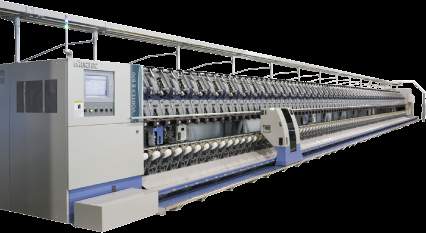
Know the key process variables in vortex spinning
The yarn structure and the quality of the yarns produced from vortex spinning has more relationship with process variables during the yarn manufacture, explains Dr G Nagarajan.
There are many different spinning systems in textile industry. Some of them are in commercial use such as ring spinning, rotor, air jet and air vortex. Friction spinning system although it is a very easy method for yarn manufacturing like insertion of twist in the yarn by a pair of rotating drums, it suffers a serious disadvantage in yarn strength due to ‘twist loss’. Air Vortex spinning is the latest and proven technology to spin yarns from fibres with swirling air concept. The yarn structure and the quality of the yarns produced from vortex spinning has more relationship with process variables during the yarn manufacture. The present paper discusses the process variables.
1.0. Introduction
Many advanced spinning systems have developed in the past 4 decades and one among them is Air vortex spinning system. Although the modern spinning systems have certain advantages than the conventional ring spinning system in terms of quality, the strength of the yarn is comparatively higher than that of the other developed spinning systems. The limitations are obvious such as lengthy process route, spindle speed, traveller speed, space, labour requirements etc.
Certainly, the conventional ring spinning technique is currently the most widelyused accountingforanestimated90%oftheworldmarketspinningmachines.In Ringspinning a wide range of yarn counts and material can be spun, lower rate of yarn faults making them as a versatile spinning machine in the world. The shortcomings of the conventional ring spinning like higher hairiness has been overcome by certain modifications in the drafting zone and spinning geometry in the compact spinning system. Compact spinning is one of the modifications of ring spinning process by the help of betterintegrationoffibersintotheyarnstructure.This results in improved yarn evenness, lower hairiness and higher tensile strength for the same twist level. Open-End rotor spinning is another most commonly accepted unconventional short-staple yarn spinning technology. It is a process in which the input material to the spinning system is highly drafted, ideally to the individual fibre state. The individual fibres are subsequently collected onto the tail end of a seed yarn that is rotated to twist the fibres into the yarn structure and thereby form a new length of yarn. The spinning is continuous as the input material is continuously collected on to the open end of a previously spun yarn. Better yarn uniformity, lower hairiness, higher elongation due to ‘back doublings’ in the rotor groove. However, the rotor spinning has lower yarn strength by 10 to 30% than that of its counterpart ring spinning system.
In the early 1980s, air-jet spinning system was launched. Initially only the man-made fibres could be used as the raw material; later, it was improved for cotton yarn spinning as well. Although the developments aimed to produce 100% cotton yarns, the acceptable quality was provided with polyester/cotton blended yarns in terms of yarn strength. Today the latest development in air-jet spinning technology is the Murata vortex spinning (MVS) technology, which was firstly introduced at Osaka International Textile Machinery Show in 1997(OTEMAS’97) by Murata Machinery.
2.0. Principle of Air vortex spinning
The latest concept in air-jet spinning developed by Murata Machinery is known as the vortex spinning system which uses a modified single air nozzle. This system is claimed to be capable of producing 100% carded cotton yarns which have a ring spun-like appearance and higher tenacity due to higher number of wrapping fibres when compared with that of the previous air-jet spinning systems. The Vortex spinning system consists of a 4 roller apron drafting system. The drafting zone is divided into three zones, viz, Main draft zone, Intermediate draft zone and break draft zone. The break draft occurs between 3rd and 4th roller and intermediate draft between 2nd and 3rd roller. Main draft takes place between 1st and 2nd roller similar to speed frame 4 over 4 drafting system.
Third passage draw frame sliver is used as the feed material for vortex spinning as it requires higher sliver uniformity and parallelization. The drafted fibres after coming out of the front rollers, move towards the air-jet nozzle. Although the fibres are oriented to be twisted with the pressured air effect, the twisting motion tends to flow upward toward the front rollers of the drafting unit. The upward propagation of the fibres is prevented by a small protrusion in the spindle tip during the yarn formation. The high-speed whirled air current arises in the vortex chamber into where the pressured air is injected. The preceding parts which will be core fibres later are drawn into the vortex spun yarn trail. However, the upper portions of some fibres separated from the nip point of the front rollers are kept open. Figure 1: Vortex yarn formation.

After the departure of trailing ends from the nip point, they pass through the spiral fibre passage, and they twine over the hollow stationary spindle due to the whirling force of air-jet stream and become the wrapping fibres. Figure 1 displays the yarn formation in Murata vortex spinning system.
3.0. Yarn structure
Vortex yarn has different yarn structure when compared to that of the conventional yarn structures. Vortex spun yarn consists of two-segmented structure which includes core and wrapper fibres which covers the core part of the fibre grouping the yarn body. Since fibre separation occurs everywhere in the outer periphery of the fibre bundle, a higher number of wrapper fibres are obtained with jet-spun yarns. This leads to the production of a spun yarn with more of a ring-spun-type appearance and also with higher tenacity. The schematic diagram of vortex yarn structure is shown in Figure 2.
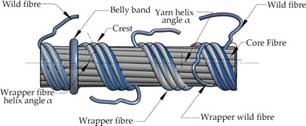
Figure 2: Vortex yarn structure
The classifications in the vortex yarn structure is explained below.
Core fibres: These fibres may be straight or inclined. Core fibres constitute a major pro- Portion of the yarn. Further, its orientation has a big impact on the stress-strain behaviour of the yarn.
Wild fibres: These fibre groups randomly protrude from the main yarn body in any direction. The wild fibres incremental adds to a more hairy yarn.
Wrapper fibres: The helix angle of wrapper fibres around the core fibres are considered similar. There might be some degree of inclination with respect to the yarn central axis.
Wrapper-wild fibres: These fibres wrap around the core fibres in a different direction from the regular wrapping fibres. The wrapper-wild fibres have a scattered appearance. There is no common angle for wrapper-wild fibres because of their disordered appearance.
Belly-band fibres: These fibre groups are the main body wrapping fibres composed of either core or wrapper fibres. Belly band fibres are observed in the upright position with respect to the yarn central axis.
Comparing the yarn structure of vortex with other spinning systems, ring spun yarns has the highest proportion of core fibres whilst the vortex yarn has minimum ratio of oriented fibres. It means that core fibres are helically embedded into the yarn. No wrapper fibres can be seen in ring spun yarn structure. Belly band fibres are more predominant in rotor spun yarns. The highest wrapper fibres could be seen in vortex yarns than the other spinning systems. It can be emphasised that there was no twist in the core fibres of the vortex yarns which was a significant feature. Moreover, the highest percentage of wild fibres could be seen on the wrapper fibres instead of on core fibres in vortex yarn structure.
Air vortex yarns has more wrapper fibres when compared to that of the jet yarn structure provided with two jet nozzles. Since only one nozzle is used in Vortex spinning, the fibre bundle separation occurs everywhere in the outer periphery of the fibre bundle. This has resulted in more number of wrapping fibres and thus resemble ring spun yarn like appearance and improved tenacity.
4.0. Process variables
The main process variables in the vortex spinning are
a. Yarn delivery speed
b. Nozzle pressure
c. Nozzle angle
d. Spindle diameter and the spindle working period
e. Draft ratio
f. The distance (L) mm between the front roller nip and the spindle tip
g. Yarn count
(a)Yarn delivery speed
The yarn delivery speed of the vortex spinning system of the latest version ranges between 500 to 550m/min. The delivery speed has an important effect on fibre loss and subsequently the yarn quality. The delivery speed determines the time spent by the fibres under the action of whirling force. Higher the speed, lesser the time spent and more the fibre loss.
(b) Nozzle pressure
The nozzle air pressure directly influences the fibre configuration and the yarn structure increasing the nozzle pressure led to the increase of the axial and tangential velocity. The fibre bundles receive higher amount of twist, the yarn becomes stronger but stiff. Changes in nozzle pressure influenced the tightness of wrapping fibres along the yarn strand as well as the amount of wrapping and the proportion of unwrapped sections. Increment of the nozzle pressure would result in high level of tightwrapping ratio. However, they were inclined to turn into irregular wrappings at very high level of nozzle air pressure. Standard nozzle pressure adopted is in between 0.4mPa to 0.6mPa depending upon the fibre material. Higher nozzle pressure also results in lower hairiness values up to a certain limit. If the nozzle pressure is increased beyond 0.6mPa, there are more chances for the hairiness to get worse due to the formation of wild fibres. This was attributed to the rate of change in radial position of a fibre (mean migration intensity) becoming higher at the high nozzle pressure values
(c) Nozzle angle
The effect of nozzle angle on the swirling air during yarn formation influences axial, tangential and radial velocities inside the nozzle block. This is quite complex in nature while studying the fluid flow under dynamic conditions. Axial velocity acts in “x” direction, radial velocity in “y” direction and tangential velocity in “z” direction. Increasing the nozzle angle (θ) cause increase in axial velocity and decrease in tangential velocity. The radial velocity also increases which expands the fibre bundle which results in more number of open end trailing fibres. Standard nozzle angle is 70•.
(d) Spindle diameter and the spindle working period
The tightness of the wrapping fibres on the vortex yarn structure is influenced by the spindle diameter. Four spindle diameters are available, viz, 1.1,1.2,1.3 & 1.4 mm. Larger the spindle diameter (1.4mm), lower the unevenness of the yarns. On the contrary, the yarns exhibit higher hairiness and lower tenacity values. This is attributed to the more freedom in movement of fibres and the fibres arrange themselves around the spindle tip in large spindle diameters. Alternatively, when the spindle diameter is reduced from 1.3 to 1.2mm, yarn unevenness increases due to the restricted movement of the fibres around the spindle tip.
The wear of the spindle increased with an increasing period. Comparing the performance of the spindle wear from the start up to 4 months, spindle wear occurs at the tip zone and around the spindle as well. Due to this, the tenacity, breaking elongation and work of rupture also varies due to the wear rate of the spindle.
(e) Draft ratio
Higher the total draft and lower the intermediate draft, lower will be the thick and thin places. In general, the intermediate draft plays an important role in yarn quality and tensile properties. With an intermediate draft of 2.5, higher breaking elongation and breaking work is obtained, however, thick and thin places would increase. This is mainly attributed to the slippage of fibres during drafting. For any material, there should be an optimum level of intermediate draft. When it reaches the optimum level, further increase in drafting force would cause the fibres more slippery and the main draft could not control the fibre slippage as the main draft is higher. Hence an optimum intermediate draft of 2.3 should be preferred.
(f) The distance (L) mm between the front roller nip and the spindle tip
The effect of distance between front roller nip point and the spindle was significantly important for the fibre loss and the number of wrapping fibres. Figure 3 shows the distance (L) between the front roller nip and the spindle.
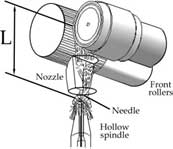
Figure 3: Front roller nip to spindle tip distance (L) in mm
The short front roller to the spindle distance produced more even yarns with fewer imperfections and less hairiness. If the distance is short, the most of the fiber ends were tightly assembled, and there were fewer open-ended fibres. Hence, a yarn similar to MJS yarn with parallel core fibres mostly but fewer open-ended fibres was observed. In that case, yarn evenness and the imperfection results were more pleasing because of the minimum risk of losing control of fibres.
(g) Yarn count
As in the case of other spinning systems, higher production speeds would worsen the yarn quality. The delivery speed, yarn count and the nozzle pressure are the important variables which affect the yarn quality. Yarn evenness, imperfections, tensile properties and hairiness were all affected significantly from the parameters. It means that yarn count is also highly correlated with the vortex yarn properties.
5.0. Fibre specifications for optimum results
The fibre specifications in order of importance for successful application of vortex yarns are:
a. Fibre fineness
b. Length
c. Tenacity
d. Cleanliness
e. Inter- Fibre friction
a. Fibre fineness
Number of fibres required for spinning yarns in air vortex/airjet is greater than that of the ring spinning. Finer fibres generally bring down the bending rigidity of the vortex yarns and also increase the tightness of the wrappings as well. However, as a result of finer fibres, nep level will increase which may create clogging of nozzles. The fibre fineness should be around 1.3dtex.
b. Length
Long fibres give long and firm wrappings around the core. However, long fibres are more prone to the formation of neps. Hence the length should be restricted to 38mm for polyester/cotton blends and 44mm for polyester/viscose blends.
c. Tenacity
Yarn tenacity is generally influenced by the fibre strength. Hence strong fibres are recommended for use in vortex spinning. In addition, fibre elongation is an important parameter in order to generate enough wrapping compression.
d. Cleanliness
Sliver purity or cleanliness is a critical factor in vortex spinning. Any trash particles or fibrous neps present in the material would hinder free rotation of yarn in the narrow air jets. This would affect the twist insertion, weak places and even an end break.
e. Inter fibre friction
Higher fibre to fibre cohesion is desirable as it increases the inter fibre cohesion coupled with production of stronger yarns and minimum end breaks.
6.0. Conclusion
The swirling air is used to manufacture yarns instead of any mechanical part used in other systems. In fact, Vortex spinning is a modern alternative for ring and rotor spinning. The yarns are less hairy, low pilling and higher abrasion resistance, high moisture absorption, good color fastness and fast drying capabilities. Despite the advantages, many process variables like airflow characteristics, nozzle pressure, diameter of the nozzle orifice directly influence the vortex magnitude. Air vortex spinning has to come out with viable solution to solve twin problems like harsh feel and manufacture of 100% carded cotton yarns to be competitive with ring spinning.
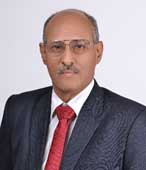
About the Author
Dr G Nagarajan is a Senior Technologist in Texcoms Textile Solutions, having a vast experience of 35 years in textiles, working in the industry, academia as well as research. He has published more than 15 research papers in national and international journals and 3 textile books. He has presented his research studies in various technological conferences held in India. He has traveled across the globe working and providing consultations to mills and institutions. He has been well received and appreciated by the Ministry of Industries & Commerce of Ethiopia for improving the quality of the yarns to Uster 5% level.