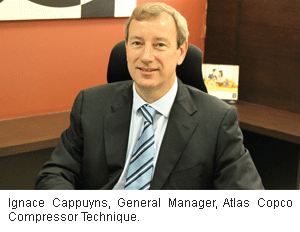
Many textile clients for Atlas Copcos proven technology
Atlas Copco Compressor Technique, a subsidiary of Atlas Copco, provides industrial compressors, vacuum solutions, gas and process compressors and expanders, air and gas treatment equipment
Atlas Copco Compressor Technique, a subsidiary of Atlas Copco, provides industrial compressors, vacuum solutions, gas and process compressors and expanders, air and gas treatment equipment and air management systems. The company recently built a new production facility facility at Chakan, Maharashtra for industrial compressors from 5 to 90 kW and portable compressors from 85 to 1,350 cfm. The factory was built in accordance with Atlas Copco´s globally accepted Sustainable Building Standard and in line with Leadership in Energy & Environmental Design (LEED) best practices has lately been certified by the Indian Green Building Council (IGBC) as a GOLD rated Green Factory Building.
In an interaction with The Indian Textile Journal, Ignace Cappuyns, General Manager, Atlas Copco Compressor Technique, India, talks on the wide range of product portfolio for the Indian market and its recently installed AIRnet, a modular compressed air piping system at a major mill.
Editor: What are the products for the textile industry in your portfolio? Please give us some features of these products?
Ignace Cappuyns (IC): Atlas Copco Compressor Technique has a wide range of products in their product portfolio and can provide complete solution in compressed air requirements. As far as the textile industry is concerned, we have a variety of products, which can be used in this segment like oil injected screw compressors, oil free screw compressors (which complies with ISO8573-1 Class 0) ensures 100 per cent oil-free air at the outlet of the compressor, uniquely designed centrifugal compressor with horizontally split gear box for large air requirements, air dryers to ensure 100 per cent moisture-free air, energy efficient screw blowers for low pressure applications like effluent treatment plants, energy savers to ensure compressors running in their optimum efficiency. We also have an option of screw compressors provided along with variable speed drive to take care of the variable load demands with 70 per cent turn-down and also the option of skid mounted air dryers (rotary drum type heat of compression technology) which ensures (-) 20 D.C. pressure dew point means 100 per cent moist-free air, energy recovery unit, which recovers the heat generated during the compressor process through water. This hot water can be used for various applications in the textile plant like for boiler feed, dyeing, etc. We also have very innovative products in our portfolio like air-net modular piping, which is designed to optimise transportation of compressed air from generation to consumption point with least possible pressure drops and also ensures leak-proof air network and smart box, which has smart link services to monitor healthiness of compressor remotely.
Editor: How are these products faring in the Indian market? How do you rate Indian market´s response vis-a-vis other Asian markets?
IC: Atlas Copco strongly believes in innovations and so invests lot in the research and development activities of products. We have several uniquely designed products, keeping three major aspects of Indian industry in mind high energy efficient, environment friendly, safe and reliable. Due to this, our products have always been acknowledged and accepted as technically-superior products and have an edge over other products in the market. We have many installations of our products in the Indian textile industry and they have been working for more than three decades now. We are getting tremendous response in Indian textile market as Atlas Copco always offer them the proven technology with the benefits in terms of performance, energy efficiency, carbon footprint, return on investments, etc.
Editor: You have recently installed an AIRnet, a modular compressed air piping system at a major mill. Please throw some light on this and also tell us how many such projects have been done in past and how many more are in t