/CAE from DassaultSystèmes SE, Paris (France).
Modelling of the simulation model / solution approach
Within the simulation, the real environment of the heat protection textile is simplified by suitable assumptions. The heat transport at the heat protection textile by convection is negligible, since only a small air movement takes place underneath the tightly fitting upper protective clothing. The upper protective clothing reduces the incoming radiant heat so that it is neglected assuming an ideal protective clothing. The radiation contributions of the heat protection underwear are neglected due to the low radiation intensity.
In a next step, the subsystem of the heat protection textile is simplified with the help of suitable assumptions. The textile layers are assumed to be solid materials with isotropic material properties. Air inclusions within textile layers and the use of different materials in one layer are considered by adjusting the material parameters. Thus, material parameters averaged over individual textile layers are used. The material parameters mass density, thermal conductivity and specific heat capacity are required to model the heat transfer of the textile model. The energy absorption of the phase changing material is considered by the parameter of the specific melting enthalpy ?h = 198 . The specific heat capacity of the latent heat accumulator is c = 2,4 . The next step involves assembling the sub models to form an overall model. Finite elements are used here. The sub models are linked by a loss-free thermal energy transfer.
Evaluation of the simulation
With 79.2 °C (see Figure 2), the final temperature of the simulation is slightly higher than comparable final temperatures recorded in real tests on heat protection textiles with contact heat and without pressure.The maximum value of the temperature in the simulation corresponds to a temperature of “T†_â€max†“=72 °C†. One reason for this is that outgoing heat flows are not modelled. In reality, textiles are surrounded by air. A circulation of the air at the textile, which is caused by temperature differences, leads to a cooling of the textile by natural convection. This effect is intensified by forced convection in the form of air movements in the test environment.
The heat transfer mechanisms in the simulation model are mapped on the simulation scale of textile layer planes. This means that heat transfer mechanisms at fibre scale with air inclusions are not mapped due to the fineness of the model. The characteristic element length of a finite element of the simulation is “l†_â€element†“ = 0,884 mm†and thus represents a compromise between a sufficiently precise resolution of the temperature distribution and a reasonable calculation time of the simulation.
In the simulation, the honeycomb structure of the real textiles is simulated. The temperatures of the honeycomb structures hardly differ from the temperature of the adjacent layer, although both layers differ in their material parameters. The insulation effect of the partially air-filled honeycomb structures is not shown in the simulation. In addition, the effect of outgoing heat flows, which are intensified by an enlarged surface, is not considered. A certain inaccuracy in the material parameters leads to the fact that the final temperatures from simulation and tests lie despite some simplifications in the same order of magnitude.
Despite the simple simulation structure, a comparison with experimental data is possible. The comparison shows that the physical phenomena of heat transfer can be represented in the simulation. With the help of the simulation, textiles can be efficiently and quickly pre-estimated in a first step. In addition, the component-by-component structure of the simulation enables rapid changes in material parameters or a change in the layer structure, which can be used to optimise heat-protective clothing. The advantage of simulation over the experimental setup is that the calculated data are not subject to the same sources of error. Thus, the environmental parameters of the simulation can be set as constant. Tests are subject to natural fluctuations and irregularities. A noise of the measured values can be excluded in the simulation. The error sources of the simulation lie in the modelling of the textile layer structure.
When using the simulation, attention must be paid to the accuracy of the material parameters used. Further physical effects, such as radiation influences, can be integrated into the simulation if the material parameters are known. It is recommended to minimize the required computing power by simplifying and exploiting symmetries in the geometry. The simulation model developed as part of the HEATex research project is used at the Institute of Textile Technology at RWTH Aachen University with the material parameters of heat protection textiles from STS Textiles GmbH, Grünbach.
References
- [1] TÜV Rheinland
- Heat check at the workplace H.E.A.T Analysis – Objective climate measurement according to DIN EN
- 27243 and assessment of heat stress at the workplace
- URL: http://www.presseportal.de/pm/31385/2279470, accessed 24.11.2016