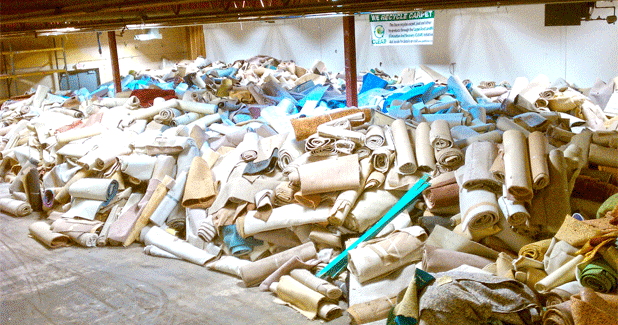
Methods to control waste in multiplying process
High-waste generation at cop winder would lead to loss of production, find NK Mahajan, RN Turukmane, DS Borse, RD Parsi and SK Dey. The Indian man-made fibre industry is creating a benchmark in allied fibre production, similarly competing with global man-made fibre industries. Some industries have practices to produce fibre, yarn and filaments on large scale without the measure to control hard waste during the multiplying process. This is why they cannot stand in the international market in terms of quality productivity.
High-waste generation at cop winder would lead to loss of production, find NK Mahajan, RN Turukmane, DS Borse, RD Parsi and SK Dey.
The Indian man-made fibre industry is creating a benchmark in allied fibre production, similarly competing with global man-made fibre industries. Some industries have practices to produce fibre, yarn and filaments on large scale without the measure to control hard waste during the multiplying process. This is why they cannot stand in the international market in terms of quality productivity.
Most of the synthetic fibre industries generate high bottom waste during the multiplying process. This brings down the manufacturers to huge losses. Multiplying is an essential operation in a man-made fibre industry before processing yarn for doubling, assembly winding and cabling processes. High-waste generation at cop winder would lead to loss of production and non-profitable job to the industry. The impact of high- and low-density rewinding packages create more bottom waste in subsequent operations for this cop winder machine as it needs attention while using it for rewinding of filament yarn from bigger cheese to small cops suitable for twisting machine.
The quality of package depends on the yarn pitch, angle of wind and stroke height. All these parameters would lead to produce a package with desired density, weight and yarn content of the package. Tension variation on cop winding machine leads to deteriorating the package density. While using it for assembly winding and cabling, the prepared supply packages exhaust at a faster rate by keeping ample amount of bottom waste on packages. This would in turn increase the hard waste.
- Count – Polyester 300 D
- Machine –Cop winder
- Make – Weave tech Engineers 28 S
The parameters considered for optimisation on cop winder include: bobbin diameter, bobbin weight and yarn tension.
Table 1 shows that there is a variation in DTY bobbin weight and diameter, there are 20 (300 diameter) polyester DTY samples that were run on cop winder machine with existing tension. It was observed that there was significant differences in weight of supply packages. So some packages were exhausted early on doubler machine. It was found that due to uneven tension, the packages differ in density and run out at a faster rate during the multiplying process.
The table 2 shows variation in bobbin weight and diameter of 300 DTY (polyester). About 120 cN tension setting was done on the machine. It was observed that there was no significant difference in package weight and package diameter, so no packages were exhausted on doubler machine due to even tension uniform density packages produced, which resulted in no further complication exhausted at same time. The graph shows waste control on doubler machine. It is clear that the bottom waste generated in multiplying process was 4.1 per cent at regular tension practices. After making changes on the machine and tension was set to 120cN, it was observed that there was no significant difference in package weight and package diameter. So no packages were exhausted abruptly, and everything got exhausted on time. Those packages were produced by equal tension with uniform density, which resulted in reduction of waste from 4.1 per cent to 0.67 per cent. This practice helps the industry to save yarn cost.
- The feed packages received from texturing department have variation in their weight so it generates high bottom waste
- High bottom waste was occurred in TFO cop because of multiple breakage on doubler machine.
- Inadequate maintenance of machinery
- Length measuring device: The function of the device is measured the length of yarn which wounds on the cop, but in actual practice it was not functioning properly resulted in cop weight variation.
- Worker and operator negligence & wrong work practices: If any break is occurred worker didn’t attended the fault in time.
It is conclude that before tension it was observed that there was significant difference in package weight so some packages were exhaust early on doubler machine. It was stated that due to uneven tension package density varies causes problem in doubler machine because of uneven tension during package build up on cop winder. It is very clear that the bottom waste more, i.e.,
4.1 per cent after setting tension, i.e., 120 cN it was observed that there was no significant difference in package weight and package diameter so no packages were exhaust on doubler machine and due to even tension i.e 120 cN on package, uniform density packages produced which result in to no further complication and result in to waste reduction to 0.67 per cent from 4.1 per cent.
1. Kumar, R. S. (2014). Process management in spinning. CRC Press.
2. Adanur, S. (1995). Wellington Sears handbook of industrial textiles. CRC Press.
3.Shanmuganandam D, Sreenivasan J and Suresh Balu I (2013): 29th Costs, Operational Performance and Yarn Quality Study, SITRA publication, Vol 58, No 1.
4. Kathirvel Pandian G and Shanmuganandam D (1996): Measures to Control Hard Waste in Spinning, SITRA publication, Vol 41, No 11, March.
5. Gupta, V. B., & Kothari, V. K. (Eds.). (2012). Manufactured fibre technology. Springer Science & Business Media.
The article is authored by: NK Mahajan, RN Turukmane, DS Borse, RD Parsi and SK Dey. They are from the Centre for Textile Functions, MPSTME, SVKM’S NMIMS, Shirpur Campus, Dhule District, Maharashtra – 425405.