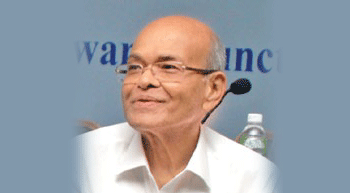
Machinery import soars as local high-tech R&D front limps
Good news: Textile machinery production has gone up by 15 per cent in 2013-14 out of which spinning machinery´s contribution is over 50 per cent. Bad news: Textile machinery import is still soaring, and attempt to produce high-tech machines in India is a non-starter.
Good news: Textile machinery production has gone up by 15 per cent in 2013-14 out of which spinning machinery´s contribution is over 50 per cent. Bad news: Textile machinery import is still soaring, and attempt to produce high-tech machines in India is a non-starter.
Textile machinery industry in India has a few problems sticking out like sore thumbs since time immemorial. The capacity of the over 1400 industrial units is to the tune of Rs 9000 crore against a demand of Rs 14,000 crore. The capacity utilisation has hardly inched up from 60 per cent, with the result that imports, including a sizeable chunk of used machinery (20 per cent of machinery import), amounts to around Rs 9,000 crore every year. Undoubtedly, a deplorable situation! The oft-repeated question is why has India´s textile machinery base faltered in R&D, though the country has eight textile research institutions (TRAs). Of course, 80 per cent of the industry is in small segment, where R&D is out of reach because of fund scarcity. But, the situation has now reached serious proportions, igniting concerns from many a quarter, as our neighbour, China, which has been good at copying technologies for a long time, is also turning out some original equipment in some important segments of the textile industry including spinning, weaving and processing. This was clearly evident at the recently-concluded ITMA Asia in Shanghai, during which the Chinese strides in textile technologies raised even a few European eyebrows.
Are there any solution?
Yes, says a confident- looking Textile Machinery Manufacturers Association, which has proposed development of high speed high-tech shuttleless rapier looms of international standard through a consortium of five manufacturers from India with technical guidance and support from the Central Manufacturing Technology Institute (CMTI), Bangalore. The project cost is put tentatively at Rs 20 crore with 90 per cent funding from the Government under the PPP mode.
Is this a good beginning? Will it take off? Only question after question tumbles out, and answers seem to be a far cry!
But at the recently-held AGM of TMMA, some thought-provoking suggestions surfaced from none other than two eminent personalities – Yogesh Kusumgar, President & CEO of Kusumgar Corporates, Mumbai and Padma Bhushan Dr T Ramasami, Former Secretary, Department of Science & Technology, Govt of India.
The Chinese Model
Assemble first, get help from ancillary units or source, develop technology simultaneously and launch the venture, says Yogesh Kusumgar.
¨Globalisation has thrown a lot of challenges to the Indian textile industry, which is not only huge but is very diverse and dynamic. Our industry has to grow in terms of diversity, volume, value, quality and quantity. I am impressed by the spinning segment, which has contributed almost 50 per cent of the total machinery production in the country.
Can the machinery producers take up the challenge of producing high-tech machinery in India, which will help reducing the trade balance in favour of our country, since the import content in this segment is very high. In terms of number and value, weaving machines stand on an upper level, but not at the highest level. In spite of declining shuttle weaving, we have good local and export business in this. But what about shuttleless weaving? Even in shuttleless weaving, the global trend is in water-jet and airjet. How many air-jet and water-jet shuttleless weaving machines have been imported in the last decade into the country? How many manufacturers from India has taken serious interest in making these machines in India? Some scanty attempts have been made but this will help neither the entrepreneurs not the country.