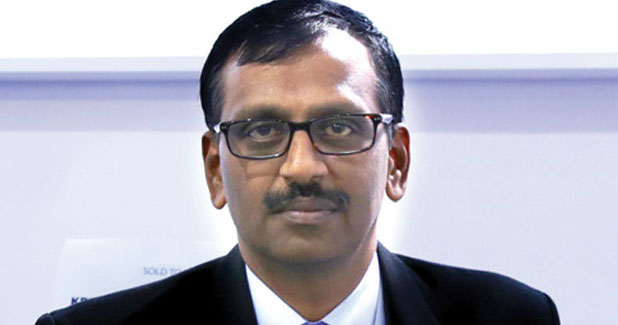
MAG SPinFO: Online spindle monitoring system
SPinFO acquires data from individual spindles in ringframe; individual machines precisely and provides a detailed overview of the machine performance to the users.
SPinFO acquires data from individual spindles in ringframe; individual machines precisely and provides a detailed overview of the machine performance to the users.
MAG Solvics introduced its online spinning monitoring system in ITMA 2015 and received very good response from the customers. MAG successfully completed many installations from reputed mills and many are in progress. SPinFO is designed to give complete information about the performance of the spinning mill. It helps in optimising the deployed resources by continuously monitoring and controlling the essential process variables and improves the productivity and quality, thereby increasing the profitability of the mill.
SPinFO acquires data from individual spindles in ringframe; individual machines precisely and provides a detailed overview of the machine performance to the users at various levels such as operators, supervisors, maintenance personnel, managers and the top management for immediate action, analysis and prompt decision making, thus ensuring the increased performance of the spinning mill through reduced manufacturing cost.
Monitoring parameters include production, doffs stoppages, end brakes, rogue spindles, slip spindles, idle spindles, draft, twist, power consumption*, air consumption*, temperature and RH*.
Note: * means optional.
Six tier information system includes: Tier 1 – Spindle level; Tier 2 – Sectional level; Tier 3 – Machine level; Tier 4 – Block level; Tier 5 – Plant level; and Tier 6 – Mail and SMS.
Tier 1 – Spindle level: All the end breaks and deviations are sensed and alerted through two colour LED placed in individual spindles. End breaks, rogue, slip and idle spindles are shown in Tier 1, which is important for operators and shop-floor staff.
Tier 2 – Sectional level: One LED is placed at section which consists of 24 spindles. Any deviations in these spindles are alerted in section LEDs apart from individual spindle LEDs. This LED is bigger in size and attracts the operator from longer distance to attend where they can identify the spindles with spindle LEDs. Tier 3 – Machine level: The MDU fixed at the aisle way displays all the important data for the operator and supervisors like end breaks, end mending time, deviation spindles (rogue, slip and idle), spindle efficiency, power consumption (UKG), pre-doff/doff/stop signalling through two colour LEDs.
Tier 4 – Block level: The info panel displays the current consolidated performance of the department covering all the parameters through slides. It provides the top performing machines, operators, alerts and other parameters.
Tier 5 – Plant level: The client software developed by MAG is very unique to the spinning mill. Any client PCs can be connected to the main server. The special dashboard at the entry screen gives a snapshot of current performance of the department. This includes production (hour-wise and machine-wise), end breaks, deviation spindles, stoppage, doff, power, temperature and efficiency of the whole department. The parameter which exceeds the given standards is highlighted by two colours for alert and warning.
Analysis and reports
- Dynamic analysis facilitates numerical as well as graphical analysis of the data through,
- Detailed analysis
- Comparative analysis with graph
- Trend analysis with graph
- Speed curve analysis
- Comparative report with sort and filter options for easier and faster analysis
- Analysis results can be exported to excel for sharing and storing
The standard fixed reports and comparison reports have many options – machine, machine group, count, mixing, operator, shed, supervisor for all parameters. Analysis report provides data in numerical and graphical format and has all the combinations mentioned above. Instantaneous machine status display and drafts are also provided.
Speed curve analysis is very beneficial to gauge the performance of the machine. Power analysis is another very important tool for monitoring the energy usage. All the important data like Kwh, voltage, frequency, power factor and UKG are provided. Based on this, management can compare the power consumption of individual machines and take decision or fine tune the machines for optimum usage.
Tier 6 – Mail & SMS: This is user configurable and any type of alerts can be set. MIS report which has all the important details and most required by the top management is sent automatically after completion of every day through mail.
Benefits include:
- Management personnel and technicians can closely observe the performance of the deployed resources and make effective decisions.
- Maintenance personnel can easily identify the deviations in the machinery and respond immediately, ensuring the optimum performance of the machinery.
- Operators can effortlessly find the end breaks or stoppages and prioritise its patrolling pattern to increase the productivity.
- A healthy Work culture is created at all levels by enabling the resources to work smarter rather than to work harder.
For further information: MAG Solvics Private Limited, S.F. # 149/5, Dynamic Center, Solavampalayam (P.O.), Kinathukadavu, Coimbatore – 642 109. Tel: +91 4259 2427 00 | Mob: +91 7667844803 Email: marketing@magsolvics.com | Web: www.magsolvics.com