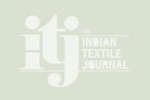
Prospects, challenges and remedies of TEI industry
The Indian Textile Engineering Industry (TEI) is more than 100 years old with an illustrious history of achievements, including manufacture of advanced spinning machinery, power looms, weaving preparatory machines, finishing and dyeing machines, etc. It has also made a mark in the world specially in the field of export of accessories which amount to nearly two-third of last year?s export of about Rs 2,600 crore.
The Indian TEI has the potential to grow more than 10 times to a $10 billion industry provided all the stakeholders including the Government adopt a mission to ?Make India a world leader in textiles by 2025?, says Kishore Khaitan.
The Indian Textile Engineering Industry (TEI) is more than 100 years old with an illustrious history of achievements, including manufacture of advanced spinning machinery, power looms, weaving preparatory machines, finishing and dyeing machines, etc. It has also made a mark in the world specially in the field of export of accessories which amount to nearly two-third of last year?s export of about Rs 2,600 crore.
However, due to structural problems, lack of fiscal policy support and small size of firms engaged in the business, the industry has not grown to its potential. Import of machinery and spares in India (Rs 10,385 crore) still constitutes more than 70 per cent in value of domestic demand. In comparison, China, which had a negligible TEI in 1990, has now grown into a major manufacturer and exporter of textile machinery and spares. Indian manufacturers sold about Rs 3,900 crore worth machinery and spares in India and exported about Rs 2,600 crore (40 per cent of production), while operating at only 60 per cent capacity utilisation.
The Indian TEI has the potential to grow more than 10 times to a $10 billion industry provided all the stakeholders including the Government adopt a mission to ?Make India a world leader in textiles by 2025?. We have the skills, the tradition, the designs, the manpower, the raw material and a large domestic market to achieve this but it shall remain a pipe dream if we do not channelise all forces to this common goal.
We would like to briefly mention the problems hampering the industry growth and the remedial measures required:
1. Lack of scale and technology: Most firms are SMEs who do not have the wherewithal to compete with global giants. High interest rates, reluctance of mills for using domestic products, lack of access to latest technology, lack of R&D infrastructure with academic institutions not geared up to undertake R&D projects on commercial basis, lack of innovation and zero-defects culture, archaic labour laws ? these and innumerable other hurdles are the well-known impediments.
2. Lack of presence in all sectors: India does not possess advanced technology to offer machinery and parts for knitting, garmenting, non-wovens, technical textiles, embroidery, made-ups, garment accessories, etc. besides being leagues behind in weaving and finishing of fabrics.
3. Adverse import policy: Many machines are imported at concessional or nil duty while components attract 25 per cent or more duty (including CVD). Second hand machines were also till last year enjoying subsidised interest and capital subsidy and duty concessions under TUF, EPCG and State promotional schemes whereas similar benefits were not available to local products.
4. Lack of government support for technology advancement: While huge subsidies are provided under TUF scheme to subsidise imports, the Indian TEI is not offered any concessional benefits similar to TUF to develop advanced indigenous technology to make machinery and components at par with international standards. This is in spite of fact that Indian machinery is typically 40-60 per cent cheaper than imported in most cases. If the government promotes technology among Indian manufacturers by offering a TUF scheme for TEI, there may not be any need for TUF for the textile industry as machinery and parts will be available at 40-60 per cent lower cost! However, the strong lobby of foreign suppliers supported by domestic mills due to TUF scheme, had prevented this from happening in spite of the obvious advantages. Also the TUF for textile machinery would cost the Government not more than 20 per cent of what it provides for the textile industry. Huge savings to exchequer through subsidy reduction can be done if this faulty approach is corrected.
5. Lack of ecosystem to support innovation: While mills readily adopt new advancements by manufacturers abroad and willingly pay a huge mark-up on it, they are usually reluctant to try and encourage domestic innovators? products having apprehensions of quality, performance, reliability, consistency etc., even though the product is available at a fraction of the price. Also the innovator gets no financial support in terms of soft loans and if his innovation fails, he has to close his company and sell collateral to repay the loan.
6. Lack of advanced technical education: Most of the institutes have old curriculum, lack of modern and functioning laboratory, lack of practical field experience and also don?t teach basic communication and management skills to students to prepare them for the real world. As such, all employers have to train the new recruits extensively, thus causing a great loss to the nation, to their productivity and competitiveness, to their ability to innovate and improve operations.
7. Uncompetitive textile industry: When the customer (mills) are in a weak financial position, they cannot adequately support TEI. Cheap imports through FTAs, SAARC countries and under wrong ITC code lead to dumping of imports from China and other countries at unsustainable prices. At the same time, import barriers that discriminate against Indian textiles as compared to China or LDC countries prevent domestic industry from getting their fair share of export market.
However, the situation is not as hopeless as it sounds since there is still a possibility to address these problems in a cohesive and united manner by all stake-holders.
We are the second largest producer of textiles in the world, one of the largest markets and one of the largest importers of textile machinery. So the foundation exists, only the right action is required. The following are the suggested remedies for each of above problems:
1. Building scale and technology: The Government policy can help domestic manufacturers to build their capacity and technology through several fiscal and policy measures such as concessional import duty on import of components, TUF scheme for TEI, special soft loans scheme for JVs with manufacturers abroad for acquiring latest technology, concessional infrastructure in TEI parks (similar to textile parks scheme), special export promotion schemes to support export marketing efforts, subsidies for undertaking technical training and process improvement programs by adopting TPM, LEAN, Cluster programs similar to what the auto components industry ahs been able to achieve, special incentives for Mills and machinery manufacturers on buying domestic machinery and parts, special assistance for supporting opening of offices or warehouses abroad, etc.
2. Provide attractive scheme for leading machinery manufacturers in weak presence sectors: If special scheme for investment under MAKE IN INDIA, including tax holidays, are offered to encourage foreign suppliers to set up manufacturing in India, it will help develop local industry for components and also in due course lead to new Indian manufacturers for the same machinery, thus building a healthy and competitive market domestically and drastically cutting down on imports. Currently there is no incentive for manufacturers abroad to manufacture in India since the import policy favours them. The secret of China?s success is in their ability to get foreign investment for domestic manufacturing of textile machinery and parts.
3. Import policy biased towards domestic manufacturers: If, and only if, manufacturing in India entails savings in taxes as compared to imports will Indian TEI start becoming competitive and imports will be discouraged. This would lead to a rush of foreign manufacturers setting shop in India to prevent losing this growing and very important global market. China was smart enough to realize this early on and even forced companies to invest in China if they wanted their market.
4. Government support: Already covered under point 1.
5. Ecosystem to promote innovation: It is a huge challenge to change the mindset of all stakeholders involved ? the producers, the customers, the government and the academia. But it is worth it if it helps promotes innovation. Mills adopting an innovation support policy, institutions having grants to promote and support industrial research and innovation projects on commercial basis, practical training made mandatory for students to become employable, national awards for innovation in textiles and machinery to recognize best efforts and successes and manufacturers adopting advanced manufacturing practices and quality norms in their plants and becoming committed to offer consistent world class quality at competitive priced, backed up with efficient after-sales service and timely deliveries would go a long way in transforming the current mindset.
6. World-class technical education: This can be promoted by inviting top international institutes (both for degree courses and vocational training) to start operation in India and creating a healthy competitive environment for the existing academic institutions.
7. Level-playing field: The government has a moral responsibility to give its textile industry a level playing field in the domestic market. If textile imports, subsidized by exporting country or wrongfully taking advantage of FTAs, are allowed at artificially lowered import prices.
The article is authored by Kishore Khaitan, Managing Director, Basant Wire Industries.