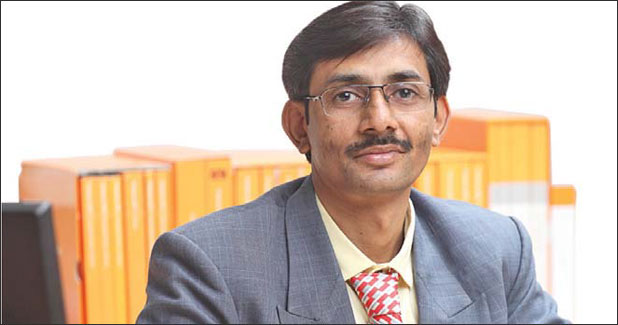
Keeping industrial electronics healthy
New generation technologies and solutions are important for all industries, including textile industry. But equally important are taking care of the aspects that affect the life of electronics on the field, says Pravin Patel, Manager ? Quality & Services, B&R Industrial Automation.
New generation technologies and solutions are important for all industries, including textile industry. But equally important are taking care of the aspects that affect the life of electronics on the field, says Pravin Patel, Manager ? Quality & Services, B&R Industrial Automation. In an interview with the Editor of Indian Textile Journal, he clarifies and provides an insight with important tips and tricks to manufacturing units and machine builder to extend the life of electronics on the field and avoiding failures.
Excerpts:
How important is automation to textile industries at this stage?
Today, all industries have become automated and everyone is looking at enhancing their position in the market to achieve supremacy by adopting advanced automation solutions such as Industrial IoT and Industry 4.0. Textile industry too is shaping up well in this direction. However, with increased use of automation, the use of electronics on the field is exponentially increasing. This electronics has to be kept running for avoiding machine breakdowns and unplanned downtimes.
Today, automation of textile machines and factories is helping manufacturers achieve desired quality, shorter time to market, productivity and profitability. However, increased automation also brings up the need for maintenance of machines and other equipment used in factories for avoiding downtimes and failures. Timely maintenance is an important aspect for a factory and getting efficient service from machine builders and automation vendors helps in enhancing machine performance and reducing machine downtimes. Automation products such as controllers, HMIs, drives, servos, PCs and peripheral devices are critical components in machines. Reliability of electronics is very important to have more service life of products.
What are the factors behind electronic failures?
Devices failures are common and cannot be prevented. Even in our daily lives, electronic components fail and sometimes without any reason. We all at least once in our time of using smart phones have experienced that our phones fail without reason. Industrial conditions are harsher and thus the reasons for failure could differ from our usual electronics. It is observed that operating condition, power conditions and stress on electronics components contribute to a bulk of failures.
Operating conditions means the ambient operating temperature, humidity, environment , the devices operated in dust (for e.g., cotton fibres, flup), humidity, high temperatures, vibrations, chemical contamination?s, gaseous fumes, etc cause corrosion and oxidations. Such factors cause failure of products or one may experience sporadic behaviour of electronics. Heat reduces the service life of automation products, leading to intermittent tripping of control systems. This could result in stoppages, machine breakdowns and affects continuous processes.
Dust accumulation on PCBs is one of the causes of overheating in electronics increasing thermal resistance. Dust even acts as a conducting agent causing short circuits or even arching between components. This combined with humidity, vapours, oils or lubricating agents, cotton fibers can severely damage electronics. Vibrations affect mechanical strength of electronics especially at solder connections or cable joints. Corrosion of electronics occurs due to entry of liquid, condensation, vapors and raw materials in manufacturing.
Can you throw more light on failures caused by power conditions?
Surge, spikes, harmonics, power fluctuations, interruptions and heavy inrush during powering up are some of the power conditions leading to failures of electronics. Mains line has various problems like harmonics, surge, spikes, fluctuations, interruption, heavy inrush currents on power resumption after outages and improper earthing. Each parameter can cause machines or devices to be damaged and it is necessary to understand the nature of the mains line and take necessary actions.
Harmonics is a distorted wave form generated in the mains supply. All electromechanical devices such as drives, dimmers, welding etc. generate harmonics. They can severely impact devices by malfunctioning, lockup, nuisance tripping, motor failures (overheating), transformer and neutral conductor overload due to excessive zero phase currents. Spikes and surges occur when voltage is 110 per cent or more above normal.
Most common cause of spikes is heavy equipment being turned off nearby or lightening strikes. These lead to computer systems, HMIs to flicker, shut off, errors or memory loss or even lead to permanent damage. Higher amplitude of spikes can even cause burning of circuit boards. Improper Earthing generates heat and results in progressive failure of insulation, leading to earth faults sparking flashover, deterioration of earthing eventually causing fires. Without proper earthing the entire system is at risk of EMI EMC problems experiencing sporadic behavior.
Power fluctuations, interruptions lead to failure of electronics in the mains power sections such as SMPS, rectifiers, DC DC converters, whereas power interruptions, inrush can damage electronics by high dv/dt (rate of rise of voltage with respect to time) and di/dt (rate of rise of current with respect to time).
Overloading and manufacturing defects are some electronic component stress, which result in failures. Such overloading is caused due to high speed of machines, cycle time, wrong applications and wrong parameter selection. The most important aspect to note is to select appropriate components as per application requirement. Solution is effective FAT & SAT test are important to identify the stress on the components, as once material placed in the production process or line has limited scope to correct back.
How can machine builders overcome these problems on the field?
Machine builders should ensure a proper cooling mechanism for control cabinets and paying attention to its installation. Other recommendation is to carry out preventive maintenance such as periodic checking of cooling fans, any entry points for foreign particles and AC temperatures. As a rule of thumb the general dimensioning criteria are to check the environmental conditions of where the cabinets would be located ? ambient temperature, humidity, installation altitude above sea level.
In such cases, machine builders could also use B&R X20 modules for monitoring the cabinet conditions and providing a detailed report to the operators or raise alarms in case of errors. Points to consider are the various types of cooling mechanisms such as natural convection cooling, forced convention cooling, closed loop cooling, air/water heat exchanger or cooling aggregates. Based on the ambient environment the choice of cooling can be deployed.
Usually device manufacturers consider various parameters for power supply disruptions and probable causes of failures etc and design and test the equipment. However, each electronic components has a band of specifications and if operated within the specifications definitely results in longer service life. Good practices of component installations is necessary with considering factors such as EMC, EMI, heat dissipation, wiring, ease of accessibility. To further extend the service life of electronics use of input reactors / harmonic filters act as a buffering of input transients due to utility and load switching elsewhere in the supply, preventing high inrush currents and reducing transient load on the input components. It also improves main input power factor, controlling emissions of line current harmonics due to rectifier input circuit and increasing the service life of dc-link capacitors.
Ultra isolation transformer has galvanic isolation and power is transferred with induced flux. This protects against short circuit on power lines, attenuates the spikes and noise signals, which may range from few milli volts to kilovolts and prevents high inrush current. It also helps in attenuating electrostatic and electromagnetic noises generated due to welding. Ultra isolation transformers are better than the line choke. Power on voltage, stabilizers and uninterrupted power supply (UPS) are also widely used effectively to counter the power supply fluctuations. Use of APFCR, ELCR, Power On delays circuits gives high protections to the machines and plants and makes the plants more robust against mains power line problems.
What are users? responsibilities to shield against such failures?
Good engineering practices such as proper limit setting, software safety interlocks, safety limit settings like overload protection, high speed protection, derating factors must be considered, along with this the training and awareness is equally important.
Component failure are experienced by itself with respect to time termed as MTBF, MTTR, MTTF and FIT. These are reliability terms based on methods and procedures for lifecycle predictions for a product.
It is essential for customers to define the reliability data when determining what product to buy for their application. MTBF (Mean time between Failure), MTTR (Mean Time to Repair), MTTF (Mean time to Failure) and FIT (Failure in Time) are ways of providing a numeric valure based on a compilation of data to quantify a failure rate and the resulting time of expected performance.
New technologies and innovative automation products are improving productivity as well as human safety. These electronic devices are vulnerable to failures but if taken care properly, failures can be reduced along with drastic increase in the service life.
It requires focusing on training and re-skilling of technicians. Periodic product training will keep technicians up-to-date with technology. Maintenance trainings imparted by machine builders and equipment providers are equally important.
Electrical consultants have special role to play as they have domain expertise and special tools to analyse failures and provide unbiased suggestions and improvements.
Corrections & Benefits
?The environmental situations in textile industries are harsh with high temperature, dust and humidity. When we visit manufacturing sites, we educate operators on how they can take care of machines in order to decrease the machine failure. We often notice that dust, oxidisation and sometimes fine cotton fibres cause electronic failures. Considering the site condition, we always propose some corrections such as installing internal cooling system and bigger space in the cabinet designs to have more AIR Flow. The machine builders and end users who have adopted the suggestions have already benefited in terms of long-term machine availability and higher productivity.? – Pravin Patel, Manager ? Services, B&R Industrial Automation