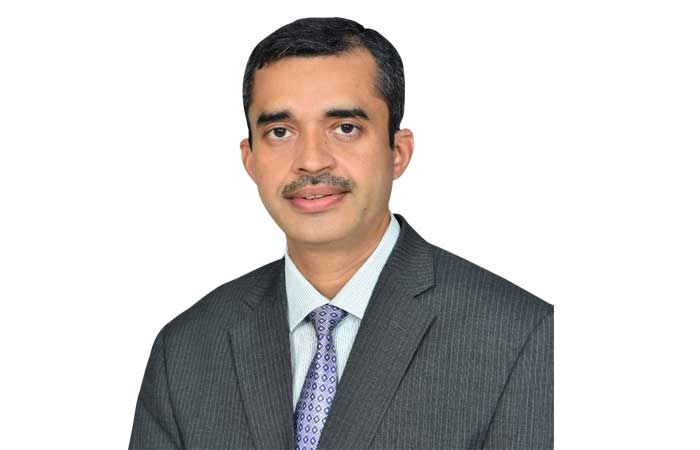
Many stakeholders are increasingly investing in ZLD systems
Pulcra Chemicals is a global company with outstanding engineering capabilities and unique processing knowledge. The company has over 140 years of experience in the production of innovative specialty chemicals for the fibre, textile and leather industries. Working in specialised fields, Pulcra focuses on innovation, health, safety, sustainability and regulatory compliance of their products. Umasankar Mahapatra, Managing Director of Pulcra Chemicals, underscores the company’s commitment to sustainable initiatives and introduces its latest offerings in an interview with Divya Shetty.
Could you share recent projects by Pulcra Chemicals addressing the environmental impact of standard dyeing processes?
During ITMA, we introduced a technology known as Sustineri Colouring, specifically designed for the dyeing process of 100 per cent cotton and polyester-cotton blends. This technology aims to significantly reduce the overall dyeing time, along with minimising energy and resource footprints. The benefits include time savings, decreased water and steam consumption, and overall energy efficiency. This promising and revolutionary technology is currently in the early stages of commercialisation and is a collaborative effort between H&M brands to enhance the sustainability of the dyeing process.
Considering the water-intensive nature of cotton dyeing, can you discuss Pulcra Chemicals’ innovations aimed at reducing water and energy usage in the process?
The Sustineri Colouring technology enables a notable reduction of approximately 50 per cent to 60 per cent in water consumption. Additionally, our widely accepted technology for denim manufacturing, specifically in Indigo and Sulphur dyeing, addresses the considerable water usage in these processes. The adoption of this dyeing technology in denim offers opportunities for resource conservation, encompassing both water and dye substances. Furthermore, through the acquisition of Devan chemicals from Belgium in 2021, Pulcra now offers a diverse range of functional finishes, predominantly bio-based with ingredients ranging from 90 per cent to 95 pe cent. This not only ensures product safety for consumers but also promotes safety in manufacturing. These initiatives represent our commitment to contributing to sustainable practices in the textile industry.
How does the company manage and treat its wastewater, and are there any challenges in implementing such facilities?
In the realm of specialty chemical manufacturing, the process is not inherently water-intensive in terms of output, as water serves as a raw material. Contrary to a common misconception associating the chemical industry with high pollution, this is not universally accurate. In specialty manufacturing, involving formulation and reactions, water functions as an input, and the discharge is minimal. Discharges are limited to sanitary use and occasional vessel cleaning during product changes, both of which are treated through our Zero Liquid Discharge (ZLD) process.
The Zero Liquid Discharge (ZLD) process entails the comprehensive treatment of water emanating from industrial processes to achieve a complete absence of liquid discharge. The treated water undergoes an effluent process, incorporating a series of filtration stages and membrane utilisation, culminating in an evaporator that facilitates water recovery. This ensures that no liquid is released into drainage systems. In contrast, traditional Effluent Treatment Plants (ETP) typically discharge water, subject to specific regulatory specifications mandated by local authorities.
The emphasis remains on the absence of liquid discharge, making zero liquid discharge the standard, even within the textile manufacturing sector. Notably, textile processes generate substantial effluent, with water consumption ranging from 50 to 100 litres per kilogram of finished textile.
Many stakeholders are increasingly investing in ZLD systems to enable the reuse of approximately 90-95 per cent of the recovered water in their processes. This trend is exemplified by the textile industry in Tirupur, where a significant portion of the sector has adopted ZLD practices. The momentum is spreading to other regions, reflecting a growing recognition of the need for water self-reliance.
Kindly share current trends in the textile chemical industry.
The prevailing trend in the chemical industry centres around prioritising safety in chemistry, particularly in the use of non-hazardous ingredients during textile manufacturing. This emphasis aims to prevent the emission of toxic fumes and mitigate potential skin-related issues. Additionally, there is a concerted effort to minimise the environmental footprint when discharging chemicals, aligning with the focal points of brands, retailers, and local authorities.
Compliance requirements pose a notable challenge, with increasing demands for adherence to standards such as JTHC and GOTS. However, this proliferation of certification standards introduces duplication and, consequently, additional costs for manufacturers.
Innovation within the industry is geared towards enhancing process efficiency by reducing processing time and overall temperature requirements. This is particularly relevant in textile dyeing processes, which traditionally operate at high temperatures, consuming significant energy. Chemical suppliers are actively contributing to sustainability goals by minimising energy and water footprints and enhancing product safety.
A fourth aspect involves the creation of differentiated and functional products, catering to both commodity and performance textiles. Chemical suppliers play a crucial role in assisting customers to differentiate their products by incorporating new functionalities, enhancing ease of use, and delivering health benefits and comfort.
In the context of Pulcra’s specific products, the focus lies in providing functional finishes, such as antimicrobial solutions sourced from bio-based linseed oil, offering environmental safety. Other differentiated products include bio-based thermal regulation, providing wearer comfort, and phase-change materials for temperature maintenance, with applications in both apparel and home textiles.
Could you please elucidate the company’s short-term and long-term objectives?
The short-term objective involves significant market expansion across all countries of our presence to augment market share and overall volume. This expansion is complemented by a strategic focus on differentiation within the dynamic landscape of specialty chemicals, given the intensifying competition. Emphasis is placed on continual innovation through research and development, introducing new chemistries and processes to maintain a distinctive position. Recognising the inevitable commoditisation of existing products over time, this proactive differentiation is crucial.
Historically recognised primarily in the textile sector for fabric treatment, Pulcra has strategically diversified its product portfolio in recent years. This expansion encompasses the incorporation of various products in finishing and other domains, contributing to an extended market presence. The company is particularly committed to advancing its position in technical textiles, with a focus on developing coated products for flame retardant applications. These applications span military, commercial, and home farming sectors, representing key areas of growth and strategic concentration.