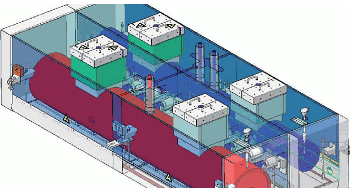
New system concepts for spinning filament yarns
Two spinning concepts for the economic production of high quality bico filament yarns promise tailormade solutions for all applications, explain Günter Schütt and Susanne Beyer from Oerlikon. Although bicomponent yarns have been around for about 50 years now and they are not a new phenomenon, we have seen a constant increase in demand over the past few years (with frequent fashion-related peaks in 2015, for example). Reasons for this development are manifold. In addition to current fashion trends, new, highly-efficient solutions for manufacturing textile fabrics such as circular knitting, for instance, reduce production costs.
Two spinning concepts for the economic production of high quality bico filament yarns promise tailormade solutions for all applications, explain Günter Schütt and Susanne Beyer from Oerlikon.
Although bicomponent yarns have been around for about 50 years now and they are not a new phenomenon, we have seen a constant increase in demand over the past few years (with frequent fashion-related peaks in 2015, for example). Reasons for this development are manifold. In addition to current fashion trends, new, highly-efficient solutions for manufacturing textile fabrics such as circular knitting, for instance, reduce production costs.
Bicomponent yarns offer a huge range of possible crosssections. In general, these yarns comprise two different polymers, which give them specific properties. Bicomponent yarns with the corresponding cross-sections are manufactured depending on the desired application. Here, the four best-known cross-sections are core-sheath, side-by-side, segmented-pie and islands-in-the-sea.
Core-sheath and side-by-side cross-sections are typical and often used in staple fibre yarns, while the other two crosssections are predominantly filament yarns. While core-sheath bicomponent yarns are frequently processed as bonding fibres for nonwovens, the focus when manufacturing side-by-side bicomponent yarns is on the desired self-crimping effect. Segmented-pie and islands-in-the-sea cross-sections are mainly manufactured for producing super-microfibres, i.e., less than 0.3 dpf.
Diverse cross-sections
The most wide-spread are core-sheath cross-sections; their applications are extremely diverse. Core-sheath cross-sections are predominantly used as staple fibres or as continuous filament in spunbond products. Major applications are described in the following.
Bicomponent fibres or bicomponent filaments are frequently used as bonding fibres or filaments to bond the actual fibres and filaments together. In the case of carded nonwovens, for example, the sheath polymer of a bicomponent staple fibre is melted on in an oven. The melting point of the sheath material is lower than that of the core material, with the result that the core fibres adhere at the crossing points. Here, the sheath is usually completely dissolved and consequently acts as an adhesive. To ensure sufficient adhesion, the sheath ratio of the fibre is relatively high at around 50 per cent.
Frequently used polymer combinations (core/sheath) include PET/CoPET (low melt) and PP/PE. In the case of fibres and filaments with special properties, additives or colour and/or titanium-dioxide (TiO2) masterbatches are fed into the sheath polymer to achieve special properties. These can – for example – be functional polymers for hydrophilisation or antibacterial properties. PE is a popular choice as the sheath for fibres and filaments for hygiene products with the aim of improving their tactile properties. Here, the sheath ratio lies between 10 and 30 per cent and is therefore as low as possible to keep the costs for additives and masterbatches low.
A very high proportion of the costs for manufacturing fibres and filaments are attributed to the raw materials. One option for lowering the costs is to manufacture fibres and filaments with less expensive polymers in the core, such as B-grade polymer or recycled material. The high-end and more expensive polymers form the sheath, whose ratio is relatively low at between 10 and 30 per cent. Typical material combinations here are RPET/PET, PP/PP and RPA6/PA6.
The eccentricity of the core
One special feature of the core-sheath cross-section is fibres with eccentric cores. This results in a so-called self-crimp effect. Following spinning, the filaments are drawn in a fibre line. The eccentricity of the core and the resulting differing levels of stretch create the crimp in the fibre or filament.
The same effect is achieved in the case of side-by-side cross-sections. With these, various polymers, such as PP/ PE, PET/PE, PET/CoPET are used, or the same polymers with differing viscosities (PET/PET, PP/PP). Side-by-side fibres and filaments are predominantly manufactured as circular or circular-hollow cross-sections, although other cross-sections are also possible. Typical textile fabrics made from bicomponent yarns with side-by-side cross-sections are cord fabrics, for example.
Fine yarns: bicomponent microfibres
Sea-island cross-sections form one group of bicomponent microfibres/filaments. They are manufactured as staple fibres for imitation leather or as filaments for textile applications such as velvet, for example. Typical polymer combinations (sea/island) are PET/CoPET and PA/CoPET. Following the fibre or filament manufacturing process, the sea polymer is dissolved in an alkaline solution, so that only the island filaments are left. This process creates micro filaments with titers as low as 0.03 dtex. Within the market, 37 islands per filament is the established standard, although constructions with up to 91 islands are possible at Oerlikon Neumag. However, the hole density on the spinneret decreases in this case. Fibres and filaments with a sea ratio of 30% can be reliably manufactured. Lower ratios are possible; however, this increases the risk of clotted island filaments.
Segmented-pie or orange-shaped cross-sections form the second group of bicomponent microfibres/filaments. These are found more in filament and spunbond applications and less in staple fibre applications. Filaments with 16 segments are most frequently used. However, filaments comprising 32 or 64 segments can also be manufactured. Mechanically splittable filaments are made from PET/PA6: these polymers have a low adhesion among each other and can be easily mechanically separated. In the case of nonwovens, separation is carried out using a water jet or, for textile products, by means of the dyeing process. In the past, the material ratios were frequently 50/50. However, the ratio of PA6 has – for cost reasons – been consistently reduced over time and now lies at 20 per cent.
Demanding technology for demanding yarns
The stability of the bicomponent process is decisively influenced by the pressure differences in the spin pack: the lower the pressure difference, the more stable the process. Equally relevant is the quality of the polymer used. A stable polymer of good, consistent quality and that is not particularly sensitive to temperature changes guarantees a stable spinning process. Low viscosity differences in the material and a narrow molecular weight distribution are further requirements for a reliable bicomponent process.
Oerlikon Barmag and Oerlikon Neumag have been supplying systems for the manufacture of bicomponent staple fibre yarns and filament yarns since the mid-1980s and are hence able to draw on extensive process know-how and expertise. The two manmade fibre systems constructors have already equipped both staple fibre systems and systems used for the manufacture of BCF, POY, FDY and spunbond with bicomponent spinning machinery. Here, the primary focus was on the four cross-sections already mentioned.
The requirements for the systems and processes are becoming increasingly complex. Mixing ratios of 70/30 have long been standard now, with larger mixing ratios – such as 90/10 for core-sheath bicomponent yarns – increasingly shifting into the foreground. Correspondingly, separate special temperature controls for each polymer type and an expanded process window are standard for Oerlikon Barmag and Oerlikon Neumag concepts.
System concepts
With all bicomponent system concepts, the temperature transfer for the differing polymers A and B can be set separately all the way through to the spin beam; in other words, for the extruder, the melt filter and the polymer lines through to the spin beam.
Depending on the polymer type, it is recommended that the temperatures be separated even more systematically. With these concepts, the temperatures are separated until directly before the polymers reach the spin packs; specifically the melt inlet lines, the spinning pumps and the majority of the melt lines from the spinning pumps to the spin packs.
Depending on the system concept, the temperature transfer for polymer B differs in length (Fig. 2). Irrespective of this, the two polymers meet in the spin pack. Here, a joint temperature level is achieved, which results in the corresponding polymer viscosities. To ensure even spinning quality, the ratios of the polymer viscosities should not be too disparate. In the case of side-by-side processes, substantial differences in viscosity result in spinning errors. So-called ‘dog legs’, for example, lead to the melt flow bending just below the spinneret.
Single-temperature system
This system concept includes separate temperature transfer up to the polymer entering the spin beam. The starting situation: polymer A (i.e. PET) has a process temperature greater than or equal to polymer B (i.e. PA6). Generally, the distribution lines for polymer A and the spin beam have the same temperatures. They are frequently connected to an HTM circuit.
However, systematic temperature separation, as made possible in the case of the dual-temperature system, is nevertheless not always essential. For some bicomponent processes – such as processing recycled polymer or B-grade polymer in the core and virgin polymer in the sheath, for example – the same process temperatures are set. For some staple fibre and spunbond products, the temperature transfer is also as in the case of the single-temperature system, although the process temperatures are very different. One example of these is the core-sheath fibres PET/PE: the processing temperature for PET is around 295 °C and around 210 °C for PE. This is possible because PE is relatively insensitive to higher temperatures and the dwell times are low due to the throughput.
Dual-temperature system
The principle of this concept is the separate polymer transfer, each with its own temperature control system up to just before the spin pack. Systematic temperature separation is important in the case of processing polymers which tend to have a high risk of degradation, such as PS, TPU, and several modified polymers, such as CoPET, CoPA6, CoPP, etc.
For example the monomer formation of PA6 increases exponentially to the processing temperature. For sensitive polymers, it is necessary to keep the dwell time within the higher tempered spin beam as short as possible (Fig. 3). Due to the design of the dual-temperature system the dwell time of component B in the temperature ambit of component A is reduced significantly.
In the case of the dual-temperature system, the spinning pumps and melt distribution systems for component B are located in a separate housing. This, in turn, is connected to its own HTM circuit; the transition to the housing with the spin packs is consistently heated. Standard market constructions where this is not the case have the significant disadvantage that the melt in the non-heated areas freezes and forms a plug in the event of a production stop. This blocks the melt flow, which brings the entire system to a standstill.
SP8xB
Thanks to a new spinning system concept, sensitive polymers can now also be processed to make bicomponent yarns in the filament yarn segment. The basis of the new technology is the above-described dual-temperature system. With this, the quality and the viscosity of the polymers can be accurately adjusted in accordance with the respective process requirements.
The stringent separation of the HTM heating systems of both polymer lines and the spinning pump ensure the least possible damage to each polymer type right up to the point at which the two components are combined in the spin pack, hence guaranteeing optimum spinning conditions.
The new system is based on the SP8x spin beam concept and, needless to say, offers energy cost advantages compared to the rectangular concept, such as considerably lower heating power. Less sensitive polymers can also be effortlessly manufactured using the standard SP8xB bicomponent spinning unit. The new spinning system concept is available both for the single-row and – as a unique concept within the market – for the two-row, Z-design arrangement spin pack.
Summary
Oerlikon Barmag and Oerlikon Neumag offer tailor-made concepts for all applications. For standard polymer and standard cross-sections, the single-temperature system is the ideal solution; whereas the dual-temperature system is recommended for microfibres and temperature-sensitive polymers.
However, most co-polymers available on the market are considerably more stable and hence more temperature-independent than even a few years ago.
Correspondingly, the ratio of polymers for which systematic separation of the temperature transfers right up to the spin pack is essential now lies as between 5 and 10 per cent. The vast majority of cross-sections can be manufactured using the single-temperature system. This in turn has significant cost advantages in production.
With the patented Oerlikon Manmade Fibers segment dual-temperature system, sensitive polymers are processed into high-quality bicomponent fibres and filaments. This concept also offers yarn producers a considerable degree of flexibility.
For further information:
Oerlikon Barmag
Zweigniederlassung der
Oerlikon Textile GmbH & Co. KG
Zwickauer Straße 247
09116 Chemnitz, Germany
Tel: +49 371 23 88 240
Email: info-spinnzwirn.barmag@oerlikon.com