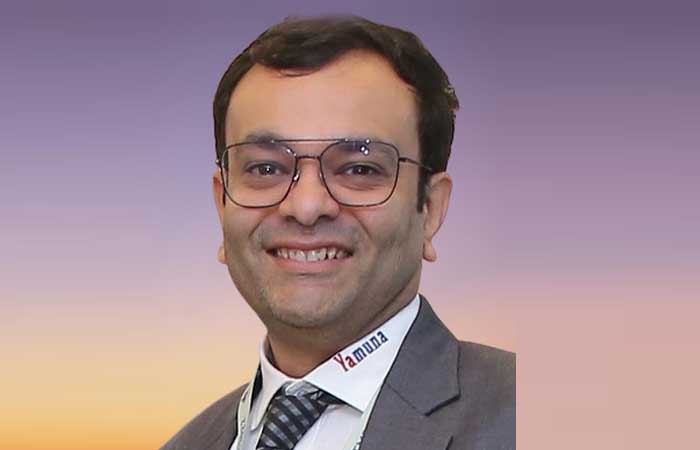
Prashant Mangukia: We need to gear up our capacities and capabilities to achieve the target of $350 billion
Yamuna Machine Works was established in 1990, and started its manufacturing activity with Hot Air Stenters. Today, it is ranked among the leading manufacturers for textile processing, finishing machinery and associated branches of industries. We are a leading manufacturing and export house engaged in manufacturing textile processing machineries and customised solutions for wovens, non wovens, knits, denims, carpets and technical textiles. Our wide range of machinery for different segments of textiles is nurtured over 3 decades of experience and adding products in our range as the demands changed in the industry over the years. We have complete solutions for textile processing from singeing to pre-treatment to dyeing and finally finishing machines. Prashant Mangukia, Director, Yamuna Machine Works, shares present state of the Indian textile machinery industry and how is his company contributing to it.
How is your company serving customers from the textile & apparels (T&As) segment?
We, at Yamuna, are continually updating our products to stay ahead of the rapid development of process technology, ensuring the competitiveness of our customers. As a part of our continuous up gradation and looking at the responses we are receiving from the market we have added a dedicated team of professionals to serve customers having innovative ideas and vision for developing technical textiles and other related products and projects. i.e. we not only supply machines we also support our customers to develop products and give training for the production as well as machine handling.
According to you, what is the present state of the Indian T&A industry and textile machinery & accessories (TMA) industry?
The Indian textile industry has been undergoing challenging times for the last 2 to 3 years. Although the domestic demand for the garments is quite steady, the export growth has been negative in the last 3 years. Only in this fiscal year, there has been positive growth, thanks to the destocking by the buyers in the US and EU and the political turmoil in Bangladesh. In contrast, the exports of home textiles have shown steady demand in exports in the last 2 years. The spinning sector has been facing underutilisation for quite some time. This and the raw material price volatility have affected their margins. The fabric demand also was affected mainly in the MMF segment, due to the dumping of MMF knitted fabrics at very low prices from China. Now this issue is being taken care of by the government by declaring a minimum import price for synthetic knitted fabrics. The garment segment, though received export orders which shifted from Bangladesh, is unlikely to continue with success due to a lack of capacity.
The textile machinery and accessories industry draws its fate from the textile industry hence some segments of the industry had a very tough time. Especially the spinning machinery demand was low while weaving, knitting and processing machinery investments showed positive trends during the year. The textile machinery market size is around Rs.20,000 crore out of which nearly 60 per cent of the machinery gets imported from China, Europe and Japan, mainly in weaving, knitting, processing and garment making.
The Indian textile sector has set an ambitious target of achieving $350 billion in market size by 2030. In your opinion, what are the significant challenges or barriers that could hinder this progress?
Although the government has set an ambitious target of $350 billion market size including $100 billion in exports for 2030, this seems a very difficult task, especially with the present numbers ($168 billion market size and $40 billion in exports) and the present condition of the industry. The asking rate seems very high with the present capacity of the industry, bottlenecks in the value chain and the challenges in exports. Against this backdrop, the target seems very challenging.
The biggest challenges are
- Lack of capacity in garments
- Absence of Ecosystem supporting garment manufacturing
- Fractured textile value chain
- Limited FTAs
- Tariff barriers in the EU and US markets affecting competitiveness
- Stricter Sustainability and ESG Regulations from the EU
- With the majority of industry in MSME, adopting sustainable manufacturing is difficult
- Lack of adequate textile machinery manufacturing capacity to support the growth of the textile industry
How important is technological modernisation for enhancing the Indian T&As industry’s global competitiveness? What more can be done to accelerate the adoption of cutting-edge technologies in this sector?
It is very important to adopt the latest technologies and modernise the existing capacity. Over and above this it is also important to adopt best manufacturing practices for efficient manufacturing, quality consistency and cost competitiveness. The spinning capacity is fairly modern while weaving and processing need a lot of investments to upgrade the industry. In the case of China, one of the factors contributing to the high growth of their T&A industry is the strong support of the local textile machinery manufacturing industry. That is not the case in India. India still depends on imports of over 60 per cent of the annual textile machinery requirement, more so in weaving, knitting, processing and garmenting. It is necessary to attract investments in manufacturing of textile machinery including import substitute machinery through joint ventures or collaborations, where technologies are not available locally. More focus on digitalisation, and automation is necessary for matching the best manufacturing infrastructure in the world.
What opportunities do you foresee for your company as the Indian T&As industry aims to achieve their 2030 target?
As Indian T&A industry is poised to grow in the coming years at much faster pace than it has been in the past, to achieve the ambitious target laid down by ministry for 2030. To make this possible, entire value chain of industry needs to work in synergy and machinery and infrastructure are integral part of it. Which means we also need to gear up our capacities and capabilities to make this possible. This will open a lot of opportunities for machinery segment especially processing machines as it has been one of the bottlenecks in manufacturing. To achieve this we have to have indigenous machines to keep the overall investment low and make it feasible. This is the window where in Yamuna fits in very well and we see ample of opportunities in coming years.
With the need for sustainability growing in the T&As industry, how is your company helping T&A makers to achieve their green goals?
Sustainable manufacturing has become an essential in line with the changing global trends. Our customers who export their goods are fast adopting sustainable practices and materials and expect us to also supply machines which comply with these requirements
The design of Yamuna machines involves less water, energy and chemicals in process for the end user and helps save wastages Yamuna offers ergonomic design machine as per customer needs, thus envelopes minimum use of natural resources and optimise their production and enhances customer sustainable goals. Yamuna aims to serve its customers even beyond warranty and prioritising efforts to minimise breakdowns at the same time we are also making our manufacturing processes more sustainable – While manufacturing machines we use SAP program which helps control inventory, right first-time component manufacture, avoid duplicity and checking at each stage in the WIP inventory.
What measures should the government take to further strengthen the Indian T&As and TMA industries?
The government should take steps on the following points: Help industry create an ecosystem in garments like in Bangladesh and China, Expedite closing of Free Trade Agreements (FTAs) with the trading blocs/countries, Create an efficient Ecosystem for textile manufacturers to grow, Encourage creation of capacities in garment making, Encourage manufacturing of import substitute and man-made fibre-based products, Accelerate the Skill Development initiatives, Encourage local textile machinery manufacturing
What are emerging trends in the textile machinery & accessories industry?
Some of the major trends are:
- More usage of automation and digitalisation
- Application of AI and machine learning
- Focus on increasing the energy efficiency of machines
- Lesser usage of water and chemicals
- Reduction in wastage
- Recycling
- Machines designed for Sustainable Manufacturing
- Online monitoring of the process and fault detection
- Tele-services to the customers
What are your growth plans in the next two years?
Our ambition is to become a truly global company in the coming decade and for that we are expanding our manufacturing program as well as our reach to different corners of the globe. We see ourselves as a leading innovative machinery manufacturer with strong global presence in the years to come. We also want to become single window supplier in processing machinery and provide cutting edge solutions to industry when it comes to customsied machines and technologies. The future is being viewed with enthusiasm where the key task seems to be continued up-gradation to newer technologies to maintain highest level of productivity, efficiency and quality of the fabric treated on our machines.