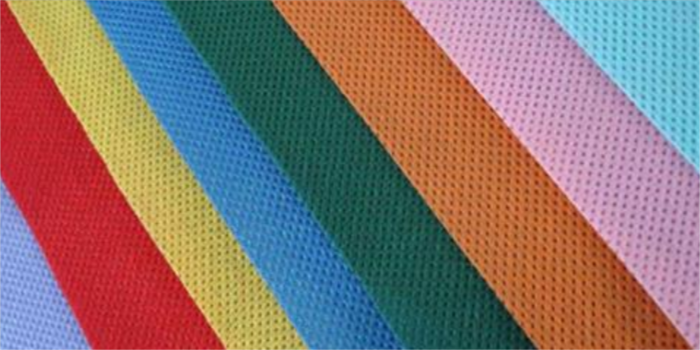
Radici invests €15M in new line
RadiciGroup invests EUR 15 million in a new production line for meltblown nonwoven, the filtering material used in protective face masks.
A strategic
decision aimed at more independent Italian production of personal protective
equipment RadiciGroup has taken the next step in its commitment to the health
emergency response, by making a sizeable investment for the purchase of a new
production line for meltblown nonwoven, the material used for manufacturing
protective face masks and other personal protective equipment (PPE).
The Group has
been at the forefront in the fight against the spread of COVID-19 from the very
beginning of the pandemic, above all by rapidly setting up a production chain
involving local factories for the manufacture of spunbond nonwoven for medical
gowns and other personal protective equipment. As a result, the Group quickly
came to the decision to produce meltblown nonwoven, a type of nonwoven not
readily available in the Italian market, but indispensable in the manufacture
of surgical masks.
“In the midst
of the pandemic crisis,†said Maurizio
Radici, vice president and COO of RadiciGroup, “the lack of meltblown
nonwoven became evident. We kept receiving tens of requests from potential
customers. A very small quantity of meltblown material is produced in Europe,
which is certainly not sufficient to meet demand in a health emergency. Given
our extensive experience in the field of nonwovens, we swiftly began figuring out
how to set up a chain for the production of PPE in Italy. And, as soon as the
opportunity arose to take concrete action, we had no hesitation to jump on itâ€.
The
investment made by RadiciGroup for the meltblown nonwoven production line is
EUR 15 million. Presently being installed, the large new line is extremely
sophisticated and technologically advanced. It has a high production capacity
and can also realise products with special technical characteristics, not only
made of polypropylene, but also other polymers, such as polyester, polyamide
and TPU. The new line is being set up at Tessiture Pietro Radici SpA, a Group
company based in Gandino (Bergamo), where work was previously carried out to
ready the site.
Enrico Buriani, CEO of Tessiture Pietro
Radici, added:
“With this new line installed in the Seriana Valley – among the areas in Italy
that have been hardest hit by the coronavirus pandemic, RadiciGroup will become
one of the few European manufacturers able to offer both spunbond nonwoven – a
well-known product already produced by Tessiture Pietro Radici for many years
and used in protective face masks as both the outer layer of fabric and the
inner one in direct contact with the face – and meltblown, which is the real
filtering and protective component of all types of masks, including surgical
and FFP2 or FFP3 protective masks. In terms of production capacity, the new
line will be able to produce about 120 tonnes/month of meltblown nonwoven, or
enough material to make about 170 million surgical masks per month.
The objective
is to reduce the dependence on imports from non-European countries – indeed,
during the pandemic, there have been long slowdowns in deliveries of imports –
and to bring back to Italy the production of essential products for health protection
needed during health emergencies. Suffice it to say that, from February to
August 2020, Italy imported EUR 2.66 billion worth of masks, 92 per cent of
which came from China (source: Assosistema – Confindustria).
“We believe
it is vital for Italy not to be caught unprepared in future health
emergencies,†Radici continued. “Our country must have its own production of
essential goods, and our purchase of the new line for the production of
meltblown nonwoven is a step in that direction. At the same time, the
production line is an investment for our Group, because we must also consider
the fact that other technical applications will be found for this material,
such as filtration, thus presenting prospects for economic sustainability in
the medium term.â€
On the
technical side, meltblown fabric is a continuous filament nonwoven (from 1 to 5
microns in diameter), has excellent filtering capability even for particles of
microscopic size, such as viruses, and ensures breathability and protection.
The installation
of the machinery will be completed in January 2021, after which the line will
start operating 24 hours a day, 7 days a week.