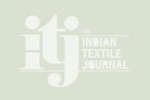
MAG launches online spinning monitoring system
The yarn manufacturing sector is a critical segment in the textile manufacturing chain as it is a resource - intensive process. Therefore, around the world, this segments of manufacturing faces numerous challenges in maintaining competitive manufacturing costs while meeting quality requirements.
The yarn manufacturing sector is a critical segment in the textile manufacturing chain as it is a resource – intensive process. Therefore, around the world, this segments of manufacturing faces numerous challenges in maintaining competitive manufacturing costs while meeting quality requirements. Deviations such as end breaks, rogue spindles, slip spindles, idle spindles, irregular drafts, irregular twists and extended doffs which are caused due to human negligence, faulty machine parts or undesirable raw material quality account for major deterioration in the efficiency of the mill. Energy management is another crucial part, which can save to a greater extent for a spinning mill, thus increasing the profitability. Continuous monitoring and controlling the essential process variables during the textile manufacturing process improves the quality and productivity.
SPinFO, the Spinning information system developed by MAG, acquires data from each and every spinning point precisely right from preparatory to winding and provides a detailed overview of the manufacturing process to the users at various levels, thus ensuring the success of the spinning mill at a lower manufacturing cost. The immense benefits of SPinFO include:
- Management personnel and technicians can closely observe the performance of the deployed resources and make effective decisions.
- Maintenance personnel can easily identify the deviations in the machinery and respond immediately, ensuring the optimum performance of the machinery.
- Operators can effortlessly find the end breaks or stoppages and prioritise their patrolling pattern to increase the productivity.
- A healthy Work culture is created at all levels by enabling the resources to work smarter rather than to work harder.
Six Tier Information Systems
- Spindle Level – Two colour LED with two types of indication for each spindle to indicate deviations instantly.
- Sectional Level – Two colour Blinking LED indication at every section of the ring frame
- Machine Level – Seven Segment Display unit and Signalling lamp for each machine side.
- Block level – Live statistics for the current shift is displayed in a large information panel (LED TV).
- Plant Level – Detailed Information about all the resources throughout the plant can be obtained from the client software
- Mail & SMS – Alerts and Periodic reporting via Mail and SMS to defined persons
Dynamic and User friendly Software
- Windows based informative and user friendly software.
- Well organised dash board renders two-level graphical information about the current shift.
- Power and Draft monitoring with average and instantaneous values in graphical form.
Dynamic Analysis facilitates numerical as well as graphical analysis of the data through,
- Detailed Analysis
- Comparative Analysis with Graph
- Trend Analysis with Graph
- Speed curve analysis (for end breaks and power analysis)
- Reports with multiple filter options and user configurable parameters.
- Data rich MIS Report with graphs for quick and easy analysis of the situation.
- Print and export to MS excel or PDF options.
- Multiple language support to enhance the end user accessibility.
- Client Server configuration to enable simultaneous multiple user access
- Wireless Data Transfer to reduce wiring complexity and maintenance