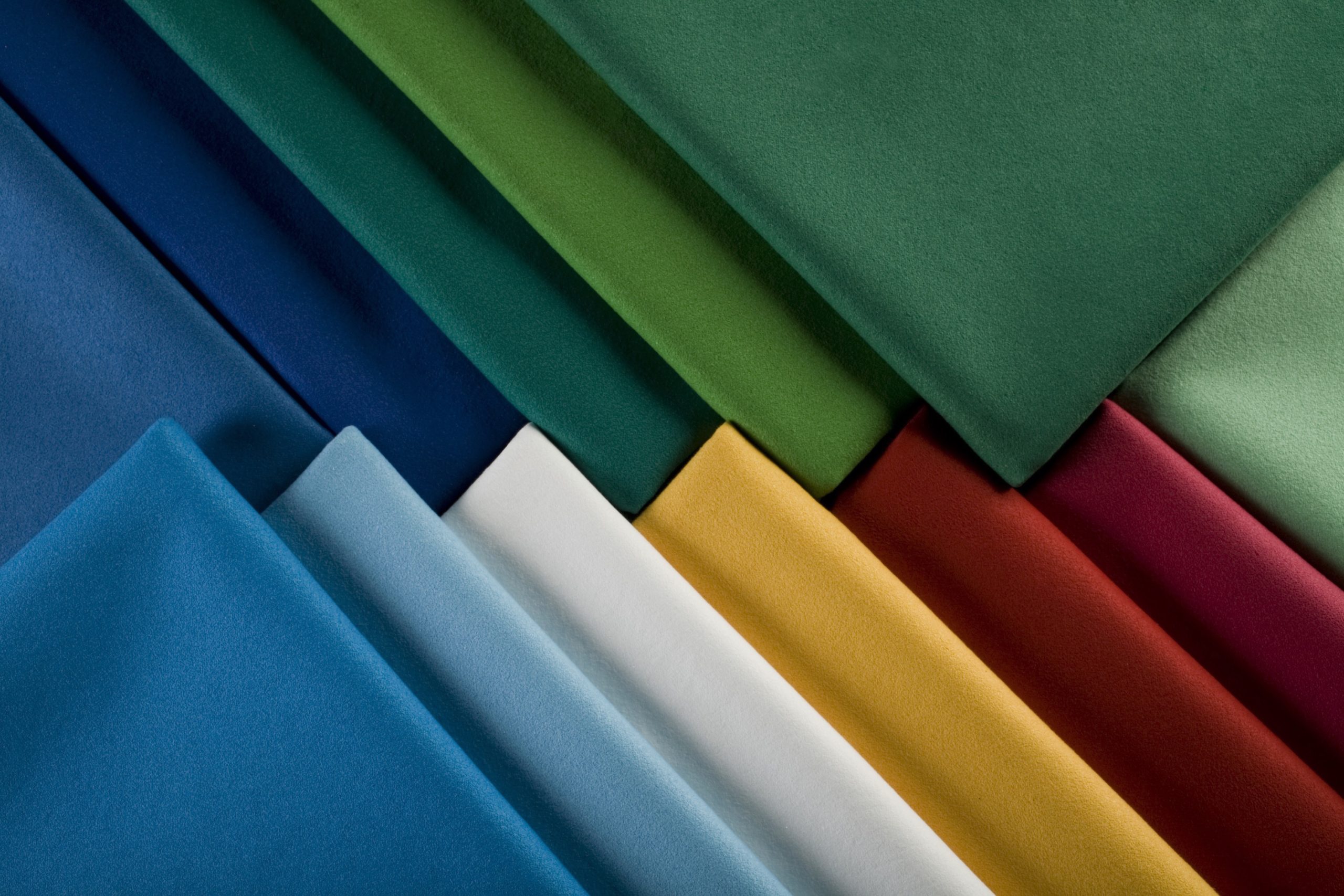
Improving yarn imperfection in polyester cotton blends by optimising flat-to-cylinder setting
This study was conducted to improve yarn Imperfections by changing the flat to Cylinder setting in the C4 Rieter card Machine, explains Mesay Dubale Tigabu and Abayneh Kebede Kasemo.
In textile Industries, processing parameters, and machinery conditions play a decisive role in deciding the quality of the yarn produced. The objective of this study is to improve the quality of the yarn by adjusting the setting between revolving flats and the Cylinder, while the other machine and process parameters were kept constant. Five points between flat and Cylinder were changed into 3.5,3, 2.5, 2.5, and 2.5 mm and have been used to produce 21 Ne Polycotton blended yarns. The improvement in the yarn quality due to the new setting is assessed. It is found that the thin place, thick place, neps and unevenness in the yarn has reduced considerably with this new setting. The total imperfections/km (IPI) of 30/70 Polycotton yarn improved from 1579/km to 727/km. The clearer cut per 100 km after the new setting has shown a significant improvement by having lower number of cuts and better working performance.
- Introduction
The end use of a garment depends on the properties of the fabric. A fabric property depends on the properties of the constituent yarn. With the diversification of the market, spinners are forced to produce quality yarn. Yarn quality is influenced by various types of yarn faults that affect the quality of the fabric produced. At every stage of the yarn production process, different types of faults are generated in the yarn surface frequently or at intervals which are called yarn faults. According to USTER statistics, the most widely used quality parameters for yarn are its evenness, coefficient of mass variation (CV), imperfections (thin places, thick places, and neps), and strength. Yarn imperfection is an important yarn parameter that affects yarn and fabric processing, and quality parameter and it has a decisive influence on the utility and market value of yarn. A high level of imperfections would also lead to more stoppages in the subsequent processes such as ends down in downstream processing and a disturbing appearance in the fabric as well. The lower the imperfections in the yarn, the better the fabric’s appearance and market value.
Higher fibre openness results in less imperfection in yarn because fibre openness results in better fiber individualisation in card sliver, which in turn produces quality yarn. The carding process has a major impact on yarn imperfection.
The card is the heart of the spinning mill or well-carded is half-spun, which is a significant importance of carding. Fibre to yarn conversion process has been affected by several factors, which include properties of raw material, level of technology, machinery, and skill of machine operators. In cotton fiber spinning, the cost of raw material plays an important role, since it accounts for over 50 per cent of the total cost of the ring-spun yarn. After the blow room, carding is the first and only machine (in the card process), which can reduce neps (small knots of entangled fibres), seed coat neps, and the remaining impurities which cannot be removed by the blow room section.
The better quality of the carded sliver is not only dependent on trash and nep content but also on the evenness in card web (weight per unit area), fiber parallelization and fibre-to-fibre separation, and minimising short-term variation in sliver thickness. However, to obtain this quality, the setting parameters of carding machine play an important role, and a small change in the setting is enough to produce inferior sliver quality. Normally, the quality of the yarn is very much dependent on the quality of the sliver for sure. According to the SITRA norms, the setting between Flat and Cylinder for High-production cards is 0.25,0.2,0.2, and 0.2mm. As we decrease the gap between the flat and cylinder in the carding machine, the carding actions between cylinder and flats are to separate flocks to individual fiber and also to eliminate the fine dirt particles and dust, neps, short fiber, etc.).
The Uster statistics is the only global benchmarking tool based on the global collection and testing of fibre, sliver, roving, and yarn samples that have been produced in every part of the world. According to Uster statistics percentile 2018, At the 50 per cent percentile level, the expected thin, thick, and neps number per 1000m of Cotton/Polyester,70/30, carded 20Ne yarn is 2, 91, and 169 respectively and the total imperfection at 50 per cent Uster statistics percentile level is 262.
Materials and methods
Materials
The fibre materials used in the study are 70 percent cotton and 30 percent recycled polyester respectively. The cotton fibre properties are tested in Uster HVI 1000 and the properties of Recycled Polyester Fibre are provided by the fibre manufacturer. The basic cotton and the recycled PET parameters are given in Table 1.
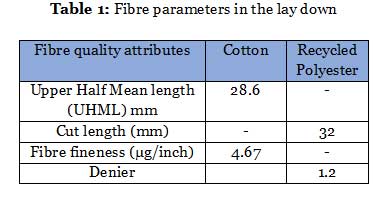
Methods
The mill has been producing the PC blended yarns by blending the polyester fibre and cotton in the Blow room blending method after processing the polyester fibre separately. The trials were conducted at the carding machine by changing the setting of the cylinder to flat on the C4 Rieter card. The delivery speed of the carding machine is 82m/min and the sliver hank maintained is 0.11 Ne. Before changing the settings in the card, the card slivers were collected and processed in the draw frame, speed frame, ring frame, and in auto winding machines as well in a controlled study. The yarn count produced is Ne 21 PC. For both the samples, the breaker and finisher draw frame(Vouk, Sh/D-E) sliver count maintained was 0.12 Ne. The roving count in (Zinser,660) was maintained as 0.78 Ne. The yarn samples were prepared in a Ring Frame machine (FIOMAX 1000, Suessen) with the same spindle speed and the same spindle number. Finally, the small ring cop was changed to a big package by Autoconer (Muratec 7 – V).
In this study, the settings between the flat to the main cylinder are changed from 0.75,0.75,0.75,0.75 and 0.75mm to 0.35,0.30,0.25,0.25 and 0.25. The speed of the carding cylinder, flat, liker in, and doffer are mentioned in the following Table 2.
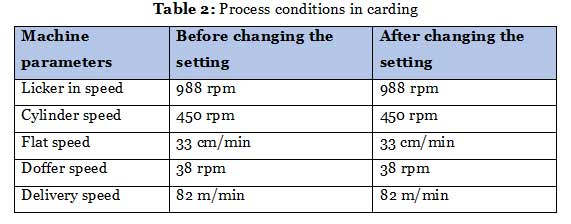
The yarn samples collected f both trials were tested for their yarn quality attributes such as unevenness, and imperfections in Uster Tester 5 tester after conditioning them in a standard laboratory testing atmosphere at International standard test conditions of 65 per cent RH and 20 º C. The single thread strength of the yarns was tested in TEXTECHNO STATIMAT ME+ Tensile Tester.
Results and discussions
The setting between cylinders to flat changes from setting 1 (0.75,0.75,0.75, and 0.75mm) to setting 2 (0.35,0.3,0.25,0.25, and 0.25 mm). Due to this, thin places decreased from 29.3 to 11.8, the thick place in the yarn decreased from 730 to 400.3, and neps in the yarn decreased from 819 to 314. Generally, the total imperfection decreased from 1578.8 to 726.6. The result shown in Table 3, is more than 54 percent improvement in this new setting 2. The Clearer cuts per 100 km decreased from 120 to 81. It means there is a 33 percent clear-cut decrease in autoconer because of the reduction in yarn imperfection. The reason for the overall improvement in yarn imperfections in the new setting is mainly due to the better carding action between cylinder and flats and uniformity in the settings at all 5 points. A wider gap between these two regions impairs the carding action which would result in improper fiber individualisation. On the other hand, too close settings between cylinder and flats than recommended would reduce the wire life of both the cylinder and flats and consequently higher flat waste. Hence, a judicious selection of setting based on the fibre material processed has to be taken into consideration. The optimum setting between flat and cylinder will improve the carding actions which means trash, neps, and short fibre contents are extracted. As a result, the degree of fiber parallelisation will increase. Because of this, the variation in the yarn thickness will be reduced. Therefore the yarn imperfection and unevenness will also be less.
Besides improvement in yarn Imperfections, the strength of the yarn (RKM)has increased from 12.18 cN/tex to 12.52 cN/tex an increase of around 2.7 per cent which is not statistically significant.
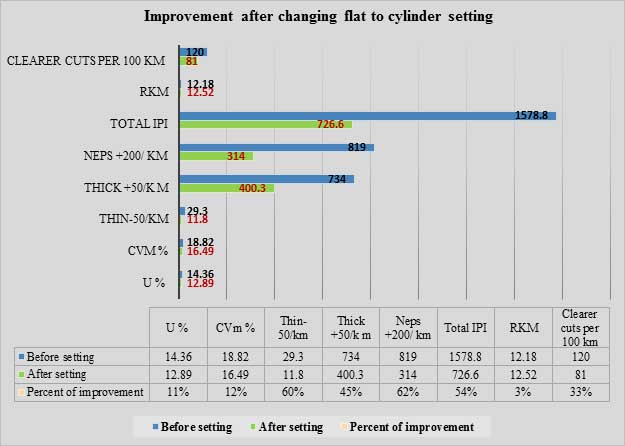
Figure 1: Improvement after changing flat to cylinder setting
The total imperfection improved after a new setting between the revolving flat to the main cylinder. But when compared with USTER statistics 2018, to reach the 50 per cent percentile level for 70/30 Cotton/Polyester carded 20 Ne yarn needs a further 64 per cent reduction in yarn imperfection on other causes.
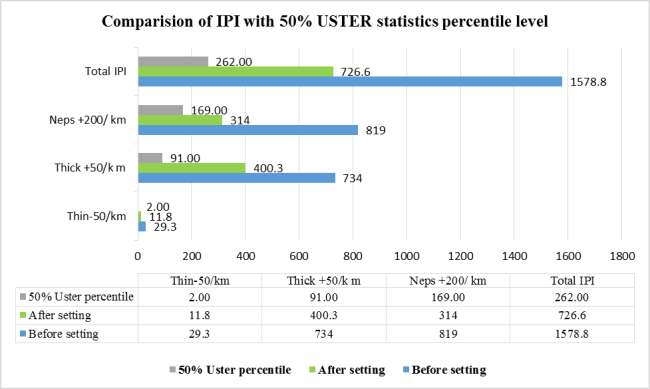
Figure 2: Comparison of Imperfection with Uster standards
Conclusions
This study was conducted to improve yarn Imperfections by changing the flat to Cylinder setting in the C4 Rieter card Machine. The setting between cylinder to flat changes to the new one, The gap between cylinder and flats was reduced, which gives more intensive opening, individualisation, and parallelisation of fibre. Because of these intensive action neps, short fibre and trash contents were removed. This action helps to reduce the total imperfections of the yarn.
References
- Effect of flat speed of carding machine on the carded sliver and yarn quality Mohammad Mamunur Rashid, KZM Abdul Motaleb and Ayub Nabi Khan
- Effect of Feed Plate to Taker-in Distance of Carding Machine on the Quality of Cotton Card Sliver and CVC Ring-spun Yarn
- Comparing Quality Parameters of Yarn Produced by Ring, Rotor, and Compact Spinning System. Zahidul Islam, MDAssistant Professor, Department of Yarn Engineering, Bangladesh,University of Textiles, Dhaka, Bangladesh
- Uster, Uster Statistics, Uster, Uster, Switzerland, 2018.
- Study on the Influence of Fiber Properties on Yarn Imperfections in Ring Spun YarnsJ. Ochola, J. Kisato, L. Kinuthia, J. Mwasiagi and A. Waithaka
- Analysis on the Defects in Yarn Manufacturing Process & its Prevention in Textile Industry Neha Gupta Department of Mechanical Engineering, Integral University, Lucknow, India
- Kumar RS. Process management in spinning. New York: CRC Press, 2014
- Bagwan ASA, Jadhav K (2016) Card Setting: A Factor for Controlling Sliver Quality and Yarn. J Textile Sci Eng 6: 246. doi:10.4172/2165- 8064.1000246
- Alagirusamy R. Process control in blow room and carding operations. In: Das A and Majumdar A (eds) Process control in textile manufacturing. Amsterdam: Elsevier, 2012, pp. 132–157.
About the author:
Mesay Dubale Tigabu is a MTech in Textile Engineering from IIT Delhi. He is currently working as the Associated Researcher at the Manufacturing Industry Development Institute, Textile & Garment Research & Development Centre.
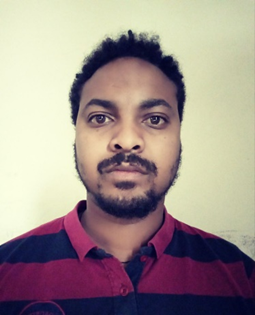
Abayneh Kebede Kasemo is a BSc in Textile Engineering Bahir, Dar, Ethiopia. He is currently working as the Assistance Researcher at the Manufacturing Industry Development Institute, Textile & Garment Research & Development Centre.