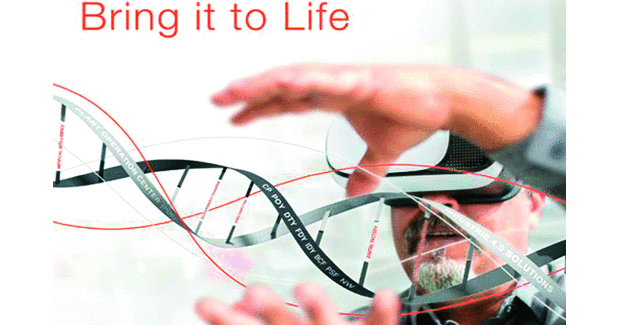
Oerlikon: En route to digital yarn factory
The wiping robot has been operating at two major yarn manufacturers in China now.
From Melt to Yarn, Fibres and Nonwovens – Bring it to Life†– is the motto under which the Oerlikon Manmade Fibers Segment will transform itself into a digital machinery and plant manufacturing company showcasing its power as one of the innovation leaders for the production of chemical fibres. En route to the digital yarn factory, technologies such as artificial intelligence, machine learning or innovative HMI (Human Machine Interface) solutions promise the bridging between material and data flow – for customer value.
The scenario of the future: textile production – from the supply chain through to dispatch – is autonomously controlled in the fully-networked Factory 4.0. The product being created controls and monitors the processes itself using embedded sensors. The manufacturing or order status is known at all times, raw materials are automatically reordered, wear and maintenance are planned as integral parts of the production process and error processes are identified, alleviated or displayed. This should cut costs, convert production lines more flexibly and help reduce downtime and waste. For this, the machine construction sector has to provide correspondingly intelligent and Web-enabled production systems. No easy feat, as this requires interfaces between all systems involved and the collation, channeling and evaluation of tremendous volumes of data in real time.
Oerlikon Manmade Fibers Segment wants to face those technical development challenges and has high standards. “We want to become the textile machine construction trendsetter for technologies of this kind,†says CEO Georg Stausberg. The first steps on this journey have already been taken. The Plant Operation Center (POC) for process monitoring enables the collation of existing production data in a central location and to make these data available. HMI based services such as process monitoring via a service online app on smart phones and tablets were introduced as well as an assistance system based on mixed-reality glasses (Microsoft HoloLens). The system supports predictive maintenance concepts and enables virtual 360-degree tours through spinning systems.
AIM4DTY: Automated detection of error
Te company gave an insight to this as well as an outlook for new developments for the digitisation of the process chain “From Melt to Yarn, Fibers and Nonwovenâ€. The digital future solution AIM4DTY provides help with the identification of possible error causes in texturing machines to help reduce quality risks. Here, machine learning is being used: The system recognises and is being “trained†using trend charts and their respective errors. An example: In the texturing machine, the UNITENS monitoring sensor measures the yarn tension at all positions. An error is generated if a measurement value does not lie within the prescribed tolerances. In a lot of cases, the form of the graphs can provide information on the error causes and ultimately provide targeted and efficient response to these. A manual analysis and optimisation is nearly impossible with more than 1,25,000 graphs per day. With the automated solution, AIM4DTY the information is instantly available to customers, therefore allowing them to immediately optimise the quality during running production.
Here, data security, data minimisation and transparency are extremely important. This means that the data are utilised at the customer site as far as possible and only transferred to the Oerlikon central customer data centre if required – and only following customer approval. “We process all data in accordance with the new European General Data Protection Regulation (GDPR), taking all further international data protection standards into account. Our customers always know which data we use and whyâ€, explains Mario Arcidiacono, Business Intelligence & Data Warehouse specialist for the Oerlikon Manmade Fibers Segment.
Wiping robot with intelligent control
The advantage of the wiping robot used for the cleaning of the spinnerets is automation: intelligent control system that connects machines and processes. The information relating to all wiping positions, cycles and times can be saved in the management system. The robot accesses the saved wiping intervals in an automated and safety-relevant manner. The robot can cope with up to 48 positions.
However, more decisive here is the impact of the intelligent control system, with whose help the spinning pump can be moved up and down in an automated and ‘in-time’ manner. To this end, pump stops can be kept to the absolute minimum using a robot, considerably reducing the impact of the wiping on both the polycondensation system process stability and on the yarn data of the spun yarn. The advantages over the manual process are for example extended cleaning cycles, less silicon use, more production time, less operating costs as well as advantages for human resources and health management. The wiping robot has been operating at two major yarn manufacturers in China now.
World premiere: Staple FORCE S1100
There are even more news regarding the exhibition to come: The Staple FORCE S1100 is a one-step plant, which spins, draws, crimps, cuts and bales in a single process step, produces small batches (up to 15 tonnes per day) and can be swiftly reconfigured for various requirements, including polymer, dye and titer changes. Its process control system for easy operation is absolutely unique. The service for repair-coating from Oerlikon Barmag for thread-handling parts such as godet jackets also includes the expert’s know-how to identify and review abrasion in order to recreate the correct surface structure at the location. This way they can provide all important requirements to creating optimal plant and yarn quality.
News from the PA6/66 sector
With the acquisition of the PE Polymer Engineering Plant Construction GmbH, based in Thuringia, Germany, Oerlikon Manmade Fibers Segment expanded its now completed polyamide process chain for fibers and filaments. The now available and tested technologies in the melt preparation process include the entire polyamide 6 polycondensation systems division and its PA6/66 co-polymer and the patented dimer-hydrolysis procedures for feeding recycled-lactam with the very highest end-product quality.