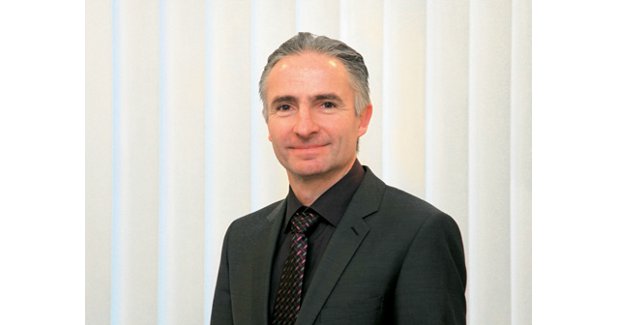
Industry 4.0 is already present at our customers: Reichman
Oerlikon Manmade Fiber technology is all about high quality and cost efficient production. Thus for us, Smart Factory is another important lever to achieve significant steps towards this goal.
Interview with Markus Reichwein, Head of Product Management, Oerlikon Manmade Fibers.
Oerlikon Manmade Fiber technology is all about high quality and cost efficient production. Thus for us, Smart Factory is another important lever to achieve significant steps towards this goal. With our Industry 4.0 solution Plant Operation Center (POC), our customers in India as well as globally are using a system, which offers Total Quality Management of the production chain for example from POY to DTY. Process deviations are tracked down efficiently, and the products are traced throughout the value chain. Fast identification of error sources and implementation of corrections allows to shift manpower away from trouble shooting and routine jobs. The modular system which can be configured exactly according to customer needs also supports in production planning, performance monitoring as well as in maintenance and production recipe management. All those features become increasingly important with the requirement of the Indian market for smaller lot sizes and flexibility for various manmade fiber specialities. (The POC offers production cost advantages with higher product quality levels and improved utilisation rates as well as savings in consumption.)
As described above, Industry 4.0 is already present at our customers using the POC. Features like remote support via augmented reality for us at Oerlikon Manmade Fibers is another tool to support our customers efficiently with our broad expert knowledge in trouble shooting and maintenance processes. In this regard the digital link between our customers and us via the myOerlikon (www.myoerlikon.com) customer portal supplies a cutting-edge solution for a customer-oriented global information and support platform, not only for spare parts and project related information. (The platform also offers information on new products, training videos and a tracking function.)
Also a new range of predictive services is coming up in view of the increasing digitalisation of production plants. But today nothing goes without automation. Automated bobbin doffing, transport and packing is common at our production lines. We are continuously working to expand the automation level with further solutions for our customers.