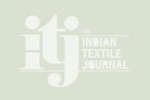
Savio exhibits automatic winder POLAR/E PREMIUM
Savio introduces for the first time in an international exhibition the new winder POLAR/E PREMIUM, after its road show in China and in Turkey in late 2013.
Savio introduces for the first time in an international exhibition the new winder POLAR/E PREMIUM, after its road show in China and in Turkey in late 2013. This new fully automatic machine is addressed to any spinning mills no matter the type of ring spinning frames, with or without automatic doffing. The trend to the automation is widely spreading around, also in those textile environments where generally the up-stream process is still managed in a manual way, and consequently the spinning bobbins would not be specifically favourable for an automatic handling.
This new Savio winder represents the "universal solutionö and the perfect reply to these additional needs.
This is where the new POLAR/E PREMIUM fits in:
- Total machinery layout freedom.
- Full automation of the feeding process.
- Geared to process bobbins of any shape and quality with greatest possible efficiency.
POLAR/E Premium machine fact sheet:
- Higher loading rate for feeding up to 72 spindles: the innovative twin sorting delivers two bobbins simultaneously
- Feeding bobbin capacity up to n¦ 3000 per hour: a new high-speed optical scanner reads the profile of the bobbin. An air jet system distributes the bobbins between the two high-speed peg loaders. The system is the fastest available as it rely on minimum number of moving parts.
- End finder stations: End finder stations are designed to handle bobbins with yarn reserve at the bottom of the tube (in ring frames without automatic doffing, the presence of bottom reserve is usually erratic). The machine design has been focused on the layout of the end finder stations to optimise the bobbin distribution. Same stations are distributed along the machine sections, consequently allowing an evenly and balanced bobbins distribution to the whole machine. Minimum distance between feeding and spindles is important in case of long machines. The machine comes with two end finder stations as standard, but according to the requirement of the process a third station can be added.
- Backup station: A great help to ensure the highest efficiency of the winding process is given by the Backup station, which processes all those bobbins rejected by spindles and the end finder stations for different reasons: bad shaped bobbins, bobbins with yarn remnants, technological alarms (off-standard quality yarn values). Its dedicated slow-moving sorting cycle permits to reach a very high efficiency, with the result that manual reprocessing by the operator is no longer required.
- Whenever a bobbin is rejected, the reason for the rejection is recorded onto a ID tag embedded in each and every peg.
- Bobbin tube stripper: any yarn remnants on tube will be removed by the efficient stripper. Perfectly clean tubes can consequently be returned to spinning room.
At ITMA ASIA in Shanghai, Savio will also display the automatic winder model ORION SUPER M, which is already a best seller in the Chinese market. This manual feeding winder is particularly designed for the Far East market in order to meet the high yarn quality demand, together with high production output, reduced energy consumption, maintenance and investment. The machine, with manual bobbins feeding and manual or automatic packages doffing, completely controls all the parameters of the winding process by the main PC. In addition, the machine has the self-diagnosis monitoring per each winding head. High productivity, together with yarn and package quality level, can be obtained thanks to the flexible and intelligent cycle, in addition to the controlled and customized dynamic drum acceleration.
For futher information:
Paolo Puntoni, Marketing Director, Email: p.puntoni@saviospa.it